Sustainability
New Technician Training | Our Contribution Activities to SDGs
Building the Foundation for Technical Employees through One-Year of Training
Updated July 2024. The affiliation and job description are those at the time of the interview
In order to make products that satisfy customers in all aspects, such as quality, price (cost) and delivery time, it is essential to have excellent technicians. Fuji Electric is focusing on developing human resources in manufacturing and has established a residential training center called the Technical & Skill Training Department in Konosu City, Saitama Prefecture as a facility related to the Production Technology Center. A year of attentive training is provided for new technical employees who have just graduated from high school to build their foundation as working adults. We do our best to support the realization of a fulfilling career.
Human development is the starting point of manufacturing
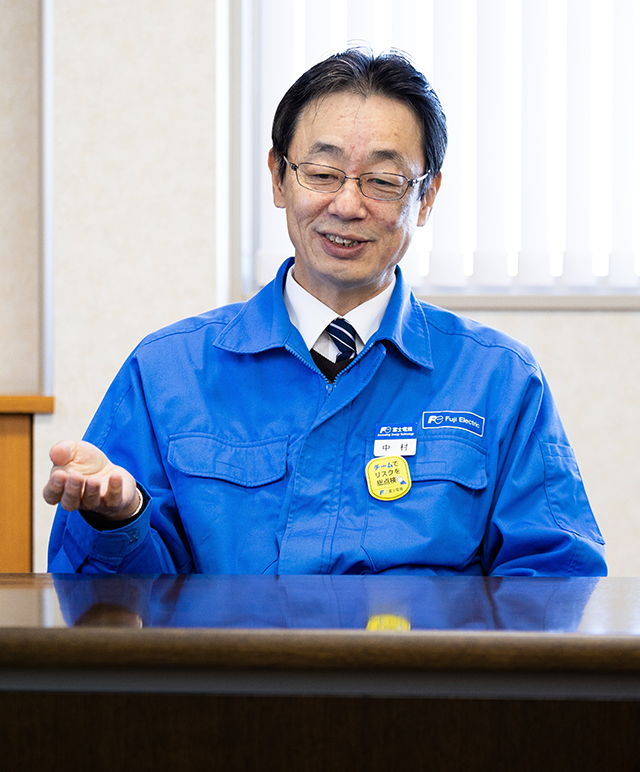
Training for high school graduates at the Technical & Skill Training Department has a long history. The training has continuously evolved over more than 30 years to support Fuji Electric’s quality. Kunihiro Nakamura, General Manager of the Technical & Skill Training Department, explains the purpose and characteristics of the training:
“At the Technical & Skill Training Department of Fuji Electric, we focus on training technicians, and we have established an annual curriculum of 1,650 hours, which exceeds the legal requirement for education hours (1,400 hours). The purpose is not just to acquire the basic knowledge, techniques and skills needed in the workplace. Through dormitory life, daily life guidance, mountain climbing and training at a Zen temple, we help the trainees establish a foundation as a member of society.”
In FY2024, we have 73 trainees. They are divided into five departments, which are electronic equipment, electrical equipment, machine processing, precision processing and plastic working, where they hone their fundamental skills to actively work on shop floors. Nakamura expresses his passion for the training as follows.
“We are looking at human resources development over the medium to long term. If we cut corners on human resources development, there will inevitably be a backlash in product quality. That is why we take great care in training and thoroughly train the minds, skills and bodies of our technical employees. ‘Human development’ is the first step and the starting point of ‘manufacturing’”
Fostering a sense of professionalism in manufacturing
One major goal in the training of the Technical & Skill Training Department is to ensure the trainees acquire the techniques and skills needed to perform smoothly on shop floors. The trainees not only work on acquiring the basic techniques and skills needed in the workplace, such as practical training on basic tasks, safety education, classroom learning on electricity, quality control and production engineering, but also work on obtaining the qualifications required in production processes, such as welding and cutting by machine processing. In addition, the content of the training that takes the place of assignment into consideration is substantial and, Masahiko Asami, Chief Instructor of the Technical & Skill Training Department, outlines it as follows.
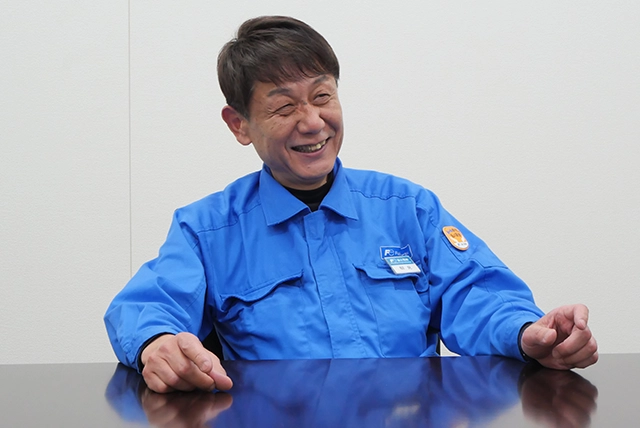
“The trainees are divided into five specialized departments based on the nature of the business of their assigned workplaces and they work on assignments within the time limit. Through repeated practice, they come to be able to complete production within the time limit and achieve accuracy above the passing line
The Technical & Skill Training Department does not consider it sufficient to train the trainees so that they only acquire techniques. Haruhiko Sakamoto, an instructor, says that he wants trainees to learn the spirit at the core of manufacturing through various types of training and practice.
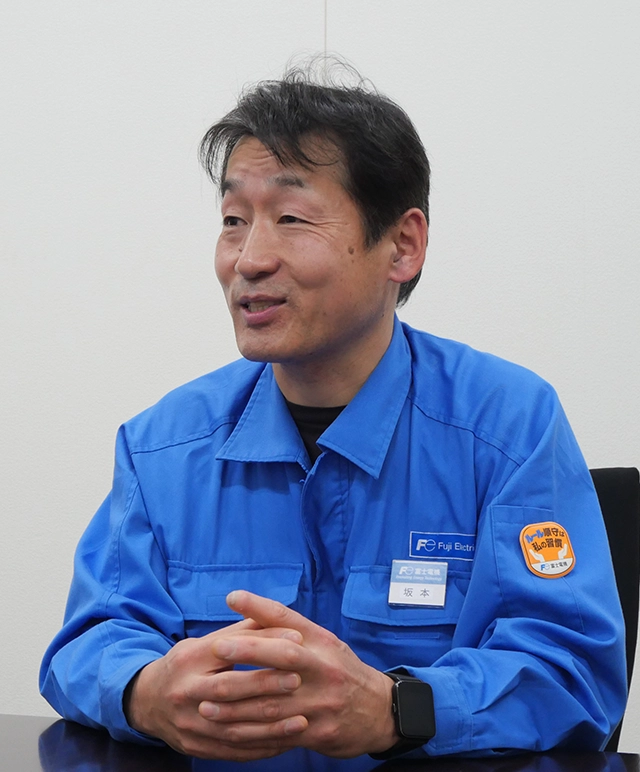
“We place importance on encouraging trainees to have a sense of ‘professionalism’ in manufacturing. Poor quality directly concerns customer safety. That is why it is necessary even in training to continue to refine their skills with the same professionalism that they will use in their work. Some trainees feel discouraged by being unable to get good scores in the practice for the skill check (qualifying exam) but, once they are on the shop floor, they are expected to get perfect scores. In fact, professional manufacturing is whether or not they can go even further. We aim to develop the potential of each individual by giving careful and considerate guidance while also sometimes offering harsh criticism.”
Acquiring the frame of mind that you are a member of society through holistic training
The Technical & Skill Training Department has another mission. That is to provide holistic training for the trainees. The trainees start their day with a morning run and calisthenics, which facilitate the acquisition of a well-regulated lifestyle and good physical strength that enables them to concentrate on their work for long periods of time. There are also unique training items such as team building through mountain hiking and facing themselves through Zen meditation, as well as volunteer activities and overseas tours to broaden their perspective. Asami explains the aim of these activities:
“The trainees have entered the Technical & Skill Training Department after having just graduated from high school, so they still have a lot of growing to do in order to become full-fledged members of society. Training is a job. Their attitude and willingness to engage in training have a major influence on the way they acquire techniques and skills. For this reason, we place great emphasis on daily guidance to ensure that they develop good mindsets as members of society. Their frame of mind is a major factor in determining their subsequent development.”
One of the great benefits of humanity training for trainees is the team life provided by the residential system. Sakamoto explains its benefits:
“After joining the company, the trainees are given roles such as dormitory leader, room leader and group leader. Those roles help instill a sense of responsibility in the team. For example, the dormitory leader is required to set rules such as the use of facilities and to take the initiative in solving any problem that has occurred. During the training period, trainees are also evaluated on their daily lifestyle habits using a point system, and they lose points for tardiness and forgetting items and win extra points for participating in volunteer activities. Giving them a clear evaluation axis increases opportunities for improvement.”
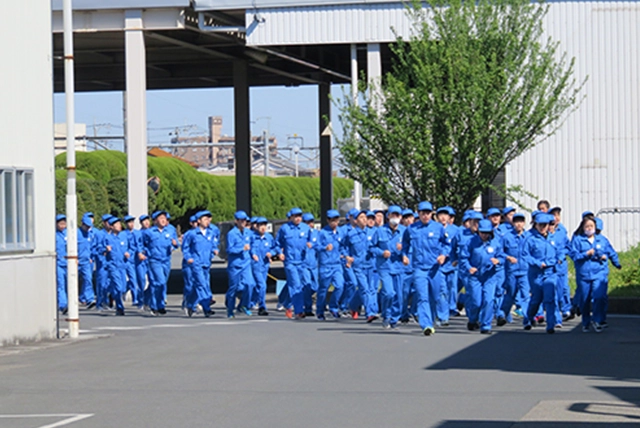
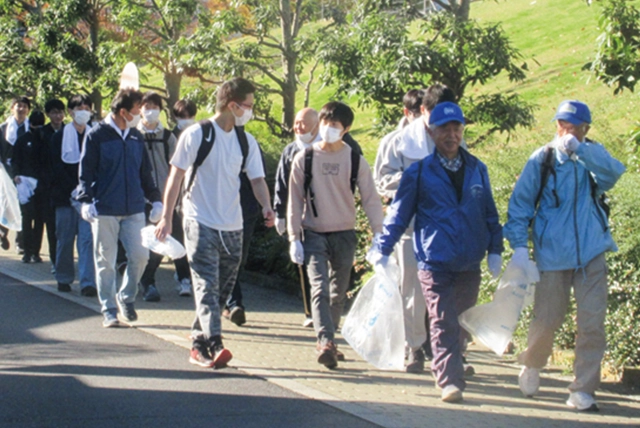
The development of our trainees is the greatest pleasure of all
Manufacturing is based on the development of human resources. We nurture each individual over the course of one year. The training at the Technical & Skill Training Department is the starting point of Fuji Electric’s pride in quality and is the original landscape to the manufacturing floor where products are made by teamwork. The instructors, who have trained many trainees up to now, describe the best part of their job in human resources development as follows.
“When I see their exemplary appearance at the completion ceremony, I feel extremely rewarded. Trainees, who initially could not even do proper greetings, express their gratitude, saying ‘Thank you for taking care of us for a year!’ at the completion ceremony... that is when a sense of achievement as well as relief wells up in me.” (Sakamoto)
“It’s greatly rewarding whenever I see proof of their growth and development in any area. When I hear about technical employees who have left here and are now active on their individual shop floors, I feel happy as if it was about myself. I hope that they will be good supporters of quality and play a role in the future of Fuji Electric.” (Asami)
“In the Technical & Skill Training Department, after passing the skill check, all trainees form teams to work on the graduation assignment. The team members are selected from the five departments in a balanced manner and they use what they have learned while holding discussions with each other to create works that also incorporate a playful spirit .... Every April, I feel the tension of having to take care of new employees for one year, but the moment when I see that everyone has completed their graduation assignment without incident makes me extremely happy.” (Nakamura)
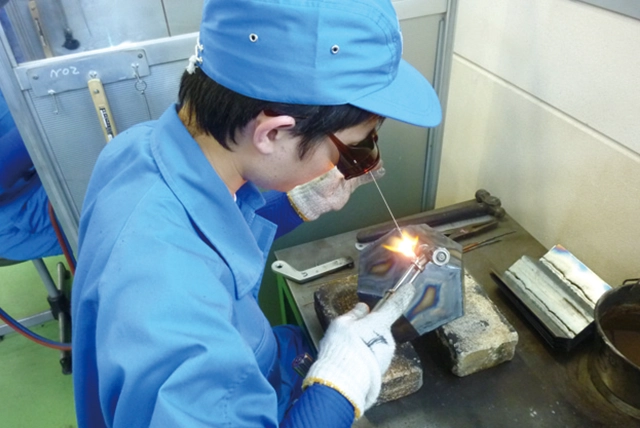
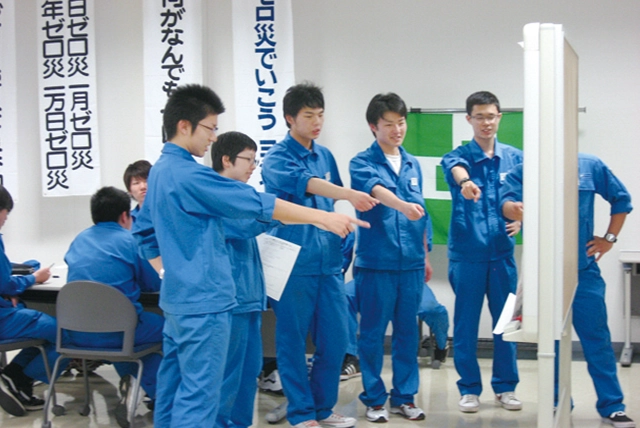
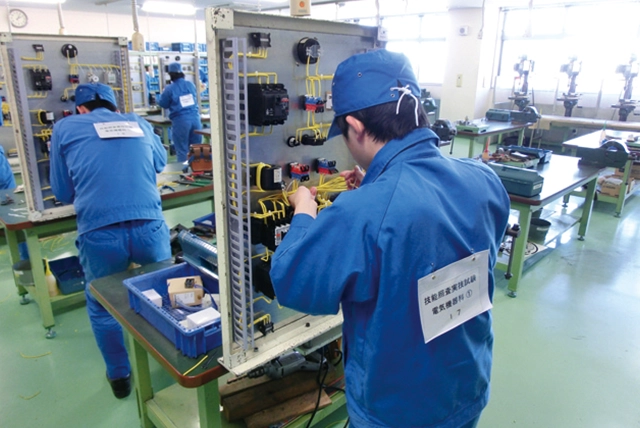
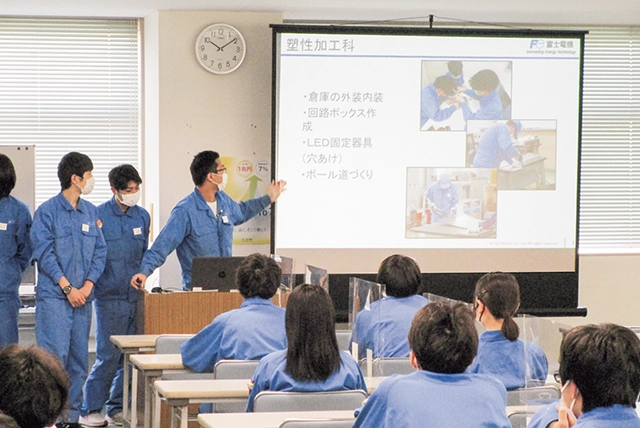
Voice of trainees
Haruto Akimoto, Kawasaki Factory
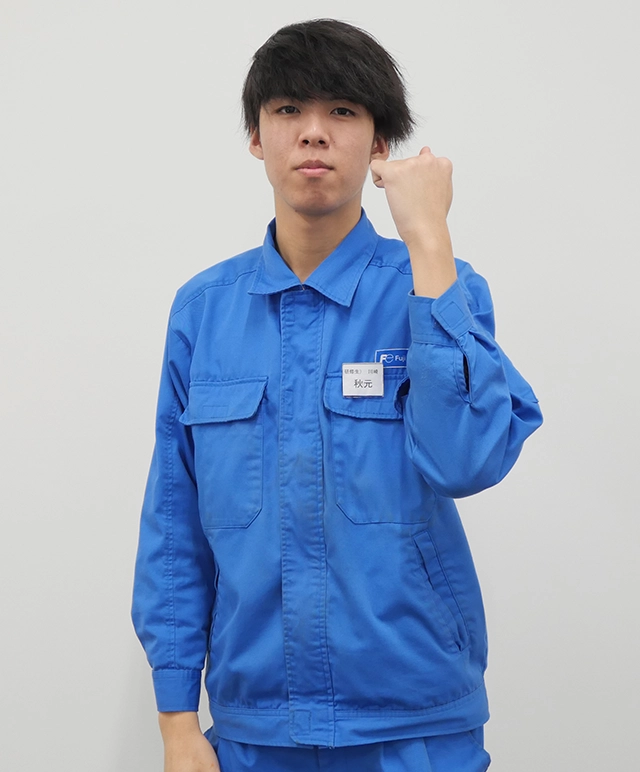
To be honest, at the beginning of the training, I couldn’t shake my student mindset. At one point, the instructor chastised me, and it made me realize how immature I was. I knew I wouldn’t make it to the starting line if I couldn’t pass the skill check (graduation exam), so I buckled down, worked hard on my daily training, and collaborated with my peers to teach one another our strong points. That allowed me to grow through friendly competition.
The reason I decided to join Fuji Electric was the admiration I felt for the craftsmen I saw working silently on huge products when I visited the Kawasaki Factory. Fuji Electric is active around the world. I’m sure that I will have a lot to learn after the assignment, but I will do my best to become a full-fledged employee and play an active role!
Ayaka Hanjo, Suzuka Factory
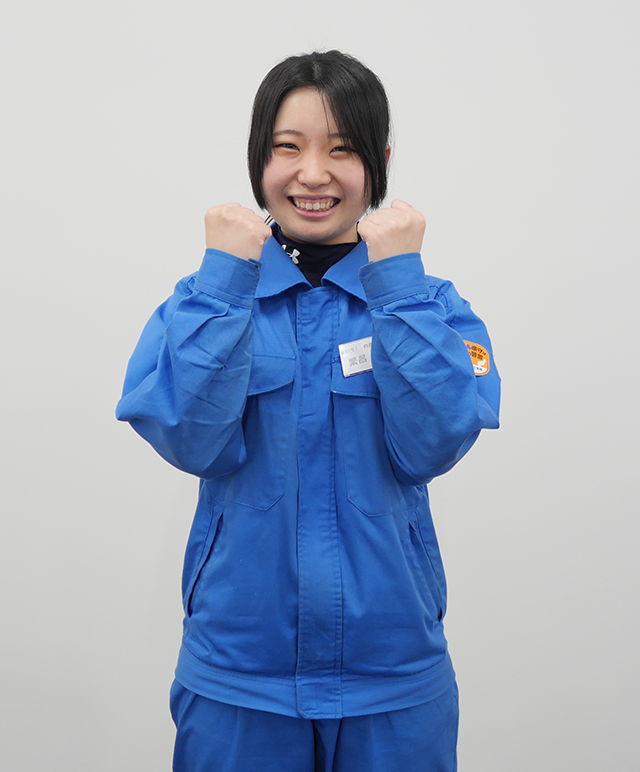
I joined Fuji Electric because I’m interested in environmental issues and want to help solve them. I went to an agricultural high school and had no knowledge of electricity or machinery, so I started out with a feeling of anxiety. But I didn’t want to give up on things that I didn’t understand, so I started asking lots of questions and picking up information with the help of my peers and our instructors. In the skill check, I was able to complete my task not only within the time limit but with some time remaining. That gave me confidence for the future.
Now that I’m about to be assigned, to be honest, I’m a ball of nerves, but I’ll do my best. I hope I can rely on everyone at the Suzuka Factory to teach me!
Hayata Matsumoto, Chiba Factory
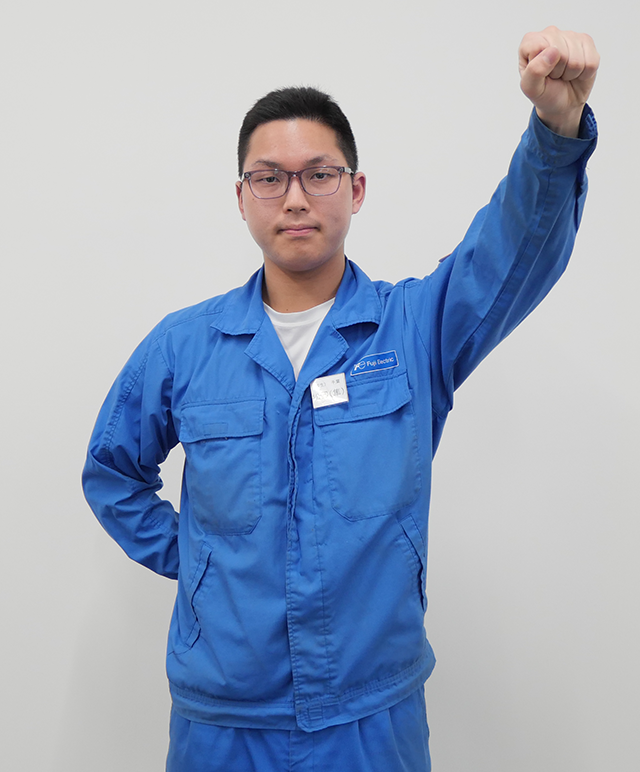
I’ve always liked making plastic models, so I never felt bored with the repeated exercises in the training. I actually found it fun to improve the level of completion of the work I was assigned. I’m also the type of person who hates to lose, so I tried to learn from other people’s strengths and I worked hard to improve my skills. In the end, the switchboard I built was chosen as an example to display in the classroom, which made me happy. As dormitory leader, I also worked to improve our lives in the dormitory. For example, I used a magnet board to make a user management table for washing machines and bicycles.
I think that the training taught me the necessary fundamentals for doing my job. When I’m assigned to the Chiba Factory, I want to learn from my senior colleagues so that I can play an active role as soon as possible.
Relevant SDG targets
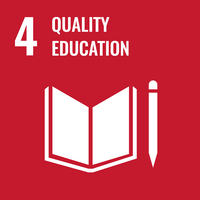
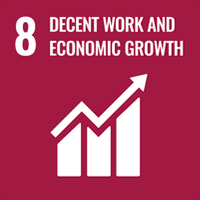
One of the items in Fuji Electric’s Corporate Code of Conduct is “Respect and value all people.” We have set employee competence development as one of the most important management themes and pledged to strengthen human resources development to realize the growth of each and every employee and the maximization of our strengths as a team through respect for diversity. We have set our focus on SDGs goals 4. Quality Education and 8. Decent Work and Economic Growth and are working to promote the success of diverse human resources and improve employee engagement.