The Ultimate Next-Generation Energy: Following the Cutting-Edge Development of AEM Water Electrolysis for Green Hydrogen
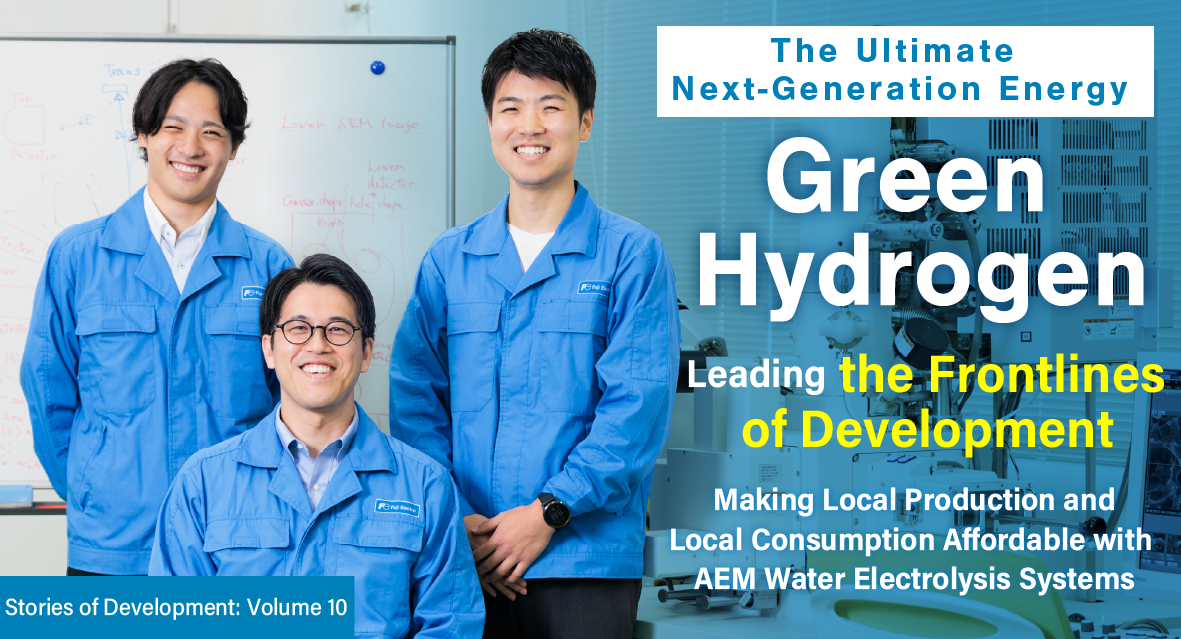
Hydrogen has been attracting attention as a next-generation energy source. In particular, green hydrogen is a promising energy source in terms of decarbonization, as it uses electricity derived from renewable energy with no CO2 emissions during the production process. However, there are many issues that need to be addressed in order to produce green hydrogen and achieve the widespread use of hydrogen energy. In response to these challenges, Fuji Electric is developing a new hydrogen production method.
The method is known as AEM water electrolysis.
What issues does this hydrogen production method address? We asked three members of the development team.
A new technology to realize low costs
Hydrogen is extracted by passing electricity through water, splitting it into hydrogen and oxygen (a process known as water electrolysis). The method of electrolysis differs depending on the type of electrolyte membrane. Conventional water electrolysis is called PEM(Note 1) water electrolysis, while the new method under development by Fuji Electric is known as AEM(Note 2) water electrolysis.
-
(Note 1)
-
PEM: Proton Exchange Membrane
-
(Note 2)
-
AEM: Anion Exchange Membrane
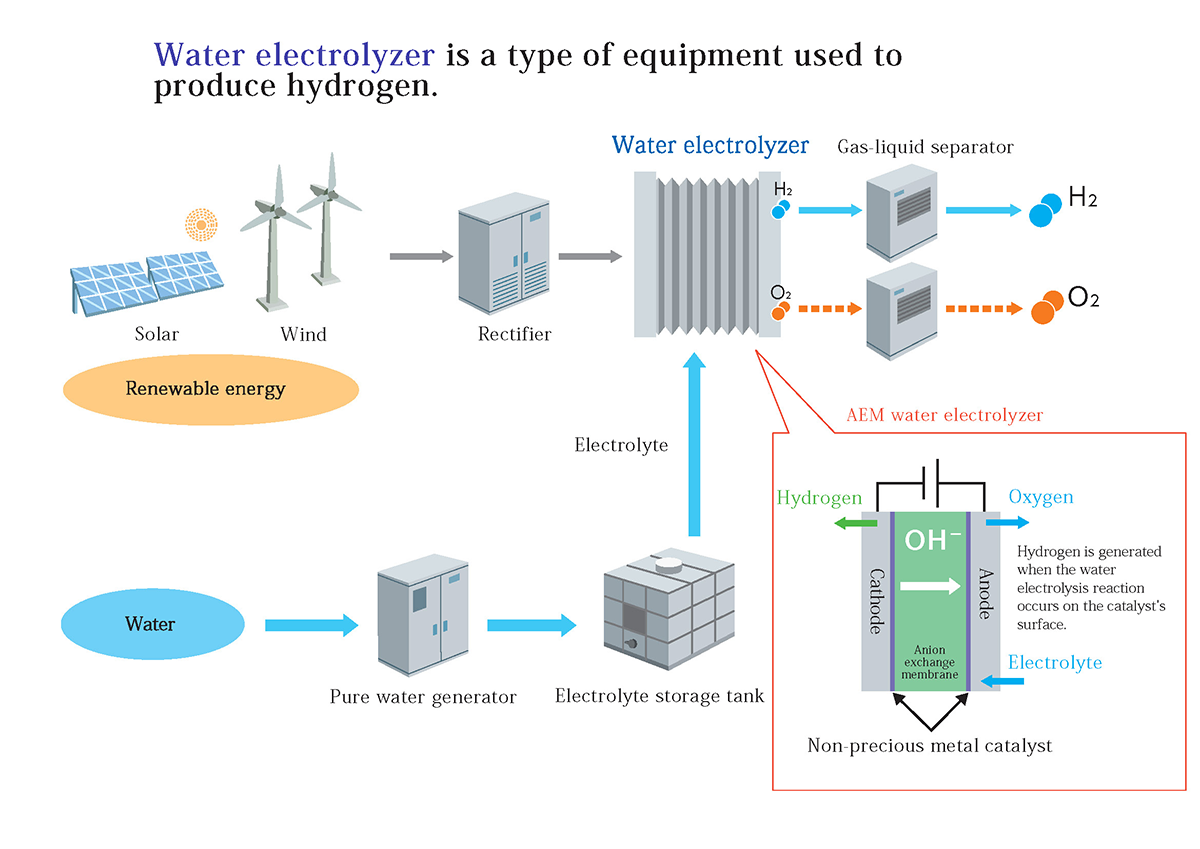
While PEM water electrolysis requires the use of expensive metals such as iridium to serve as catalysts for the electrodes, inexpensive metals such as nickel are sufficient catalysts in AEM water electrolysis. For this reason, it is more cost-effective than PEM water electrolysis, and the catalyst metals are more easily sourced, making it beneficial from a resource strategy perspective. However, due to challenges like the durability of components, few manufacturers have been involved in developing the method.
Utilizing hydrogen in familiar places to achieve decarbonization
The team leader, Dr. Hirakata, shared his thoughts regarding the significance of developing an AEM water electrolysis system.
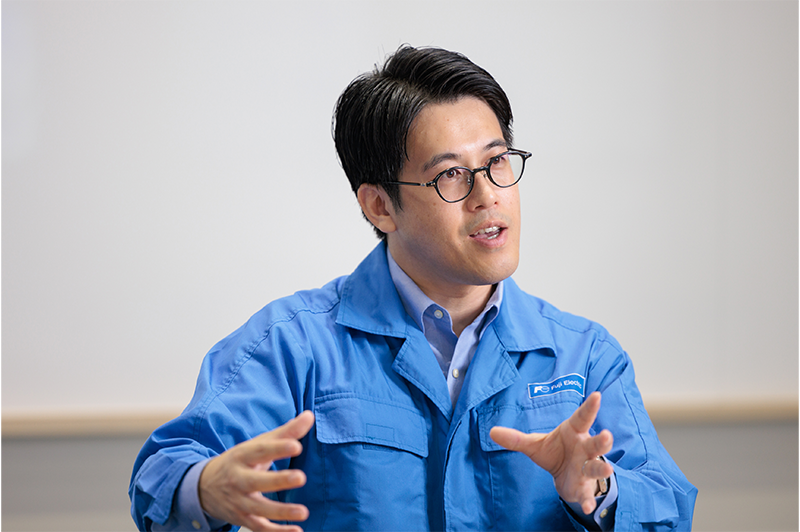
“Fuji Electric has been offering many products involved in the utilization of hydrogen, such as fuel cells and rectifiers that serve as power sources for water electrolysis, but water electrolysis systems were the last piece of equipment that has yet to be sold on the market. Water electrolysis is the most important process in hydrogen production. If we can commercialize AEM water electrolysis equipment, we will be able to provide customers with a single set of products that will allow them to utilize green hydrogen,” he explains.
In regions where electricity derived from renewable energy can be supplied cheaply, high-volume hydrogen production is expected to reduce costs. This is driving the trend toward larger water electrolysis systems. Such operations required hydrogen to be transported to the place of demand, posing the challenge of developing the necessary infrastructure. To address this issue, Fuji Electric is developing small- and medium-scale systems. The aim is to enable the installation of low-cost, small- and medium-scale hydrogen systems near factories and offices, enabling hydrogen to be used on the spot for local production and consumption. This results in the advancement of decarbonization through the use of hydrogen in places we visit in our day-to-day.
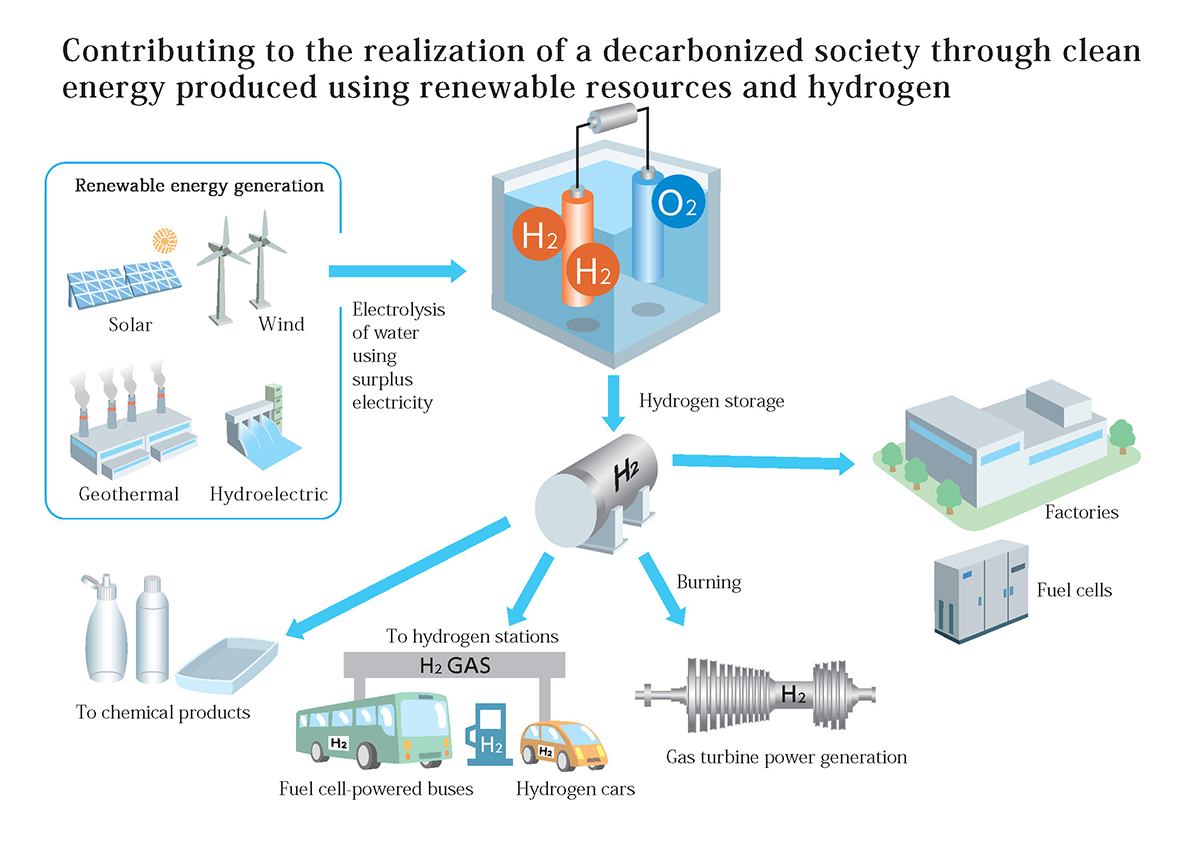
AEM water electrolysis can contribute to lower hydrogen costs!
For the Fuji Electric team, the starting point for the development process was technology cultivated in the production of fuel cells. Efforts were boosted by the development of technologies for important components such as electrolyte membranes and electrode catalysts at universities and other institutions that are leading the nation in fuel cell research. These components are being developed through open innovation, utilizing industry-academia-government collaborations and corporate partnerships. Fuji Electric is developing prototypes for water electrolyzers equipped with the latest electrolyte membranes and electrode catalysts while sharing component-related challenges with universities and companies in order to improve component properties. In these ways, we are developing technologies for safer and more efficient water electrolysis.
Dr. Hirakata, the team leader, studied fuel cells as a student. It has been eleven years since he joined the company. Water electrolysis shares many technological aspects in common with fuel cells. As such, he has been using his knowledge from his university days to lead his team. “It was our job to see if it was still worth the company's resources to invest in AEM water electrolysis going forward. We're finally seeing the value of our investment,” he explains.
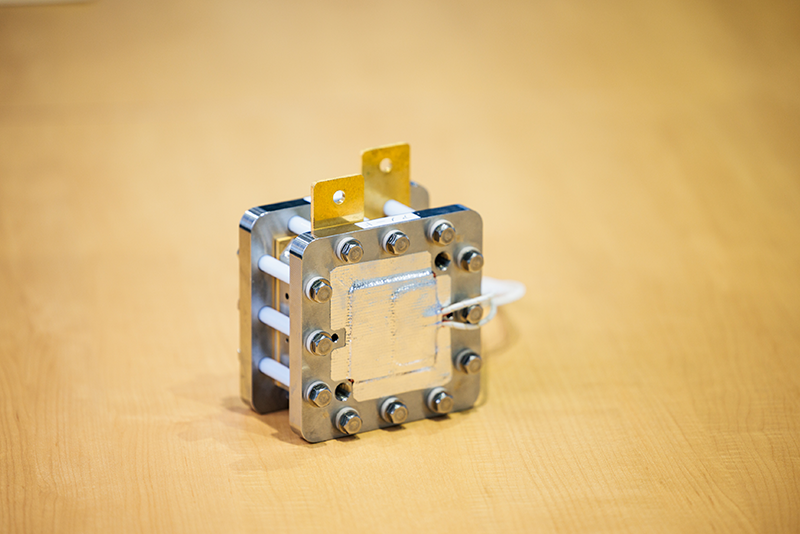
The rewarding experience of seeing the final product
Mr. Sato, who joined the company as a mid-career recruit, highlights the development of a cell(Note) structure that optimizes water electrolysis on catalysts as one technical challenge.“There are still many unknowns that need to be clarified, such as what kind of structure is necessary for the electrolyte to flow evenly throughout the cell.Moreover, the performance of electrolyte membranes and catalysts is constantly improving, and we have to keep up with that,” he relates.
-
(Note)
-
Cell: The basic reaction unit of a water electrolysis device
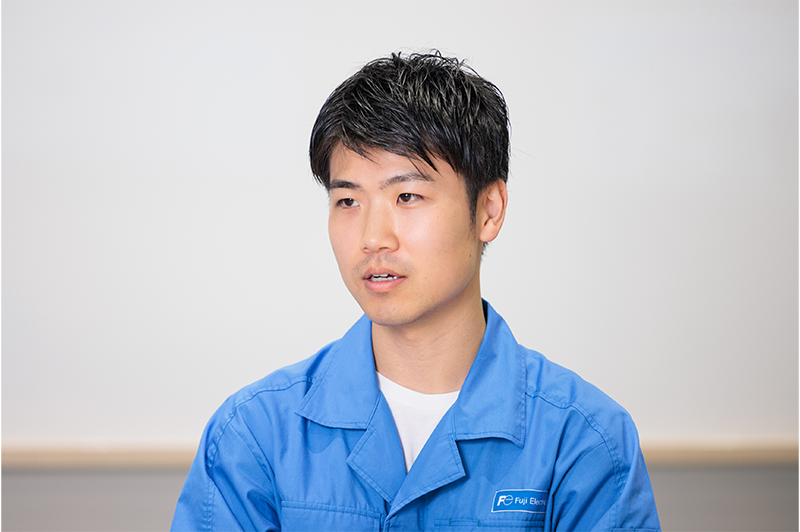
“The development process is rewarding because you can see how the final product will be used by customers and how it will benefit them,” Mr. Sato says.
Realistic evaluations are now becoming feasible
AEM water electrolysis is a new technology, and as such, standard evaluation methods have not yet been established for Water electrolysis efficiency, service life, and other indicators. In his second year at the company, Mr. Torai has been tasked with thinking about the electrolysis operating conditions under which evaluations should be carried out while developing technologies.
“The mechanism by which water electrolysis cells degrade is still unclear. At present, we are focusing on clarifying what kind of degradation is occurring based on the results of the experiments. From there, we identify key areas for investigation and take action,” he explains.
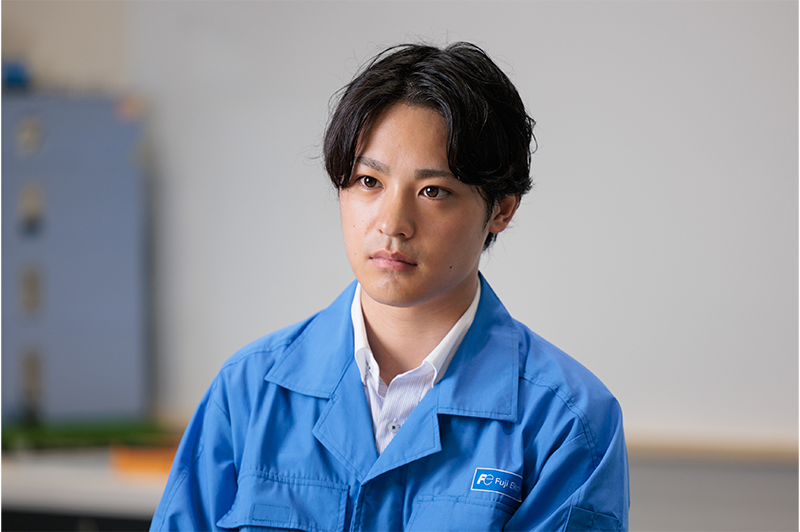
Addressing the challenges of extending service life and increasing reaction efficiency
Along with cell development, technological challenges include extending the service life of the equipment and improving electrolysis efficiency. As a result of joint research by industry-academia collaboration, the team achieved a level of electrolysis efficiency equivalent to that of PEM water electrolysis devices that are already on the market in a lab-sized water electrolyzer designed by Fuji Electric, which is equipped with the latest electrolyte membrane and catalyst.
On the other hand, since AEM water electrolysis is still a new technology, it is not yet clear how the structure of the electrolyte membrane, catalyst, and water electrolyzer affects the reaction efficiency and service life. In order to ensure the reliability of the product, it is particularly important to extend the service life. To this end, a method to verify the service life must be established after clarifying the degradation mechanism.
“To create a product, we need to gradually increase the size of the water electrolyzer. Increasing the size, however, results in areas that are not used for the reaction, which may reduce the efficiency and shorten the service life,” Dr. Hirakata explains. “We will need to do a lot of verification.”
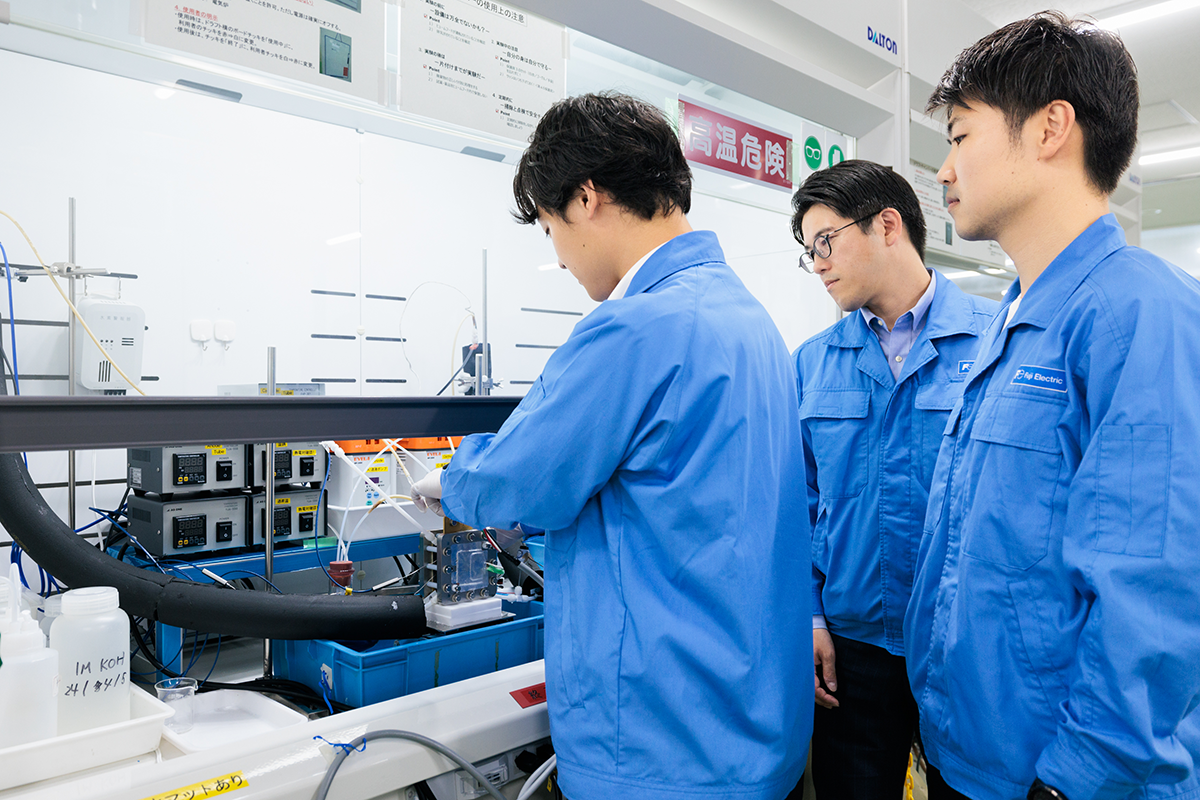
For this reason, the three project members are taking turns visiting partner universities, which are equipped with testing equipment.
"To evaluate the reaction properties and the service life, water electrolysis must be carried out continuously. That's why the three of us work together and take turns going to the university in shifts of about three days and two nights,” Mr. Torai says.
Team members work independently, aiming for product launch in 2030
Successful technological development alone does not lead to the launch of a product. In parallel with technological development, the company is currently planning product specifications in consultation with the marketing department.
Projects that involve the pursuit of new technologies require researchers to think freely.
Having worked to foster a workplace where people can have open discussions, Dr. Hirakata says, “I’ve been receiving a lot of new proposals from these two. Now, my job is to input my knowledge back to the team members and allow them to develop their ideas. I think our biggest achievement is that we have fostered a framework in which each member can work independently, focusing on a distinct sub-theme.” Mr. Sato relates, “The technology is new to the entire world, so we learn new things every day. It feels rewarding to witness my own growth as I accomplish tasks.”
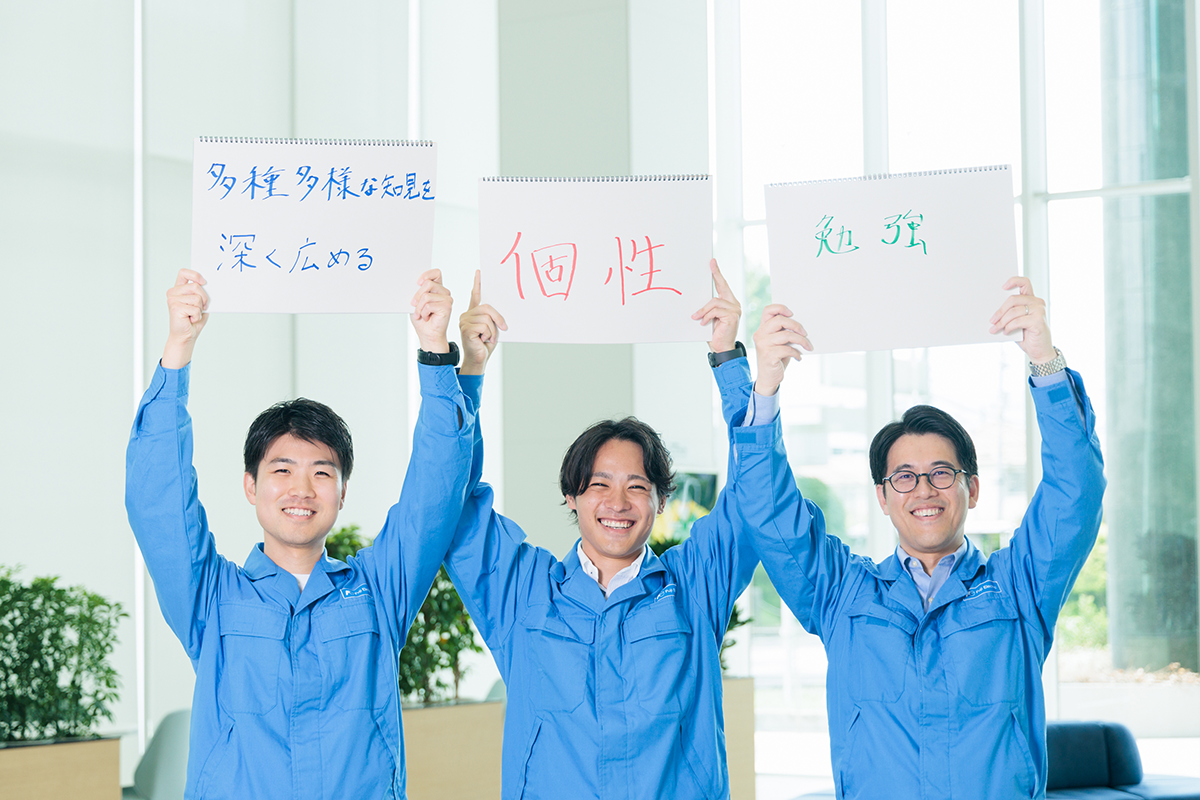
Dr. Hirakata (right) wrote the word “study.” He elaborates, “After joining the company, I continue to study like I did at university.Now, I'm studying not only water electrolysis but also how to be a team leader.”“I chose Fuji Electric because it’s a company where I could make the most of my individuality,” says Mr. Torai (middle), who wrote “individuality.”Mr. Sato (left) wrote, “Expanding and deepening a wide range of knowledge.”He explains that it was through this project that he realized that the quickest way to advance research and development is through steady, methodical progress from the fundamentals.
The technology to produce green hydrogen, the ultimate next-generation energy source, will be a game-changer in the push for rapid decarbonization, enabling local production and consumption of hydrogen at low cost. Development is still in progress, but the goal is in sight. Dr. Hirakata and his team continue their efforts to develop an AEM water electrolyzer with an eye to launching the product in 2030.
Recommended
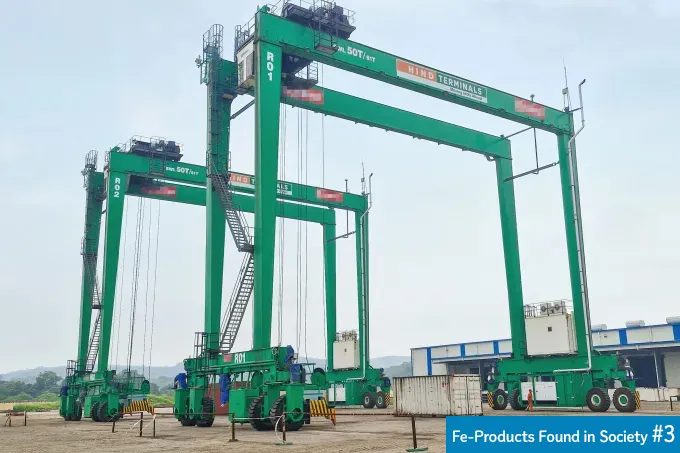
July 30,2025
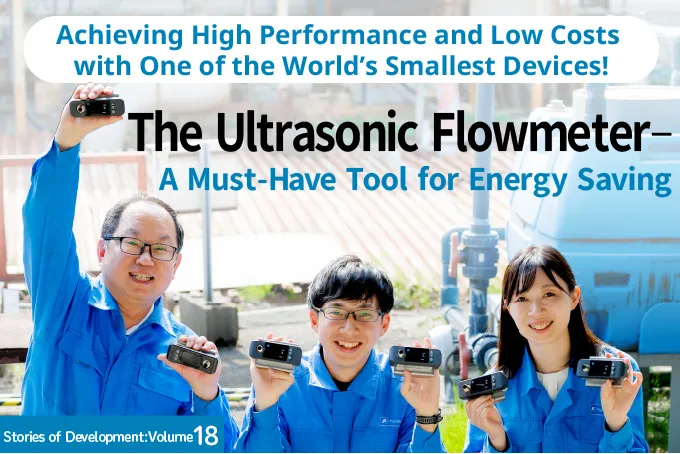
July 28,2025
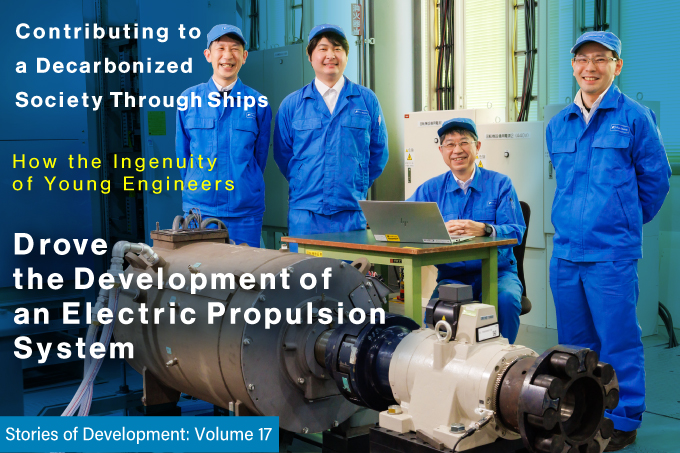
July 7,2025
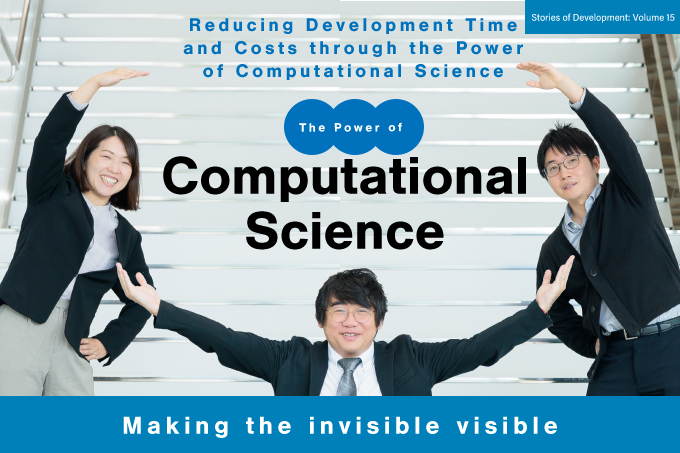
June 27,2025