Sustainability
Achieve a Decarbonized Society
At Fuji Electric, we are seeking to achieve carbon neutrality across the supply chain; this is in line with our Environmental Vision 2050, which we formulated in response to the global shift toward carbon neutrality and the Japanese government’s decarbonization goals. To help us achieve our Fiscal 2030 Goals, which serve as interim goals for our Environmental Vision, we are working to ensure that various measures are incorporated into the action plans of each of our departments.
Action Plan to Reduce Greenhouse Gas Emissions
Society has been making great progress in preventing global warming since the adoption of the Paris Agreement in December 2015. The agreement stipulates that the average worldwide temperature increase must be kept sufficiently below 2°C compared to pre-industrial levels, and that efforts must be made to limit the increase to 1.5°C. Against this backdrop, Fuji Electric set a target in fiscal 2018 to reduce greenhouse gas emissions (Scope 1+2) in production activities by fiscal 2030, and formulated its “Environmental Vision 2050” in fiscal 2019.
Despite this, social trends have been accelerating more quickly than we had initially anticipated. For example, in 2020, major countries around the world started raising their greenhouse gas emission reduction targets. Amid this fast-moving social trend toward decarbonization, Fuji Electric partially revised its “Environmental Vision 2050” in 2021, announcing that it will aim for carbon neutrality in its entire supply chain. In addition, we also revised our fiscal 2030 target in March 2022, raising the target for greenhouse gas emissions in production activities and establishing a new target for reducing greenhouse gas emissions (Scope 1+2+3) throughout the entire supply chain.
Furthermore, we obtained certification for the “1.5°C level” by SBTi (Science Based Targets Initiative), an international initiative, in 2022 for our new reduction targets for Scope 1+2 and Scope 3.
Reducing Greenhouse Gas Emissions During Production
Reduction of Total Greenhouse Gas Emissions
Fuji Electric takes greenhouse gas (GHG) emissions as a metrics to assess our activities for realizing a society with net-zero carbon emissions. We define greenhouse gas emissions as the sum of CO2 emitted through energy consumption and greenhouse gases such as HFC, PFCs, SF6, and NF3 emitted in the production process.
Even before formulating Environmental Vision 2050, we were working to reduce GHG emissions from production activities.
The target set for fiscal 2030 aims at a more than 46% reduction of CO2 equivalent on the fiscal 2019 results, and an 85% reduction from fiscal 1990 (global base year for the Kyoto Protocol).
Greenhouse gas emissions reduction initiatives and results in production activities (fiscal 2023)
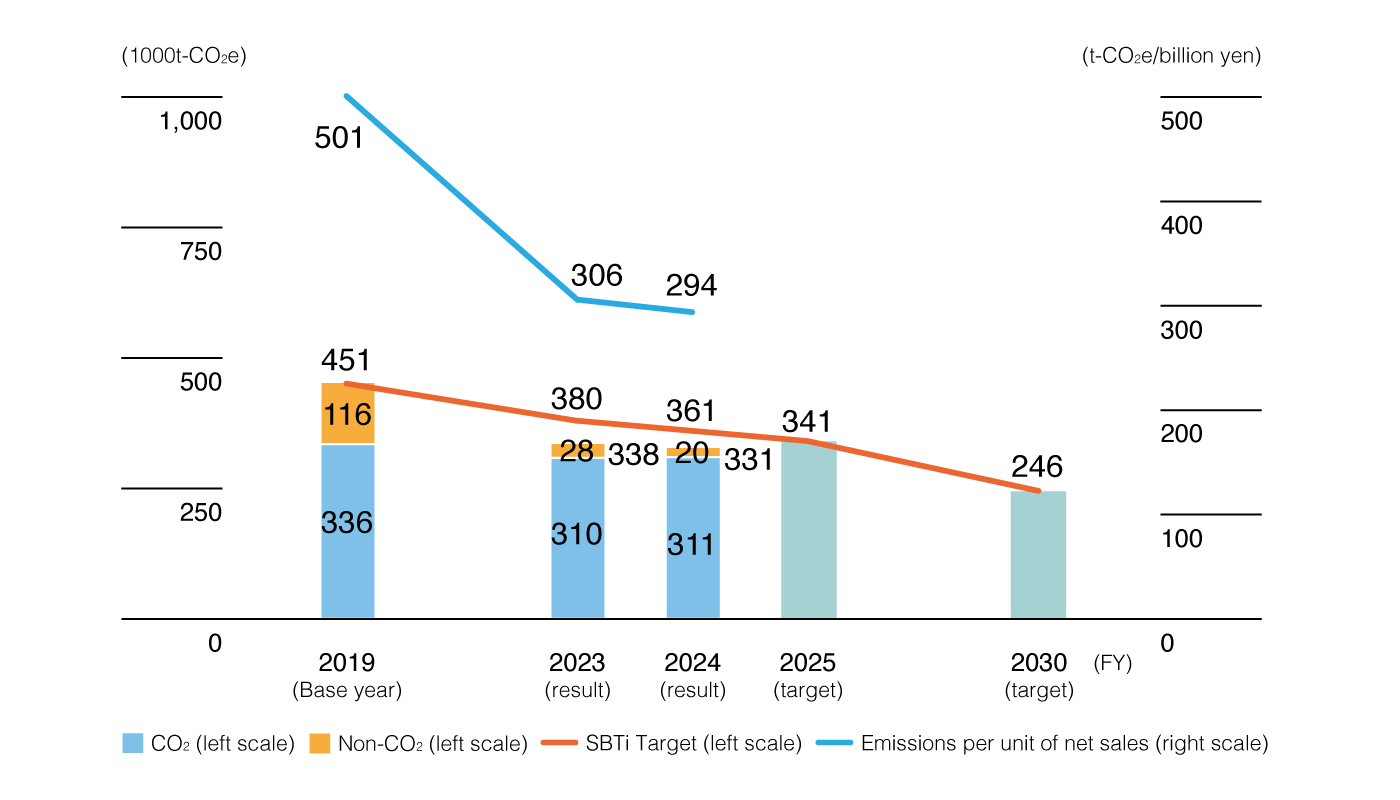
1.<Scope>
The aggregation range is equivalent to 95.2% of the entire Group (percentage figures refer to our environmental management activities)
(1)Japan: All production sites and consolidated production subsidiaries
(2)Overseas: Consolidated production subsidiaries excluding the two sites that are not certified under ISO 14001
2.<Power coefficients>
Japan:
For fiscal years 2023 and 2024, power coefficients were obtained from “Adjusted Emissions Factors for Electricity Supply Companies,” as published in Emission Factors for Power Supplied by an Electric Utility Company, jointly issued by the Ministry of the Environment and the Ministry of Economy, Trade and Industry.
For fiscal years 2019 to 2022, power coefficients were calculated with reference to KEIDANREN's Commitment to a Low Carbon Society; in fiscal 2022, this resulted in a power coefficient of 0.436 kg-CO₂e/kWh.
Overseas:
Power coefficients, as defined in IEA’s Emissions Factors 2024, are based on the most recent country-specific data, with reference to the year 2022.
3.<Calculation of Scope 2>
Scope 2 emissions in Japan have been calculated in accordance with market-based methods since fiscal year 2023.
Actual greenhouse gas emissions in production activities in fiscal 2024 were 331 thousands of tons. This achievement was approximately 8% below the target for the fiscal year (below 360 thousands of tons). Since this target value corresponded to the value of the SBT action plan (the value for fiscal 2023 on the straight line connecting the base value for fiscal 2019 and the target value for fiscal 2030), it can be said that we are currently on track to achieve results that will meet the SBT plan.
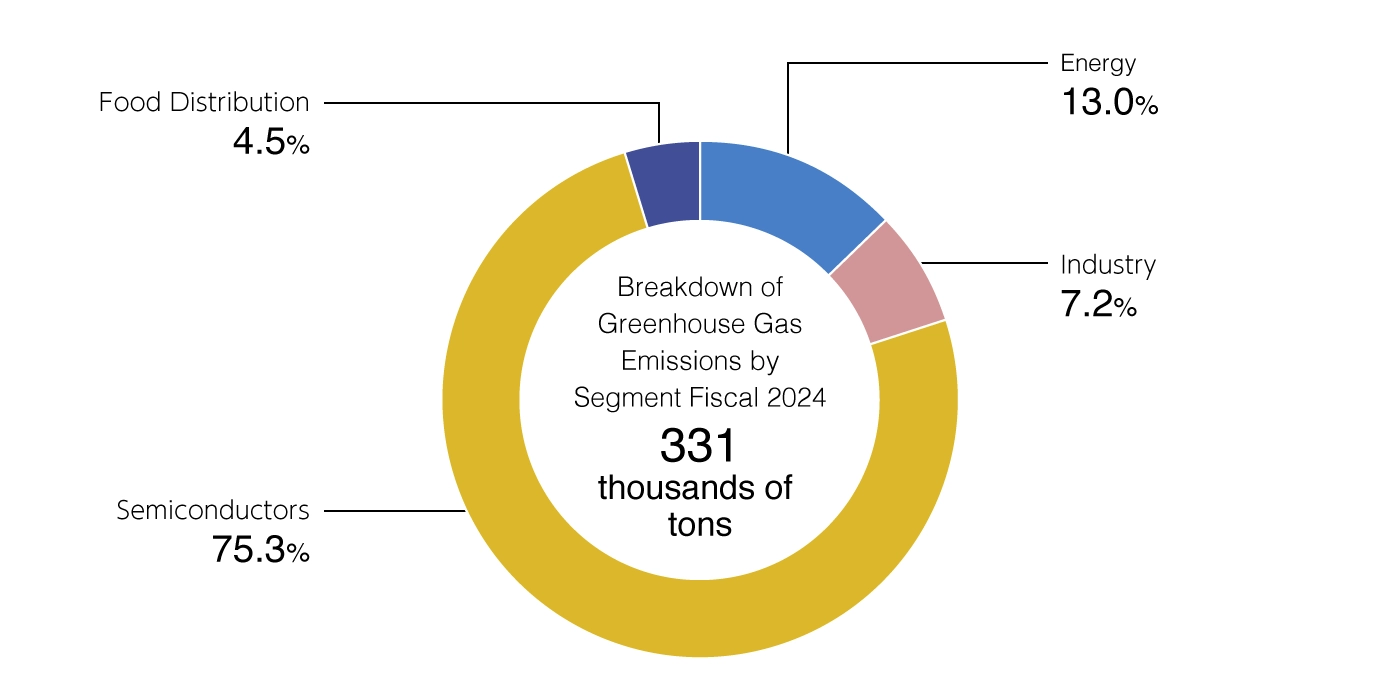
-
Energy-saving activities (solar power, installation of high-efficiency lighting, air conditioning, etc.): -2 thousands of tons (0.6%)
-
Greenhouse gas replacement: -4 thousands of tons (1.2%)
-
Effects of new solar power installations: -4 thousands of tons (1.2%)
-
Purchase of both renewable energy and renewable energy certificates -13 thousands of tons (3.9%)
Total emissions reduction based on the measures: -23 thousands of tons (6.9%)
Greenhouse Gas Emissions: Results and Future Measures
CO2 emitted during production comes under Scope 1 and Scope 2 emissions.
-
Scope 1:Direct greenhouse gas emissions by the reporting company itself.(eg. fuel combustion, industrial process)
-
CO₂ directly emitted from factories due to combustion of fuel during cogeneration power generation, boilers, drying furnaces, etc.
-
Four greenhouse gas types directly emitted from production processes
-
-
Scope 2:Indirect emissions from the use of electricity, heat, or steam supplied by others.
Until now, we have worked to reduce CO2 emissions mainly through energy-saving activities aimed at increasing energy efficiency. However, it became clear that we could not meet our medium-term target by simply expanding conventional energy-saving measures. For this reason, we have been reviewing our investment criteria and incorporated investments in high-efficiency air conditioners and LED lighting into a five-year renewal plan for each factory in order to reach our reduction target.
In fiscal 2022, factories associated with our semiconductor divisions began purchasing renewable energy and renewable energy certificates on a trial basis. As a result, the proportion of renewable energy in our total power consumption increased to 9.1% in fiscal 2024, reducing CO2 emissions by approximately 6,000 tons. To ensure a stable supply of renewable energy, we also signed three Power Purchase Agreements (PPAs) during the same fiscal year.
As a specific measure to achieve the goals of our “Fiscal 2030 targets (for reducing our greenhouse gas emissions)” in our “Environmental Vision 2050,” we are aiming to maximize the use of solar power generation equipment at our production sites in Japan and overseas, and are installing equipment on the rooftops of factory buildings through self-investment and through power purchase agreements (PPAs) with third-parties.
In Japan, the Chiba Factory, Mie Factory, and the Fukiage and Otawara factories of Fuji Electric FA Components & Systems Co., Ltd., commenced operations of solar power generation facilities with a total capacity of 3.3 MW in fiscal 2024.
In fiscal 2025, the Kobe Factory and Saitama Region are scheduled to commence operations of solar power generation facilities with a maximum capacity of 1.0 MW.
Overseas, Fuji SMBE Co., Ltd. commenced operations with a capacity of 0.7 MW, and Fuji Electric (Shenzhen) Co., Ltd. began operations with an increased capacity of 1.3 MW following an expansion in fiscal 2024.
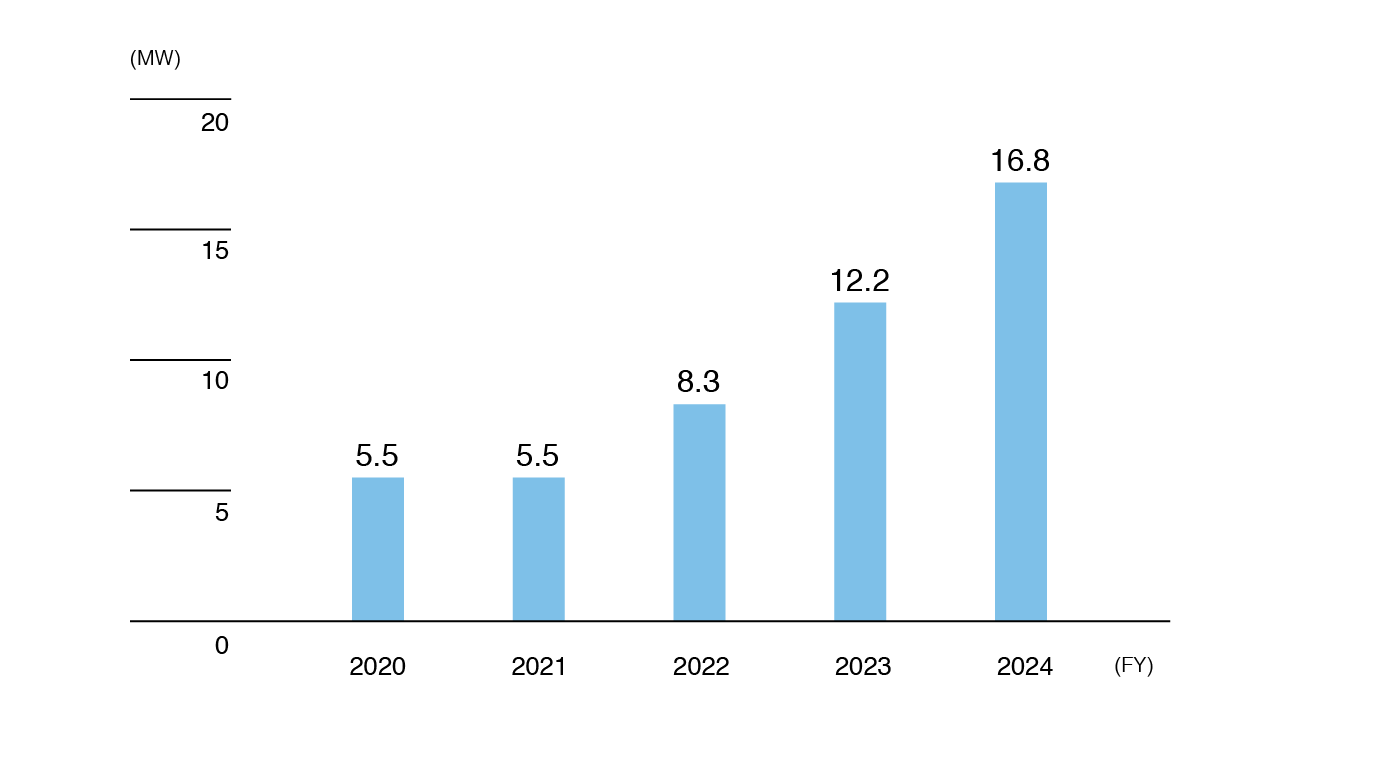
Unit: MWh
In order to reduce the volume of greenhouse gases it emits during production, in 2022 Fuji Electric launched the Renewable Energy Promotion Project, which aims to install solar power generation facilities at all company production bases. The project was spearheaded by a new energy business department with the knowhow to install renewable energy, which worked together with each of our production bases to draw up installation plans.
Specifically, 18 production bases in Japan and two bases overseas began considering the installation of solar power generation facilities. In fiscal 2024, we installed approximately 5,300 kW at five domestic sites and two overseas sites, and commenced operation. We aim to generate around 32 million kWh annually by fiscal 2027 and will continue to promote the further adoption of solar power facilities.
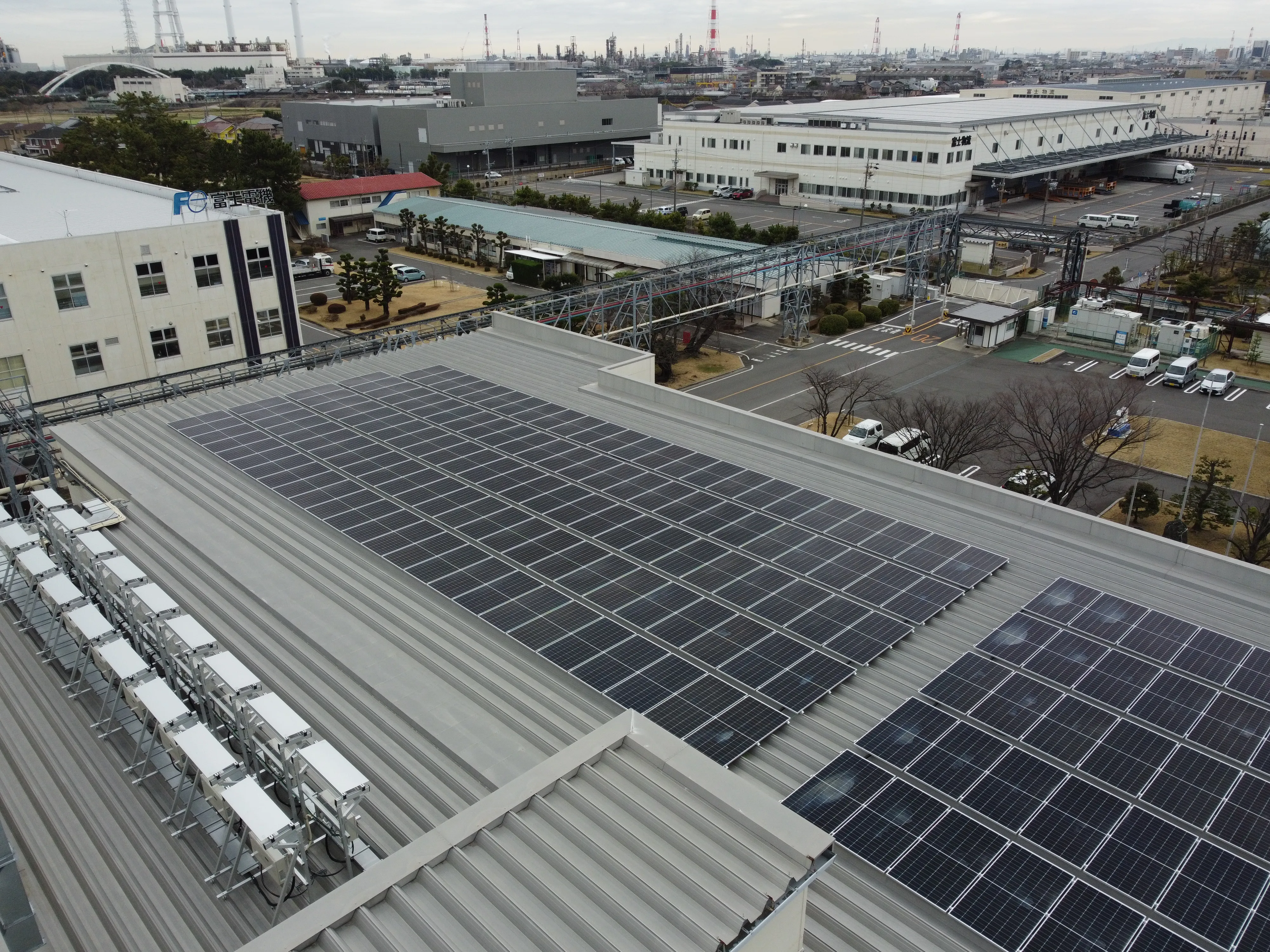
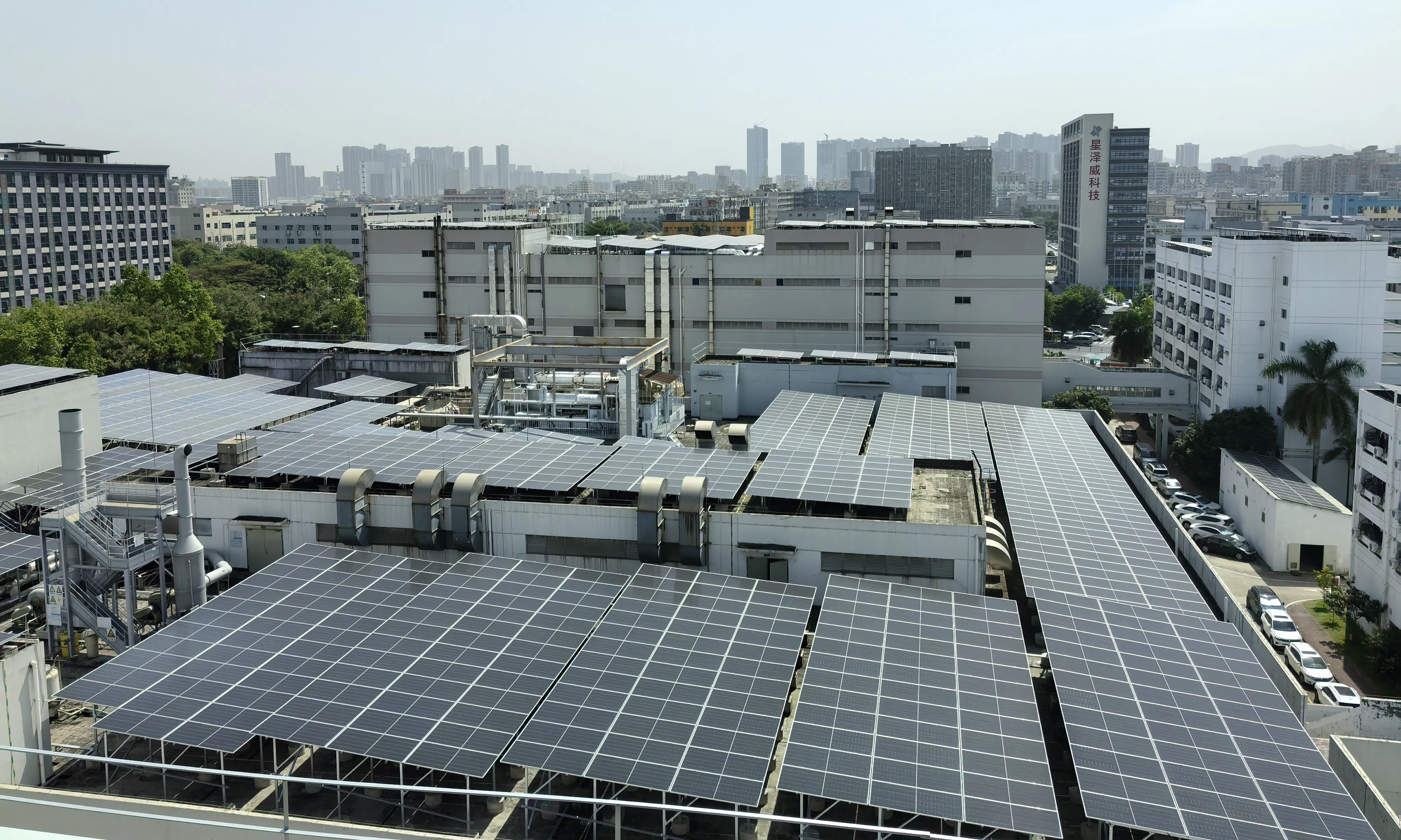
The GHGs we use and their main uses are as follows.
-
HFC (CFC substitute): Used as refrigerants, solvents, and for dry etching of semiconductors
-
PFC (perfluorocompounds): Used for dry etching of semiconductors
-
SF6 (sulfur hexafluoride): Used for dry etching of semiconductors and as insulating gas
-
NF3 (nitrogen trifluoride): Used for dry etching of semiconductors
Greenhouse gases other than CO2 (hereinafter GHGs) are calculated by multiplying direct emissions from our factories by the global warming potential (GWP), which is a CO2 conversion coefficient.
In fiscal 2024, at Matsumoto and Tsugaru Factories, which manufacture semiconductors, we are working to fit pyrolyzers to the exhaust gas systems of all semiconductor production lines installed before 2010*. These pyrolyzers are capable of decomposing 90% or more of the greenhouse gases contained in the exhaust gas.
Through these efforts, we have reduced approximately 9,000 tons of greenhouse gases other than CO₂ in 2024.
-
*
-
Semiconductor production lines installed in 2010 and later are fitted with pyrolyzers as standard.
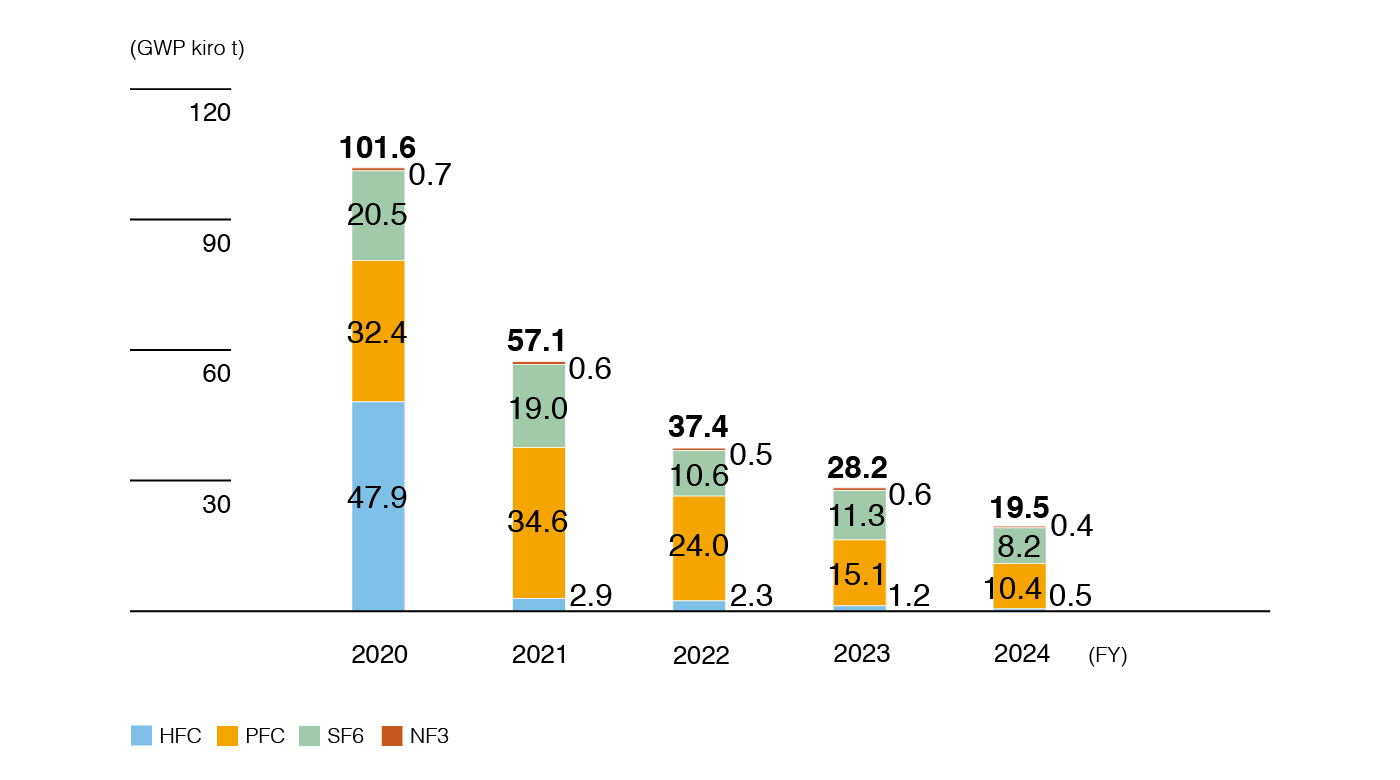
Contribution of products to Society’s CO₂ reduction
At Fuji Electric, we aim to contribute to the society-wide reduction of CO2 through innovations in our electricity and thermal energy technologies; to this end, we encourage our customers to use our clean energy and energy-saving equipment to help reduce operational CO2 emissions. To calculate the CO2 reduction effect for operational products shipped in fiscal 2009 and later, we assume the products are in operation for an entire year.
We calculate the reductions in CO2 emissions using the following equation: (“Fuji Electric existing product emissions volumes” – “Fuji Electric new product emissions volumes”) x “number of units in operation”
Contribution to CO₂ Reductions from Our Products in Use in Fiscal 2024: Targets and Results
In fiscal 2024, we achieved our target with a reduction effect of 58 million tons thanks to the use of energy-saving equipment, such as inverters in the Power Electronics segment, IGBT modules in the Semiconductors segment and clean energy in the Energy segment. The increases in reduction effect were 1.4 million tons for the Industry segment, and 0.4 million tons for the Energy segment, year-on-year.
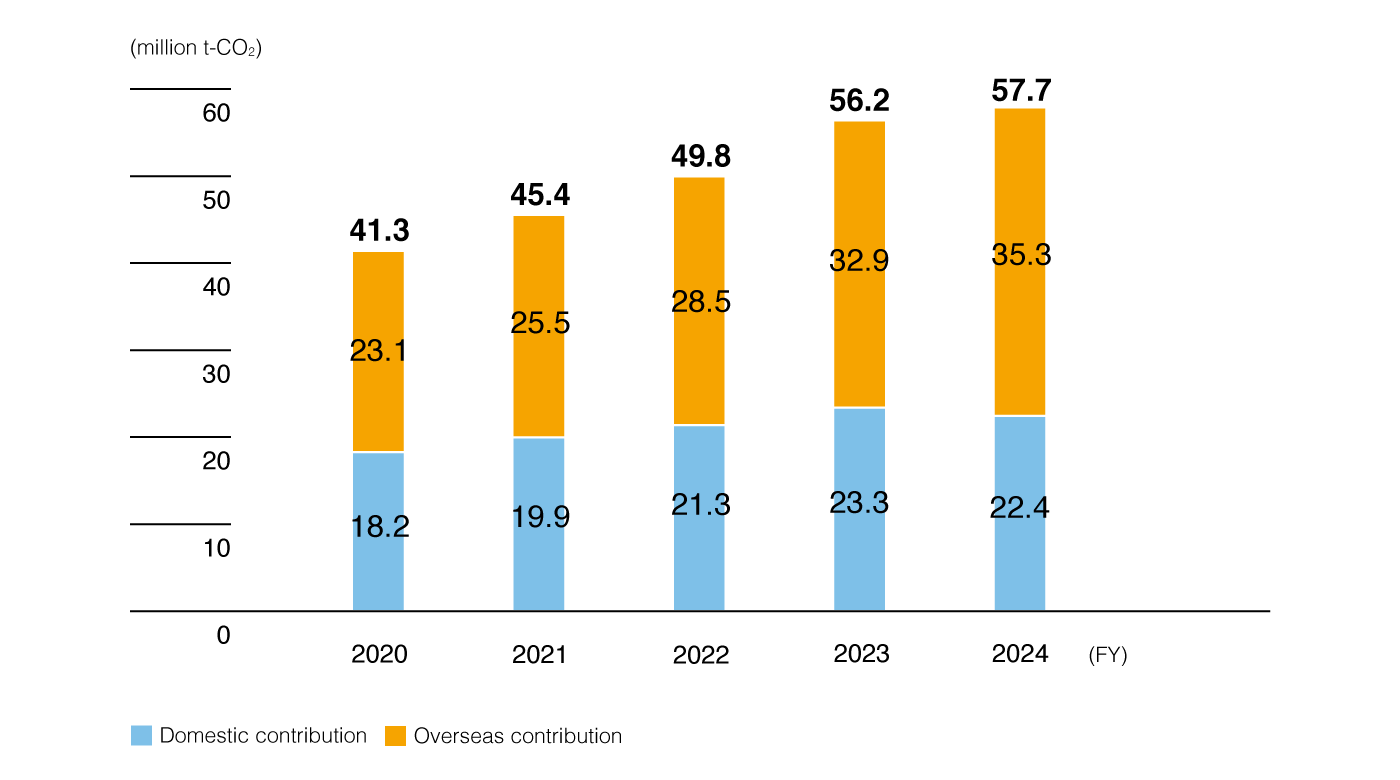
Fuji Electric’s Environmentally-friendly Products
Renewables, such as geothermal and hydroelectric power generation, are clean energy sources that contribute to the prevention of global warming. This is because they use the power of nature to generate electricity and do not emit greenhouse gases. If we could use clean energy to supply electricity to households served by existing CO2-producing power plants, we could meet their electricity needs without emitting any CO2 emissions. By promoting the proliferation of clean energy, Fuji Electric contributes to the reduction of CO2 in society.
In fiscal 2024, in the Energy segment, we delivered two geothermal power generation units with a total capacity of 93 MW, and six hydroelectric units with a total capacity of 56 MW. These facilities can produce approximately 1,300 million kWh of renewable energy per year, contributing to a reduction in societal CO₂ emissions equivalent to approximately 580 thousand tons of CO₂ annually, which would otherwise be emitted by thermal power sources.
Products supplied by the Industry segment, such as inverters, can be incorporated into factory and other equipment in order to realize energy savings in motor control and various other areas. Meanwhile, uninterruptible power systems (UPS) supplied by the Energy segment can contribute to energy saving by improving efficiency through lower electricity consumption losses. Power semiconductors, an offering in the Semiconductors segment, are used as key devices in those power electronics products, contributing to the energy efficiency through highly efficient energy conversion and power control.
In the field of industrial and automotive power semiconductors, Fuji Electric has continuously advanced the development of devices and modules that achieve low loss and high efficiency. In particular, we have focused on expanding our lineup of seventh-generation industrial IGBT modules and reducing the size of our automotive modules.
In fiscal 2024, in the industrial sector, we launched a new series of large-capacity industrial IGBT modules called the "HPnC" series, designed for solar and wind power systems. We expanded the series up to 2,300V to support larger power conversion systems, contributing to improved generation efficiency. In the automotive field, we developed a compact RC-IGBT module that incorporates our latest RC-IGBT and packaging technologies. This product achieves approximately 57% shrinkage in volume compared to conventional models (based on rated output power), supporting the electrification of lightweight and small vehicles.
Thanks to these and other initiatives in the industrial and automotive sectors, in fiscal 2024 our power semiconductor products helped reduce CO2 emissions by 5.8 million tons. Going forward, we intend to increase sales of our low-loss semiconductor products and contribute to even greater reductions in CO2 emissions.
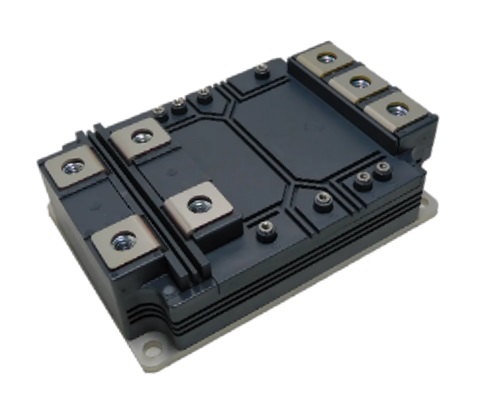
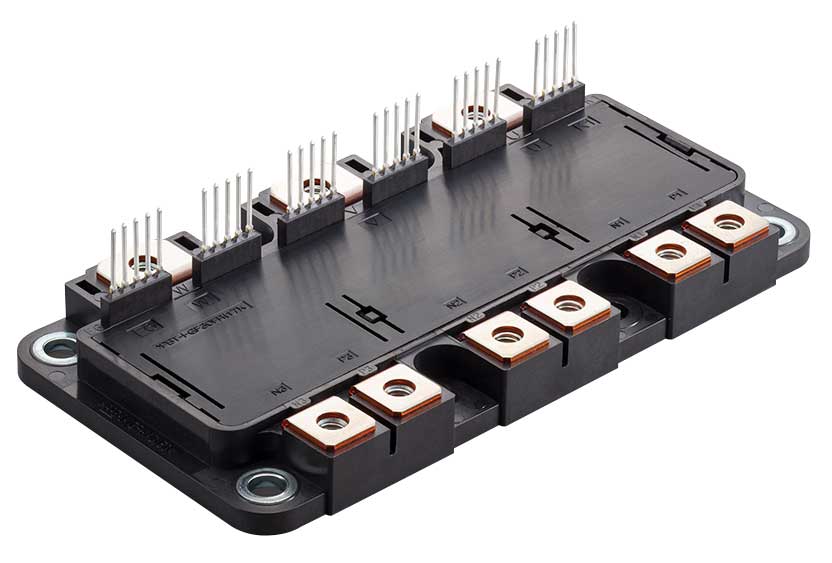
Reducing Greenhouse Gas Emissions Across the Supply Chain
Fuji Electric announced its commitment to help realize a society with net-zero carbon emissions. Going forward, in addition to production activities, including procurement and transportation, we will aim to achieve carbon neutrality across the entire supply chain by working to reduce CO2 emitted when are products are being used.
Scope3 emissions
Greenhouse gases (Scope 3) emitted indirectly upstream to downstream in Fuji Electric’s entire supply chain have been calculated since fiscal 2012 based on guidelines*1 issued by the Ministry of the Environment.
In fiscal 2022, we obtained SBT certification. SBTi has estimated emissions in categories that we were not able to calculate and has verified that it is not necessary to add them to the scope of our targets.
CO2 emissions from sold products (Scope 3, Category 11) account for more than 90% of greenhouse gases emitted across our entire supply chain.
To calculate our Category 11 emissions, in fiscal 2019 we defined both the scope and the method of calculation for emissions from sold products.
Since then, every year we have calculated emissions from the use of sold products in our seven biggest product groups, which together account for approximately 80% of the emissions of all our products.
Scopes for Greenhouse Gas Emissions
-
Scope 1: Direct emissions from sources that are owned or controlled by the company (fuel combustion and industrial processes)
-
Scope 2: Indirect emissions from the use of purchased energy (including heat and steam)
-
Scope 3: All indirect emissions not included in Scopes 1 and 2 (emissions from other companies in the value chain, etc.)
Approach to calculating Scope 3 Category 11 emissions (CO2 emissions from sold products)
-
Final products – products that customers use in their existing state
▶Products covered: industrial electric furnaces, in-store distribution equipment, and thermal power generation equipment
▶Calculation method: “no. units shipped” x “total annual power consumption (fuel consumption)” x “lifespan in years” x “power coefficient” -
Intermediate products – products that customers incorporate into their own products, before being delivered to end-users
▶Products covered: power semiconductors, low voltage inverters, motors, and transformers
▶Calculation method: “no. units shipped” x “total annual power loss (energy loss)” x “lifespan in years” x “power coefficient”
-
*1
-
“General Guidelines on Supply Chain GHG Emission Accounting, Version 3.0,” Ministry of the Environment
Scope 1: Direct greenhouse gas emissions by the reporting company itself.(eg. fuel combustion, industrial process)
Scope 2: Indirect emissions from the use of electricity, heat, or steam supplied by others.
Scope 3: Indirect emissions other than Scope 1 and Scope 2(Emissions by others related to the company's activities)
-
Note:
-
Verification by a third party has been completed for the results of the fiscal year 2022
(unit:kt-CO2)
Energy Conservation Initiatives in Logistics
In an effort to reduce CO2 emissions in the field of logistics, since 2006 the government has obligated freight owners who exceed annual distribution volumes of 30 million ton-kilometers to account for and rationalize their energy consumption. At Fuji Electric, we formulated the Freight Owner Obligations Guidelines, and calculate the energy consumed by each of our factories.
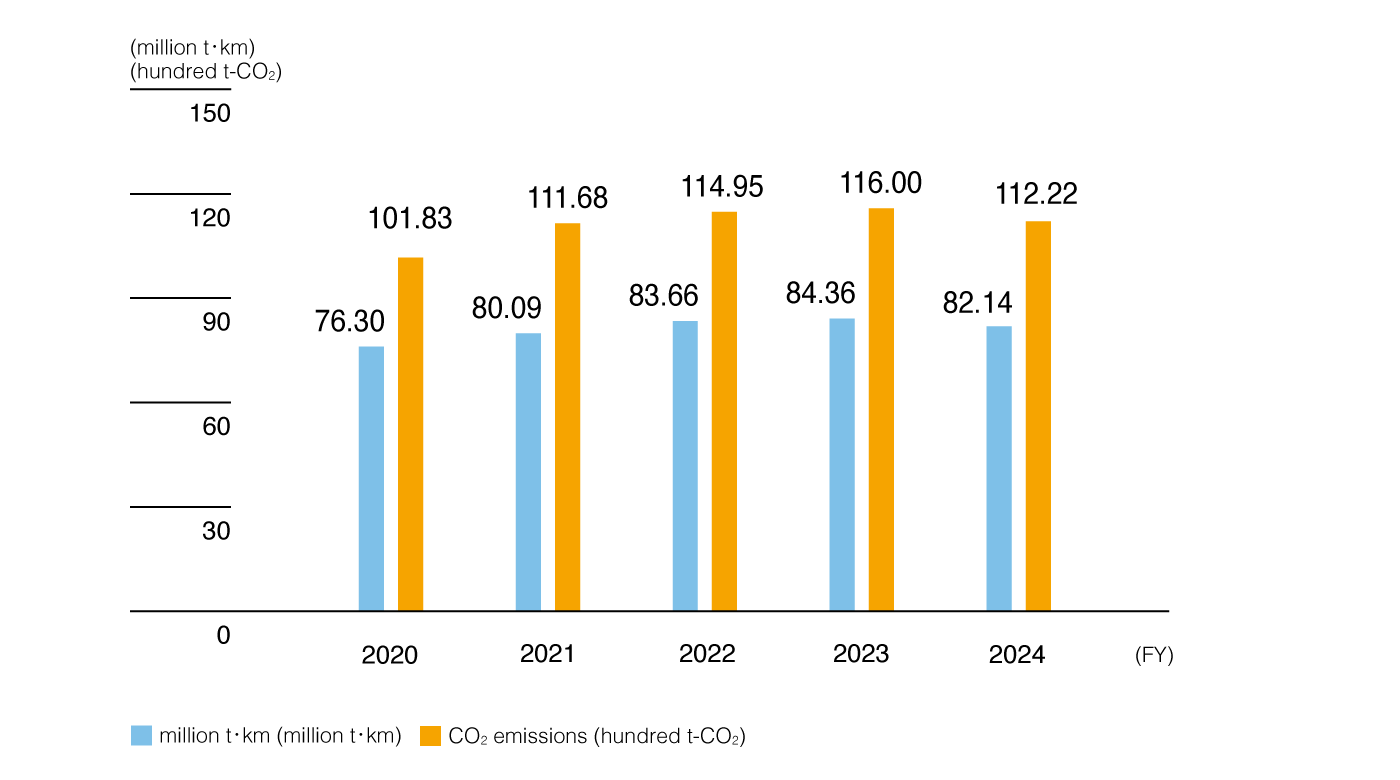
Initiatives to Reduce Environmental Load in Logistics
Fuji Electric’s logistics load in fiscal 2024 decreased 2.6% year on year, with CO2 emissions decreasing 3.3% year on year, too; this indicates that our CO2 emissions per logistics load improved year on year.
We are continually working to streamline our logistics operations. In our vending machine business, which is our most logistics-load-intensive business, we are working to expand our batch delivery method* initiatives, and this has helped us improve our CO2 emissions per logistics load.
-
*
-
Batch delivery method refers to a distribution method in which products are first shipped to regional delivery centers by 10-ton vehicles, then transported individually to each delivery destination by 4-ton vehicles. Compared with the individual delivery method of using only 4-ton vehicles, this method involves shorter mileage and thus reduces the environmental impact.