AC Drives
Industrial Drives FRENIC-GS Series
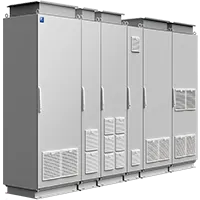
Bringing together Fuji Electric's industry leading technology and developed know how through numerous experiences.
Next-generation drives that deliver high precision and high functionality by combining superior control and monitoring performance
Features
Compact design
The PWM converter and inverter feature a slim stack structure suitable for panel mounting and replacement, while achieving a maximum capacity of 650 kVA. Up to 12 stacks of 25 kVA or less can be housed per panel, contributing to space savings in the electrical room.
Safety features
Comes standard with STO (Safe Torque Off) safety performance that meets safety certification levels SIL3 (EN 61800-5-2) and PL e (ISO/EN 13849-1) to contribute to improved safety in manufacturing facilities. Options cards can be installed to support SS1, SLS, and SBC.
Control performance
It has a speed response of 100 Hz, torque control accuracy of ±3% (when using a dedicated motor), and two types of observers, and contributes to improving product quality and productivity through its high-speed, high-precision control.
Monitoring function
Comes standard with Ethernet as the information LAN, and is also the first of its kind to support OPC UA. Contributes to stable production and promotes DX (Digital Transformation) of systems without degrading drive control performance by industry leading monitoring functions that separates the information LAN and control LAN.
FRENIC-GS configuration
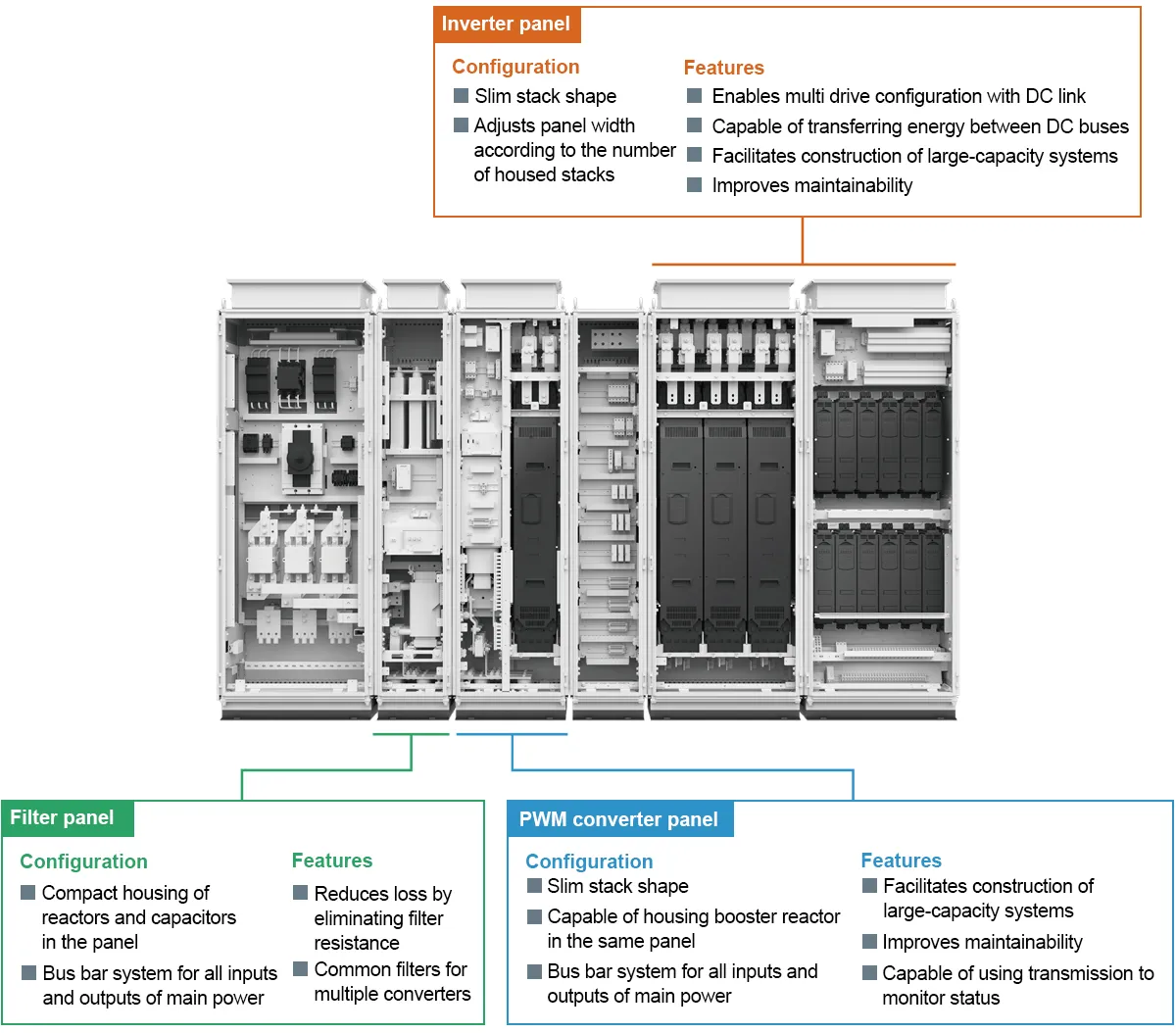
Main fields of application
Cranes
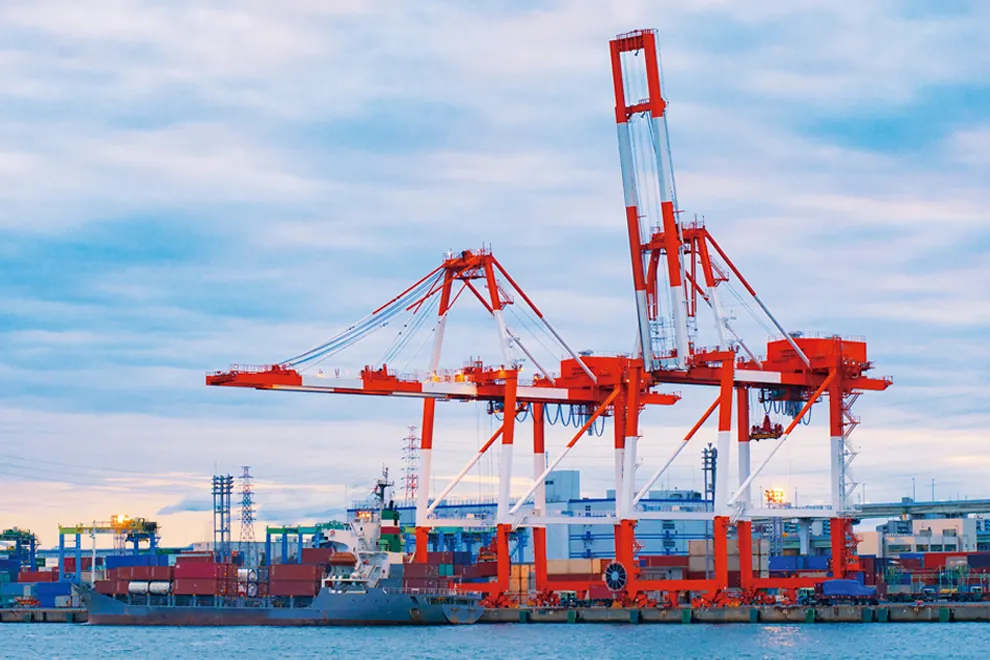
Slim stack shape enables downsizing of electrical rooms
By connecting multiple stacks in parallel, even if one stack fails, operation can continue with reduced capacity operation.
Cement
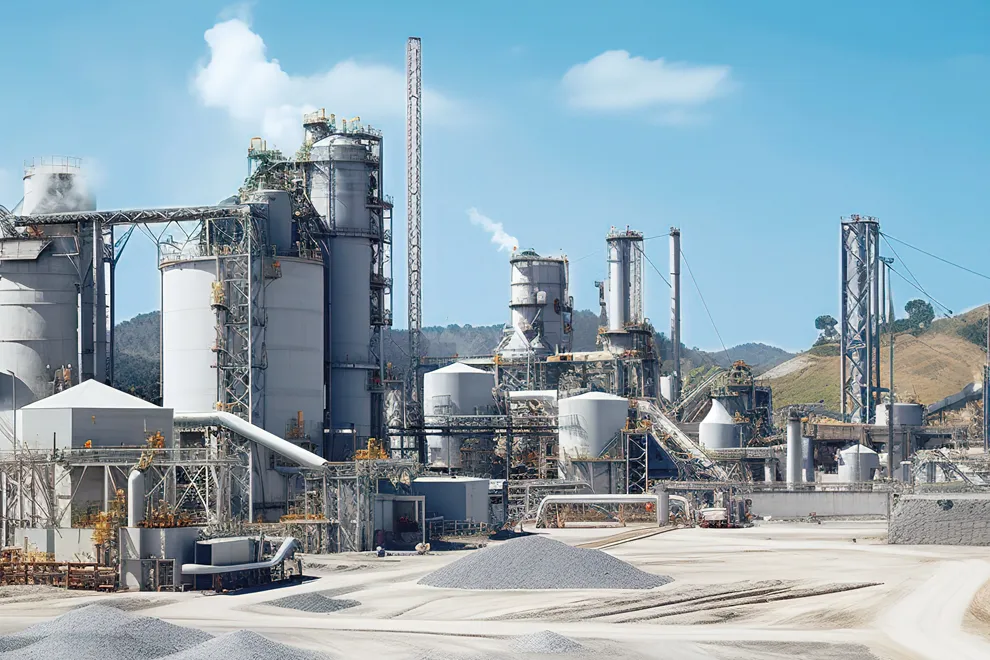
Achieves stable operation through high-speed control response even to high kiln starting torque and load fluctuations.
Highly accurate load sharing control for twin drive type kilns, overload calculations and overload alarms specific to kiln equipment are achieved by combining with a controller.
Press machines
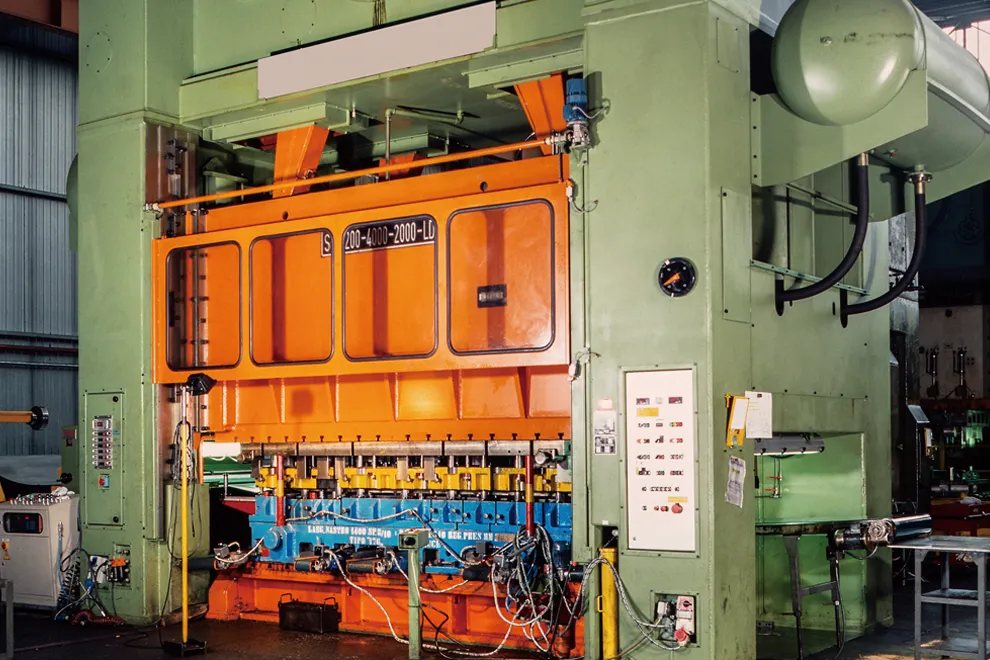
The press position is controlled based on the instantaneous position command given by the host CNC. High-response control contributes to shortened operation cycles
Larger machines are driven by multiple motors to increase thrust. Capable of precise synchronous control of multiple inverters/motors using a high-speed bus system
Papermaking
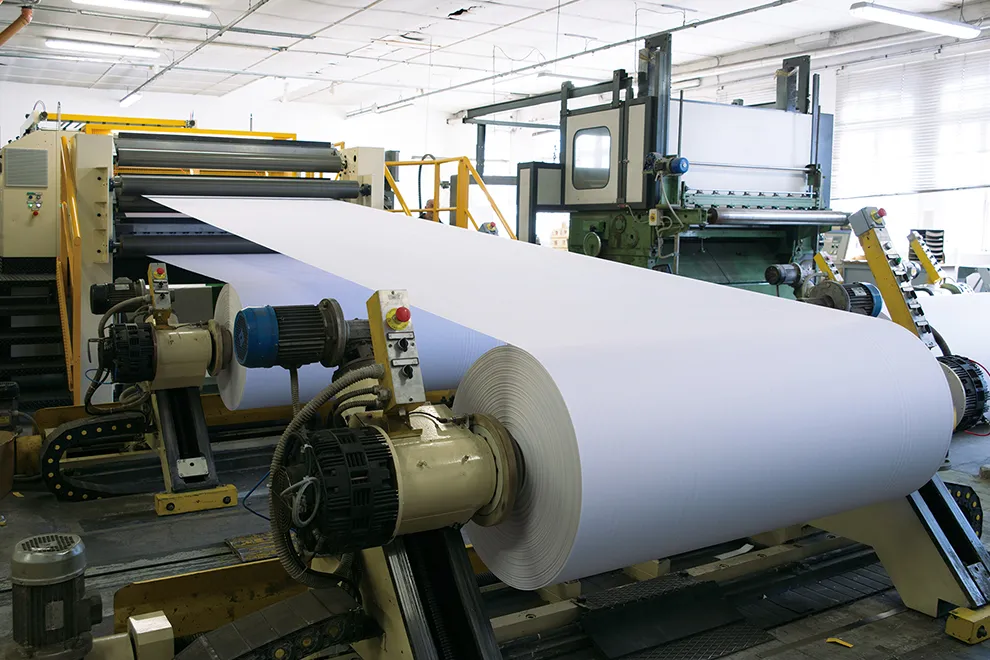
Improved tension-type winding control performance through high-precision torque control
Improved step-type winding control performance through high-speed response speed control
Achieves constant tension control using a controller that performs winding diameter calculations, etc.
Steel
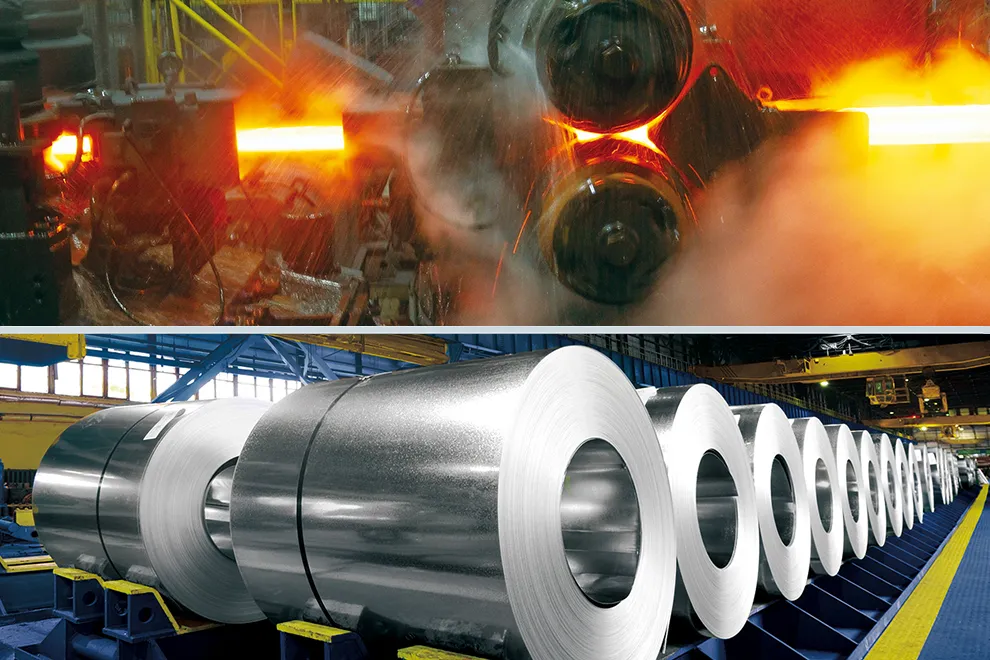
The DC distribution system enables energy transfer between driving and braking operations, and reduces the capacity of the common converter by taking into account the load factor of each motor.
Reduces the speed jump when material is removed, shortens recovery time, and shortens rolling pitch
Automotive testing machines
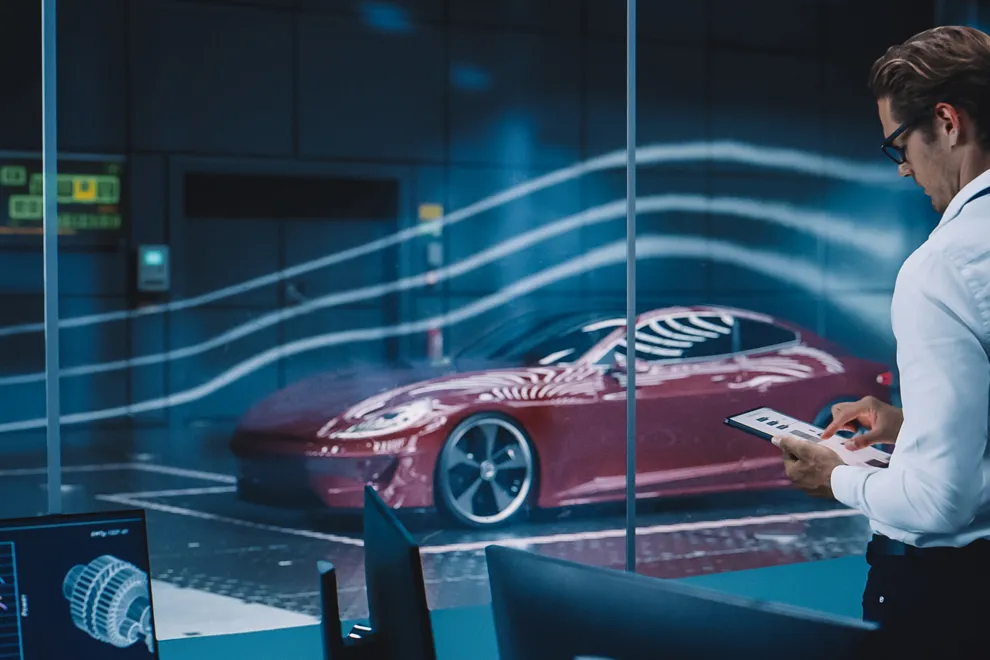
Supports high-speed rotation and high response torque control for engine and transmission tests
Capable of supporting systems in combination with controllers, such as functions that simulate vehicle body inertia for brake test equipment
Shiphandling winches
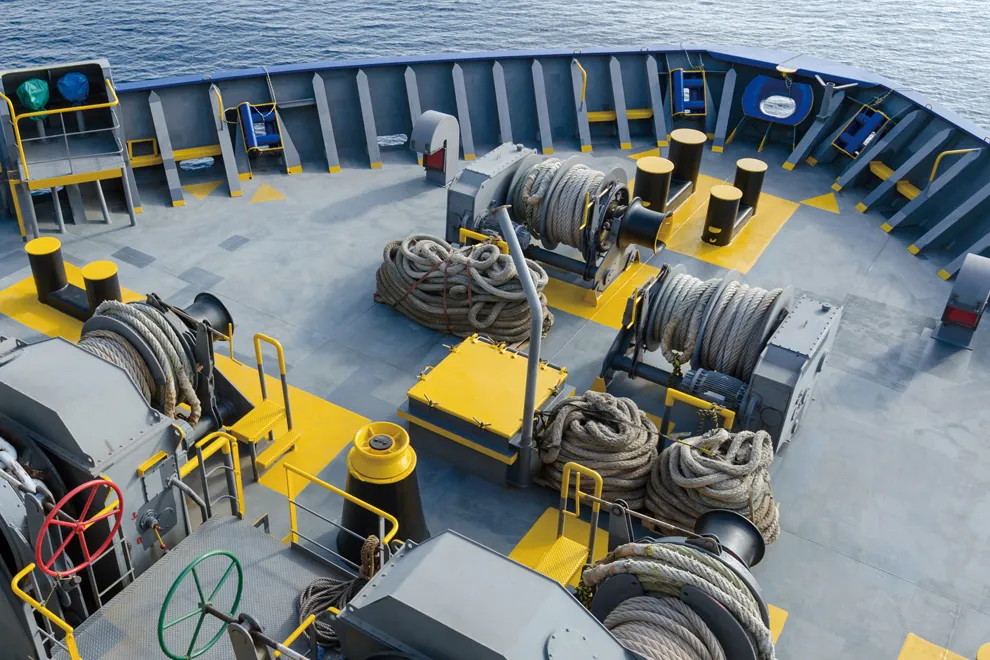
Sensorless torque control even at extremely low speeds. Achieves stable drive even in wave-induced load fluctuations
The DC distribution system enables energy transfer between driving and braking operations, and reduces the capacity of the common converter by taking into account the load factor of each motor.
Mining
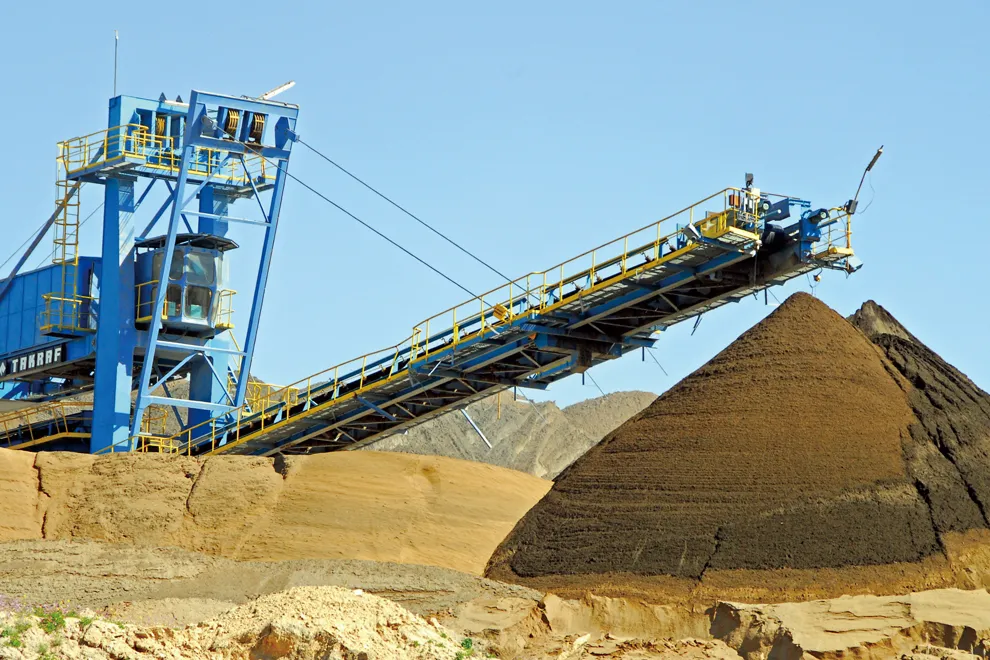
Separated control and information LANs enable remote monitoring of equipment distributed over long distances.
By connecting multiple stacks in parallel, even if one stack fails, operation can continue with reduced capacity operation.