With a Steam-Generating Heat Pump, It’s “Mission: Possible”! Let’s Speed Up Decarbonization!
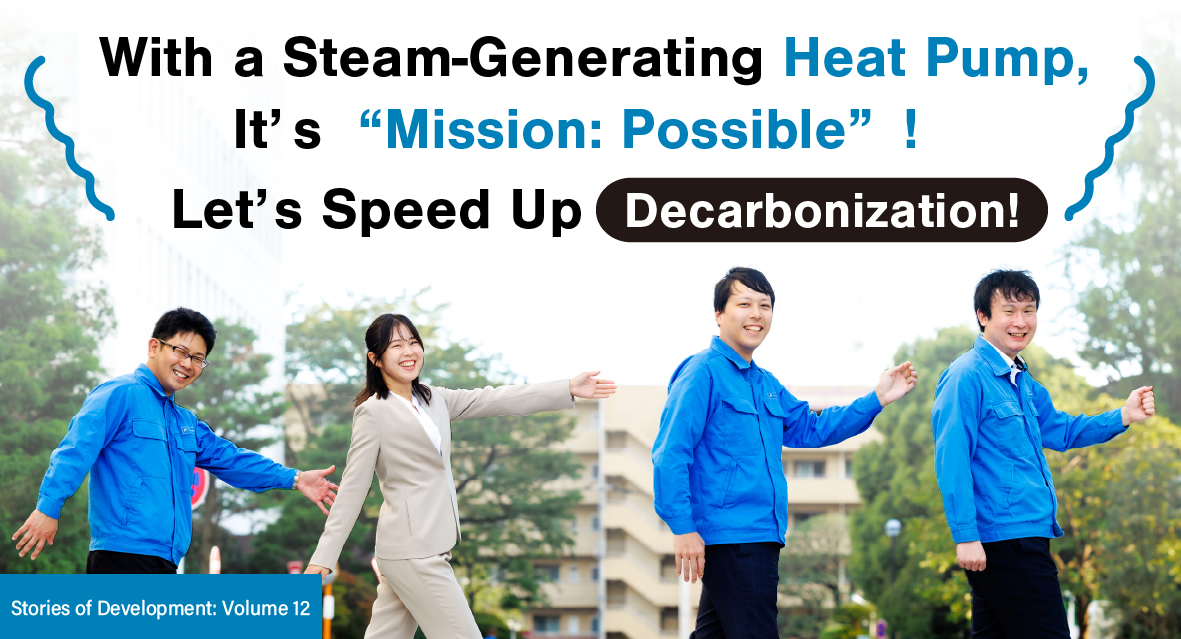
Whether it's conserving electricity or using renewable energy, companies are using various methods to work toward decarbonization. However, many of those in charge seem to believe that they have done everything they can to reduce energy consumption.
To address this issue, Fuji Electric has launched a new steam-generating heat pump (hereinafter referred to as a “heat pump”). We spoke to four employees about the appeal of heat pumps, as well as their ongoing projects.
Reducing CO2 emissions and fuel costs at the same time
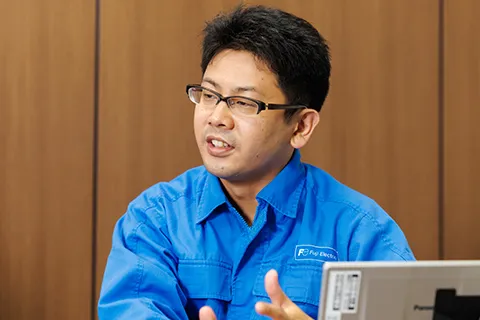
Many companies attempting to decarbonize begin cutting power consumption by, for example, reducing the amount of time that lights are kept on in factories and offices. Then, they change their sources of energy. What role does a steam-generating heat pump play?
"A heat pump is, in a nutshell, a device that recycles energy," explains Mr. Nakano, who is spearheading the development efforts.
Large amounts of wastewater are generated at factories and other production facilities. According to ordinances and other regulations, high-temperature wastewater must be cooled to 40°C or below before disposal. A steam-generating heat pump recycles the heat energy of this hot wastewater.
For example, soft drinks are heat-sterilized in sealed containers, and boilers are commonly used to generate the steam for this process. Fossil fuels are used in the process.
“The use of heat pumps makes it possible to reduce boiler usage, thereby reducing CO2 emissions and fuel costs,” says Mr. Nakano.
Heat pumps also contribute to energy conservation. While boilers are required to be located in a boiler room under the Fire Service Act, heat pumps don’t burn fuel and can therefore be placed near the items they are heating. This makes it possible to reduce the heat loss that occurs when the steam is transported through pipes.
Expanding the range of applications when reaching 150°C
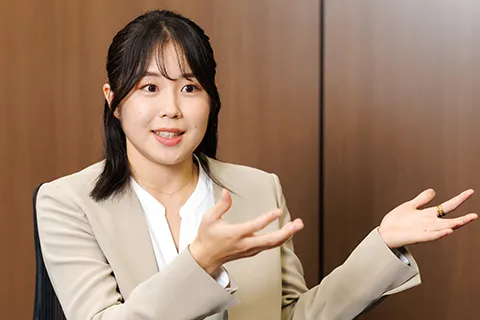
Since 2016, Fuji Electric has been selling heat pumps that generate 120°C steam. Now, it is developing a model that can increase the steam temperature to 150°C.
“Reaching 150°C would enable sterilization and degreasing in addition to the existing cleaning capabilities," explains Ms. Katayama, who is promoting new business initiatives as a sales representative for the Chubu Area Operation.
For example, when applied to the beverage sterilization process, the model under development was estimated to reduce CO2 emissions and energy costs by 40%. Heat pumps are also useful in the chemical, semiconductor, and food and beverage industries, where they are used in processes to clean plant equipment, distill chemicals, and humidify clean rooms that require electrostatic protection.
Moreover, a 150°C heat pump heats objects faster than a 120°C heat pump. In addition, the 150°C heat pump features increased steam pressure, eliminating the need for the pressure-boosting equipment previously required with the 120°C heat pump to deliver steam through the pipes. This enables installation costs to be reduced in some cases.
“Many people are not aware of heat pumps, so even the 120°C models have drawn interest. But the 150°C heat pumps, which have the potential to expand the range of applications and reduce costs, are attracting so much attention that some customers have been waiting for their release," Katayama says.
Development efforts advancing into uncharted territory

Mr. Sugihara, who is in charge of circuit design and the development of the compressor, a core component of the heat pump, relates, “The research itself started in 2015, but it wasn’t all smooth sailing.
At the time, the momentum toward decarbonization was not as strong as it is now, and we had to overcome several challenging technical hurdles, such as developing the compressor.”
The underlying technology originated in vending machines, an area where Fuji Electric dominates the market in Japan.
Vending machines are able to heat and cool drinks efficiently by controlling the compression and expansion of refrigerant through pipes in an effective manner.
Compressor control and other technologies cultivated in vending machine development have been applied in the development of these heat pumps. The temperature of beverages heated by vending machines is between 50°C and 60°C, but the, heat pumps used in factories require much higher temperatures. For this reason, the devices and components used on the inside are completely different. There is no precedent that can be relied on. As such, development efforts are advancing into uncharted territory.
“First of all, we need to find parts that can withstand the high temperature of 150°C, so we are currently working with manufacturers to select components," Mr. Sugihara explains.
As the temperature increases, the size of the heat pump body also increases.
“Factories are lined with large amounts of equipment, and there are restrictions on where the heat pumps can be installed, so we are devising a design that allows them to fit within the dimensions determined through research by our marketing department," says Mr. Sugihara. Without a pause, Mr. Nakano adds, “The piping is laid out in such a complex, winding arrangement that it makes you wonder how they came up with such a design. The hard work and ingenuity of Mr. Sugihara and the other design members really shine through."
An unconventional, “All Fuji Electric” development approach
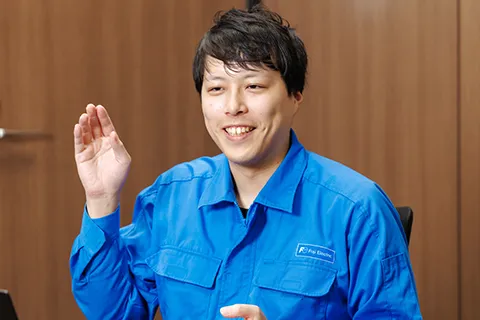
The development of this heat pump is following an unprecedented approach within Fuji Electric.
Project members include Mr. Sugihara of the Mie Factory, where vending machines are developed, as well as Ms. Katayama, a sales specialist from the Chubu Area Operation. The Kobe Factory is tasked with designing the chassis, while employees from the Tokyo Factory coordinate the project. Development efforts are being carried out through an “All Fuji Electric” approach.
In charge of the structure of the heat pump and the design of the information control panel (designing the control panel’s specifications, selecting components, and determining their layout to ensure proper machine and equipment operation) is Mr. Ozeki of the Tokyo Factory.
"In this project, our goal is not just to sell heat pumps as a stand-alone product. We also want to offer a complete solution that includes other equipment and systems as an ‘energy management system’ that meets customer needs,” he explains.
Even within Fuji Electric, different factories use their own components and procurement channels. However, if mass production is the goal moving forward, the conventional approach will not work.
“We are keenly aware of the need to fundamentally change our approach to manufacturing at the Tokyo Factory,” says Ozeki.
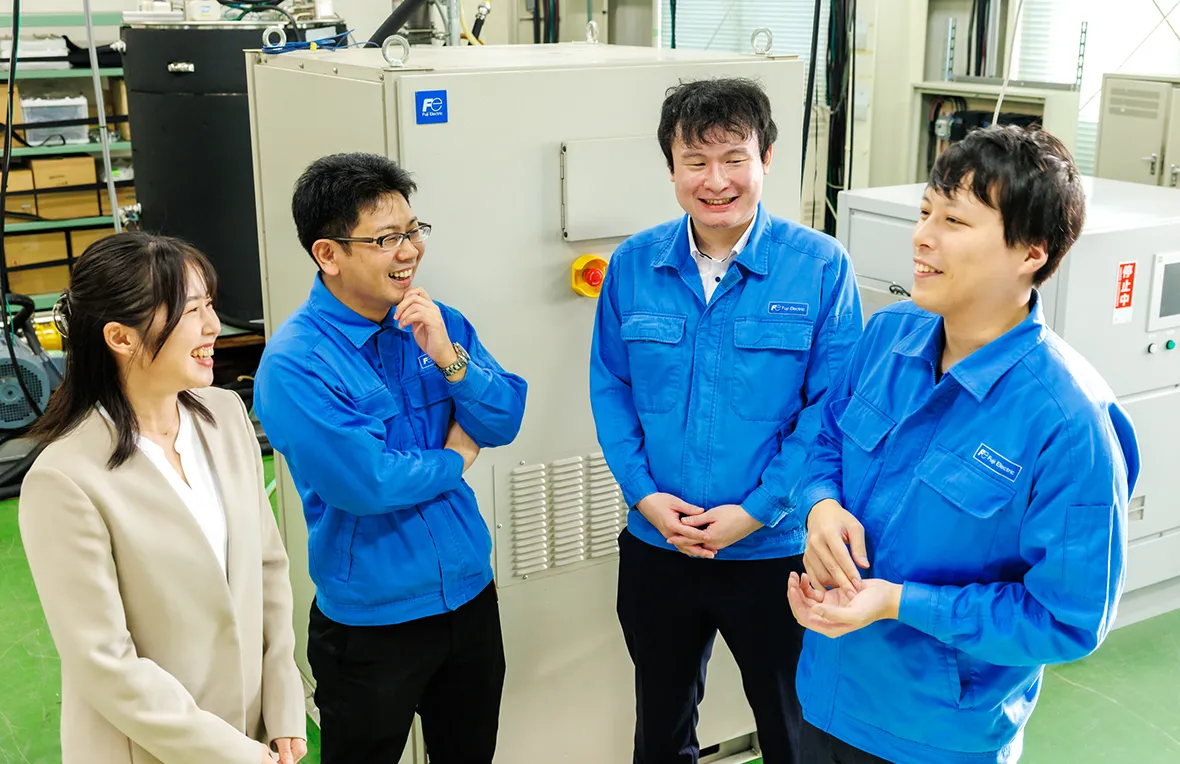
Aiming for launch in 2026
The 150°C heat pump is now in the first stage of prototyping.
Whether it’s the selection and procurement of materials, the constrained conditions of the design work, or the total production of the system, there may be one or two more hurdles to overcome before completion. However, the project members are very positive.
"Until now, the compressor, the core component of the heat pump, was procured from a German company. This time, however, we are developing the component with a partner company. The in-house development of the compressor will have a significant impact on the success or failure of this project. For Fuji Electric, which has dedicated many years to heat pump development, this represents a long-awaited achievement,” Mr. Nakano explains.
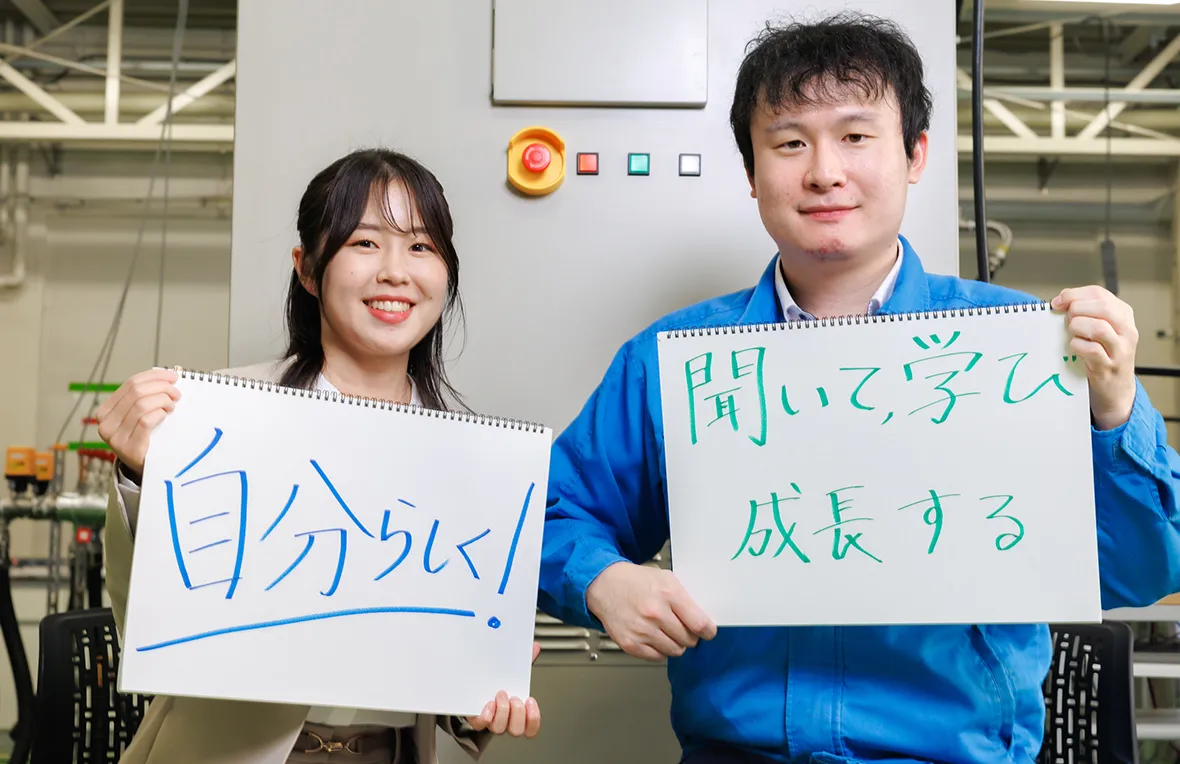
“I want you to value your individuality as a salesperson so that people will think, ‘I want to buy Fuji Electric products from this person,’” says Ms. Katayama (left). Mr. Sugihara (right) says, “You can't keep relying on others for answers. It’s important to learn and grow from each experience.”
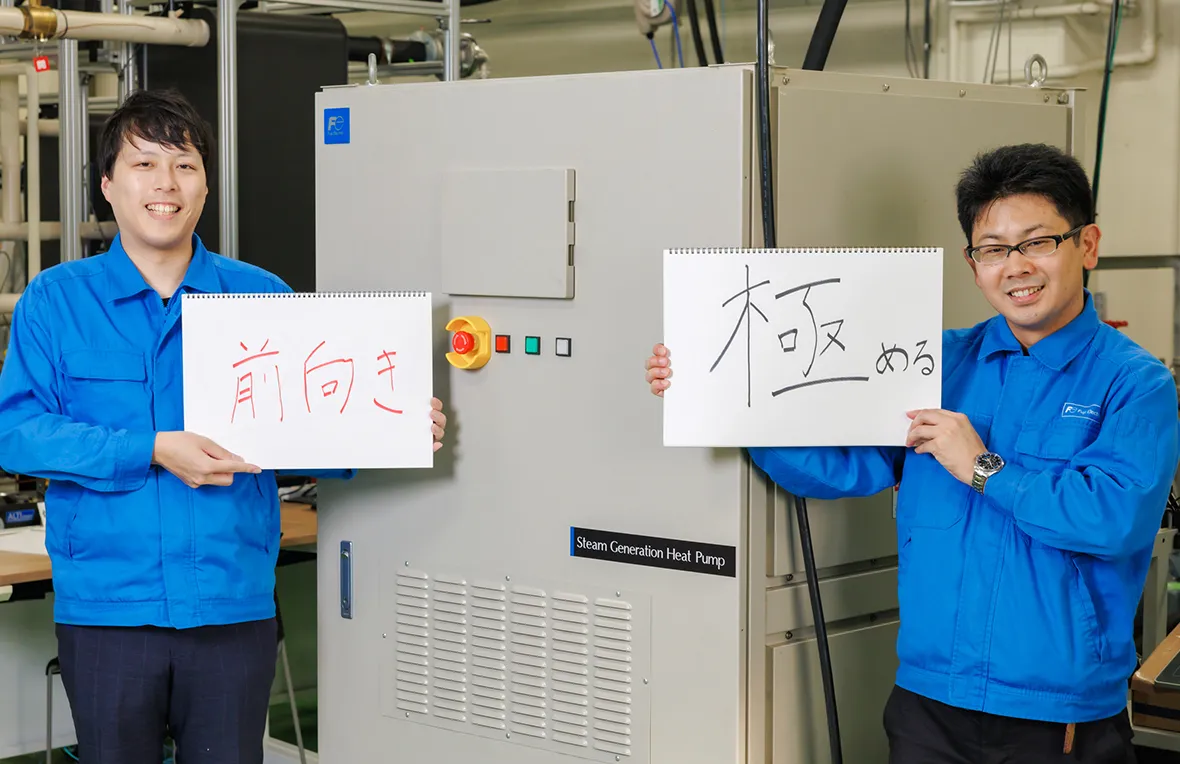
Scheduled for launch in 2026, the 150°C steam-generating heat pump represents a new approach in the effort to achieve a decarbonized society, and the development process is set to reach a critical stage in the near future.“Right now, we're just trying to solve the problems that are right in front of us, one by one.”The four project members nod in agreement.
Recommended
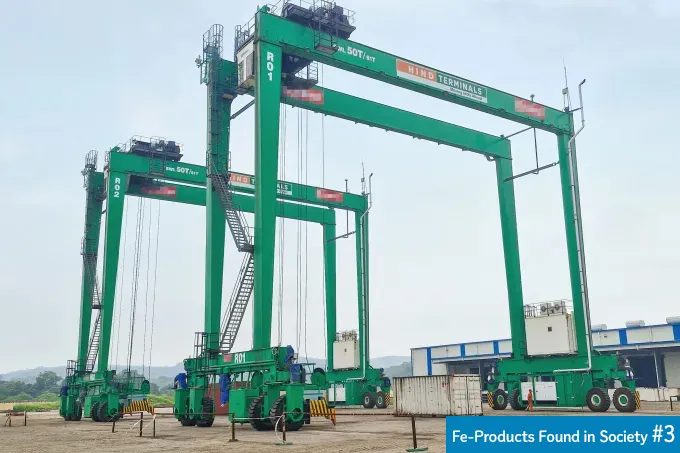
July 30,2025
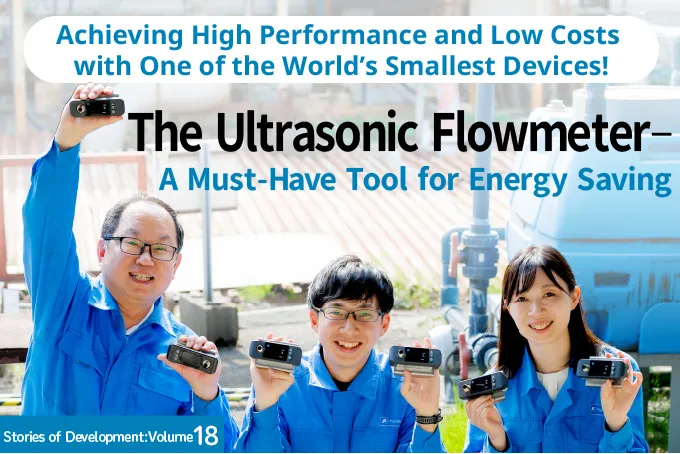
July 28,2025
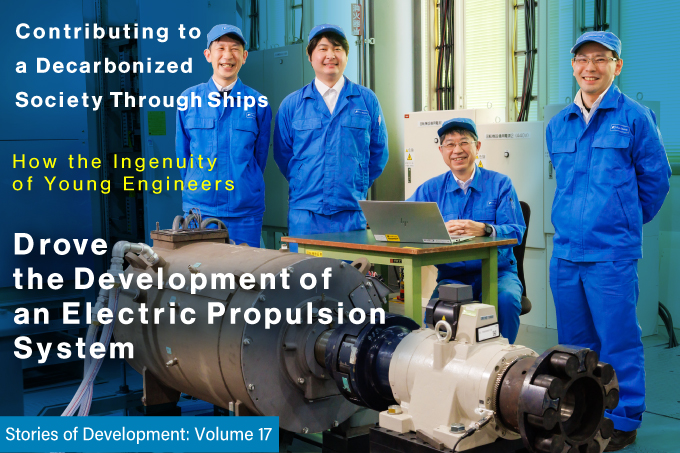
July 7,2025
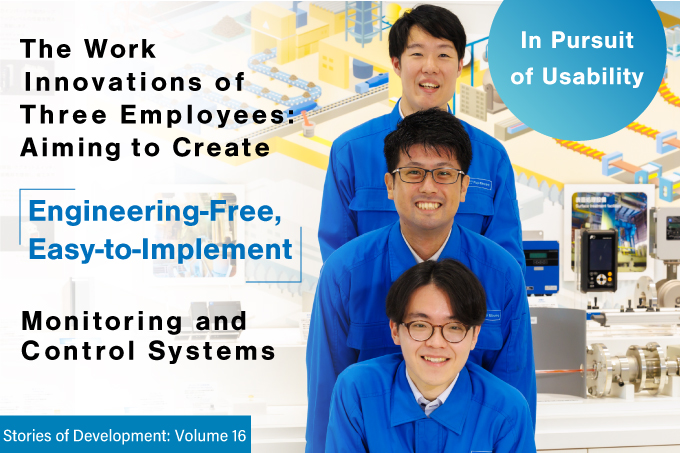
July 2,2025