Features
Well arranged core construction
The core is made of top-class Hi-B (high magnetic flux density) oriented silicon steel plate with improved exciting characteristics such as core loss, exciting current, magnetostriction, etc. The core is tightened uniformly with tempered plastic bands and also a core election equipment is employed, thus making it small-sized and lightweight together with low noise level.
In details:
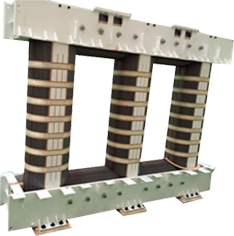
-
Since there are no holes in the core plate, it provides for easy machining and improve the characteristics.
-
The core tightening bolts are cooled directly by insulation oil since they pass through the oil duct.
-
Because of using the tempered plastic bands, the core plate ends can be tightened securely.
-
As a result of improving the space factor of core, the transformer can be made compact and lightweight.
Winding construction
Various windings have been developed in addition to the conventional twin coil disc winding, and according to the purpose of use, the optimum winding is selected from those listed below so that the specific characteristics can be fully utilized.
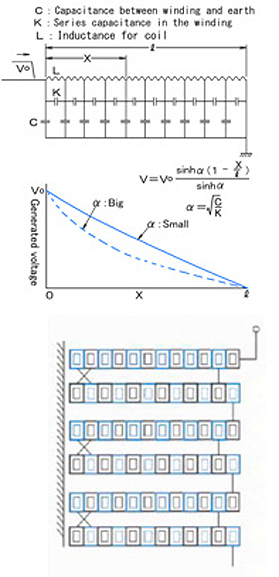
For low voltage and large current;
Cylindrical layer winding (using transposed conductor)
Helical winding
For high voltage and surge protection;
High series capacitance disc winding
For wide-range tap;
Multi-parallel cylindrical tap winding
Highly reliable insulation
For the windings of extra high voltage transformers, a high series capacitance disc winding, in which potential oscillation in the winding is suppressed to a minimum when impulse voltage is applied. The insulation in the windings, across windings and across winding and ground has been made very reliable as a result of numerous fundamental experiments and improvement of potential distribution and insulation strength by utilizing a computer. Also, extra high voltage are given a partial discharge test to verify the insulation reliability before leaving the plant.
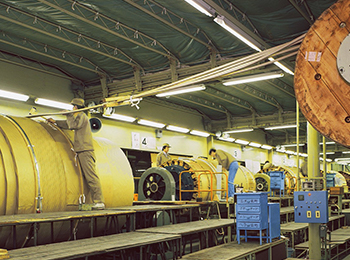
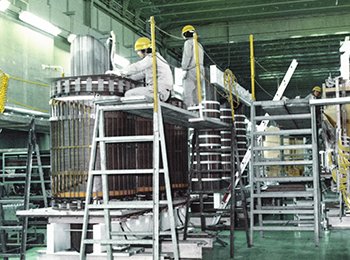
Loss reduction technology
As the winding conductor, a transposed conductor has been employed besides the rectangular copper wire to cope with the increase in transformer capacity.
The transposed conductor is made as follows;
With the finely divided rectangular conductors each insulated with synthetic resin consisting mainly of polyvinyl formal, the odd-numbered conductors are arranged in two rows as shown in Fig.2, the mutual positions of conductors are transposed in turn at a certain pitch, and with these conductors put together as a unit, the same electric insulation Kraft paper as used for ordinary rectangular copper wires is wound thereon for insulation. When this transposed conductor is used, the following merits are available:
-
1.
Reduction in stray load loss in winding
-
2.
Prevention of local overheat in winding
-
3.
Improvement in characteristics, and
-
4.
Accomplishment of lightweight and compact transformers
-
5.
Decrease in the number of connecting parts in winding
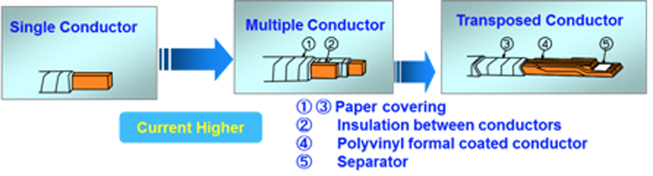
Cooling system
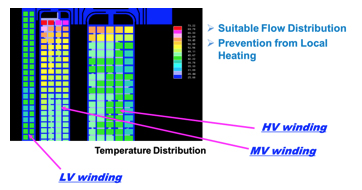
The optimum cooling system will be selected out of following according to the customer 's requirements and also taking into account the transformer capacity and circumstances at the installation site.
1) ONAN, 2) ONAF, 3) ODAN, 4)ODAF, 5) OFOW
In a large core, the core internal temperature rise is kept under the limit by providing a cooling oil duct at right angles to the steel plate stacking direction. For the winding, an oil duct is installed in the coil as required for obtaining a high cooling effect.
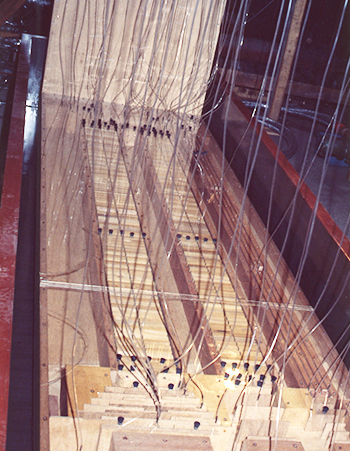
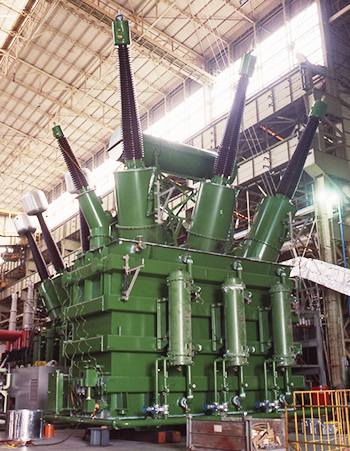