Low-Concentration Emissions Aren’t Off the Hook! Progressing Toward Carbon Neutrality with New CO2 Separation and Recovery System Technology
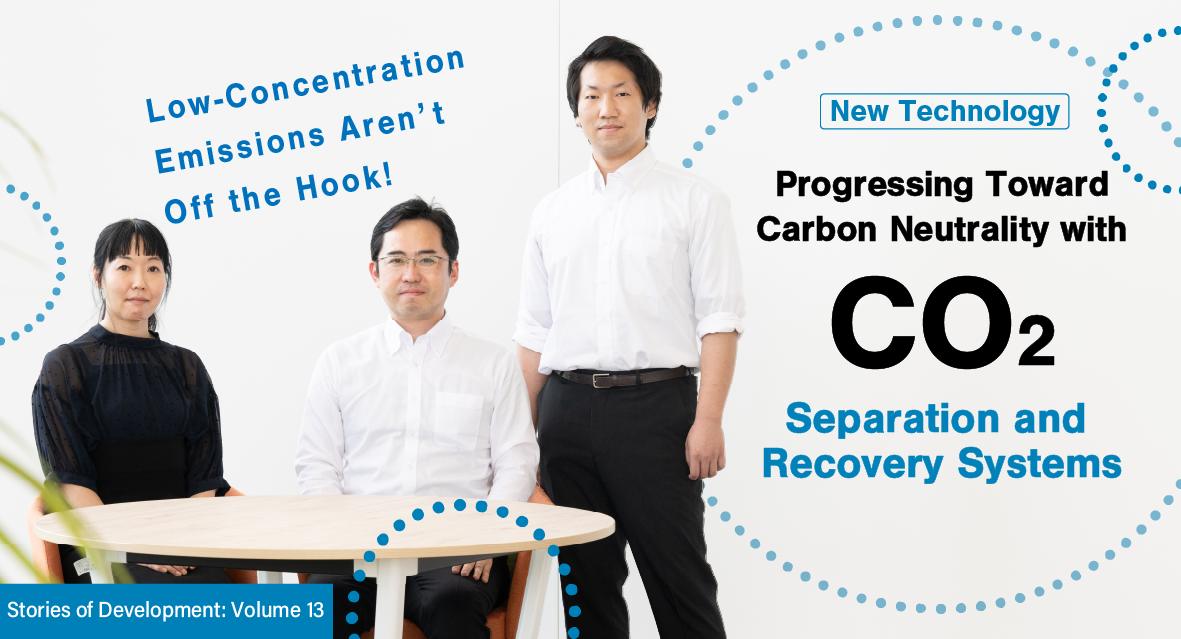
Japan has set a goal to reduce greenhouse gas emissions and achieve carbon neutrality by 2050, but reaching this target will not be easy. Achieving this goal requires us to reduce CO2 emissions from exhaust gas with low CO2 concentrations, which have previously been overlooked. Efforts are underway to recover CO2 from exhaust gas emitted from countless small factories and ships.
We spoke to three members of the development team behind Fuji Electric's CO2 recovery technology, who strive to contribute to a decarbonized society through innovative technologies.
“Many a Little” to Promote Carbon Neutrality
A system to separate and recover CO2 from exhaust gas emitted from power plants and factories is currently under development. The recovered CO2 can be stored in the ground or under the sea. In addition, it can even be reused as a resource to achieve carbon recycling. However, the issue of low concentrations makes this difficult to achieve.
Mr. Fukumura, the leader of the development team explains why.
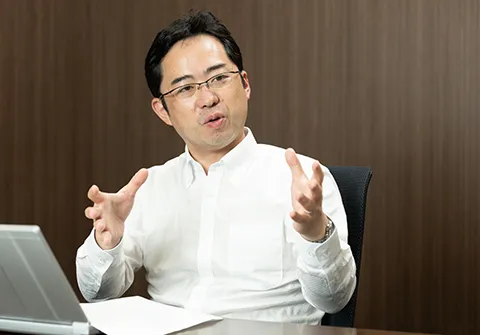
“Exhaust gas from factories and ships consists of 75% nitrogen, 20% oxygen, and just 5% CO2. It is extremely difficult to collect this 5% efficiently."
Large-scale CO2 recovery efforts have been made at thermal power plants and in the cement industry, which emit high-concentration CO2. On the other hand, measures to recover low-concentration CO2 emitted from factories and ships have fallen behind. Though each source only emits a small amount, when combined, they account for more than 10% of total CO2 emissions. As they say, “Many a little makes a mickle.” To achieve carbon neutrality, recovery of low-concentration CO2 is essential.
Moreover, the International Maritime Organization (IMO) has established targets for reducing greenhouse gas emissions by 2030, including a 20–30% reduction from 2008 levels for ships and a 46% reduction from 2013 levels for factories. Few companies have entered the low-concentration CO2 recovery business, and while it presents challenges, new needs are rapidly emerging.
In 2021, Fuji Electric became one of the first companies to begin developing a system to recover CO2 from the exhaust gas emitted by factories and ships. Regarding the difficulties they face, the team leader Mr. Fukumura relates, “Core technologies must be developed not just by combining existing technologies, but also by devising an efficient grand design for the systems and processes."
Technology to Recover CO2 from Exhaust Gas
There are four methods for separating and recovering CO2 from exhaust gas: the chemical absorption method (amine method), the physical absorption method, the solid absorption method, and the membrane separation method. Fuji Electric is developing technology that uses the membrane separation method, which is expected to enable low-cost operations. The technology recovers CO2 by passing exhaust gas through a special filter (membrane) that only CO2 can penetrate, separating it from other components. The process does not involve chemical reactions or phase changes (transitions between gas, liquid, and solid states). For this reason, the technology requires less energy and can reduce the size of separation equipment.
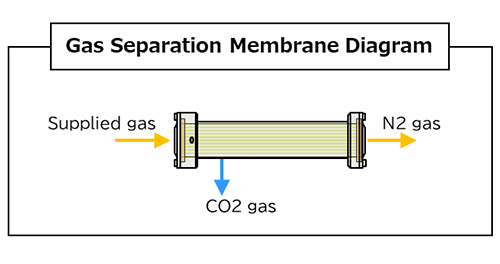
Control Technology to Operate Systems with Low Power
Existing membrane separation methods use high-capacity blowers to pump exhaust gas into the membrane. On the other hand, Fuji Electric's membrane separation method features a two-stage depressurization process in which the vacuum pump and circulation blower are controlled synchronously. As the vacuum pump extracts only the gas components that pass through the membrane, this process consumes less power than conventional systems that pressurize all of the exhaust gas.
A ship’s power is limited. Since this separation and recovery system can be operated with low power, CO2 can be recovered while leaving enough power for ship operation.
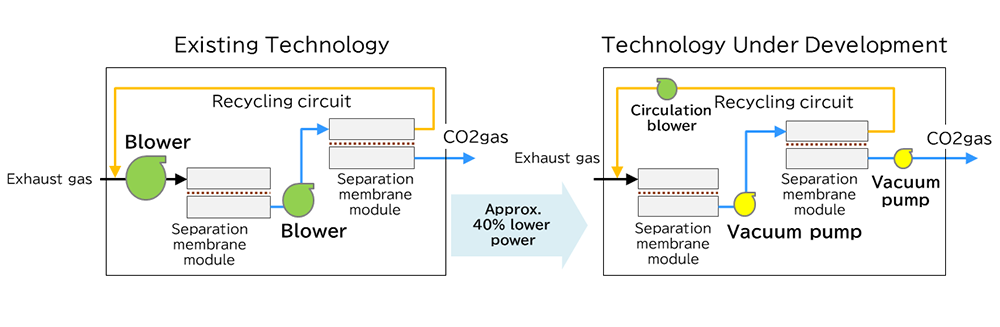
However, failure to maintain a balance between the gas flow rate and pressure prevents stable operation, and in the worst case, may lead to equipment failure. Therefore, precise control technology is essential.
“Connecting and controlling multiple power devices is difficult, but Fuji Electric can utilize its expertise in this area,” says Ms. Tagishi, a developer of control technology.
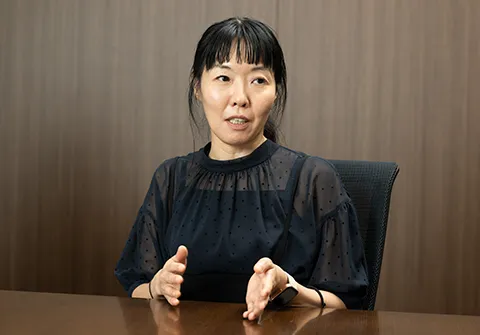
"The CO2 separation and recovery system utilizes our phosphoric acid fuel cell technology. The designs drafted by my senior colleagues were extremely complex, and I am always amazed at how they managed to fit all that piping into such a small plant. As we develop this technology, we have been incorporating the process design and packaging technologies that Fuji Electric has cultivated over the years,” Ms. Tagishi explains.
Addressing Accidents Through Steady Experimentation
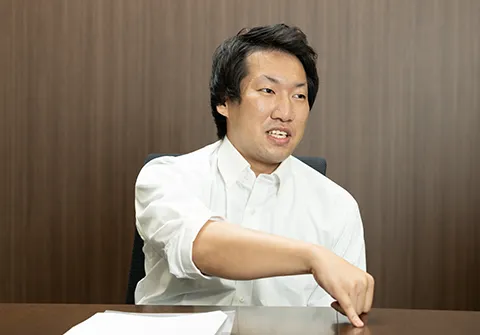
The separation membrane used in the equipment has been tested with the help of the membrane manufacturer. Tasked with building the system, Mr. Haruyama told us about the difficulties faced in the research stage. “Initially, there were many cases where the expected membrane performance did not match the testing data,” he explains.
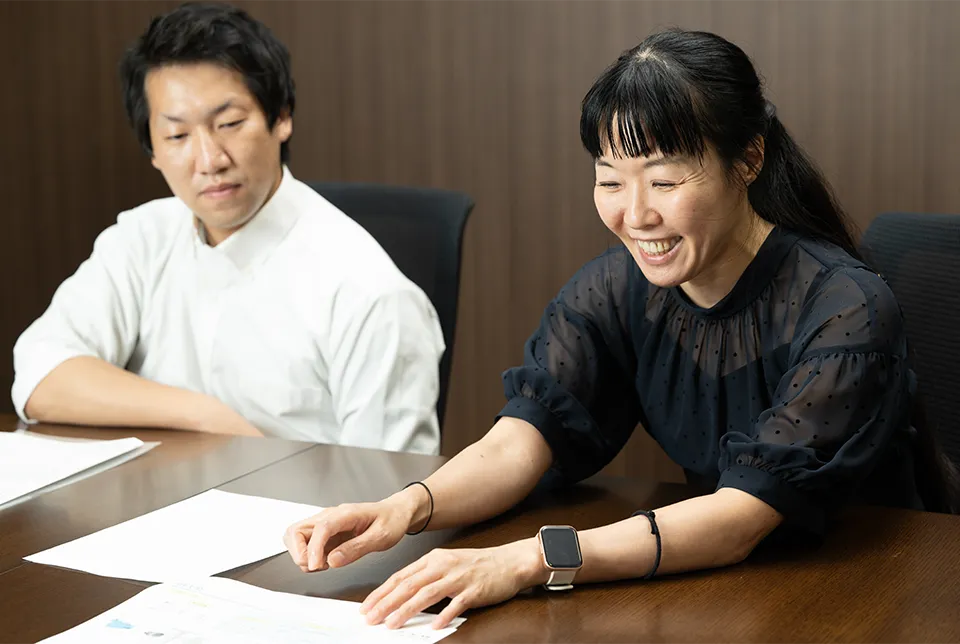
After about a month of steady experimentation, they found that a 2 to 3°C change in membrane temperature affects the flow rate of CO2 through the membrane. “It was an unexpected accident, but we’re happy with the result because we were able to obtain useful data for development,” Ms. Tagishi and Mr. Haruyama recall.
If the membrane is brought to market as a product in the future, it is highly likely to contribute to cost savings. The two continue their research every day in pursuit of an even better membrane.
Ideas from Experiments in the Marine Field
Fuji Electric's advantage is that it combines a CO2 separation and recovery system with a pretreatment system. By removing heat and dust from exhaust gas before feeding it into the CO2 recovery system, equipment failure and deterioration can be prevented.
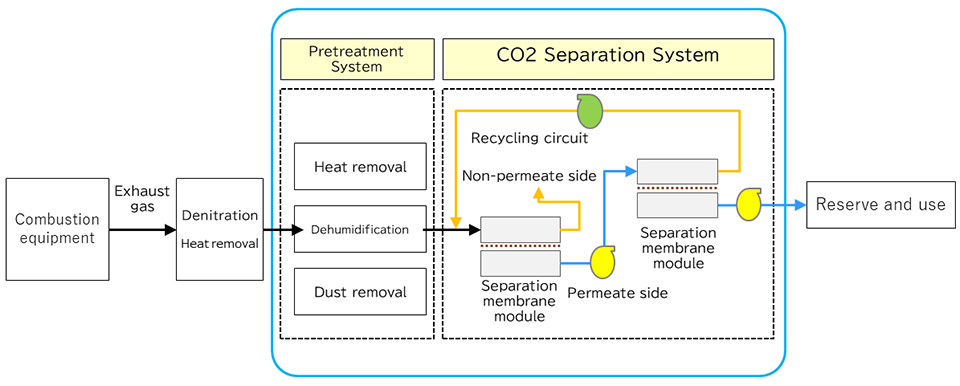
In the past, Fuji Electric has brought to market equipment to remove SOx (sulfur oxides) emitted during the combustion of heavy oil by ships, which has a track record of use in the shipping industry and in factories.
“It was thanks to our existing technology that the idea to combine CO2 recovery with pretreatment was born. I believe that we can efficiently tackle the challenges faced by society by leveraging our own technologies and linking them together,” Mr. Fukumura says.
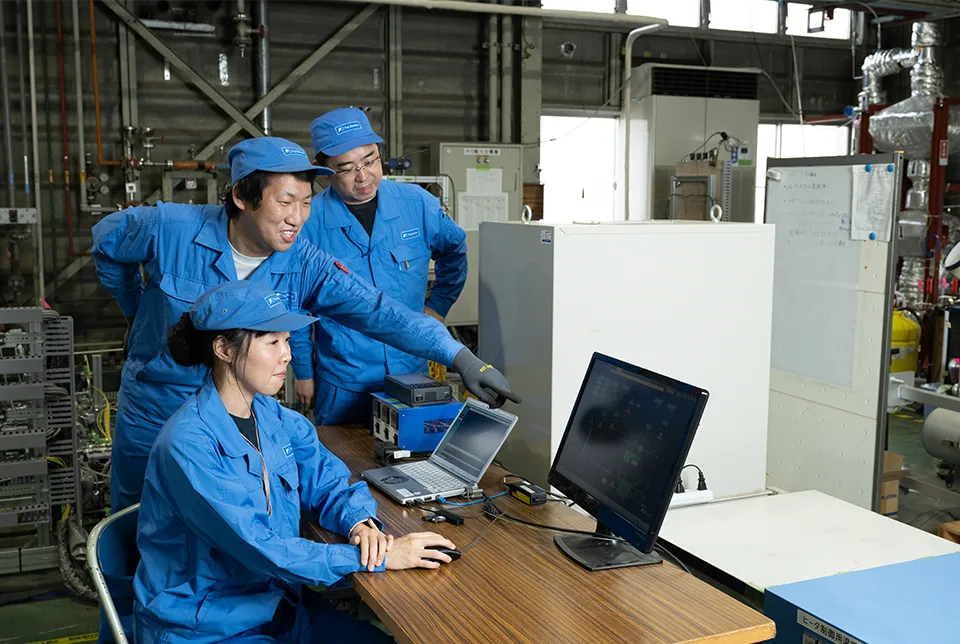
Prototype Complete! Aiming for Early Launch
A prototype of the CO2 separation and recovery system was completed at the end of December 2023, and simulated gas containing exhaust gas and certain components was fed into it to test whether it could recover CO2.
As the three of them watched anxiously, wondering whether the prototype would work properly, the system began to operate without issues.
Having had no previous experience in separation membranes or plant design, Mr. Haruyama says that he instinctively blurted out, “There’s no way this is actually working so well.” Tasked with estimating the amount of CO2 to separate, Ms. Tagishi had been searching for the optimal combination of equipment and control methods needed to achieve this goal. “With this result, it was a relief knowing we could go into the New Year with peace of mind,” she recalls.
However, another major test is scheduled for the end of the 2024 fiscal year.
“Next, we will connect the CO2 separation and recovery system to the pretreatment system. We will run the entire CO2 recovery system while feeding it real exhaust gas, so we may run into a lot of problems. I’m excited to see if it works out,” Fukumura says.
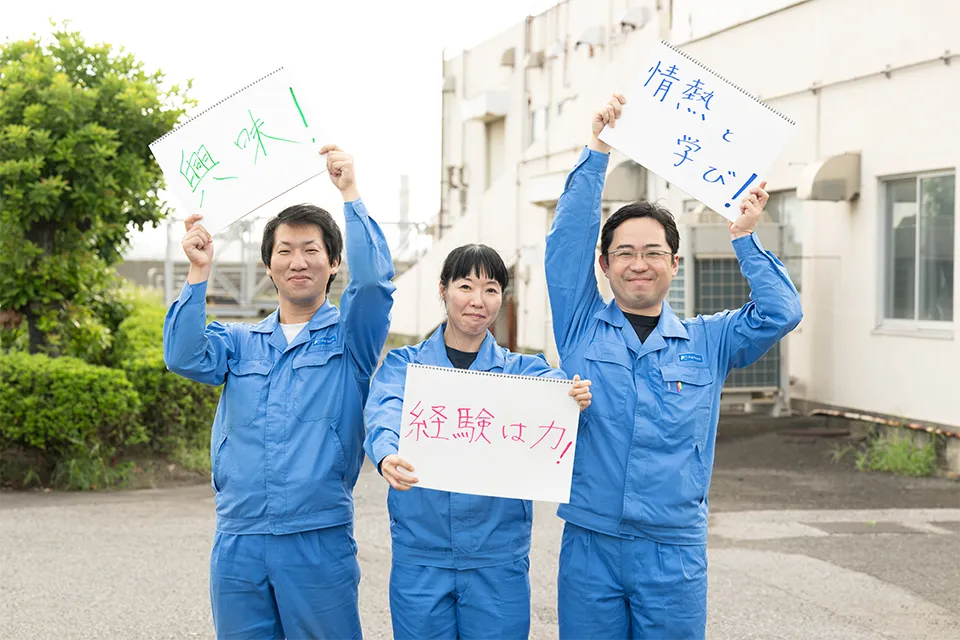
We asked the three team members to write a message to students.
"I like new things, so I'm the type of person who enjoys learning about topics I don't know much about,” Mr. Haruyama (left) says. “I think you can manage to do mostly anything as long as you are interested in it.”
Ms. Tagishi (center) relates, "Even if you think you're not good at something, as long as you keep pushing, your experience will become your strength. It’s sure to come in handy someday!”
“Fuji Electric is a company that lets you do what you want to do, so you can stay very motivated as you work,” Mr. Fukumura (right) says. “We are provided with a fulfilling educational environment that allows us to improve ourselves, as well as opportunities to learn through communication with experts from our own company and other companies. It’s a workplace full of passion and learning.”
Although they will face many difficulties along the way, Mr. Fukumura is positive that “the team's collective strength will overcome them.” The three continue to take on challenges with the aim of bringing the technology to the market as soon as possible.
Recommended
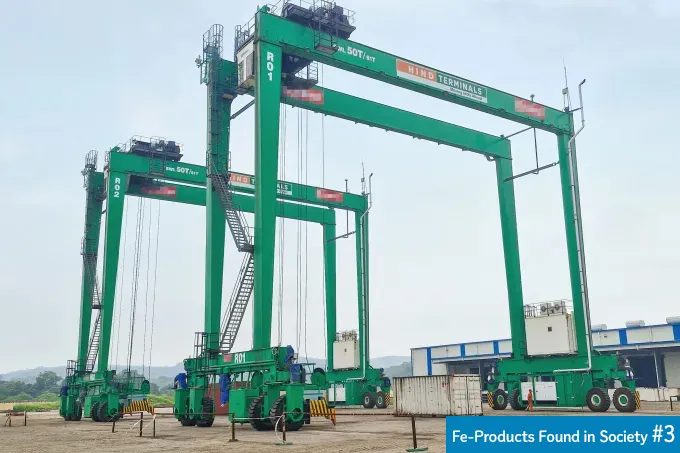
July 30,2025
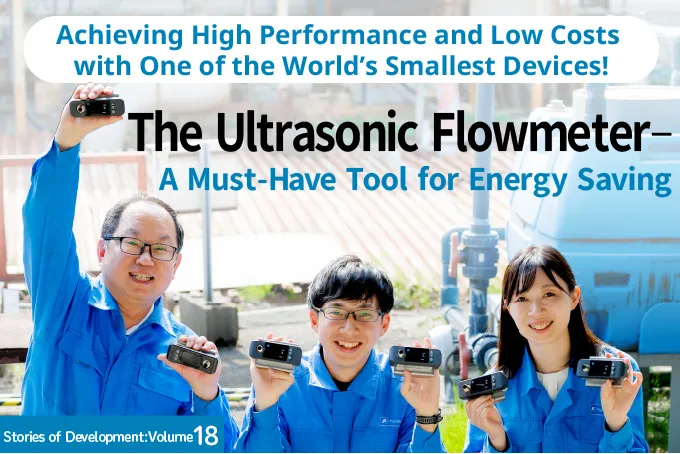
July 28,2025
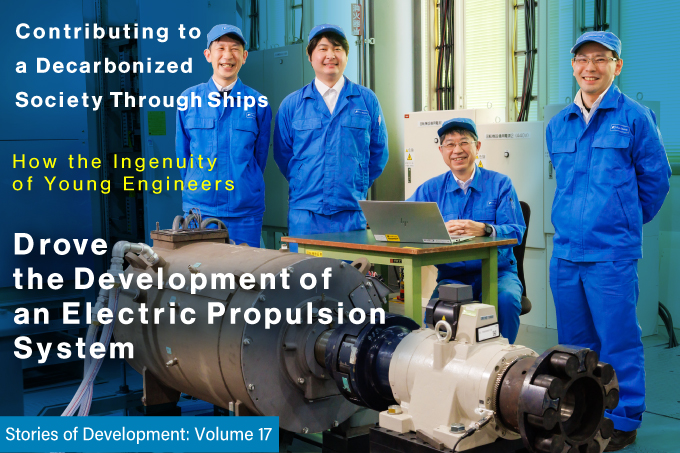
July 7,2025
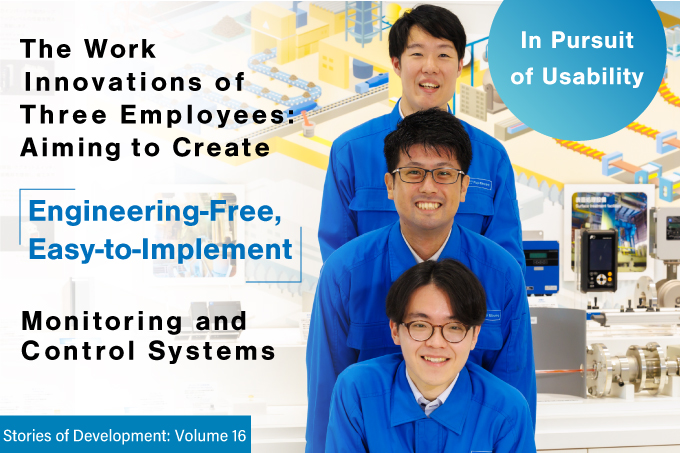
July 2,2025