Interview
Interview2. From Factories to Urban Development - Introducing Fuji Electric’s Solutions for Supporting Industrial and Social Infrastructure through “Stoppage Free Equipment”
Source: Nikkan Kogyo Shimbun Online
From November 30, 2021 to December 13, 2021
The age of digital transformation (DX) through artificial intelligence (AI) and big data utilization will continue to see an explosive increase in the volume of information processing and communication via the Internet. To ensure reliability and security, Internet data centers (IDCs) play a leading role in digital infrastructure. As a result, major IT companies throughout the world are continuing to invest heavily in IDC development.
Fuji Electric is contributing to the resilience of industrial and social infrastructure through use of its cultivated energy management technologies.
As an example, we are providing a next-generation community energy management system (CEMS) that utilizes AI for the New Sapporo Station District I Development Project. In addition, we have achieved significant energy savings for our own semiconductor factory using a factory energy management system (FEMS) that facilitates the visualization, clarification, and optimization of operations.
We interviewed the senior managers in charge of industrial and social infrastructure to learn about the strengths of our company's solutions as well as to hear their opinions on decarbonization.
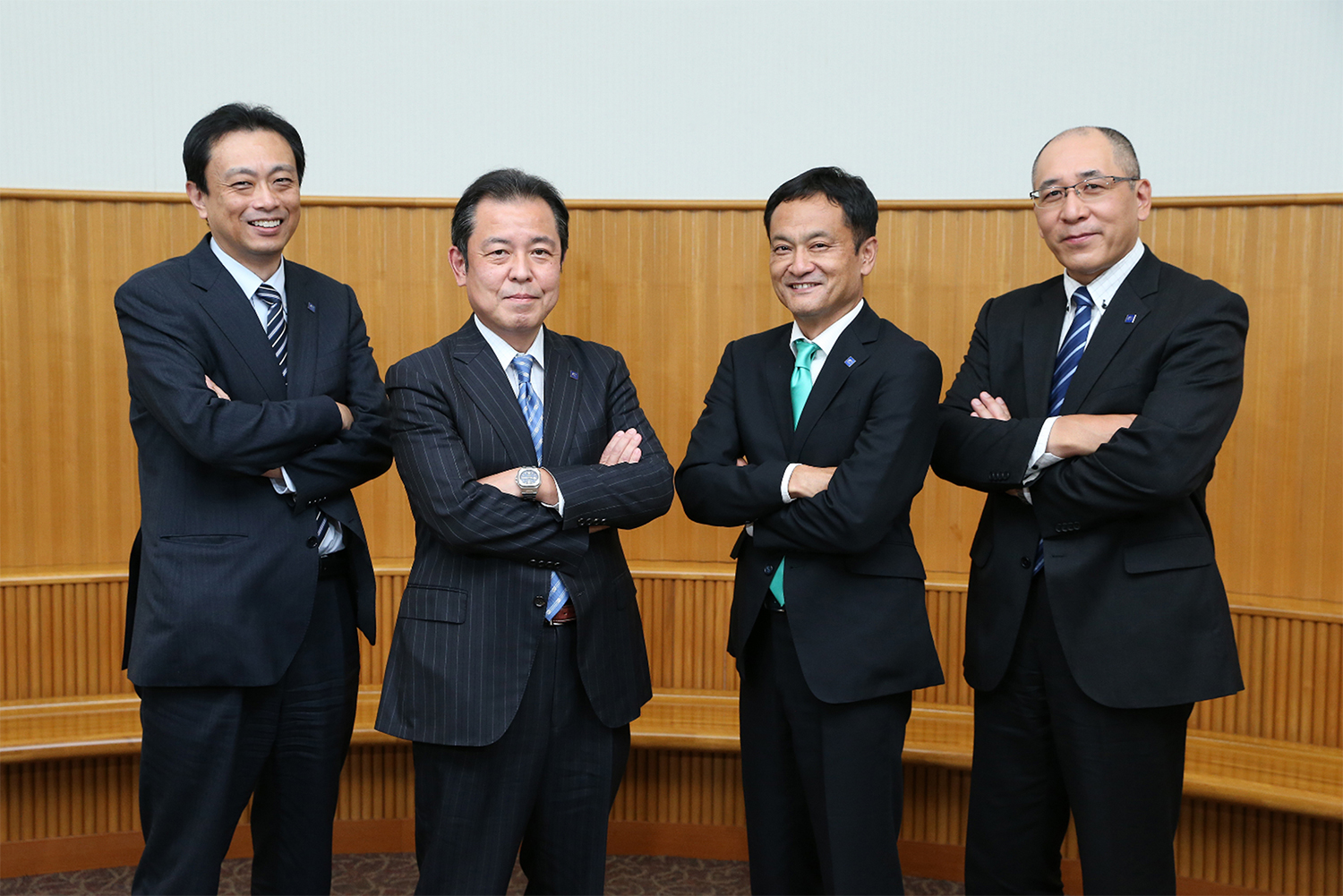
-
*
-
We wore masks except when filming, and took measures to protect ourselves from COVID-19.
Contributing to Decarbonization through Solutions that Meet Customer Needs
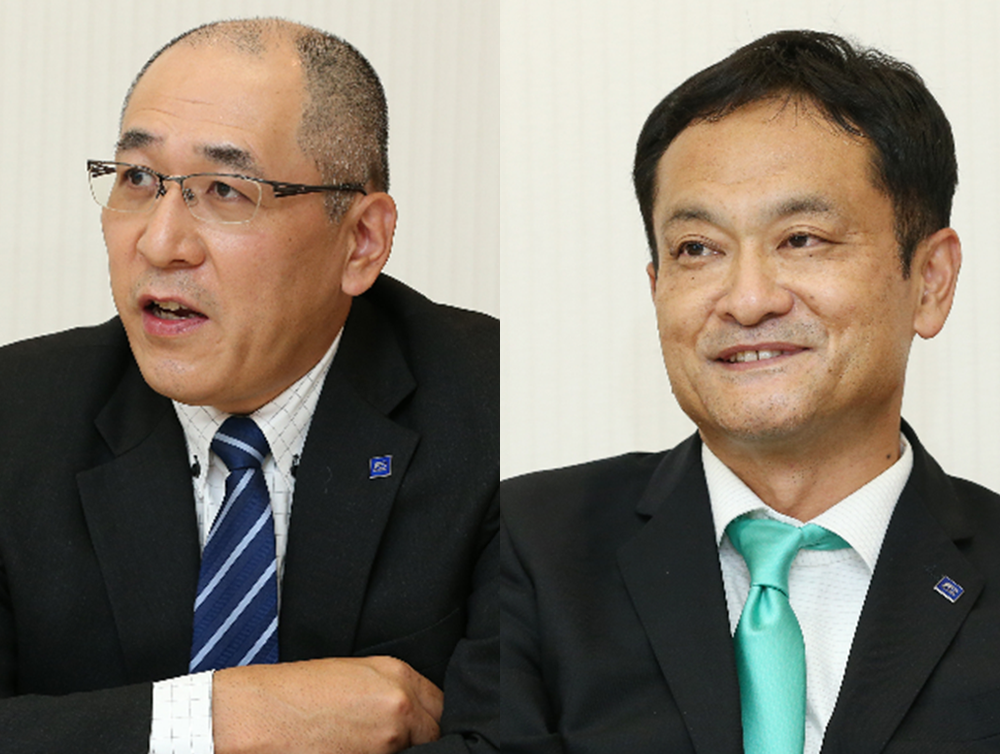
(Right) Mr. Takuro Muragishi, Senior Manager, Power Supply Engineering Dept.
Fuji Electric is developing power supply systems for IDCs and semiconductor factories, as well as solutions businesses that facilitate their construction. Mr. Shunichi Sugawa, Senior Manager of the Power Supply Engineering Department in the Power Supply and Facility Systems Division of the Power Electronics Energy Business Group at Fuji Electric, described the strengths of our company by saying, “We have a full lineup of products, from substations to generators and uninterruptible power systems (UPSs). We are able to respond to a wide range of customer needs by providing one-stop system engineering solutions for components, not just single pieces of equipment such as UPSs and transformers.
The power semiconductors used in our UPSs are made in-house, and by collaborating with our Semiconductor Division from the design stage, we have been able to gain a competitive advantage by making products more efficient and compact.”
In addition, Japan and other major countries have announced that they are endeavoring to be carbon neutral (virtually zero greenhouse gas emissions) by 2050. In this respect, it is likely that energy-intensive IDCs will be called upon to take environmental measures to the next level.
Mr. Takuro Muragishi, Senior Manager of the Electrical Facility Engineering Department, described initiatives that contribute to decarbonization by saying, “Some of our transformers have already switched their insulating oil from mineral oil to vegetable oil, and we are also developing gas-free products that do not use SF6 (sulfur hexafluoride) gas in order to reduce greenhouse effects.”
Contributing to the Construction of Social Infrastructure with Next-generation CEMS
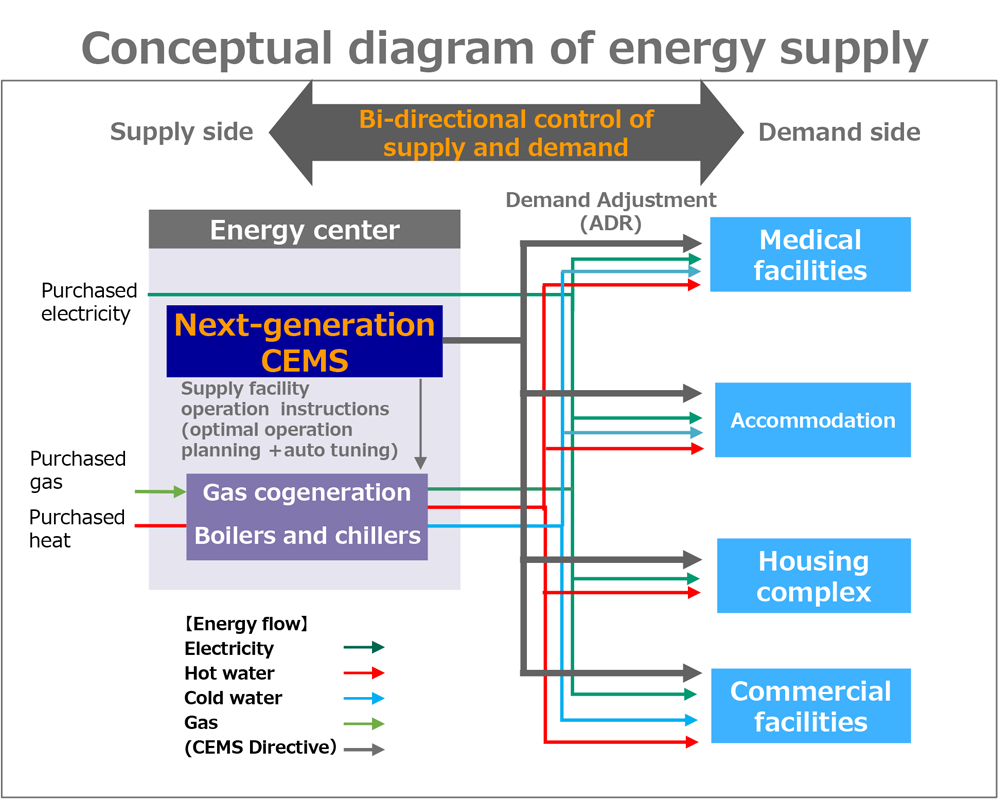
Hokkaido Gas has been participating in the “New Sapporo Station District I Development Project” and is building an energy center in the district. Natural gas cogeneration (combined heat and power) will be installed to save energy during normal operation and to strengthen the resilience of the entire district by ensuring that energy is supplied to each building in the event of a disaster.
This is a major project and Fuji Electric is contributing to it by supplying a next-generation CEMS that utilizes AI. The system derives a highly accurate and convincing demand forecast by using our unique statistical machine learning AI forecasting technology. After this, the system automatically implements optimal demand suppression while ensuring comfort on the consumer side, and also automatically regulates equipment and devices to maximize energy efficiency in the entire area. AI is also used to automate energy efficiency detection, factor analysis, and diagnosis.
The project is scheduled to be completed by the end of fiscal year 2023. However, the medical facility is expected to be completed in July 2022, and it is in conjunction with this date that commercial operations are scheduled to begin for the energy center.
Fuji Electric’s energy management technologies are not only useful for urban development, but are also utilized to save energy in factories and plants. In Japan, where electricity prices tend to be higher than in other countries, it has been a major challenge to secure international competitiveness while reducing energy costs. At the same time, management is now facing the new challenge of achieving decarbonization through reduction of carbon dioxide emissions.
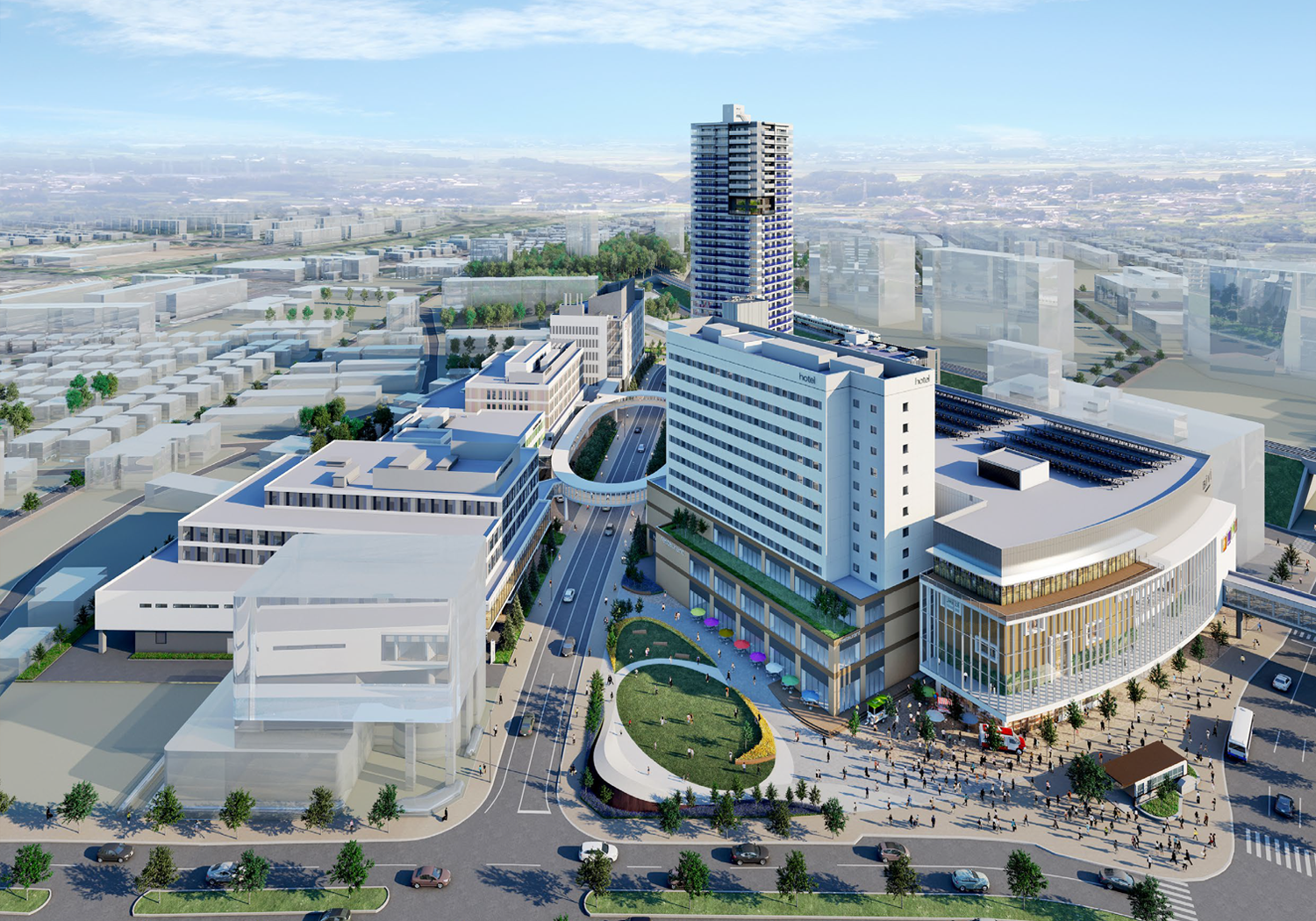
Achieving 34% Energy Savings Compared to Fiscal Year 2010 - Proprietary Energy Management System Technology Deployed at a Semiconductor Factory
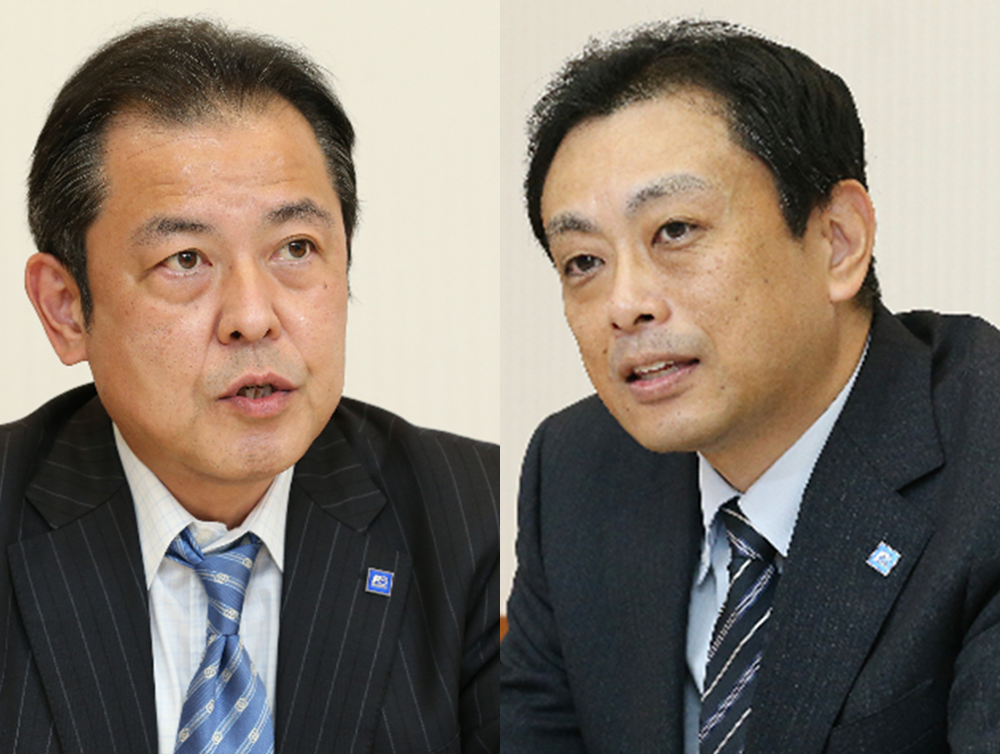
(Right) Mr. Jun Hoshino, Senior Manager, Control Equipment Dept. Factory Automation Systems Division
The distinguishing feature of Fuji Electric’s FEMS for factories is that it offers three steps for visualizing, clarifying, and optimizing operations, based on the principle of “developing energy management infrastructure to achieve improvements on a daily basis.”
Mr. Naoki Azumaya, Senior Manager of the Information System Engineering Department I in the Information Solution Division of the Power Electronics Industry Business Group at Fuji Electric, explained the flow of deployment by saying, “The first step is to visualize the situation, then to clarify the issues and the effects of improvement, and finally to balance supply and demand.”
Obviously, a poorly performing FEMS will not resonate well with customers. However, since Fuji Electric is a manufacturing company, we were able to ensure the performance of our FEMS by deploying it in our own factory as a “testbed” to demonstrate the benefits of the system firsthand.
In particular, our Yamanashi Factory located in Minami Alps City in Yamanashi Prefecture has been using the FEMS to optimize and make its power control power semiconductor production line more intelligent. Mr. Azumaya explained why he chose the Yamanashi Factory as the testbed by saying, “Semiconductor factories consume a lot of energy and any unexpected stoppage can have disastrous consequences. This area in Yamanashi has also been susceptible to momentary voltage drops, so this factory seemed ideal for testing our system.”
The Yamanashi Factory utilizes solar power generation, cogeneration, and fuel cells as additional energy sources that supplement the regular power grid. Compared to fiscal year 2010, the deployment of the three-step FEMS system was able to reduce energy consumption for the factory by 34% in just five years. Furthermore, the FEMS has enabled the factory to achieve its pre-deployment goal of improving its self-sufficiency rate for electricity from 0% to 100%.
Stabilizing Operation through Data Collection, Analysis, and Anomaly Detection
Fuji Electric has been providing components and systems that contribute to energy conservation and productivity improvement for factories.
For example, our “OnePackEdge” assembly process data collection system is helping customers solve problems at production sites that use IoT. By collecting, accumulating, visualizing, and analyzing all kinds of data on shop floors, operators can identify the cause of defective products and equipment anomalies and take preventive measures to ensure that there is no equipment downtime.
Mr. Jun Hoshino, Senior Manager of the Control Equipment Department in the Factory Automation Systems Division at Fuji Electric, has been marketing OnePackEdge as a new core product and has said, “There are many cases where data collected from manufacturing equipment is not used properly. This is why we created OnePackEdge as a system that simplifies the collection of shop floor data and stores it for easy analysis so that it can be visualized in a manner that facilitates analysis using cameras and other linked devices.”
Realizing Stoppage Free Equipment
Fuji Electric is committed to constructing resilient industrial and social infrastructure. Our equipment demonstrates a wide range of technological capabilities in various fields ranging from factories to urban development, but they all utilize the common design principle of contributing to a decarbonized society. We are dedicated to realizing “stoppage free equipment” that supports people’s lives behind the scenes through formidable technologies that supply, optimize, and stabilize energy.
Contributing to SDGs
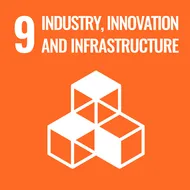
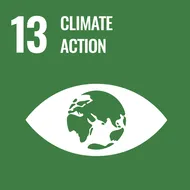
Fuji Electric’s solution achieves “Stoppage Free Equipment” and contributes to the resilience of industrial and social infrastructure through responding customer’s various problems.
Recommended
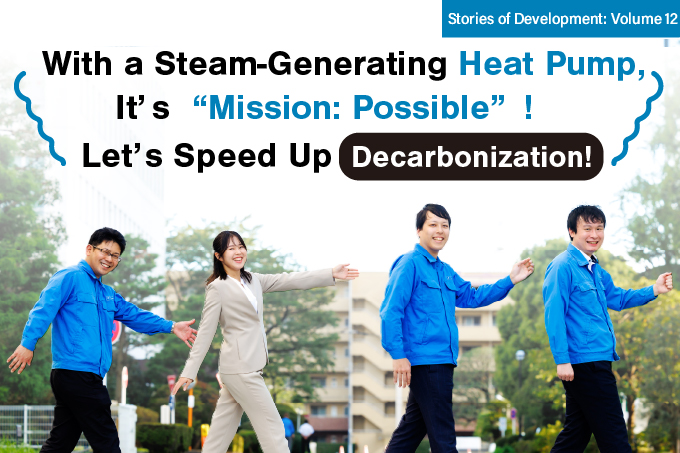
March 11,2025
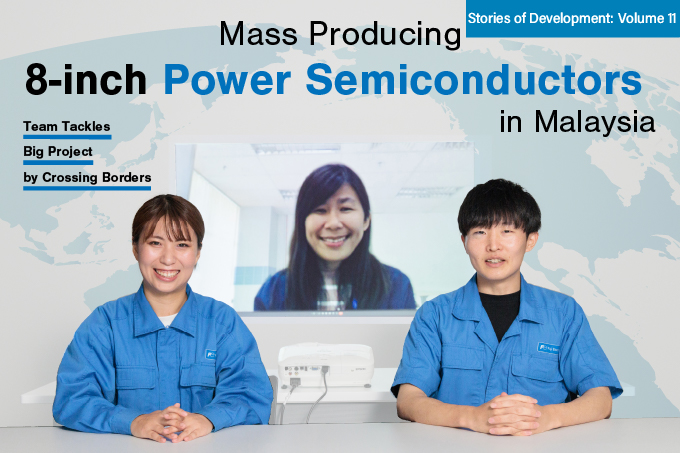
March 10,2025
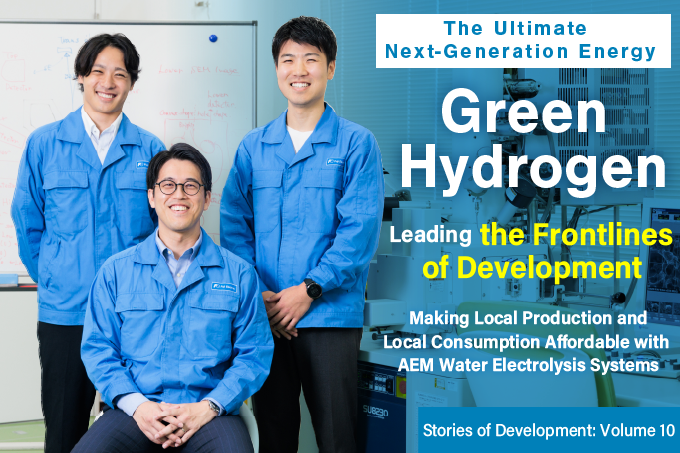
March 5,2025
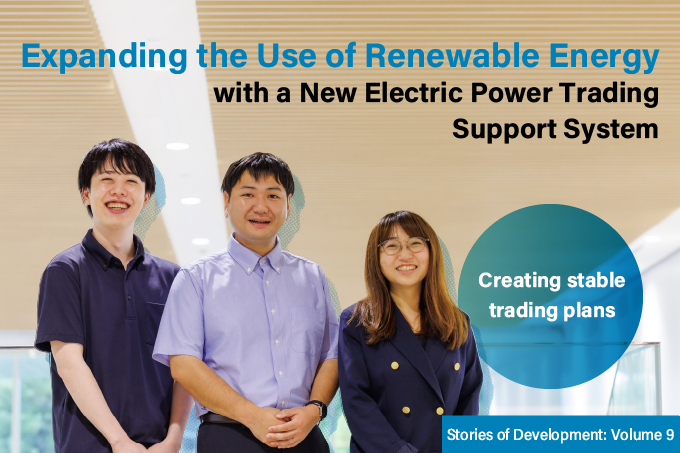
December 19,2024