How a data collection system supports “next-generation car manufacturing sites”
Not even the slightest abnormality is overlooked! Conditions on the production line are clearly discernable even from a distance! How a data collection system supports “next-generation car manufacturing sites”
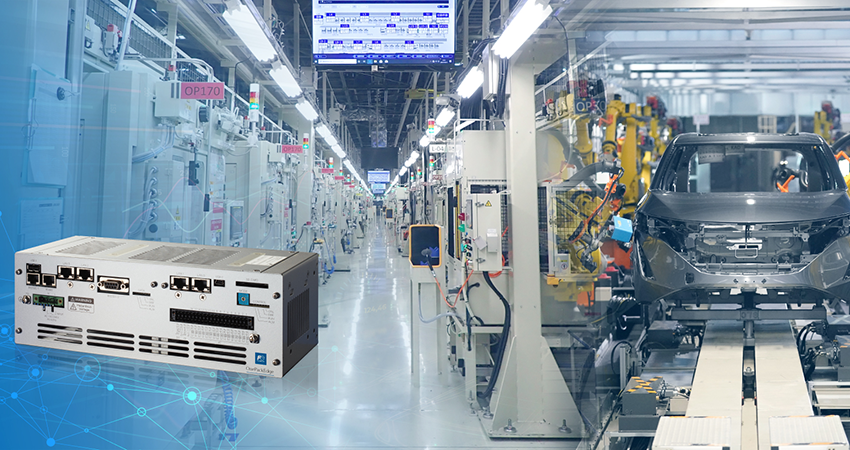
The Model T Ford was born in 1908, over a century ago. What made the Model T Ford revolutionary was its method of production: an assembly-line system that is commonplace today. It was this system that made automobiles affordable to the general public.
Fast-forward to 2021. Nissan Motor Company has just unveiled its “Nissan Intelligent Factory,” a facility based on the concept of “next-generation car manufacturing.” The place is the Nissan Tochigi Plant’s production line.
The world of automobile manufacturing is changing with blinding speed. Behind its historic advancements is “OnePackEdge,” Fuji Electric’s assembly process data collection system.
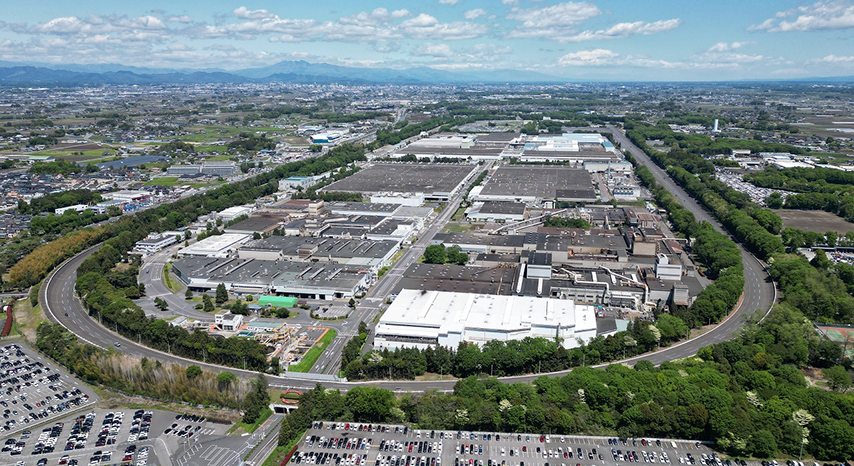
Don’t stop the production line! If it stops, get it restarted immediately!
“More and more, ‘automation’ is becoming the keyword of the future. If we can entrust human tasks to robots, we will be able to reduce errors and produce higher-quality products.”
These are the words of Mr. Shinya Ito of the Mass Production Engineering Group, Powertrain Production Engineering Department, Powertrain Production Engineering and Development Division at Nissan’s Tochigi Plant.
In the automotive industry, as in the manufacturing industry as a whole, the “skill” of those who manufacture components and assemble them can affect manufacturing speed and product quality. The Nissan Intelligent Factory, unveiled in 2021, aims to consistently mass-produce products of “the highest quality” by building into robots skills that have been amassed over long years by craftsmen.
“Take, for example, the engine parts that are under my responsibility. We manufacture those parts at a rate of about 100 per hour. We then send the parts to the next section along the engine assembly line. So, if the engine parts production schedule falls behind, this will affect following processes.”
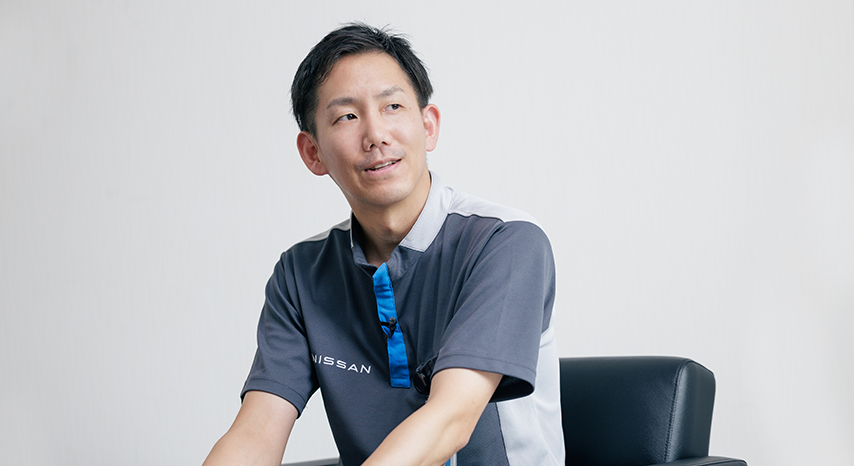
A delay of 5 or 10 minutes can significantly impact as work proceeds to subsequent processes.
How to keep the production line moving without stoppages? That is a question to which Nissan and other manufacturing companies pay constant attention.
“However, there are always situations in which production must be stopped. Sometimes, we encounter situations where it is unavoidable to stop the production line. When this happens, the main priority is to resume production as soon as possible. To prevent the recurrence of errors, it is necessary to analyze the situation and identify the root cause. This requires daily ’visualizing' and accumulating various processes and data.” (Shinya Ito)
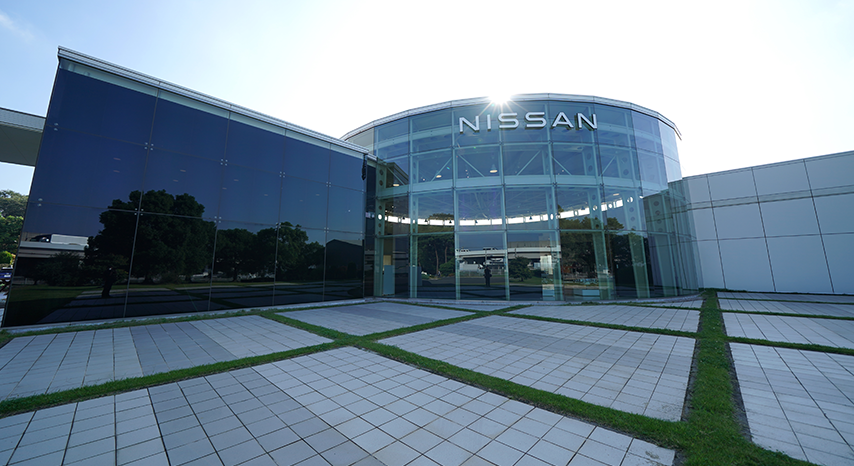
“Visualizing” craftmanship through quantification and accumulation
“We want to bring a data collection system to our brand-new engine parts production line.”
It was in 2016 that Nissan first approached Fuji Electric.
Nissan wanted Fuji Electric to help it address three main issues:
(a) To collect data with minimal modification to production facilities.
(b) To collect data from all facilities using the same format.
(c) To create a common database that can be applied to a variety of purposes.
OnePackEdge, Fuji Electric's assembly and processing data collection system, was introduced in response to these requirements.
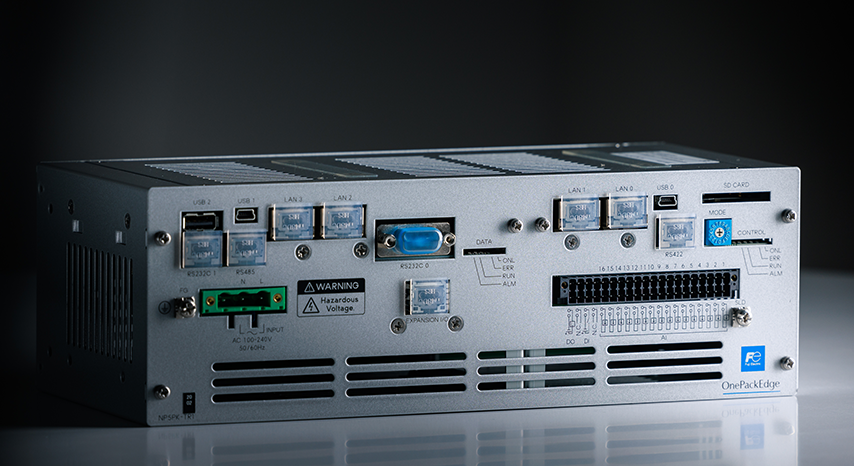
When proposing a product, we usually do so as an external supplier. However, in this case, Fuji Electric employees worked with Nissan personnel at the actual production site between 2016 and 2018 to conduct preliminary verifications of the system’s effectiveness.
Yusaku Ito of the System Planning Section, Planning Department, DX Promotion Office, Information Solution Division in Fuji Electric’s Industry Business Group says, “The system’s greatest feature is that it can consolidate measurement data from each piece of production equipment and, quite literally, create a single package from them.”
“With it, customers can easily collect data from their facilities without making major equipment modifications. The product’s strength is that it consolidates, accumulates, and visualizes collected data from multiple production facilities.”
Many plants—not just those of Nissan—use equipment supplied by multiple manufacturers. In such cases, using OnePackEdge can unify the data output methods of equipment from different manufacturers.
Hiroki Kambara of Fuji Electric’s Power Electronics Sales Group says:
"We installed the system on a production line that comprised equipment from more than 20 different manufacturers. In order to collect and output the data that Nissan required, we had to negotiate repeatedly with each of the equipment manufacturers. This project was Fuji Electric's first large-scale undertaking of this kind, so we faced challenges in coordinating the opinions of all the manufacturers. However, we were able to overcome these difficulties by developing solutions with our system and minimizing any necessary modifications to the equipment."
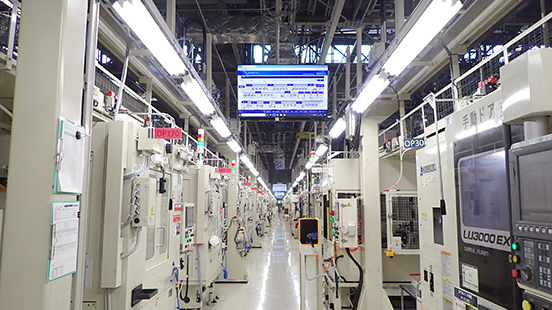
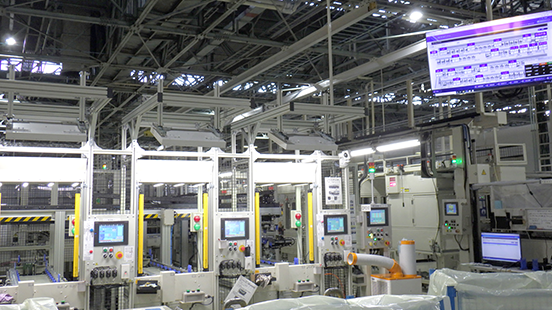
Engine parts processing line (courtesy of Nissan Motor Co., Ltd.)
The project got underway in 2016. The system went operational on the Tochigi Plant’s first line in 2020 and second line in 2021.
87 units of “OnePackEdge ”are installed on the first line and 83 on the second. After beginning operations at the Tochigi Plant, the system was also put into service at Nissan’s Iwaki Plant in Fukushima Prefecture and at Nissan Kohki Co., Ltd., a Nissan affiliate.
Nissan’s Mr. Ito says this about the effects OnePackEdge has delivered:
“When a problem occurred in the past, we had to rush from the office to the problem’s location, check the situation, and then return to the office to decide how to deal with it. But with OnePackEdge, we can see at a glance what happened and on what equipment just by starting up the computer. In addition, we can now collect analog information, such as daily operational reports that used to be handwritten, in digital form. This capability dramatically increases the speed at which we can identify and resolve problems. It really helps us.”
Even now, with production lines in operation, we continue to provide system updates in response to requests from the plant floor.
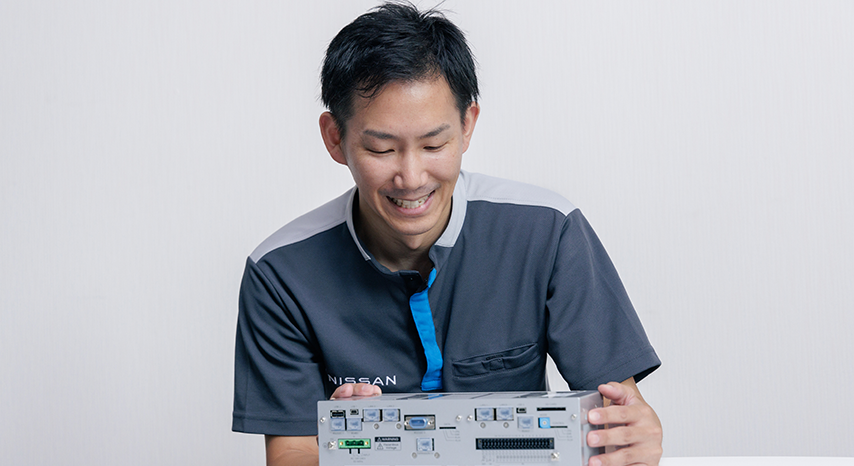
Continues Nissan’s Mr. Ito:
“The OnePackEdge units installed on each piece of production equipment collect data on the serial number assigned to each engine part. This lets us track the number to find out which equipment the part went through and its condition when it did so. We can also download data at selected periods of time. At Nissan, we are studying ways of further utilizing the collected data to achieve ‘the highest quality’.”
He adds:
“For example, if the vibration generated when drilling a hole exceeds a standard value, it is possible that the product is defective, even if it does not appear to be so to the naked eye. By visualizing such values as data, we should be able to keep defective products from moving on to subsequent processes and prevent production line stoppages due to malfunctions.”
Mr. Ito says the new lines equipped with OnePackEdge attract attention at the Tochigi Plant. In fact, some people working on other lines say things like, “I didn’t know you were doing this. It looks quite handy!”
Finally, when we asked Mr. Ito what led Nissan to use OnePackEdge, he answered, “Fuji Electric’s speedy response and competitive pricing.”
When we specified the type of data we needed, you promptly responded and presented us with new proposals, offering suggestions like "why not try this approach?" This was a great help. Additionally, your installation costs were considerably lower than those of other companies.
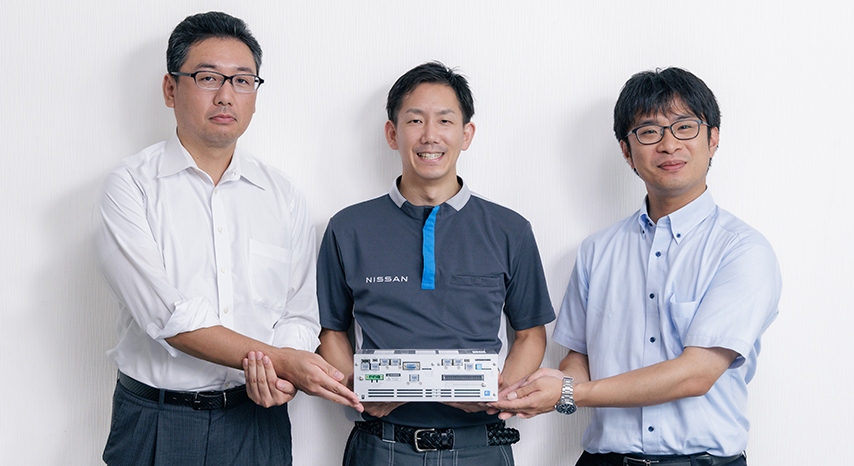
“I would urge anyone considering using OnePackEdge to speak with our sales representatives. We will propose solutions that can help resolve your production site issues.” (Hiroki Kambara)
Fuji Electric’s technology is about to turn a new page in the history of automobile manufacturing.
Contributing to SDGs
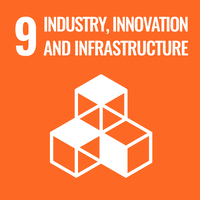
OnePackEdge is a unique IoT solution that drives manufacturing innovation.
It helps resolve a variety of issues faced by production sites, including preventing diminished on-site capabilities due to human resources shortages, responding to mass customization, improving quality, and reducing lost costs and lost time. Such benefits contribute to our efforts to address SDG Goal “9. Create a foundation for industry and technological innovation.”
Recommended
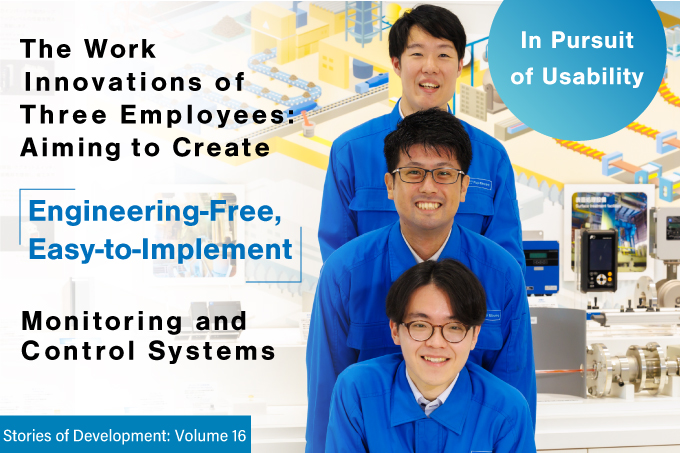
July 2,2025
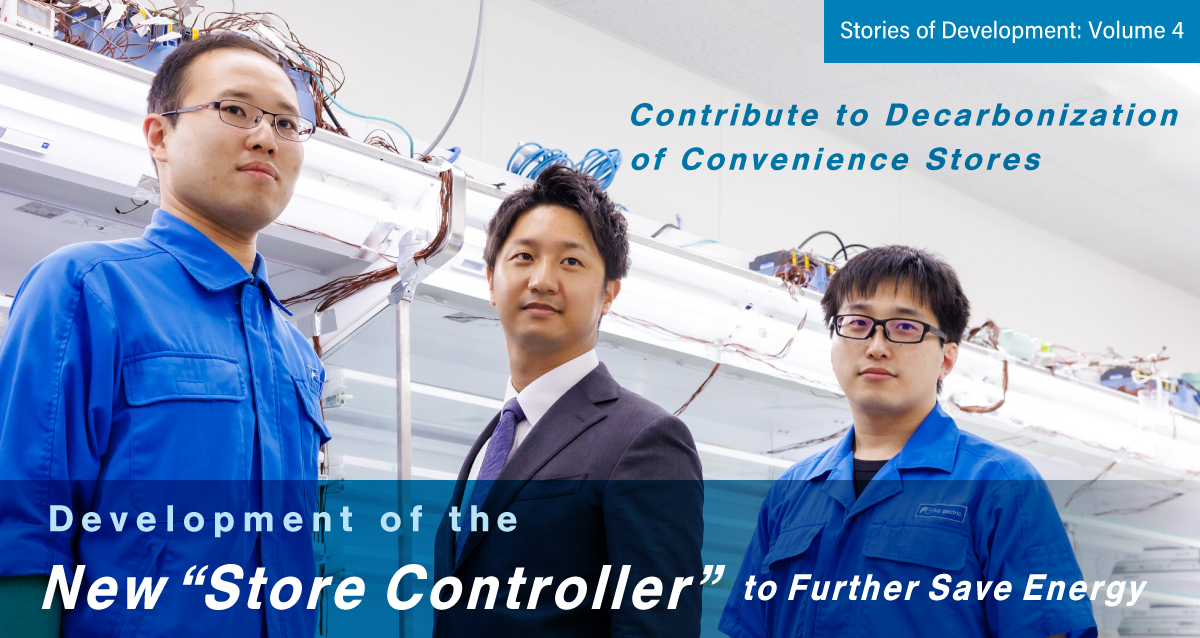
October 18,2024
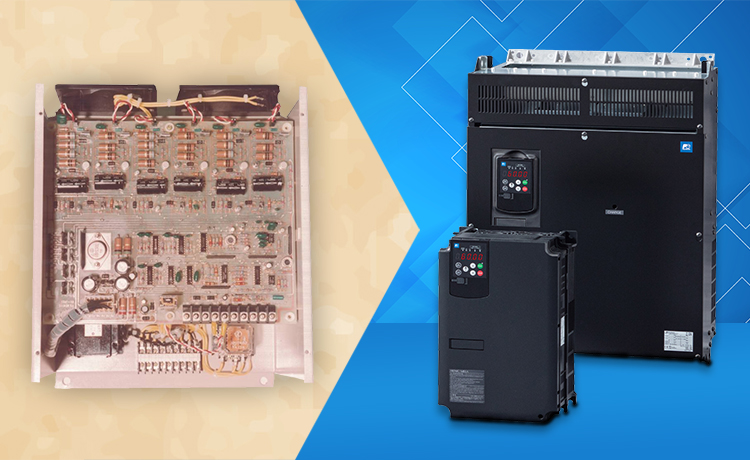
June 23,2023
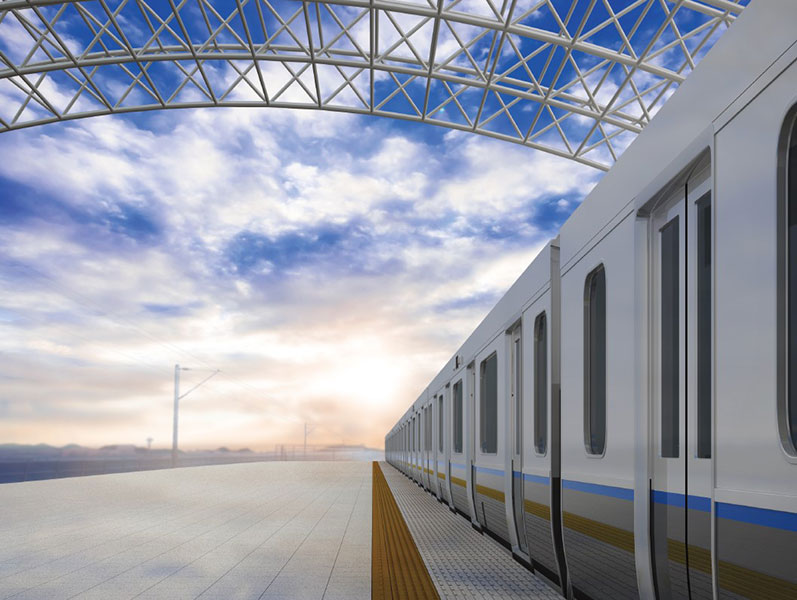
June 22,2023