Mass Producing 8-inch Power Semiconductors in Malaysia
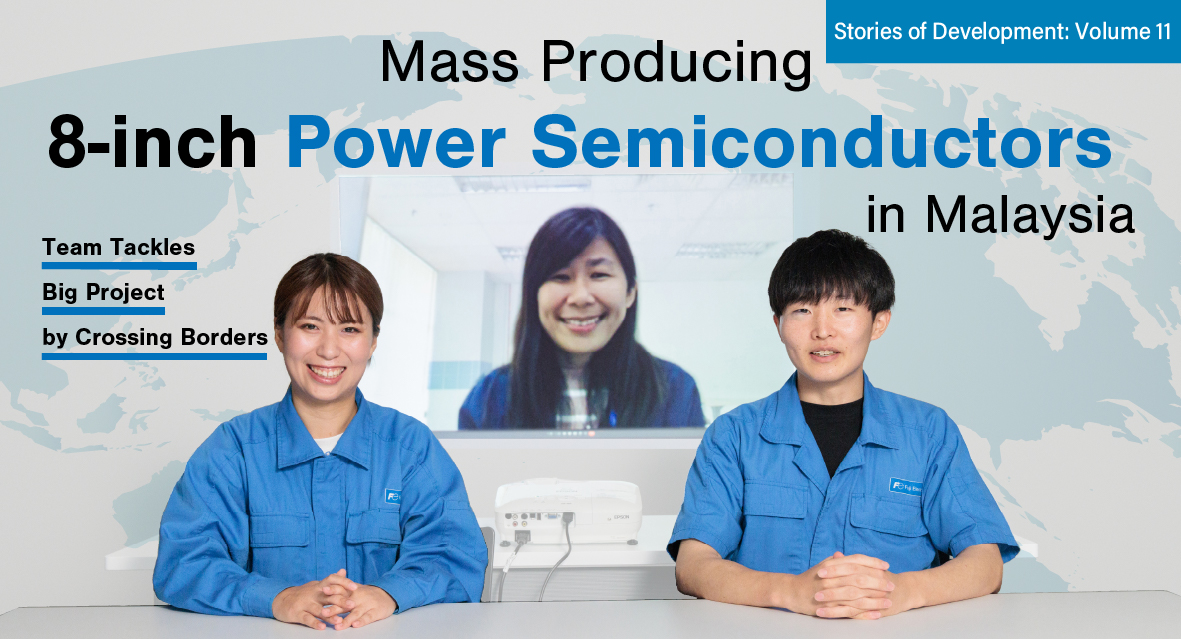
Fuji Electric began producing 8-inch wafer power semiconductors for overseas markets at its Malaysia Factory in fiscal 2023. Up until then, the factory had been producing 6-inch wafers, but with the demand for power semiconductors growing worldwide, Fuji Electric decided to increase production in Malaysia from the perspective of local production for local consumption. Since then, there has been a rapid transfer of technology between Japan and Malaysia for the applicable products. However, the transfer process encountered many difficulties including language barriers.
We interviewed two talented young engineers who assisted in the transfer, as well as a local staff member who works at the Malaysia Factory.
Transfer of industrial power semiconductors in just 18 months
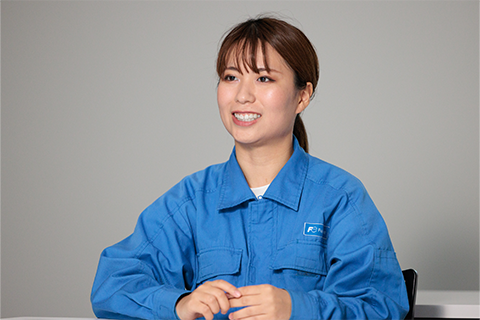
The Malaysia Factory was established in 1996 as a production factory for aluminum and glass substrates for HDDs, and began producing 6-inch wafer power semiconductor chips in 2010. After discontinuing production of aluminum and glass substrates in fiscal 2021, Fuji Electric invested approximately 50 billion yen in 8-inch wafer facilities in order to meet the growing market demand for power semiconductors. In January 2022, the transfer process began with 8-inch industrial power semiconductors. Because the manufacturing equipment and processes for 8-inch wafer power semiconductors are very different from those for 6-inch wafers, which have been conventionally produced at the Malaysia Factory, local staff needed to be fully trained starting from the basics.
The deadline for the transfer was July 2023. It was necessary to start up the production line as soon as possible in order to respond to the expansion of the semiconductor market. It was an exceptionally fast process that took about a year and a half, and it included building renovation work.
Ms. Kamidaira, who develops and designs power semiconductor chips, and Mr. Okawa, who was in charge of transferring domestic manufacturing processes, both joined the company at the same time in 2020. Ms. Kamidaira worked on industrial power semiconductors and Mr. Okawa on automotive power semiconductors, but this was the first time for them to work on transferring manufacturing processes to an overseas factory.
These two young engineers were assigned the mission of setting up a mass production system for 8-inch power semiconductors at the Malaysia Factory.
Ms. Kamidaira remarked, “I knew there was talk about transferring processes to the Malaysia Factory, so I remember thinking, ‘It’s finally time to do it.’ Since we only had about a year and a half to complete the project, I remember working backwards through the project phases and calculating that we only had about five months for prototyping and evaluation. Everything was much more hurried than usual.”
The first step was the transfer of technology for industrial power semiconductor chips. There were a total of 30 product types that needed to be transferred this time, and all of them had to be verified. This was the first time that so many types had been transferred at one time.
It usually takes about two months per one type just to test the durability of chips. Ms. Kamidaira sorted the 30 types based on their chip design differences and identified the points of concerns and items of evaluation for each. Moreover, she cooperated with the Quality Assurance Department and other departments to identify items prone to characteristic variations based on past experiences, and by focusing on these items for preliminary evaluation testing in Malaysia, she succeeded in shortening the time required for the prototype manufacturing process.
Ms. Kamidaira commented, “There was considerable pressure to transfer a large number of product types within a tight deadline. It was definitely a race against time. I felt relieved when we completed the production line and were able to perform the entire manufacturing process in Malaysia.”
After transferring the industrial chips, it was then necessary to transfer the automotive chips. To help facilitate the transfer process, Ms. Kamidaira shared all of her experiences and knowledge with Mr. Okawa, who was in charge of the automotive chips.
Solving production problems through regular remote meetings!
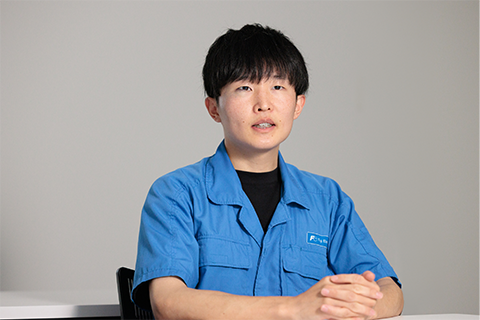
It was decided in February 2023 that automotive power semiconductors would be transferred to Malaysia. Mr. Okawa began working on the transfer in July 2023.
The transfer of automotive power semiconductor chips was more difficult than that of industrial chips because their structure is more complex and the processing requires more delicate engineering techniques. Initially, Mr. Okawa exchanged emails about wafer processing conditions with the local staff at the Malaysia Factory, but language barriers hindered progress.
Mr. Okawa recalled, “We were unable to convey our intentions to the local staff by email alone, and miscommunication sometimes caused work to come to a standstill. I sensed the need for direct communication, so we decided to hold weekly remote meetings starting in February 2024.”
This decision proved to be a good one as it prevented a major accident from occurring in the early stages of the transfer. Information sharing at remote meetings helped them quickly identify a problem in the manufacturing process of the automotive power semiconductors. After discovering the problem, Mr. Okawa immediately convened a meeting of relevant staff from Malaysia and Japan. They confirmed and ensured proper handling and setup of equipment specific to automotive applications.
Furthermore, Mr. Okawa shared his expertise in the transfer of manufacturing processes in Japan by pointing out conditions that are likely to cause defects, as well as countermeasures to improve the quality of products.
He once received a lengthy email from a local staff member during the transfer process. It was a question related to the characteristics of chips, which made him surprised that they studied in such specialized details.
Wafer fabrication is an extremely delicate technical process, and even the smallest dust particles can cause defects. Local staff understood that rigorous daily controls are required and were meticulous in their handling of processing equipment.
Mr. Okawa remarked, “The local staff had to work very hard during the transfer. The enthusiasm of the staff members really inspired me.”
Enthusiasm of local staff who support the factory
Ms. Esther Lam is a local staff member of the Malaysia Factory who joined Fuji Electric Malaysia in 2007. She was involved in the launch of the mass production of 6-inch wafers in 2021 and 8-inch wafers in April 2023, and has also been engaged in quality monitoring of products for automotive applications.
Since there are differences in the fabrication processes of 8-inch wafers, and because customer certification standards for automotive applications are stricter than those for industrial applications, local staff members came to the Matsumoto Factory in Japan in May 2023 to learn about quality control and customer service for 8-inch wafers.
This was the first time Ms. Esther Lam had the opportunity to be involved in the quality control of 8-inch wafers and automotive power semiconductors.
Ms. Esther Lam commented, “When I learned how to perform quality control inspections at the Matsumoto Factory, I really focused on what to do when defective products are detected and how to respond to them. Currently, we still make use of what we learned in the training when we encounter defective products during testing, such as what we should do next to verify areas that do not meet the standards, and what our response flow should be afterwards.”
The Malaysia Factory also has a new Customer Service Department where Ms. Esther Lam responds to customer audits. This is obviously a task that she never experienced before, but she is overcoming challenges one at a time by exchanging information with Japanese staff members when necessary.
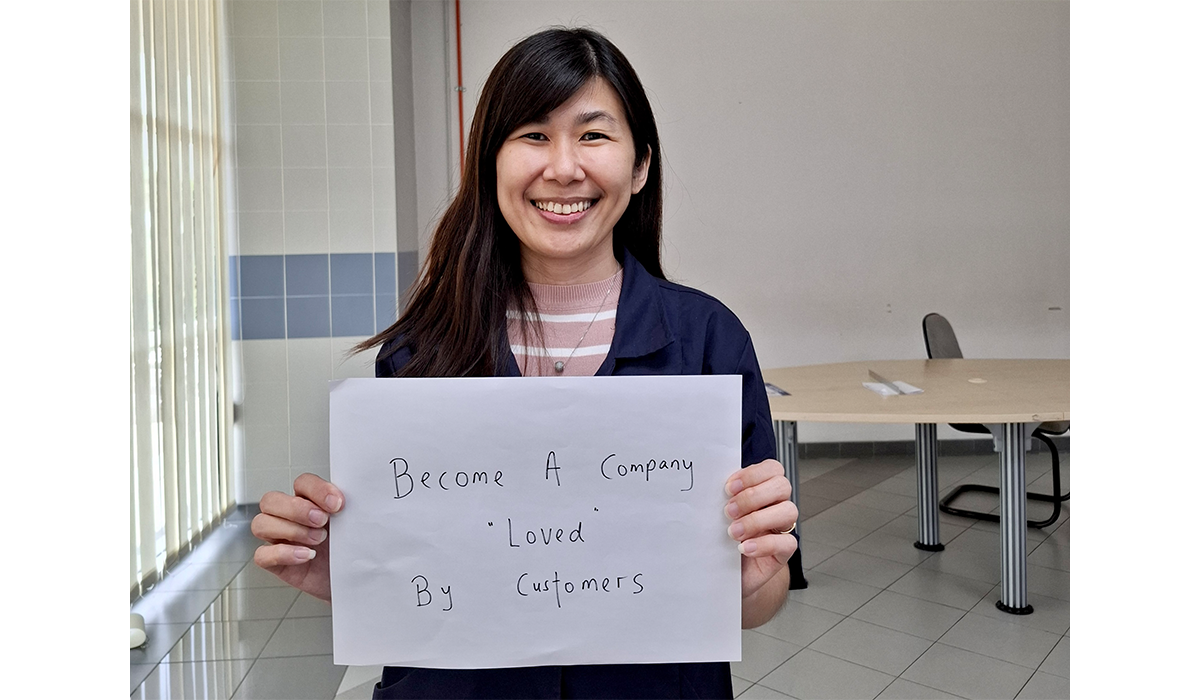
We will increase production capacity at the Malaysia Factory to meet the growing demand for semiconductors worldwide.”
A globally connected project
This big project was successful because the team crossed national boundaries. Malaysian and Japanese staff members respect and collaborate with each other to produce high quality products.
Mr. Okawa said, “We valued opportunities to exchange opinions with local staff members and proceeded with the project to transfer technology while respecting each other’s ideas. This enabled us to naturally build a relationship of trust and an environment where it is easy to consult with each other regularly. I believe that this has led to smoother cooperation between us.”
Ms. Kamidaira commented, “Semiconductors are one of Fuji Electric’s core businesses. This line of work is challenging at times, but I feel rewarded when I see the positive sales results and realize that I am making a contribution to the company.”
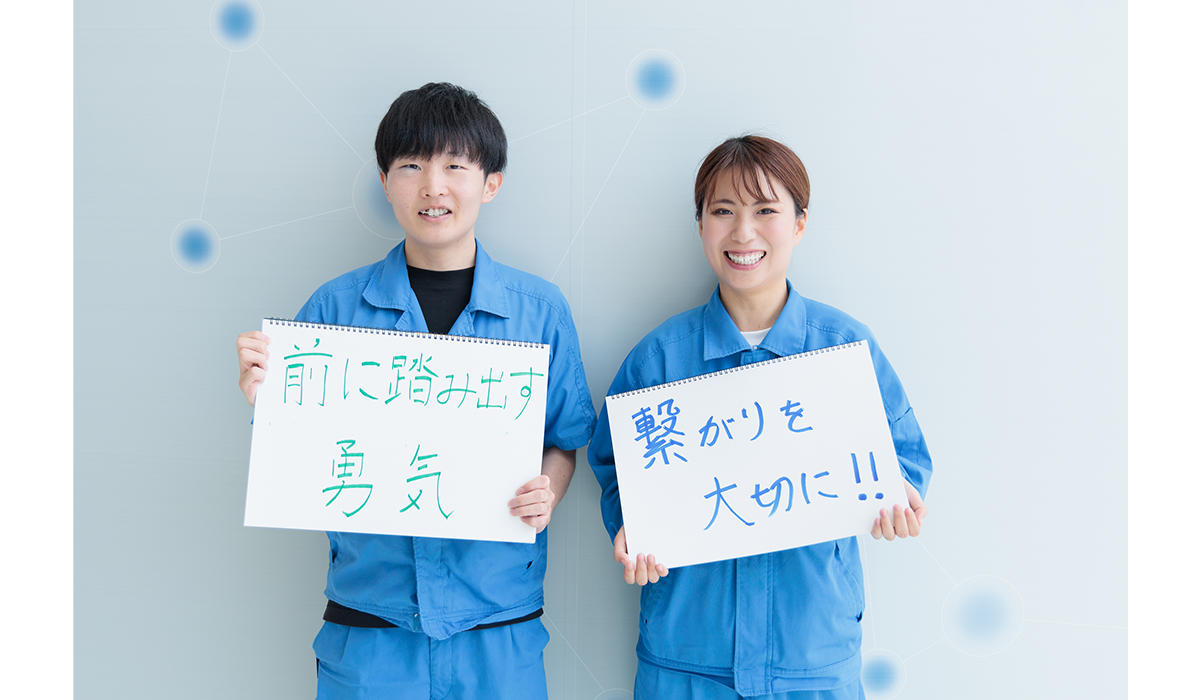
I believe it will strengthen Fuji Electric if we can make the most of lessons learned, both good and bad.”
Mr. Okawa concluded, “I was happy to be able to contribute to such a big and impactful project.
I feel more motivated than ever to achieve my goals and live up to expectations.”
The Malaysia Factory will continue to grow thanks to the enthusiasm of young employees who cross national boundaries.
Recommended
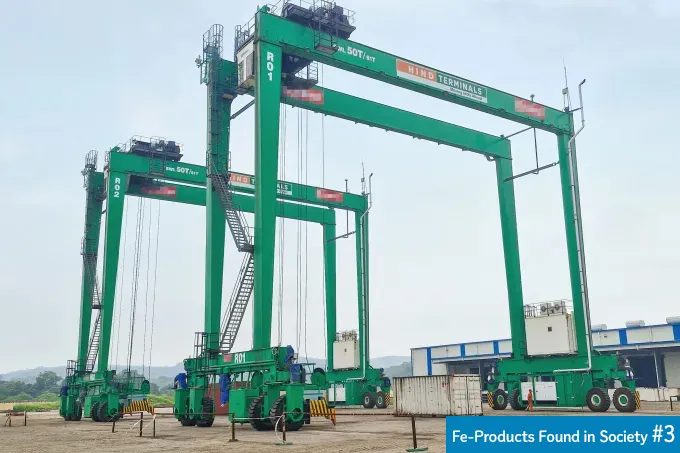
July 30,2025
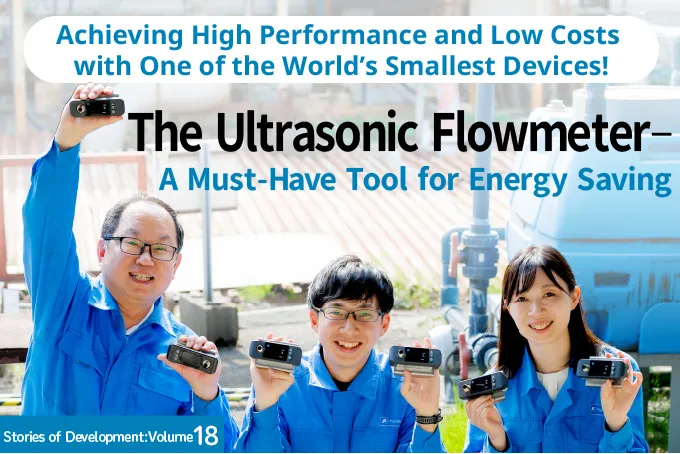
July 28,2025
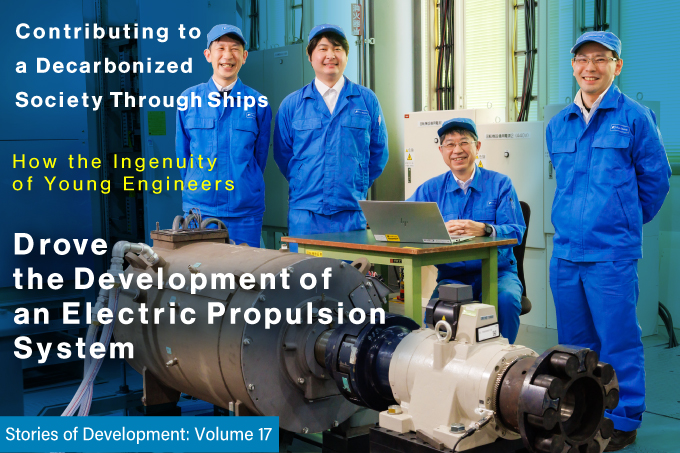
July 7,2025
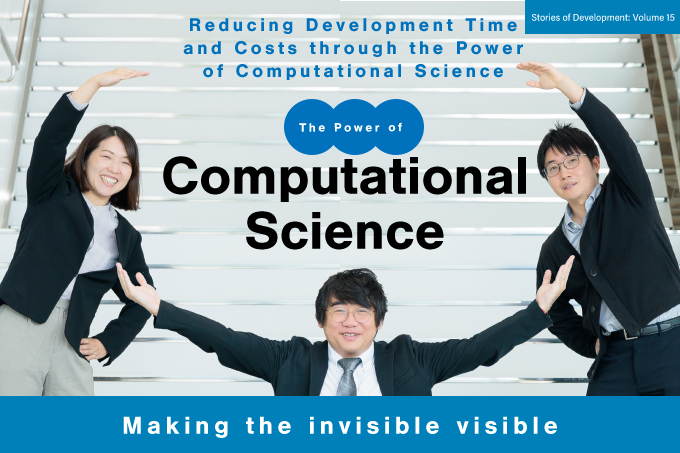
June 27,2025