Sustainability
Manufacturing Meisters | Our Contribution Activities to SDGs
Fostering Brilliance in Skilled Human Resources
Further Evolution in Fuji Electric’s Manufacturing
Further Evolution in Fuji Electric’s Manufacturing
Updated February 2023. The affiliation and job descriptions mentioned are those at the time of the interviews.
Our goal is to set forth “what all technicians should aspire to be,” provide them with training to acquire the necessary skills, and certify them. Introduced in the 2020 fiscal year, Fuji Electric’s Manufacturing Meister System is a program designed to deliver motivation and happiness to all technicians and to further strengthen Fuji Electric’s manufacturing capabilities. What kind of training is provided in this program? How do the instructors feel when they face their tasks? Here, we present an overview of the program and its results.
Clarify goals, means, and benefits, and send a strong message to technicians
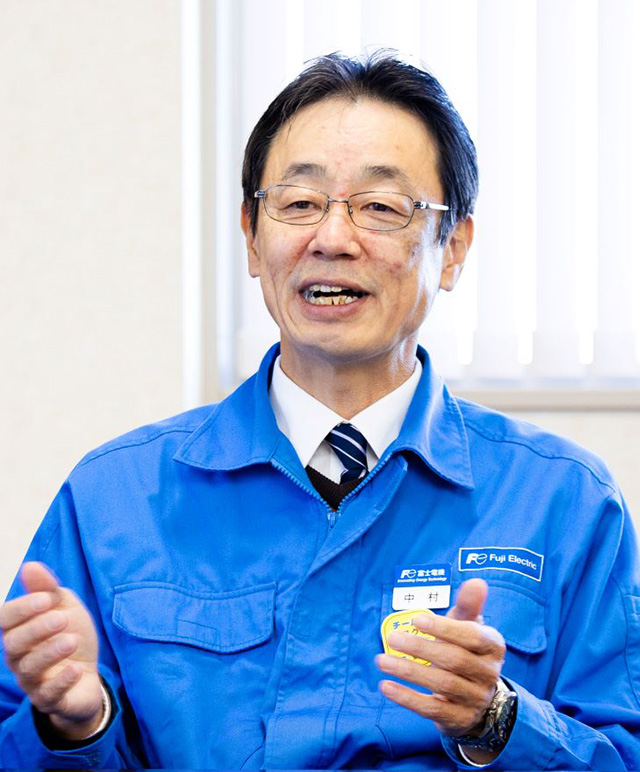
“Human resources with ‘specialized expertise and skills’ who ‘excel at improvement and streamlining processes.’” This is the definition of a Manufacturing Meister. Fuji Electric's technicians, who are honing their skills in the course of their daily work, learn industrial engineering (IE), value engineering (VE), production management and cost control through the Manufacturing Meister training program and gain the ability to improve and streamline processes. In addition, technicians who are certified as Manufacturing Meisters will receive up to 200,000 yen in incentives as bonuses according to the results of their annual improvement and streamlining efforts. Kunihiro Nakamura, General Manager of the Technical & Skill Training Department, which is responsible for Manufacturing Meister training, explains the significance of the system.
“I think this is a very meaningful system for Fuji Electric as a manufacturing company. The key is that it clearly lays out guidelines about ‘what the company wants and what should be done to take the next step’ for our technicians. It provides training opportunities as a means to achieve these goals. Furthermore, by linking the program with the compensation system, it carries a stronger message. We believe that the Meisters, who have acquired new strengths through this system, will proactively bring added value to manufacturing and further strengthen Fuji Electric’s manufacturing.”
Every possible effort was made to establish a training program to create “meaningful opportunities”
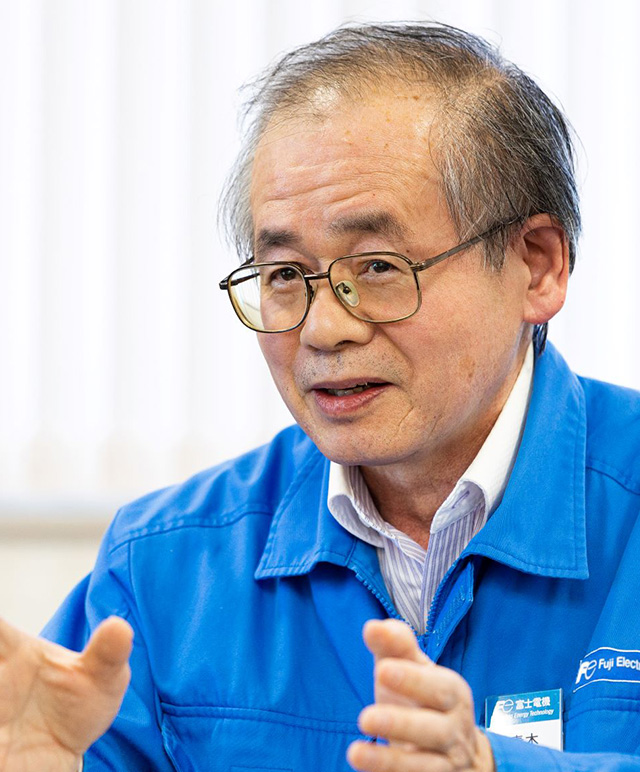
The Manufacturing Meister training program consists of seven subjects: quality control (QC), IE, VE, production management, cost control, Fuji Electric Production System (FePS) and work leader training, which are taught in five sessions a year over a period of three years. The establishment of the training system involved great difficulties. The department's Sumio Aoki reflects on the difficulties experienced during the launch period.
“In addition to the training we had provided up to that point, new training opportunities had to be created for nearly 1,000 potential Meister employees selected from individual factories. Putting the system in place alone was a painstaking task. How do we secure instructors? What system should be used to run the training program? How can we work with factory administration to achieve a system that does not affect operations or production activities? How do we create opportunities for discussion and grasp the level of understanding as the COVID-19 pandemic forces us to take the program online? If I'm being honest, we were stumped. However, I found myself greatly motivated to take on the challenge of making preparations. I understood the significance of the system and was delighted to be able to support so many technicians.”
Cross-departmental discussion provides hints for improvement
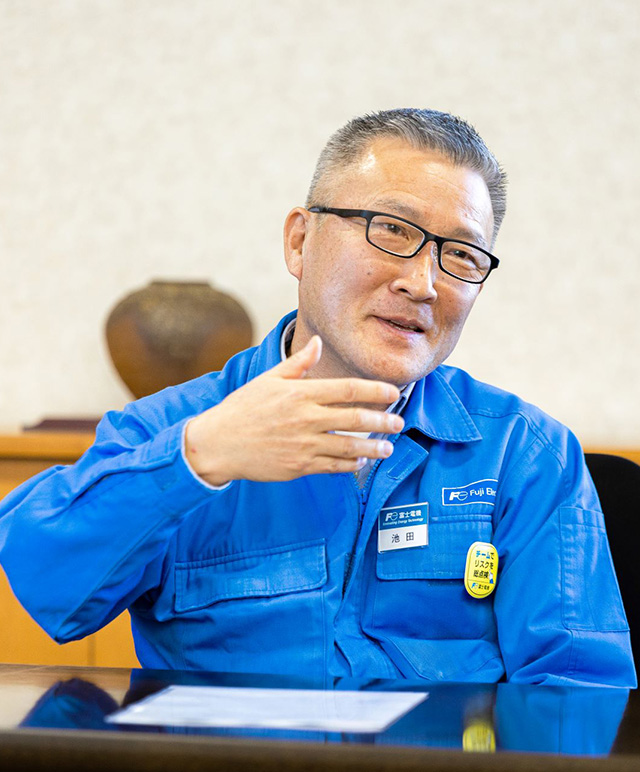
A total of 2,700 technicians from all factories have received the Manufacturing Meister training in a period of three years since 2020. There are already 336 certified Manufacturing Meisters (as of December 2022). The participants' awareness of improvements has certainly strengthened, and small improvements, such as jig and tool improvements, are picking up steam, and constructive suggestions are starting to emerge. The benefits of this training go beyond mere acquisition of knowledge. Shinji Ikeda, an instructor in the department, describes the results of the training.
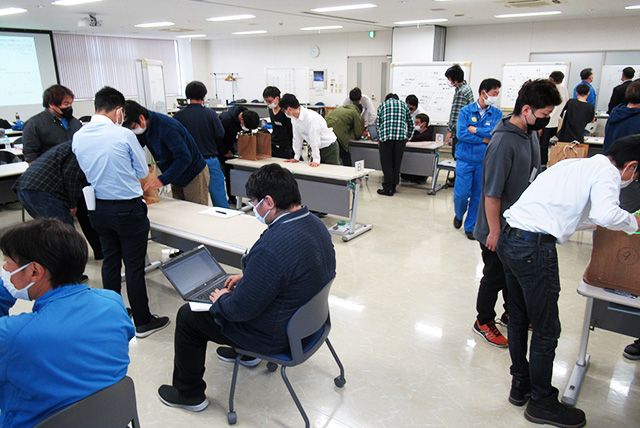
“Communication that transcends the distance between production sites seems to stimulate the participants. At Fuji Electric, which has a diverse range of businesses, including Power Electronics Energy and Industry, Power Generation, Semiconductors and Food & Beverage Distribution, some engage in manufacturing of massive products, such as equipment for power generation and substations, while others deal with small semiconductor components. They are vastly different in terms of product size, as well as the manufacturing period, which can vary from a single day to several years. These people talk to each other about the problems and concerns encountered on their respective workplaces. It seems to provide a good opportunity to grasp the essence of the subject, because making themselves understood to those who do not share their assumptions requires abstracting the subject. That tendency seems to have become stronger as they have been freed from online training to actually get together for training. It is a great moment for us instructors to witness the moment when the participants’ eyes light up.”
Manufacturing keeps changing— it’s why we cannot stop moving forward
A great number of difficulties have been overcome to establish a new training program. It has gone beyond the mere acquisition of knowledge and fostered lively communication and initiative. People of the Technical & Skill Training Department feel there has been a solid response to their effort. However, they do not like to be complacent and stop moving forward. It is because they know that, in order for the training to contribute to the ever-changing field of manufacturing, the teaching also needs to continue to evolve.
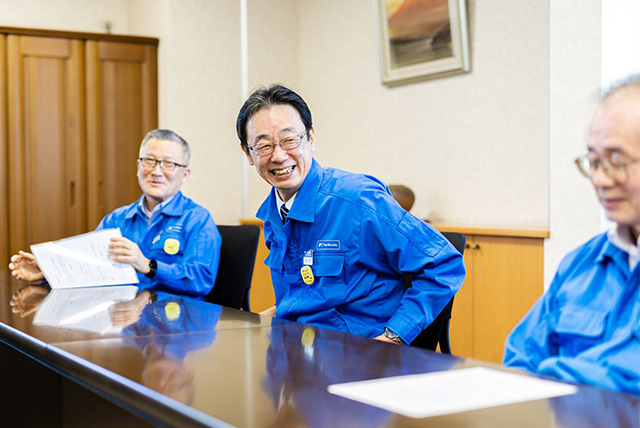
“What can be utilized on the shop floor must be provided. Otherwise, this training will become meaningless. That’s why we have to keep changing as well. We are continuing to update the training content based on feedback from the shop floor. For example, some have expressed a desire to learn about case studies of improvement and streamlining. We intend to bring opportunities for change to all our technicians,” says Aoki.
“It’s up to the participants themselves to figure out how they can apply the basics taught here on the shop floor. That's why I try to communicate the points that I want them to remember in particular. This training is mandatory to become a leader, but nothing comes out of a sense of duty. We should work together to create opportunities that lead to action on the shop floor,” says Ikeda.
“In addition to the Manufacturing Meister System, Fuji Electric is also taking on the challenge of visualizing the competence of technicians and providing them with more effective opportunities and training. After all, the source of manufacturing is people. By supporting Fuji Electric’s technicians, creating a solid core and encouraging them to take the leap forward, we hope to support the development of a fulfilling career for each of them, as well as the growth of the company,” says Nakamura.
Comments from Manufacturing Meisters
Atsushi Asano, Foreman, Manufacturing Department, Tokyo Factory, Power Electrics Industry Business Group
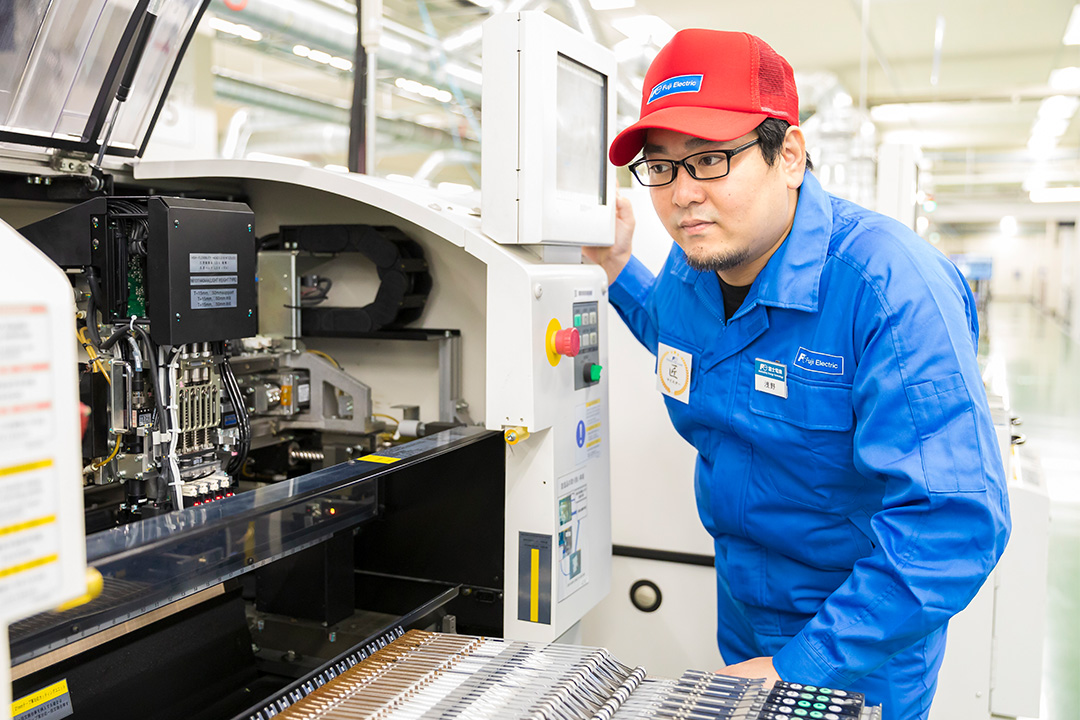
I am in charge of the automatic mounting process for printed circuit boards used in control equipment and measurement equipment, which are the main products handled by the Tokyo Factory. In the Meister training program, teaming up with Meisters from other factories and exchanging various ideas with them broadened my knowledge. When I came back to my shop floor, I found that I was able to approach improvement with a mindset that was different from before. I work on improvement while trying to come up with ideas together with other people on the shop floor, questioning “business as usual” and seeing if there are any inefficient processes or any ways to increase efficiency by cooperating with other departments.
There was a time when workers worked long hours during periods of high volume, and it seemed as if the whole staff was screaming. “Good products cannot be made unless the workers are healthy.” I believe that ensuring the health of workers is also my job as the foreman, and I intend to efficiently manufacture Fuji Electric's highest-quality products at a thriving workplace.
Katsuhiro Hasegawa, Manufacturing Chief and Foreman, Manufacturing Department, Chiba Factory, Power Electrics Energy Business Group
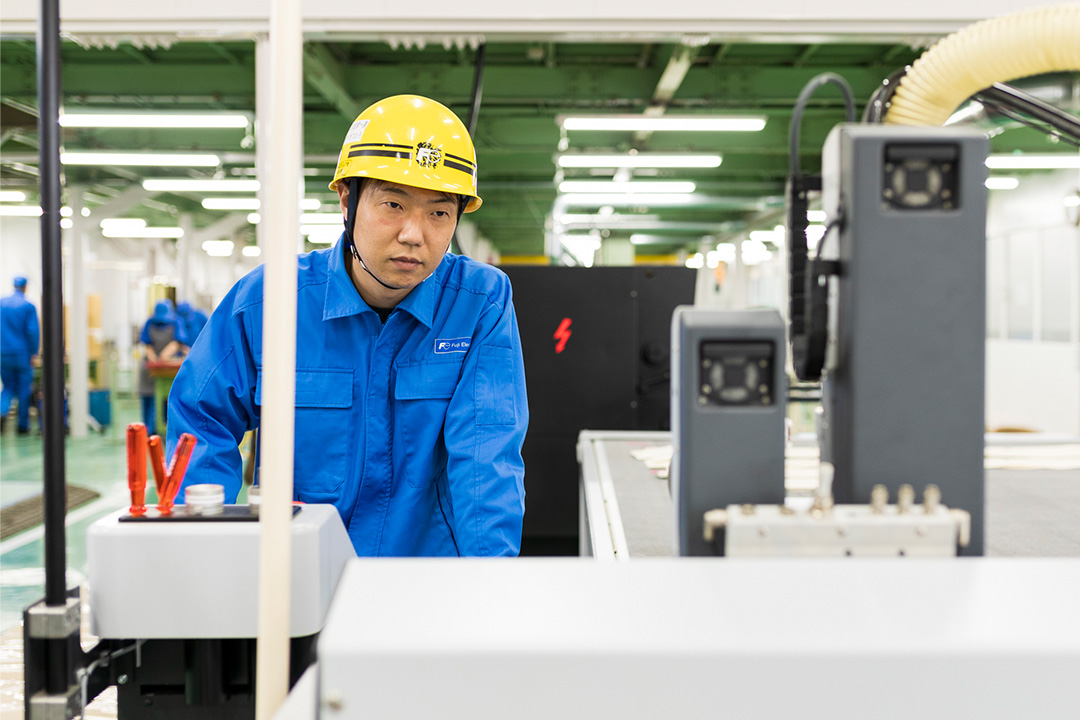
At Chiba Factory, we manufacture a variety of substation equipment including transformers and switchgear, ranging from extra-high to low voltage, and I am currently the foreman in the insulation process. The Meister training program gave me a good opportunity to share my worries and issues through group discussions, as well as sessions in which we shared stories of hardship with people from other factories. We had many issues in common even though we manufactured completely different products, and listening to everyone who had ideas that were different from mine often led to solutions for my workplace. I am making use of what I have learned in the Meister training program, such as the importance of quantification, to work on the automation of skilled tasks that have not been quantified.
“If it’s the same work, do it the easy way, and get it done more easily.” This is what I learned from my training school teacher when I was a rookie. I believe that this phrase is packed with the key elements of manufacturing, such as the importance of carrying out work safely, accurately and quickly, without overburden or wastefulness. I will move ahead with improvement activities to create a workplace where this can be experienced.
Contribution to SDGs
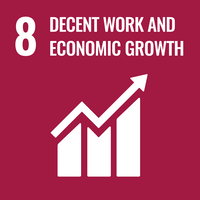
In our Corporate Code of Conduct, we declare our intent to “respect and value all people” and state that we will strengthen the human resource training process so that each employee can develop and the full potential of teams can be reached. This also contributes to our target for the SDG “8. Decent work and economic growth,” and in manufacturing training, we aim to train production engineers and technicians who will lead to global competitiveness by systematically providing education and training according to job type, class level and individual skill level.