Developing an Electric Propulsion System to Contribute to a Decarbonized Society Through Ships
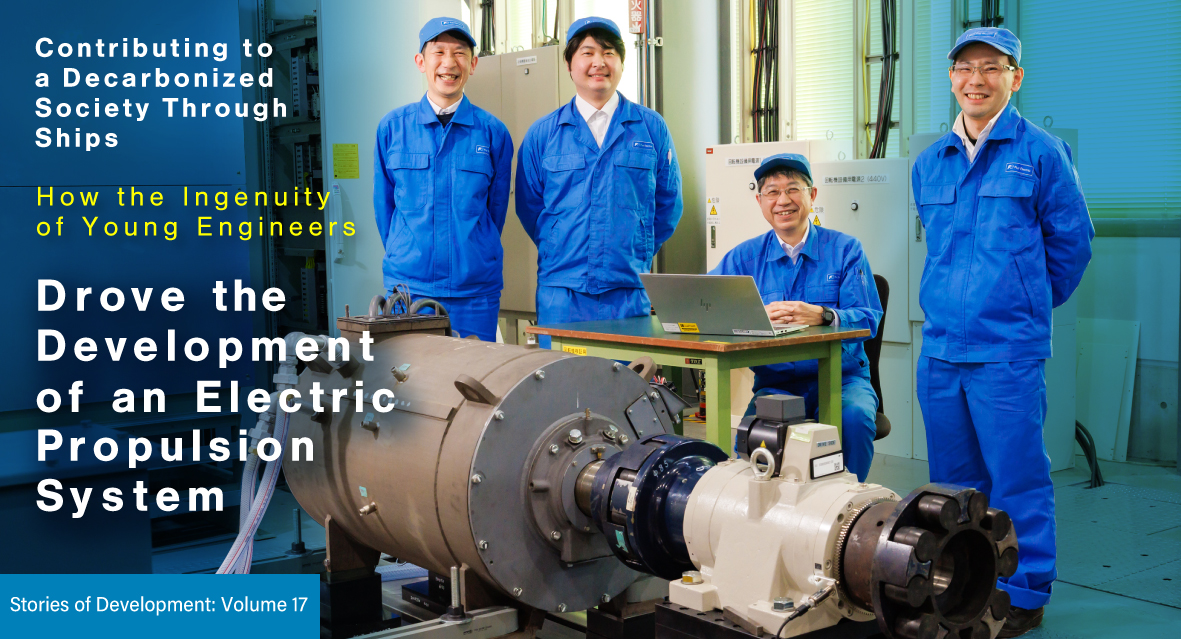
Many ships still run on diesel engines, emitting large amounts of CO2.
Fuji Electric has helped reduce emissions of air pollutants from ships by developing a system that removes sulfur oxides (SOx) from exhaust gas (scrubber).
The Rotary Machine Development Department of Fuji Electric's Development Division (Suzuka Region) is currently working on a completely new electric ship propulsion system. Like electric vehicles, this system does not emit any greenhouse gases.It was the ingenuity of young engineers that became the driving force behind overcoming hurdles in development.
Venturing into uncharted territory without examples to learn from
The brand-new electric propulsion system for ships integrates the electric equipment of the whole ship, such as an inverter, a transformer, and a battery, in addition to a motor. Development began in April 2022.
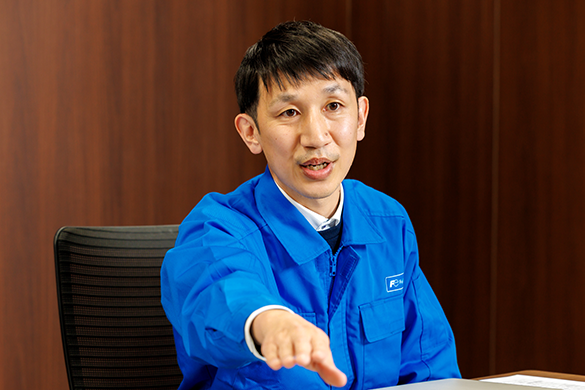
Fuji Electric has a long history of manufacturing ship motors, dating back to the pre-war era. Our motors were used in Fuji, an Antarctic research ship launched in 1965.
But the process of designing the system wasn’t able to begin right away. Mr. Sasamori, who coordinated the development of the electric propulsion system, recalls the early stage of the development process, saying, “The engineers, who had experience in industrial motors, were all at a loss.”
“Before that, we only had to understand part of the ship’s structure because we were manufacturing motors as standalone components. When it came time to develop an electric propulsion system, we realized that we didn’t have a complete picture of the ship,” Sasamori relates.
Understanding how users truly feel by listening to unfiltered customer feedback
Mr. Ito, an experienced engineer, was among those who went into the development process without a clear picture of how the motor would be used in the system.
“As we ventured into uncharted territory without examples to learn from, the shipyard operators, who are our customers, were also grasping for solutions.That's why we decided to hold discussion meetings with shipyard operators and engine and propeller manufacturers, allowing our engineers to hear directly from our customers,” Ito recalls.
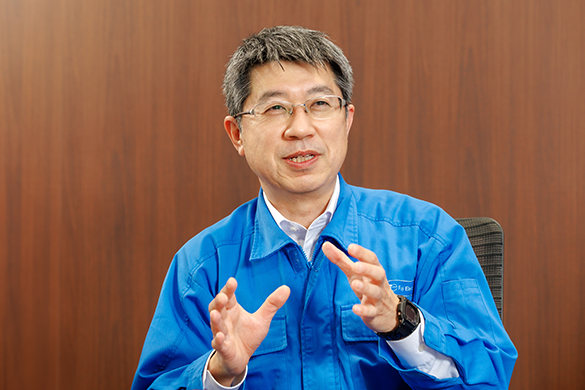
After a year of carefully listening to our customers, the specifications for the electric propulsion system were finalized.Size reduction and power were the top priorities.
In addition, researchers left the laboratory to visit customers (shipowners) in person and identify potential needs.Through frequent discussions, we were able to understand the role of electric propulsion systems on board the ship and how crews (the users) operate and maintain them.
Full-scale development work began in May 2023, a year after the decision to develop the system.
But once again, developing the system turned out to be a difficult task even for veteran researchers.The issue was that there is a trade-off between size reduction and power. Furthermore, it was clear that cooling the motor, which was prone to overheating, would be a challenge.
It was the unexpected idea of two young engineers that resulted in a breakthrough.
Inspiration from a children's TV show
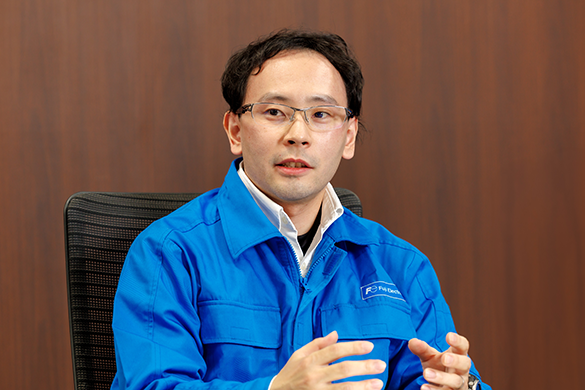
Motors rotate forward and in reverse. If output is to be kept consistent for each direction of motion, the motors cannot be made any smaller. What can be done about this?
One day in July 2023, Mr. Ota, who had been with the company for nine years, was watching TV with his 18-month-old child.
It was a feature about bridges on an educational program for children. One after another, ships passed under the bridge from both sides.While absentmindedly watching the fast-forwarded footage, Ota noticed something. This led to an epiphany.
“Most of the time, ships only move forward. This means we can specialize the ship motor for forward movement.”
By reducing the output for reverse motion and increasing the output for forward motion, the motor can be made smaller while ensuring sufficient forward power. It was a surprising blind spot that no one noticed.
A prototype controlled using unidirectional motors equipped on the left and right sides of the ship was developed and tested in a demonstration trial in the winter of 2023.The trial proved that Ota’s idea increased the output, and the project entered the actual product development phase.
“I realized that by breaking away from conventional ideas and changing my perspective just slightly, I could discover unexpected clues in familiar places,” says Ota.
Visualizing the flow of water using experience from school
At around the same time, Hamada, in his sixth year with the company, was struggling with the motor cooling system.
Generating high power can cause the motor to overheat, which can result in damage or failure of its components.
To address this, water is run through a frame installed around the motor to cool the heat-generating parts.However, this cooling mechanism is costly.
The team had an idea that might increase cooling performance while lowering costs, but there was no way to verify the approach they developed in the analysis.They were not confident that the water would flow through the metal frame as indicated in the analysis. To visualize the flow of water, the team built their own miniature model the size of a lunch box and repeatedly tested it.
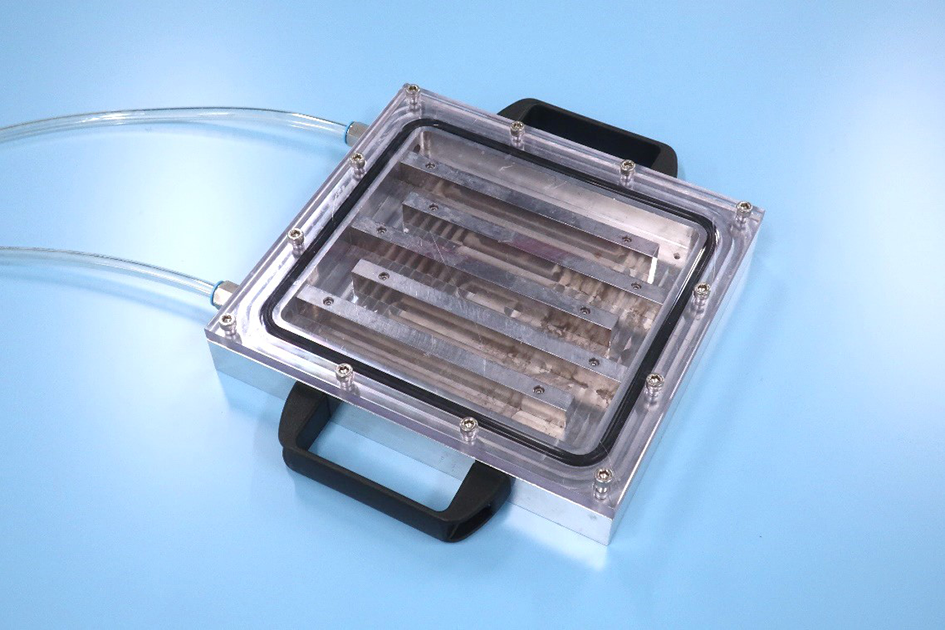
At first, they used food coloring. If the water turned red along the channel, it would be proof that the water was flowing properly. However, when the water was allowed to flow for a while, all the channels became red, making it difficult to tell which direction the water was flowing.
Mr. Hamada, who studied fluid dynamics as a student, had an epiphany. “Maybe we could use the thread we used in our flow visualization research,” he thought.
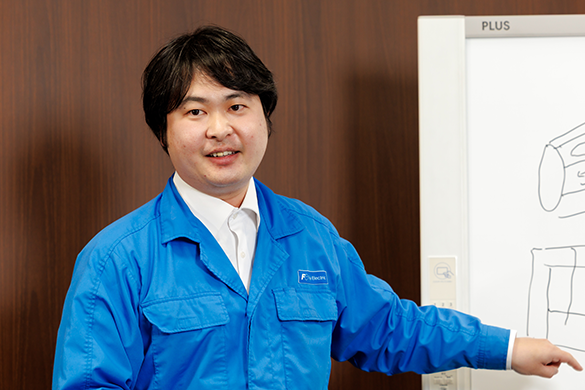
If you stick a piece of paper to the air vent of an air conditioner, you can observe the movement of the paper to see which way the air is blowing. Similarly, if you attach a thread to a partition, the orientation of the thread allows you to visualize the flow.
“As a manufacturer, it's crucial not just to rely on computer simulations, but to provide visible proof that customers can see for themselves. We cannot proceed with development if we are not confident in our data. Visualizing the flow of water using thread was a big step forward,” Hamada explains.
Following this breakthrough, the development process quickly accelerated, and a prototype of the cooling system was completed almost at the same time as the motor.
A foundation for industry-leading performance
With 1.2 times the power density of competing systems, Fuji Electric’s electric propulsion system leads the industry.
At an exhibition held in April 2024, Fuji Electric’s motors were praised for their small size relative to the power.
Backing the ideas of young employees resulted in breakthroughs in development. “No matter what you’re developing, you will never know if you’ll succeed until you try,” Ito relates.
“Fuji Electric provides a foundation for others to cover for us even if we fail. So, I want young professionals to keep taking on challenges without hesitation,” Ito says.
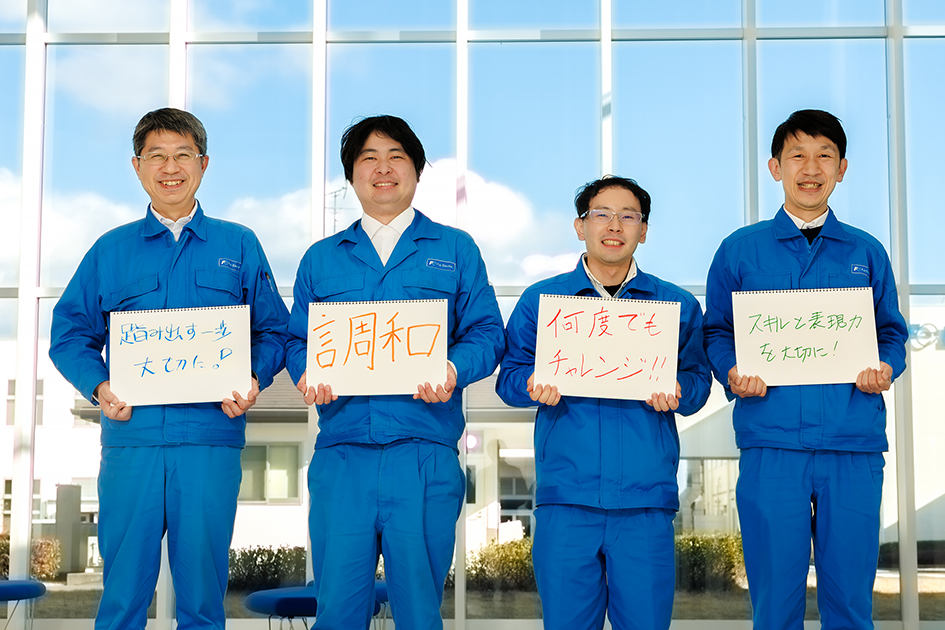
“Big things that you can’t do alone can be accomplished as a team. My message to the students is to ‘cherish the first step.’ We will support you in all your endeavors,” Ito says.
“It’s thanks to the support of many people that we’ve come this far. My message is ‘harmony.’ I came to appreciate how important it is when people from different departments collaborate,” Hamada relates.
“The most important thing is not to give up. People make mistakes all the time, but my message is to ‘keep trying.’ I want to keep creating new things in this spirit,” Ota says.
“People tend to think that engineers only talk about technical matters, but my message is to ‘embrace skill and expression,’ which are what allow us to listen to the needs of customers and promote the products we create,” Sasamori says.
“We are first aiming to launch the product so that our sales staff can start accepting orders in April 2025. We also have the advantage of having achieved industry-leading performance, so we have high expectations,” Sasamori says.
The technology also has potential applications beyond ships. One example is heavy construction equipment. The core is already in place.If we can achieve output densities that deliver sufficient power even in the harsh environments of construction sites, widespread adoption of electric control systems will no longer be a dream.
The frontier team behind the development of an unprecedented product continues to take on new challenges, with younger and more experienced members working hand in hand.
Recommended
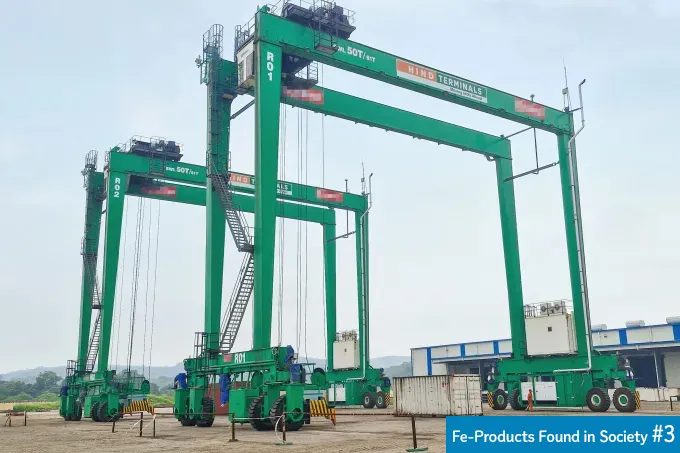
July 30,2025
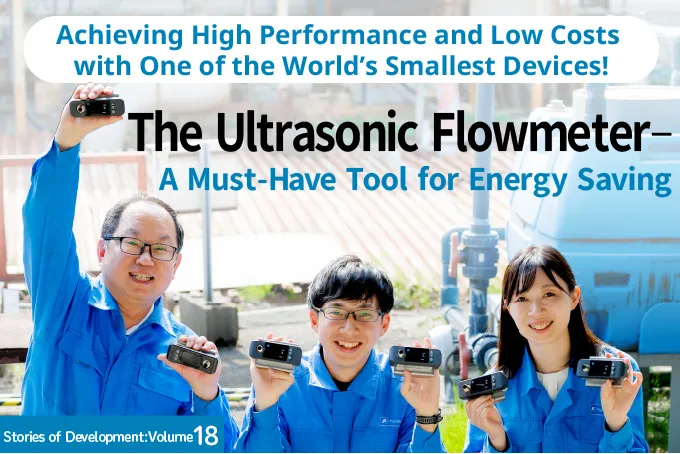
July 28,2025
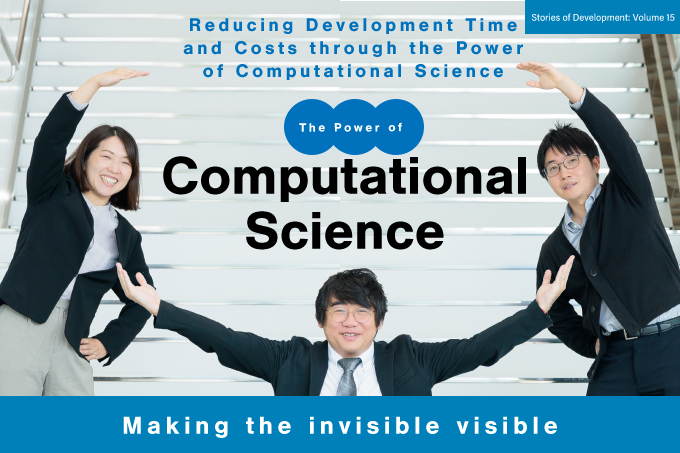
June 27,2025
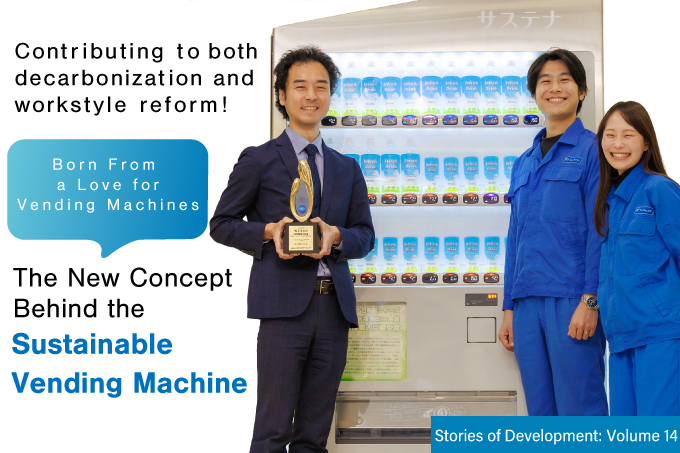
May 13,2025