Developing Storage Battery Systems for the Supply-Demand Adjustment Market
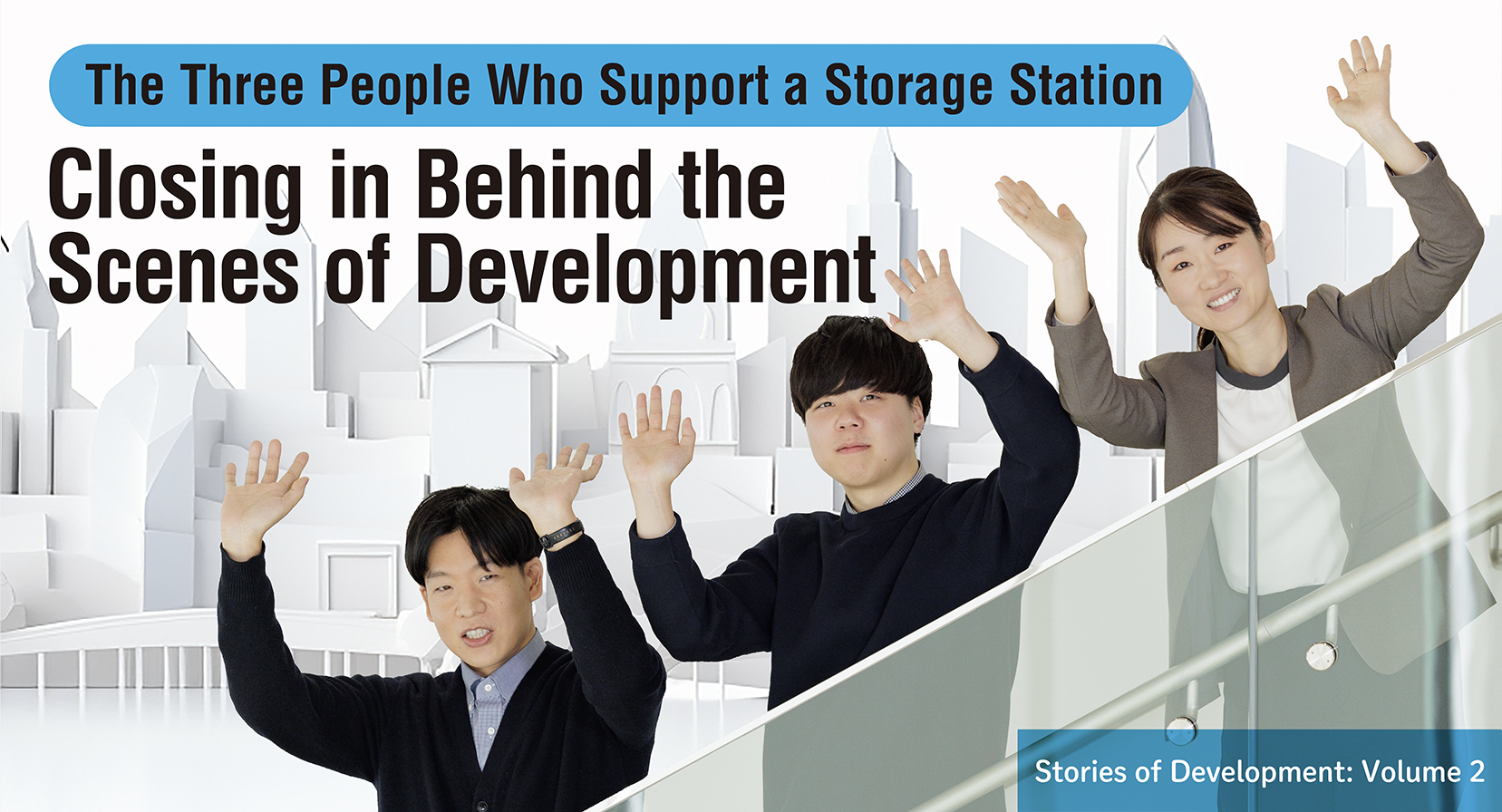
If the balance of power supply and demand can be adjusted through charging and discharging, we can effectively utilize renewable energy with unstable electricity generation.
“The EV Battery Station CHITOSE” is a power storage station with a capacity of six megawatts. It is slated to begin full-scale operation in Chitose City, Hokkaido, in the spring of 2024. This project is being promoted by Sumitomo Corporation using storage batteries for electric vehicles. With our core technology called power electronics, which can control electricity freely, Fuji Electric is participating in the project by supplying an extra-high-voltage electric distribution facility, power conditioning systems (PCSs) for storage batteries, and control equipment.
This power storage station is the first time Fuji Electric has worked on a storage battery control system for systems* for the supply-demand adjustment market. We spoke to the three Fuji Electric employees who were involved in development on the forefront to get a glimpse into the difficulties behind the scenes in the project and the start of changes in working styles that go beyond solving social issues.
-
*System: A network that transmits high-voltage power from power plants to other parts of the country
-
Fast charge/discharge of 100 to 200 ms
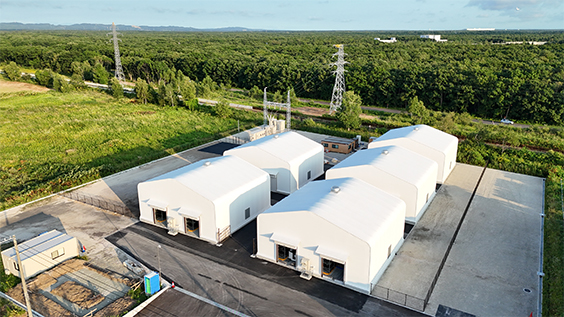
The supply and demand balance of electricity must always be the same at the same time of day, or else a shortage might cause a power outage, as a worst case example. Because of factors like these, the introduction rate of renewable energy sources like solar power and wind power, which cannot generate power stably due to weather variations or lack of sunlight, is only about 20% in Japan.
Decarbonization is a global trend, but in order to achieve it, Japan needs to increase its renewable energy introduction rate. Given this, storage battery systems that regulate the balance of power supply and demand by charging and discharging are attracting more and more attention and their introduction has been promoted. This is accelerating the enhancement of the supply-demand adjustment market, which uses stored electricity as power to regulate the balance between supply and demand.
Fuji Electric, which has been developing storage battery systems since the 1990s, has now begun full-scale operation of the “EV Battery Station CHITOSE”.
The storage batteries are new and used batteries from Nissan Motor Corporation’s Leaf electric vehicle (EV). In five buildings, about 700 batteries are arranged in an overlapping fashion, where they charge and discharge repeatedly.
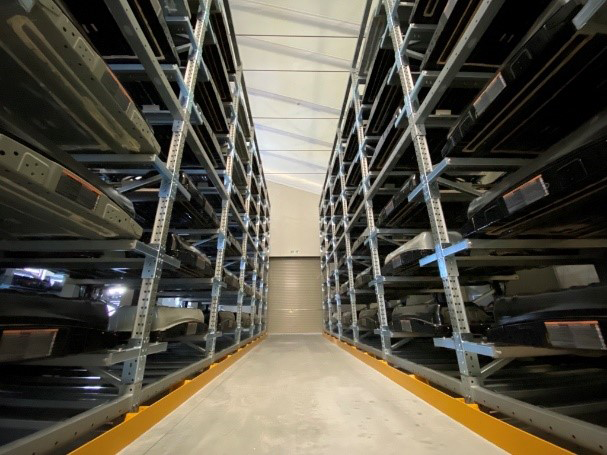
Fuji Electric’s storage battery systems play an active role in this charging and discharging.
The system controller, which serves as the control tower of the system, checks the status of the individual batteries connected to the eight battery power conditioning systems (PCSs) and distributes the charge/discharge control command values at high speed. The PCSs perform power conversion (switching between DC and AC) in response to commands from the system controller.
After all, the strength of Fuji Electric’s storage battery system is how quickly it can switch between charging and discharging. It can do this at a high speed of 100 to 200 ms depending on the electricity supply and demand situation.
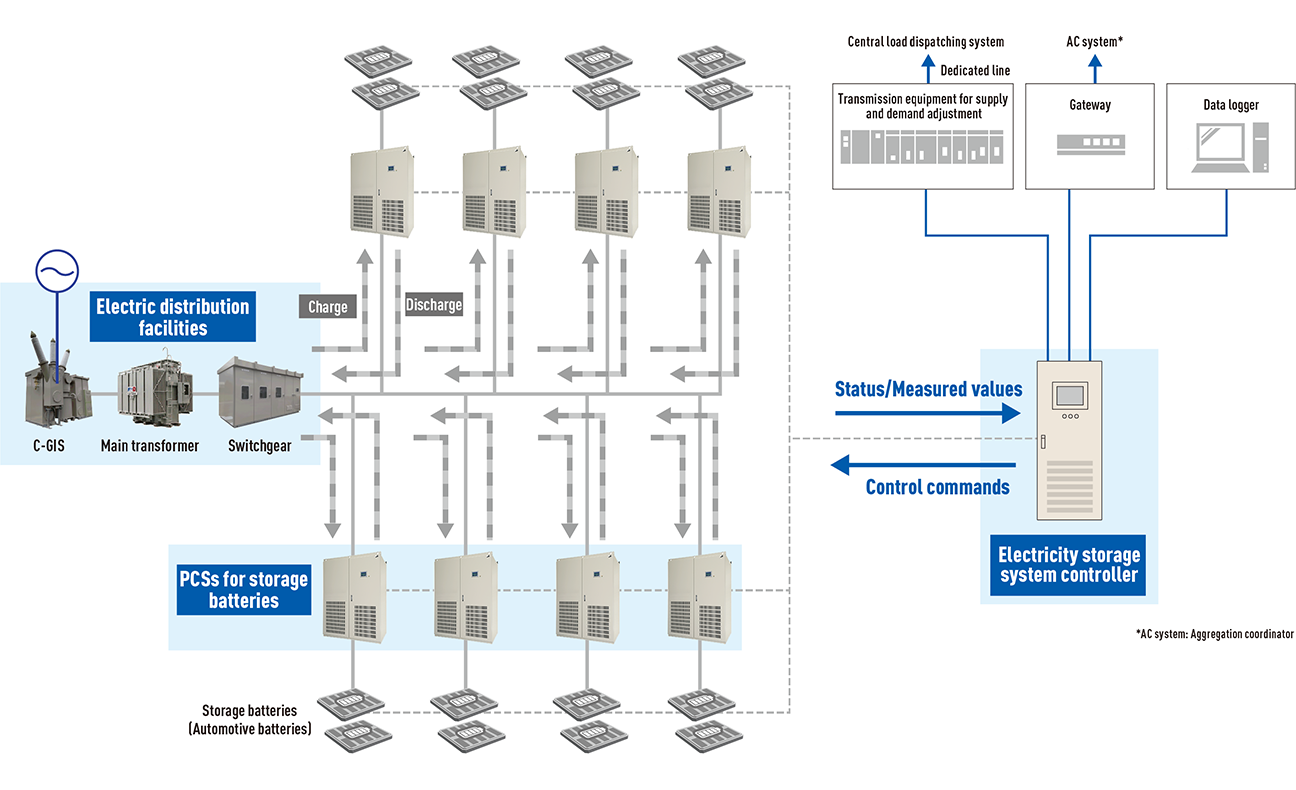
Opportunities for young employees to play active roles
Looking back on the progress thus far, project leader Kanemoto of the Energy & Control Engineering Department says,
“We endured so many difficulties, and it was only when the design department, testing department, and other organizations worked together as one team that full-scale operation was finally in our sights.”
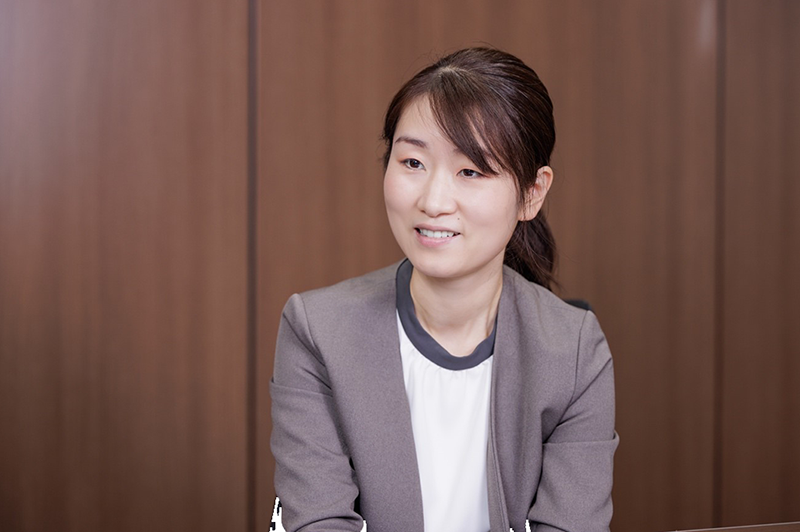
The biggest challenge was to finish in-house verification of the control software to be incorporated into the control system controller by the time the field test started in order to ensure stable operation of the storage batteries. The key was how accurate we could make the test. We had limited time before the field test began.
The person responsible for the design and production of the control software was Enomoto of the Transmission and Distribution Systems Engineering Department. He joined the company in 2022 as a new graduate, and at the end of that same year, he was selected as a member of this large-scale project. While he worked to absorb the company’s control expertise, he was assigned to work on the Chitose project as a key member of a team made up of his senior colleagues.
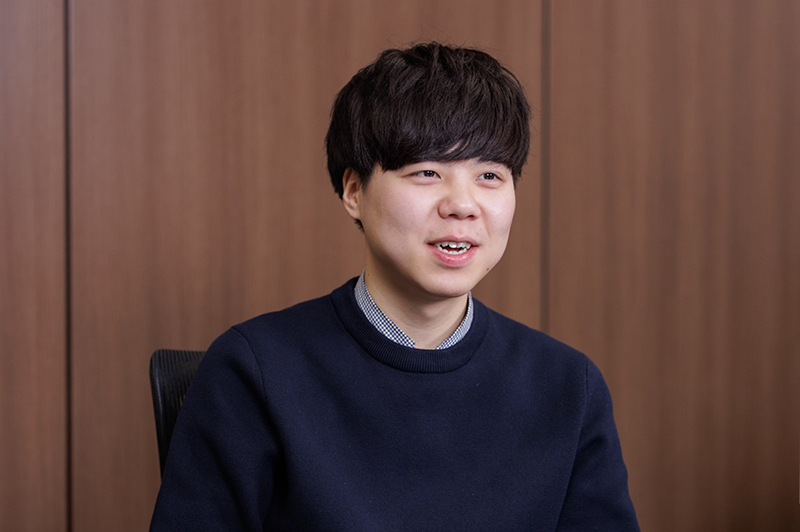
Cooperation between the testing and design departments toward a shared purpose
The development of a testing environment for in-house verification was carried out simultaneously with the design of the control software.
An EV battery unit is about the size of one tatami mat (approx. 0.88 × 1.76 meters), and it can weigh as much as 300 kg. The system was supposed to be tested at the Tokyo Factory, where space is limited, so it was not possible to conduct the test with more than 600 actual units.
“That’s why the design department and the testing department put their heads together to build a simulator and create an environment similar to the Tokyo Factory’s actual production environment,”
says Yoshimoto, a field engineer in the Power Plants Commissioning Department.
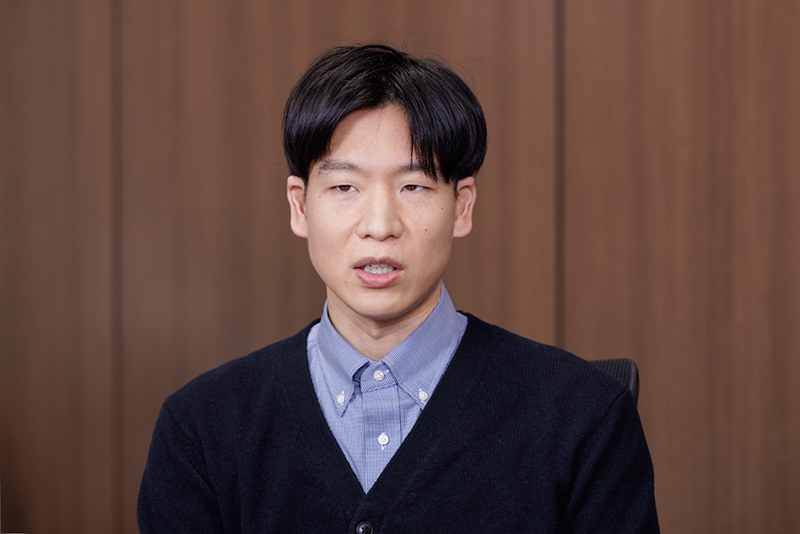
The Power Plants Commissioning Department where Yoshimoto works spends about half of the year visiting customer factories and facilities all over Japan to make sure that the systems are working properly. Yoshimoto worked on this project from the initial phase onward while splitting his time with activities like these.
In the past, Yoshimoto had not had many opportunities to be involved in engineering or design, but things were different this time.
He says, “This was the first project I was ever involved in where we had such detailed discussions with the design department.”
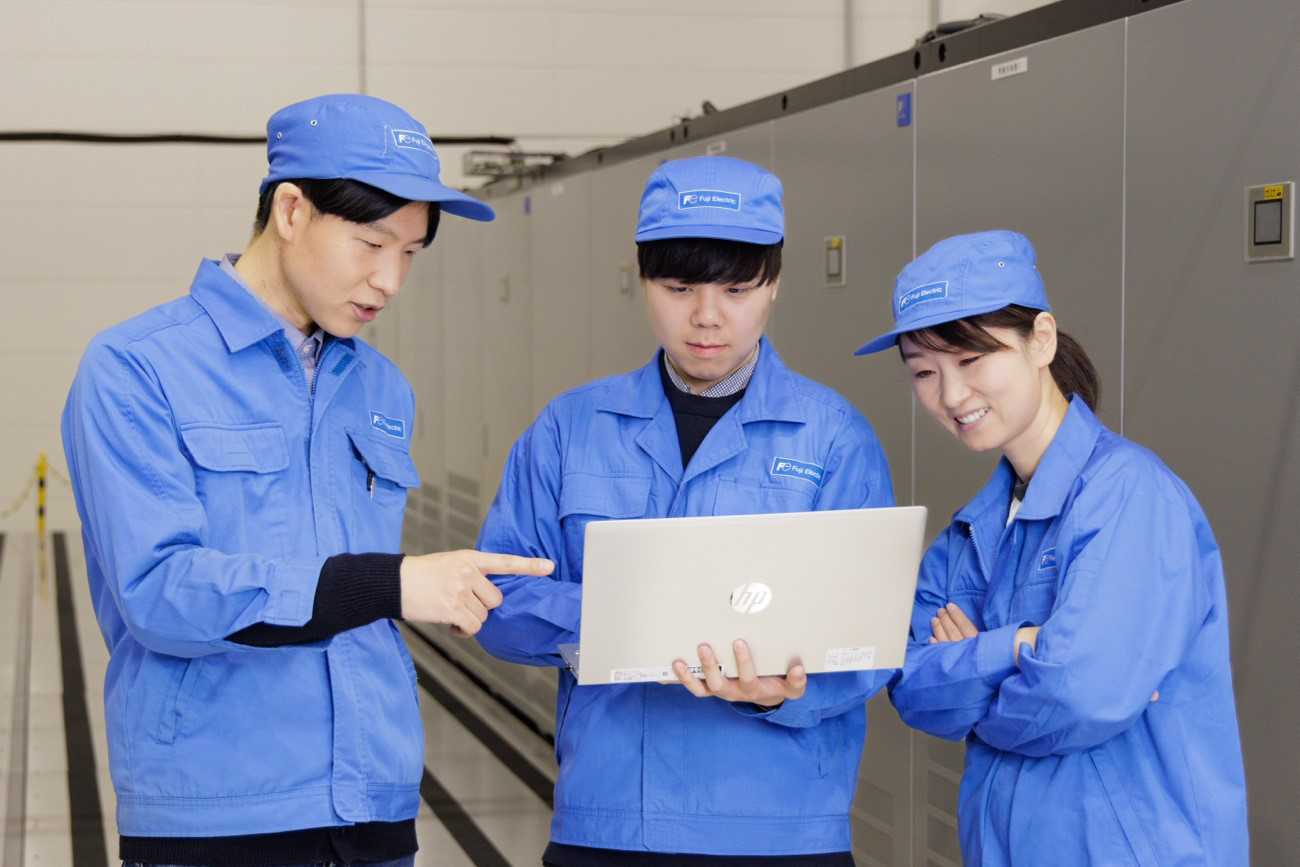
In May 2023, when Enomoto had finished designing the control software and the test environment similar to the actual production environment was in place, the Tokyo Factory began in-house verification of the software.
Unfortunately, it was then that obstacles began to rear their heads.
Cooperating across departmental boundaries toward a solution
Luckily, he was able to get through by relying on the expertise of seasoned experts. When Enomoto would return from a test, they would approach him with advice, asking what the text results had been and suggesting potential next steps. Looking back on those days, Enomoto says,
“When I was first put in charge of design and development, I thought, ‘Why did this happen to me?’ But then my boss and senior colleagues turned out to be experts who could give me all the information I wanted and more. I had many opportunities to talk with them every day, and it was the kind of atmosphere where they were ready to listen even when I had to deliver bad news. I really appreciated that.It was thanks to their incredible support that I managed to overcome those difficulties.”
Yoshimoto got to see the work of the design department up close and share what he knew.
“I think that being able to share knowledge across departments allowed us to make a more perfect storage battery system,” he says.
After several months of testing at the Tokyo Factory, the storage battery system was finally completed.
A by-product of Chitose project
Of course, the success of the project itself is important, but the Chitose project might also have created something extra, or a by-product.
Project leader Kanemoto, who had just returned from childcare leave at the time, says that the project to create a test environment similar to the production environment will serve as a model case for the future.
“When multiple projects overlap, we have always had a hard time finding people because of their other commitments. For example, some departments involve a lot of traveling,” he says. “Thanks to this project, we have created a new system that allows us to conduct tests in an environment equivalent to the customer’s right here at the Tokyo Factory. If we use this system as a platform, we will be able to propose various ways of working for employees who are raising children or providing nursing care for family members. It also has the effect of facilitating skill improvement on the individual level by getting more people to participate in a project.”
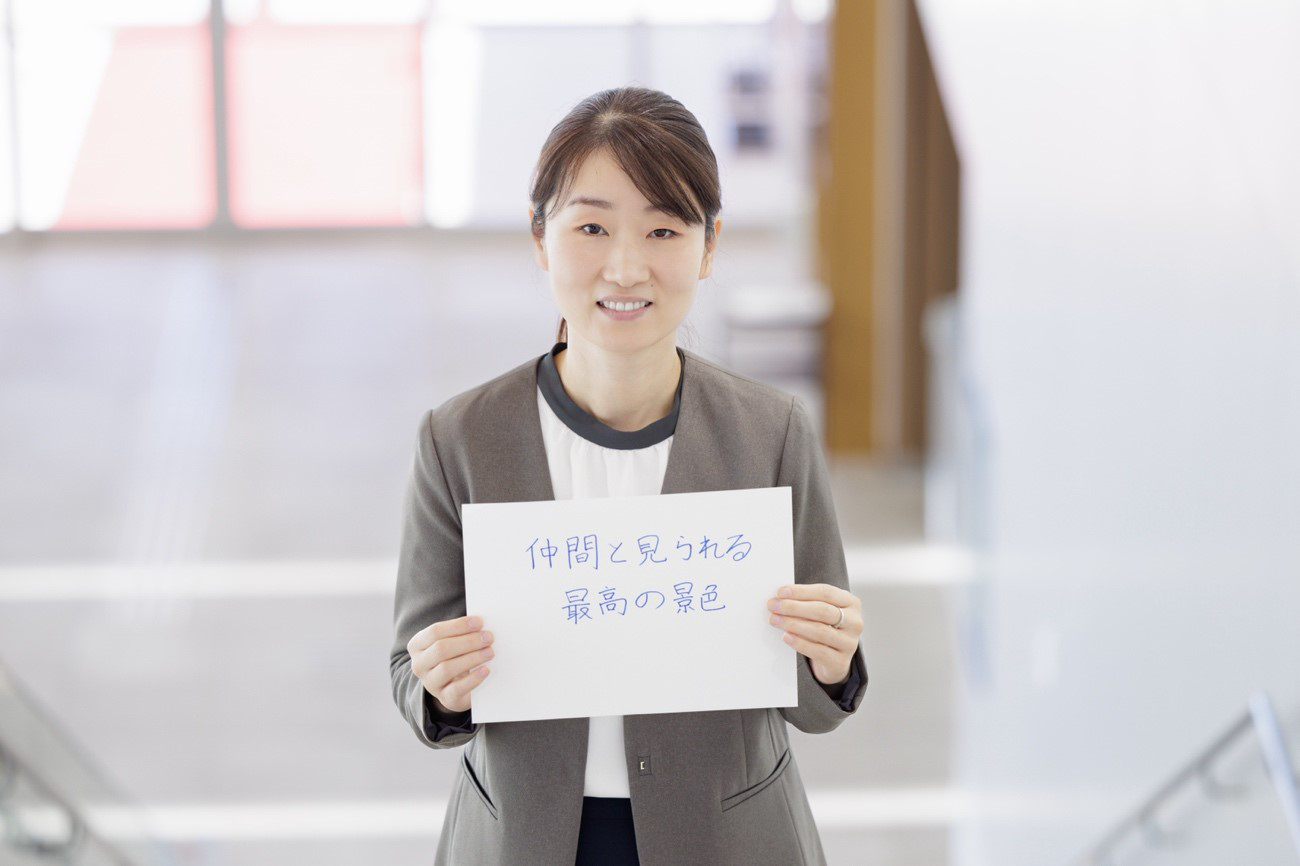
Kanemoto wrote, “The best view is one that you can share with your colleagues,” commenting, “In our workplace, people support one another to solve problems.”
Enomoto, the Gen Z employee in a major role, is using his own development as motivation for his work. He believes that acquiring skills will lead to reducing the cost and improving the quality of products and systems, which will allow him to contribute to the company.
“Being in charge of the Chitose project has allowed me to improve my skills a little,” says Enomoto. “I’ll continue to give it everything I’ve got!”
Yoshimoto, a mid-career employee, sees the Chitose project this way:
“I’ve been in the testing department since I first joined the company, so all these business trips are normal to me, but some people have circumstances that make this lifestyle difficult for them. Now that we have successfully set up a test environment at the Tokyo Factory, I think that people will have more working style options.”
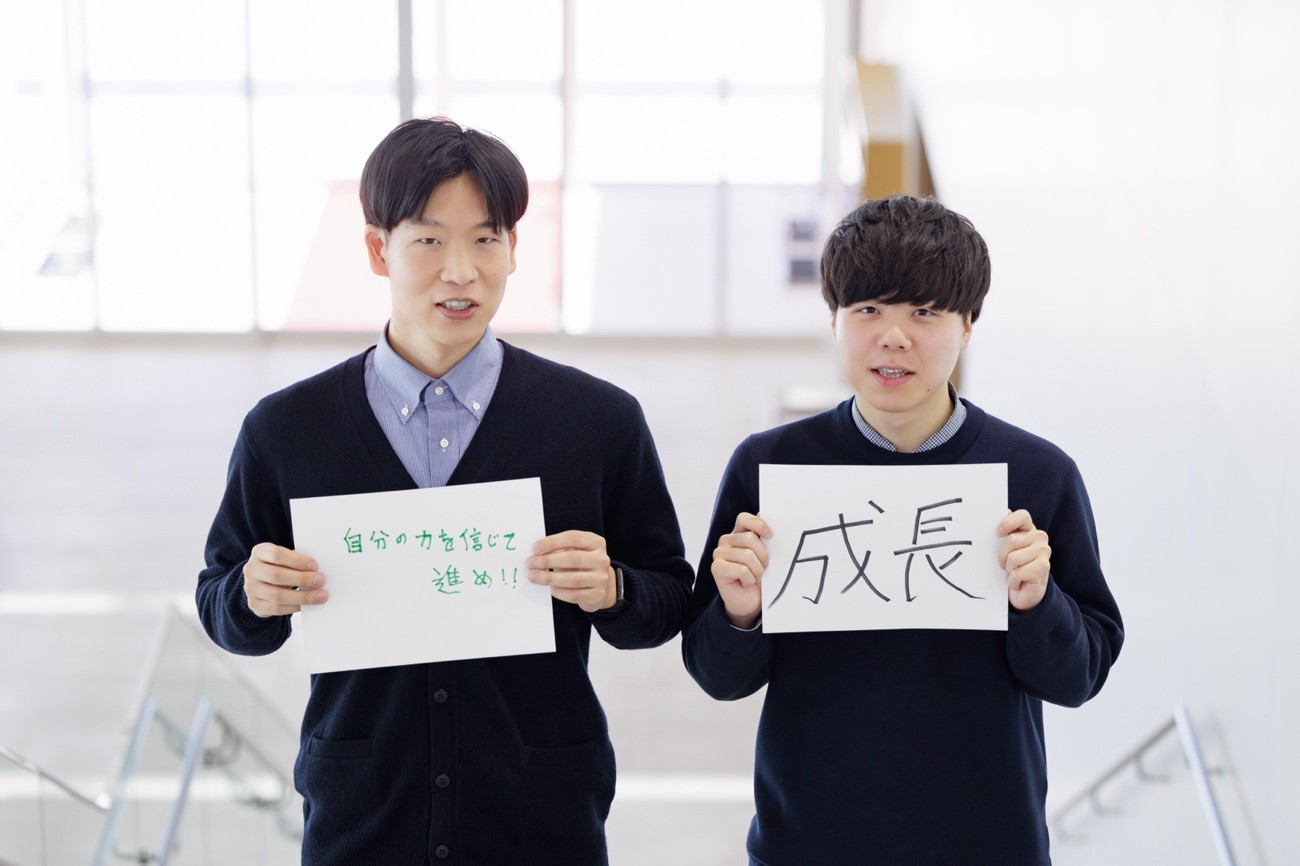
Completing a project through teamwork across departmental boundaries.
Working together to create an environment where each and every employee who supports the site can find satisfaction in their work.
The aim of the Chitose project is to realize the mission of solving social issues and to bring about new working styles that create synergy of teamwork, such as encouraging collaboration across departmental boundaries and facilitating a balance between work and childcare/nursing care.
Recommended
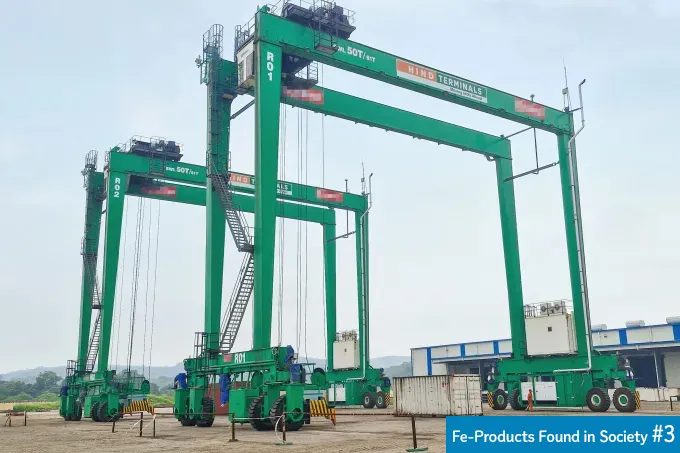
July 30,2025
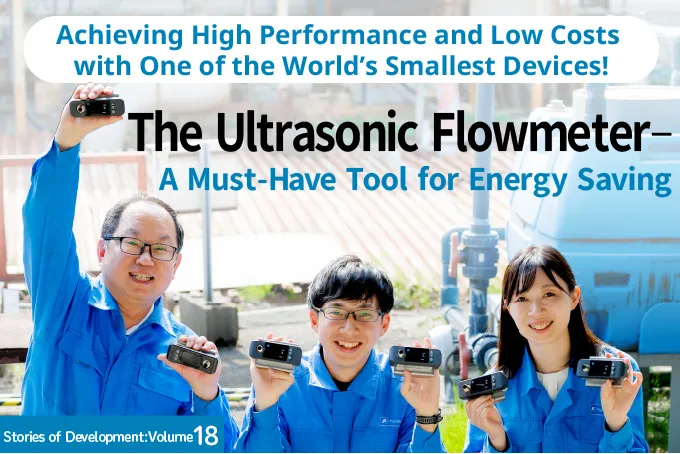
July 28,2025
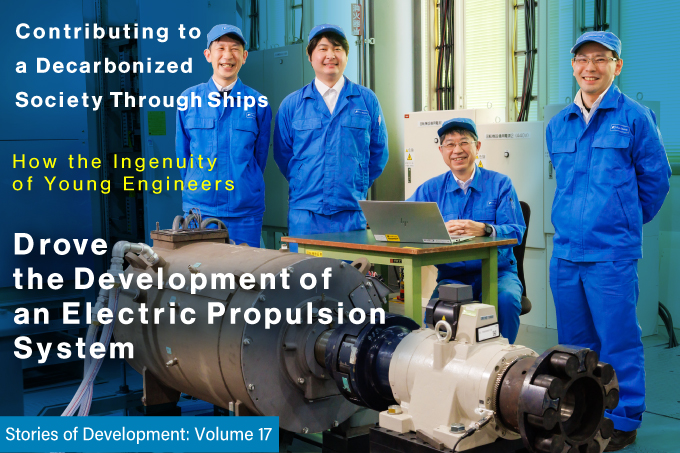
July 7,2025
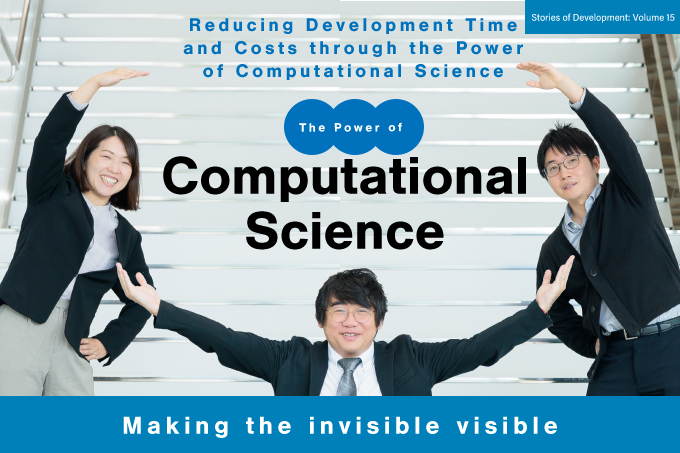
June 27,2025