IoT usage in factories
Understand in just 10 minutes!
Quick explanation of IoT usage in factories
Quick explanation of IoT usage in factories
IoT is an abbreviation for Internet of Things. IoT literally refers to technology that enables all types of devices to be connected to a network and communicate with each other in order to exchange data and control devices.
For example, IoT home appliances have become popular items these days. There is an increasing number of devices available that can be used to control various things, For example, you can remotely turn on the lights or air conditioner in your house before returning home using your smartphone, or remotely monitor your rooms and pets using network cameras. IoT is contributing to these types of devices.
This is how IoT is being currently used all around us. However, as part of a larger framework, IoT is also playing an important role in driving the digital transformation (DX) of the industrial world.
That is why the introduction of IoT is indispensable for modern factories in terms of achieving high quality manufacturing, increased productivity and efficient use of energy.
-
Worldwide expansion of IoT in manufacturing industries, including concerted efforts among emerging nations
-
Optimizing entire factories by adopting the most advanced industry-proven smart factories!
-
PLCs as essential key components for constructing smart factories
-
Latest IoT progress in smart factories! Specific success stories
Worldwide expansion of IoT in manufacturing industries, including concerted efforts among emerging nations
Presently, industries around the world are racing to digitalize their operations.
For example, Germany was quick to launch Industrie 4.0 as a national project involving industry, government and academia in order to promote the 4th industrial revolution through the use of IoT.
The United States also launched the Industrial Internet Consortium (IIC) led by companies such as GE, IBM, Cisco Systems, Intel and AT&T.
Furthermore, emerging nations are also active in this field.
The Chinese government has been promoting “Made in China 2025” as a 10-year plan that began in 2015. Similarly, India and Thailand are respectively moving forward with “Made in India” and “Thailand 4.0” and are rushing to digitalize their manufacturing industries in line with Germany’s “Industrie 4.0” initiative.
Likewise, Japan is also advocating
“Society 5.0” (https://www8.cao.go.jp/cstp/society5_0/)
as an initiative similar to Germany’s.
Japan’s initiative is broader than “Industrie 4.0” and encompasses society as a whole.
In the “5th Basic Plan for Science and Technology” of the Cabinet Office, the initiative is defined as a “human-centric society that balances economic development with the resolution of social issues through advanced systems that integrate cyber and physical spaces.”
Optimizing entire factories by adopting the most advanced industry-proven smart factories!
Industrialized countries around the world, including Germany and Japan, are using IoT to break away from traditional forms of factory automation and process automation, and are promoting the construction of the most advanced industry-proven “smart factories.”
Smart factories collect a variety of data from various machines and sensors in the field and then store it in cyberspace (on-premise and in the cloud). By using AI technology to analyze big data, the newly created value and insights can be reflected in the physical world of production sites. This type of system is known as a “CPS” (cyber-physical system).
Smart factories repeat the four phases: “data collection,” “data accumulation and analysis,” “optimization” and “implementation.” Aiming for more efficient optimization of the entire factories, the PDCA cycle is implemented.
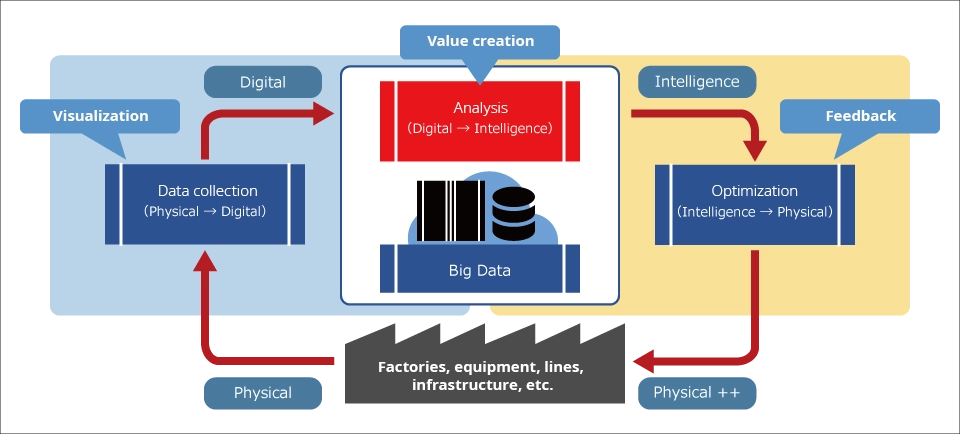
This makes it possible to “optimize the operation of machines”, “diagnose the condition of each machine” and “predict abnormalities and failures in factories.” All of this helps improve productivity, reduces maintenance costs, eliminates downtime, and achieves energy savings for entire factories through energy monitoring and other measures.
PLCs as essential key components for constructing smart factories
So far, we have explained the concepts and benefits of smart factories.
Specifically speaking, how would someone start constructing a smart factory? First, you need to know what components make up a smart factory. The figure below shows the main components.
The key component in the figure is the “PLC” (programmable logic controller) edge controller, shown in red.
PLCs are important devices for controlling the operation of various machines.
However, in terms of their position in smart factories, However, in smart factories, PLCs are positioned as edge controllers to collect time-series data from machines and sensors (field devices) in the field.
The data temporarily stored in the PLCs is uploaded to the above-mentioned server system (CPS system) via the factory’s dedicated LAN and the Internet.
In the server system, the data is analyzed by AI and other technologies to create added value that is subsequently utilized in the field.
In other words, PLCs help to convey field device data to higher-level systems in order to visualize the data.
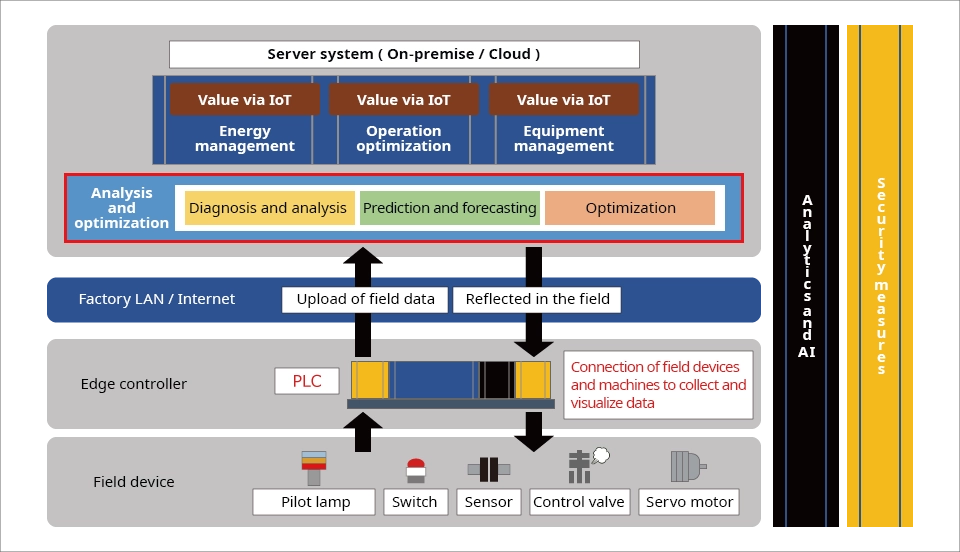
Some major electrical manufacturers have numerous technologies and components to convert their entire factories into a smart factories including manufacture of components such as PLCs.
They have taken measures to improve productivity and energy efficiency in their own factories and accumulated the knowledge and techniques for many years.
Now, many of them deploy such knowhow as solutions horizontally for other companies.
Latest IoT progress in smart factories! Specific success stories
Finally, we would like to introduce Fuji Electric’s success stories of constructing smart factories that utilize IoT.
At Fuji Electric’s Otawara Factory, which manufactures circuit breakers and earth leakage circuit breakers, a dashboard has been deployed that provides real-time visualization of quality, availability, energy, and other data.
The dashboard has enabled the factory to respond quickly to problems that arise in the field. This, in turn, has improved productivity at the factory. The dashboard streamlines and visualizes not only factory production line and production information, but also daily management information in order to achieve optimization for the entire factory.
Furthermore, at Fuji Electric’s Mie Factory, which integratively produces vending machines and other products, preventive maintenance is being implemented by monitoring for signs of abnormality in sheet-metal pressing processes in order to reduce quality defects.
Quality problems can occur if metal debris adheres to the punch when punching holes with a press. Therefore, the factory installed Fuji Electric’s “Diagnostic Sensor Hub” to collect data through the use of five sensors.
Signs of abnormality are detected by comparing the collected data with a normal model that was created from the correlation of various types of data.
This has enabled the factory to stop equipment before it malfunctions and perform maintenance to eliminate quality defects.
In addition to these examples, many other companies are continuing to pursue remote and unmanned operations as they prepare for the post COVID-19 world. Although it may be difficult to implement an advanced smart factory all at once from scratch, a good first step to making your factory smarter would be to deploy PLCs for the basic components of your factory, and then gradually expand from there.