Sustainability
Reducing greenhouse gas emissions during production | Our Contribution Activities to SDGs
SF6 gas reduction project at Fukiage Factory
-Reducing greenhouse gas emissions for sustainable manufacturing-
-Reducing greenhouse gas emissions for sustainable manufacturing-
Published in August 2023. Affiliations and responsibilities are as of the time of the interview.
To play our part in bringing about a sustainable society, we are focusing on environmental activities in accordance with our “Environmental Vision 2050.” Our manufacturing bases are currently promoting various initiatives, including reduction of greenhouse gas emissions and rigorous management and reduction of emissions of chemical substances and waste. The initiative at Fukiage Factory to reduce the greenhouse gas “SF6 gas” symbolizes our efforts. The members who developed the new technologies with all their might will talk about the project’s outline and their thoughts behind the development.
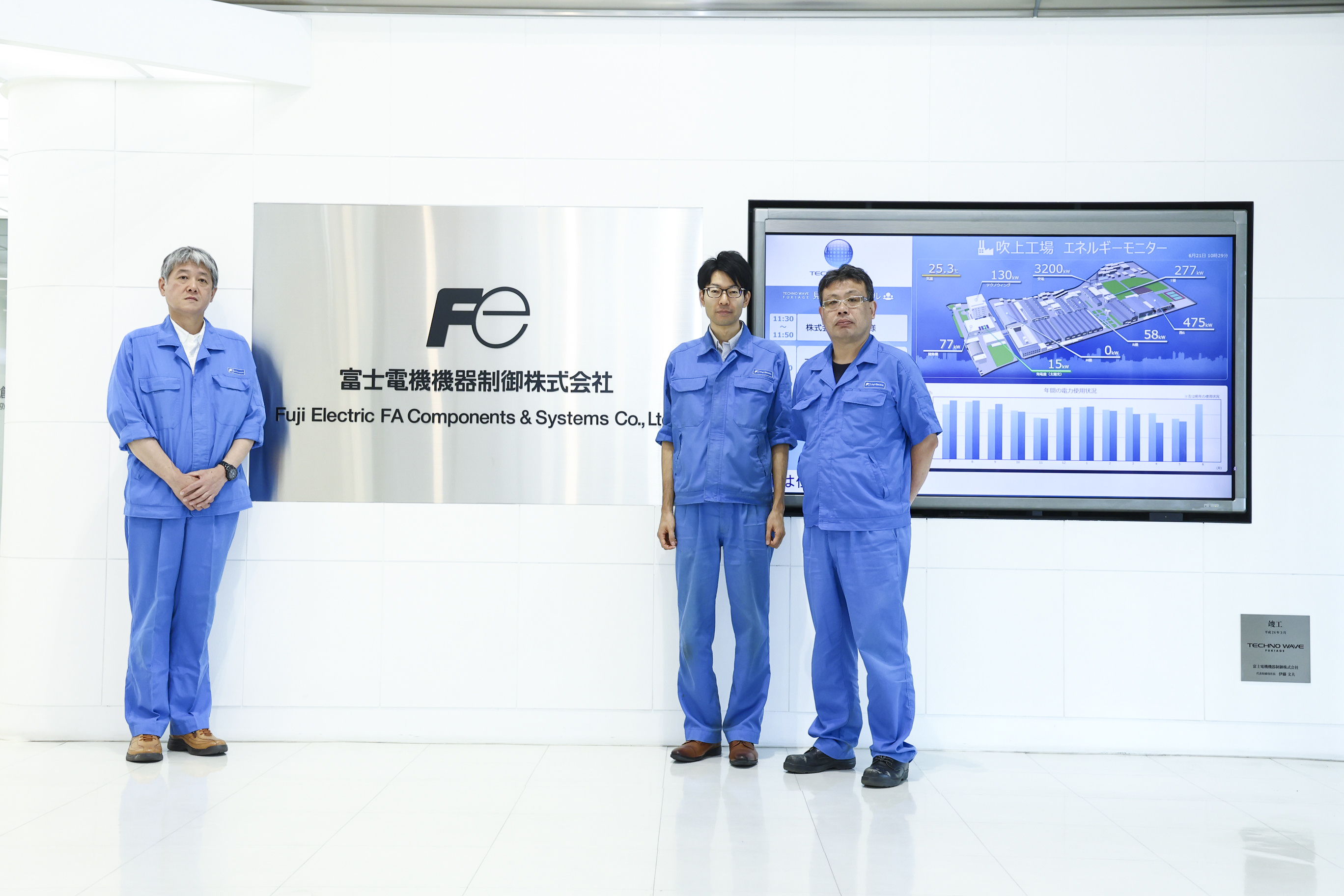
Speeding up the reduction of greenhouse gas emissions.
Environmental initiatives at Fukiage Factory started more than 10 years ago. The employees came together to promote the saving of energy and phase-out of fossil fuels, generating tangible results. Tsuyoshi Obata, Senior Manager of the Production Engineering Department, reflects on the activities at the plant.
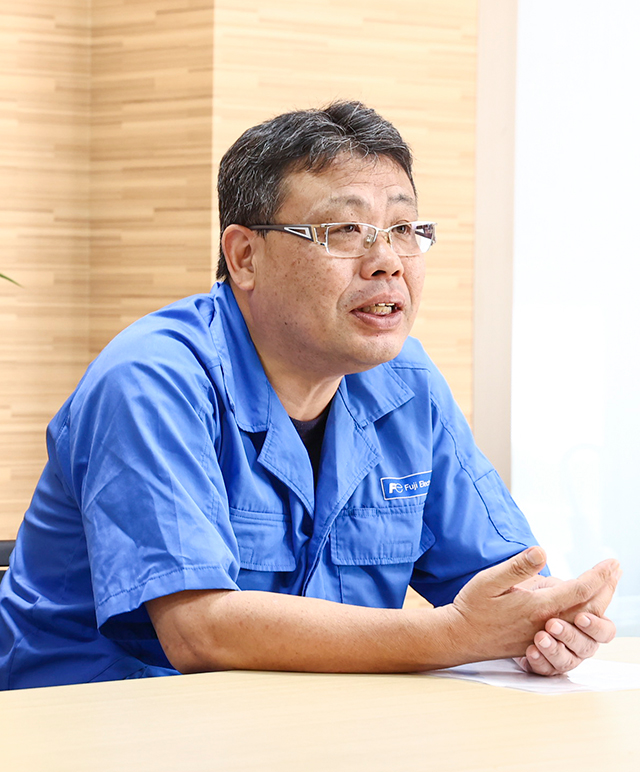
“Fukiage Factory has used an internally developed power projection system to save energy, electrifying air-conditioning facilities, and updating and improving lighting and production facilities. Our efforts have been highly received internally and externally, winning the ‘Energy Conservation Grand Prize for excellent energy conservation equipment’ in 2020. The activities became even more rigorous, taking on various challenges to cut greenhouse gas emissions during production by over 46% by 2030 (compared to FY2019).”
What caught the team’s eye was to cut the usage of the SF6 gas which is used during the production of high voltage vacuum circuit breakers. Safe for the human body and electrically insulating, this gas had been used for electrical insulation in production processes. However there was also a disadvantage; this gas has 22,800 times more global warming potential than CO2.
“‘Reduction of SF6 gas’ was a pressing issue for achieving sustainable manufacturing. The impact was enormous, accounting for approximately 70% of our factory’s greenhouse gas emissions. If we could establish new processes and technologies that did not involve this gas, our efforts to cut greenhouse gas emissions would further accelerate. I would say this project was a new challenge to explore the future for Fukiage Factory.” (Obata)
Our Environmental Vision
Fiscal 2030 Goals
Fiscal 2030 Goals
●Greenhouse gas emissions throughout the supply chain (Scope 1+2+3):
Reduction of over 46% (compared to FY2019)
●Greenhouse gas emissions through production (Scope 1+2):
Reduction of over 46% (compared to FY2019)
●Contribution to CO2 reduction in a society through our products:
Over 59 million tons/year
Tackling manufacturing innovation, with both expectation and concern.
The product surface is made smooth by application of a high voltage. We should discover a way to replace the SF6 gas used for electrical insulation in this conditioning process. That was the outline of this project. The colleagues assigned to the project to resolve this issue, were Yasunori Arai, Fukiage Manufacturing Engineering Section, Production Engineering Department, who knows everything there is to know about production technologies for vacuum insulators, and Hiroaki Nakahara, Equipment Technology Department, Production Technology Center, Production & Procurement Group, Fuji Electric, who is a facility expert. They reflected on how they felt when they were assigned.

“The technological hurdle was extremely high, impossible even if we wanted to achieve it. Reducing the SF6 gas was the key theme for us. It turned out that we were able to get support for this project from Mr. Nakahara, who had previously solved numerous issues as a facility expert. So, I was ready to make it happen, no matter what. Of course, we knew that success of the project would still be hard to come by, but our expectations had been raised like never before.” (Arai)
“I have worked on numerous facilities and technologies but had never got involved with such high-voltage facilities. Forgetting our previous ways and achieving safer and higher-quality manufacturing was a goal that was extremely hard to attain. I feel sorry for Mr. Arai because he was expecting a lot of me but frankly speaking I was just really worried.” (Nakahara)
Reduction alone is meaningless.
We should discover a new technology and manufacturing method that does not involve SF6 gas. To make this happen, the team members kept exploring every possible chance. They always remembered they should avoid adding new effort or cost compared to the current manufacturing methods. Recovering the emitted SF6 gas would be more expensive than before. The “wet method” of immersing products in oil for electrical insulation would involve two new processes — washing and drying. Eventually the team reached the conclusion of using compressed air.
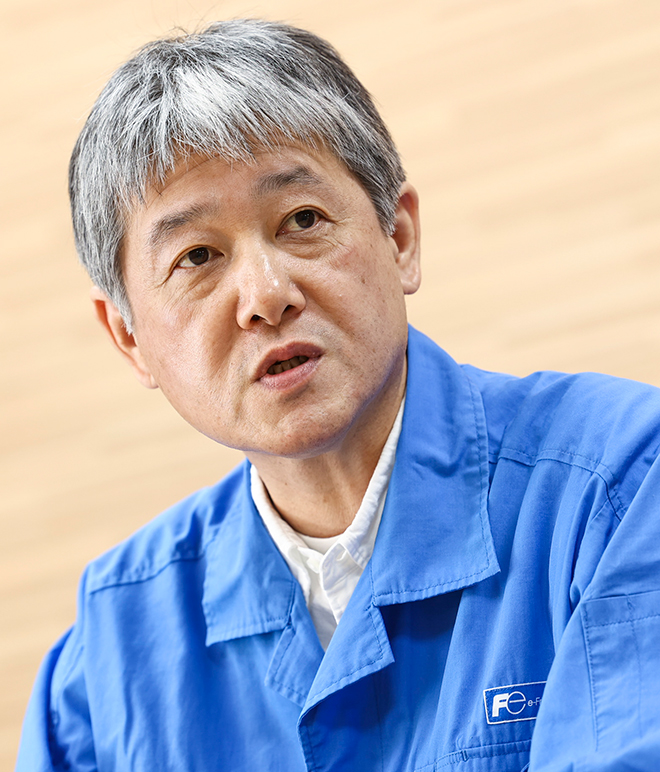
“We came up with the idea of using air from the perspectives of operability, gas management, and cost. But then we were faced with an issue that, by doing it this way, we could not achieve the electrical insulation we were targeting. So we reached the conclusion that we would compress the air to improve insulation.” (Nakahara)
The answer was derived from a process of trial and error by the team members. The created value was enormous, achieving nearly 20% more insulation than initially planned. For mass production, the team needed to consider seasonal variations and fluctuations in the processing of components, so they had reset the goal higher. In creating new facilities and manufacturing methods, improvements were made with job site operability uppermost in mind.
“We were to update and renew about 50% of the facility in use, to achieve the new manufacturing method using compressed air. In the conditioning process, the product is covered in a special container. We then send in compressed air and apply high-voltage power. The container is extremely heavy. It would need a big physical effort by a worker to carry it. So we developed a new function to automate this. As such, we are proud to have created a line that gives maximum consideration to on-site needs.” (Arai)
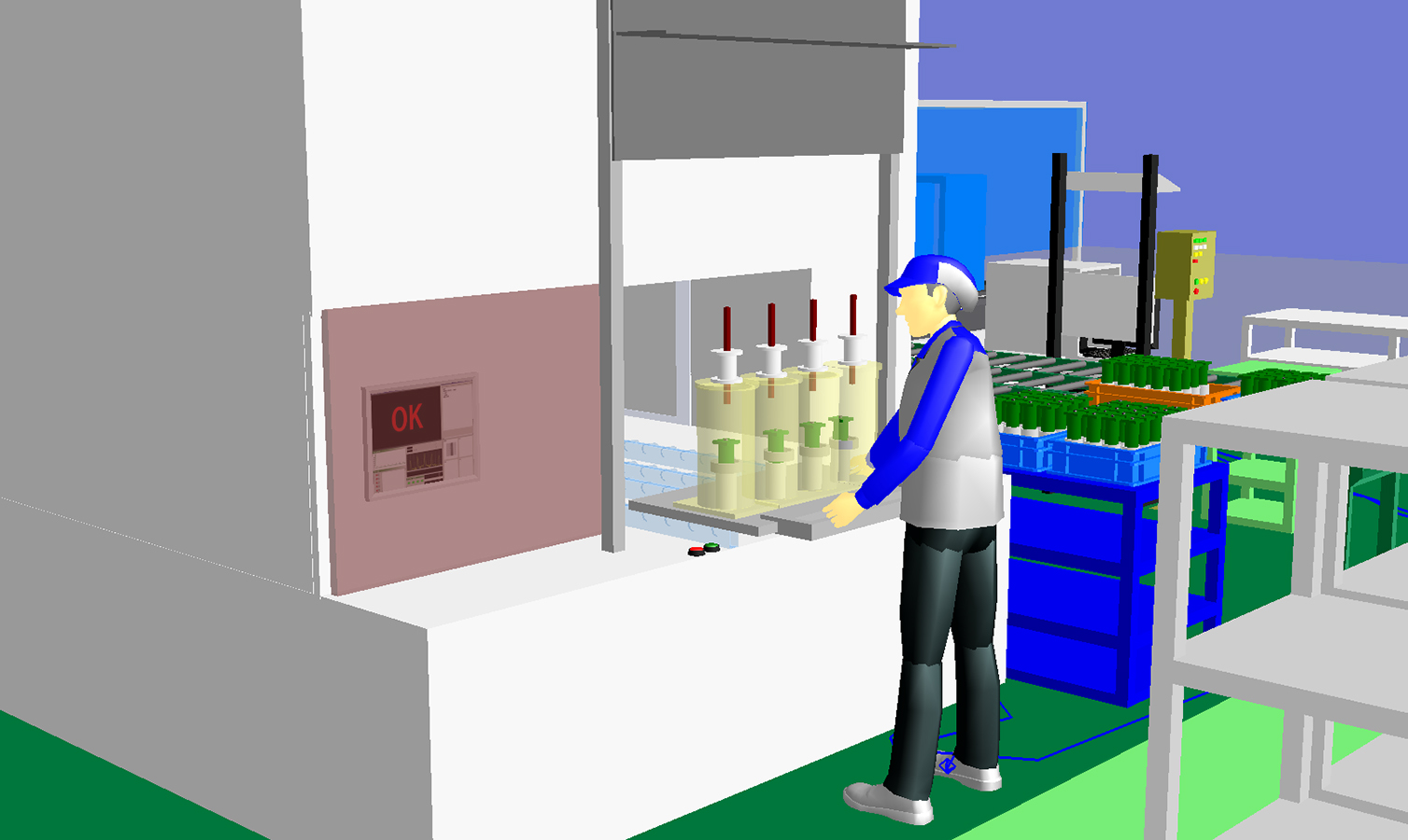
The 2030 target was achieved ahead of schedule.
The success of this project has cut the use of SF6 gas at Fukiage Factory by 95%. It means Fukiage Factory can meet its target of 46% greenhouse gas reduction by FY2030 ahead of schedule. Needless to say many Fuji Electric employees cheered for the team’s amazing achievement. The respective members look back on this incredible project.
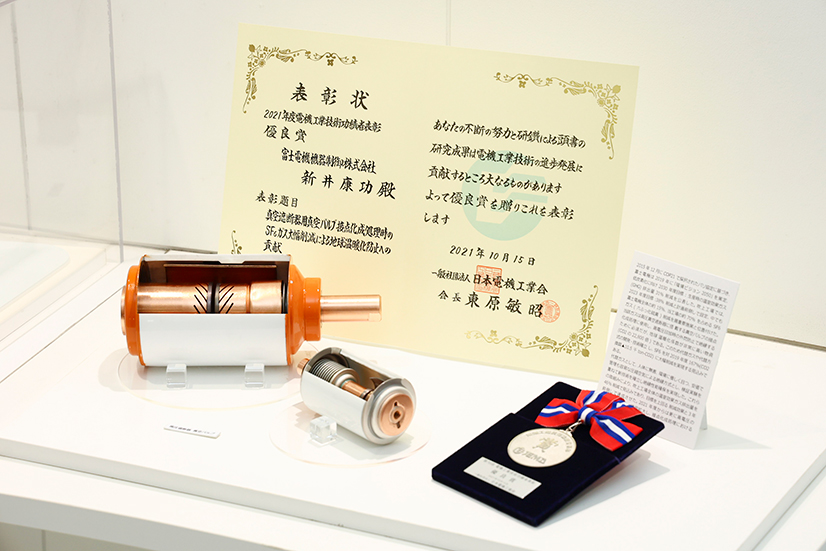
“The reason we were able to clear an issue that had troubled us for so long and take it smoothly to mass production was because our team members came together, pooled their minds, and moved the project forward, transcending divisions. We are proud to have led the project to success but that is not the goal. We would like to keep making improvements as a team and achieve the next-generation manufacturing.” (Arai)
“After the project’s success we were awarded a prize and so forth, but the thing that gave us the biggest sense of accomplishment was seeing the SF6 gas cylinders disappear from the job site. There was nothing that made us prouder, because it became clear to us that it was our technological development that was responsible for their disappearance. We want to capitalize on this experience to play our part in further brushing up of our manufacturing.” (Nakahara)
“The establishment of the new technology has significantly cut the use of SF6 gas. As project manager, I am deeply proud of the team members who have created new value. But that doesn’t mean everything has been solved. The experience and expertise we gained from this project are invaluable assets for future improvements. We want to make further challenges toward zero greenhouse gas emissions, achieving the “Environmental Vision 2050” ahead of schedule.” (Obata)
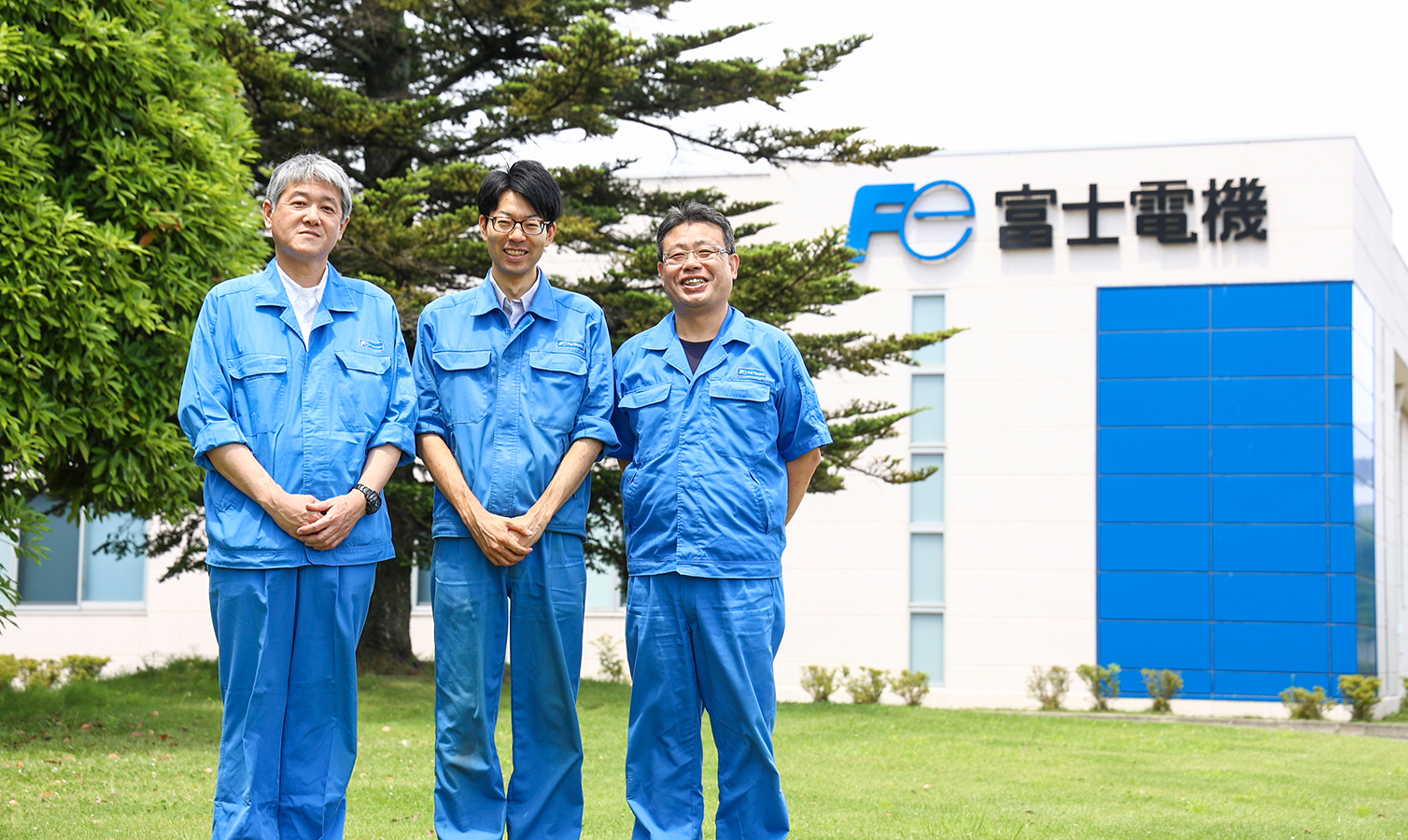
Contribution to SDGs
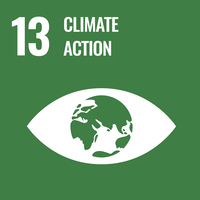
With the Fuji Electric Code of Conduct “Respect and value the global environment,” we position initiatives to conserve the global environment as one of the most prioritized management issues. SDGs target “13. Take urgent action to combat climate change and its impacts” is one of our priority goals. As a direction for our long-term environmental activities, we have established “Environmental Vision 2050” and “FY2030 Goals,” reducing greenhouse gas emissions throughout the supply chain, including our production activities.