FRENIC-MEGA (G2)
Product information
Supports vector control, sensorless vector control,
dynamic torque vector control, and V/f control.
Faster operating speeds
Increases the maximum output frequency of all control systems to 599 Hz and supports
applications that require high-speed rotation and minimal speed and torque fluctuations.
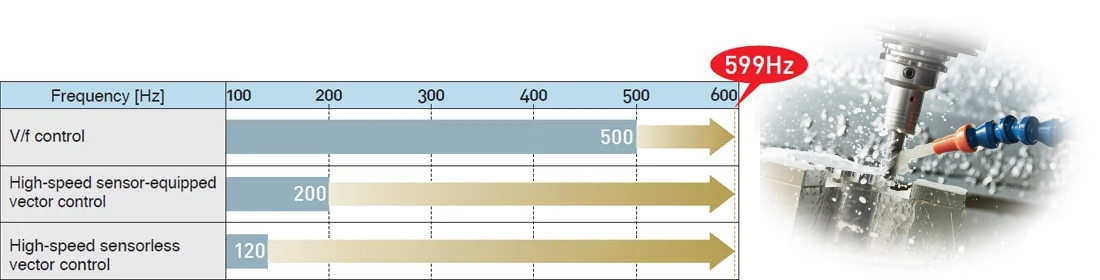
Example:Machine tools, compressors, automotive testing equipment, etc.
-
Note)
-
Due to revised export control regulations (for frequency converters), the inverter will trip when the output frequency exceeds the upper limit of 599 Hz.
Enhanced response
Improves speed and current responsiveness and stabilizes product quality by substantially reducing torque ripple and rotation irregularities.
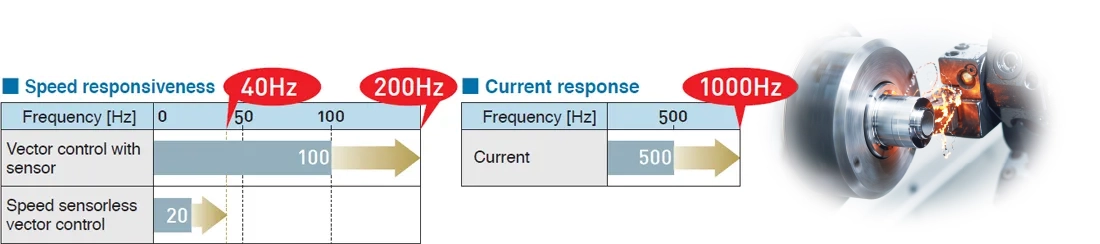
Example:Wire drawing machines, metal processing machines, printing machines, etc.
Enhanced torque
Stabilizes torque at low speeds and increases the accuracy of machine operations through its improved speed control range.
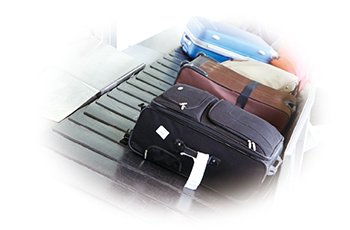
Example:Conveyance machinery, press machines, etc.
Advanced dynamic torque vector control
Enhances our proprietary dynamic torque vector control with new motor constant tuning (that takes into account the voltage of the main circuit) and newly designed magnetic flux observer.
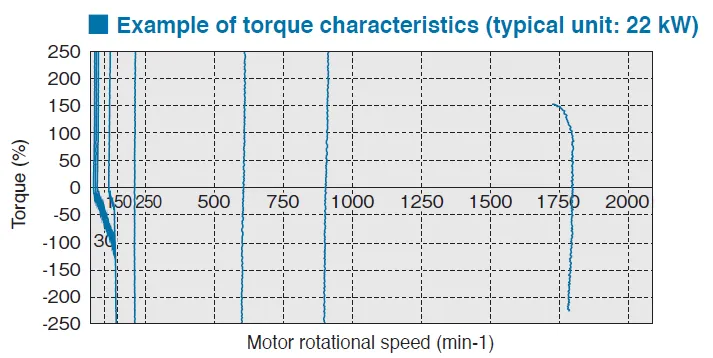
Strengthens ability to handle impact loads
Achieves its class's highest level of torque responsiveness to sudden load changes.
Minimizes fluctuations in motor rotational speed and suppresses vibration via magnetic flux control.
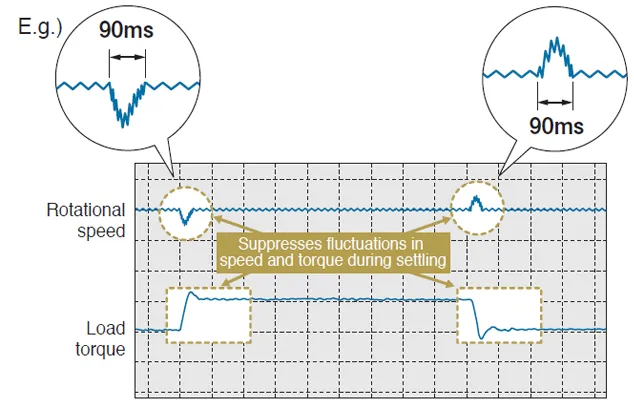
Can be used with any motor
Comes with new auto-tuning features that enable multi-drive operation using our induction and synchronous motors as well as those of other companies.
-
Note)
-
The G2 Series can replace conventional FRENIC-MEGA(GX1S) Series products (synchronous motor drive types only).
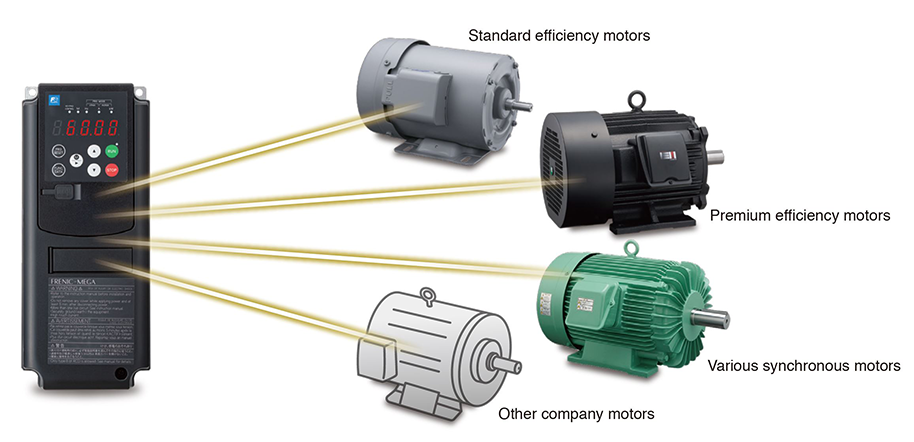
Expansion of standard applied motor capacity for the HND specification
We expanded the rated current and standard applied motor capacity (HND specification) for general loads, making it an easy replacement for our FRENIC-Eco Series (for fans and pumps).
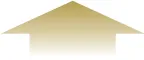
Expands the capacity of the built-in braking transistor type
Comes standard with a larger capacity range and contributes to control panel space and cost savings.
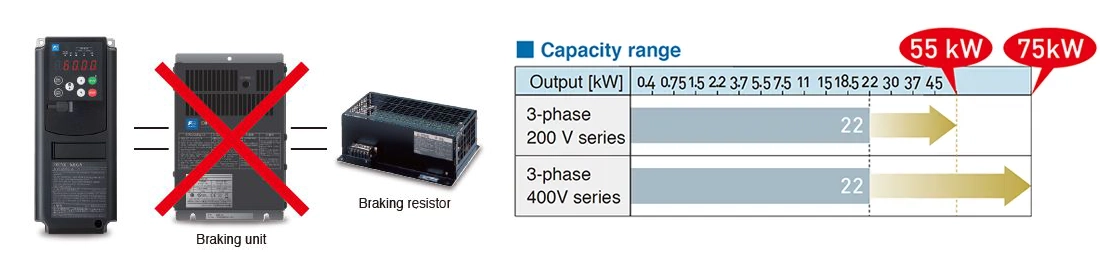
Comes with feature-rich functionality and enhances compatibility with system networks.
Positioning
Contributes to shortening machine tact time through high-precision positioning control for pulse string input and feedback output instructions.
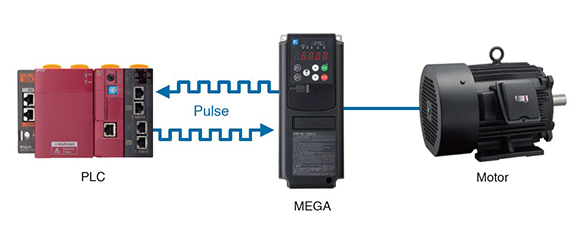
Orientation
Capable of rotator positioning, enabling machinery to be held in place via servo locking after stoppage.
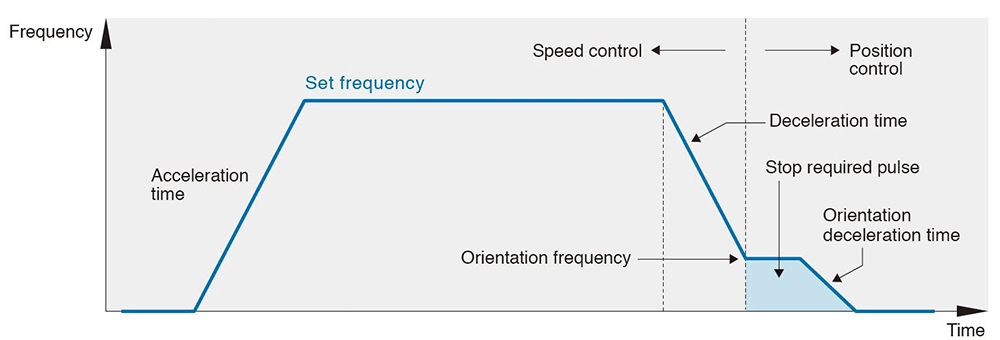
PID auto tuning
Simplifies optimization via automatic adjustment of proportional and integral gains, resulting in shorter system start-up times.
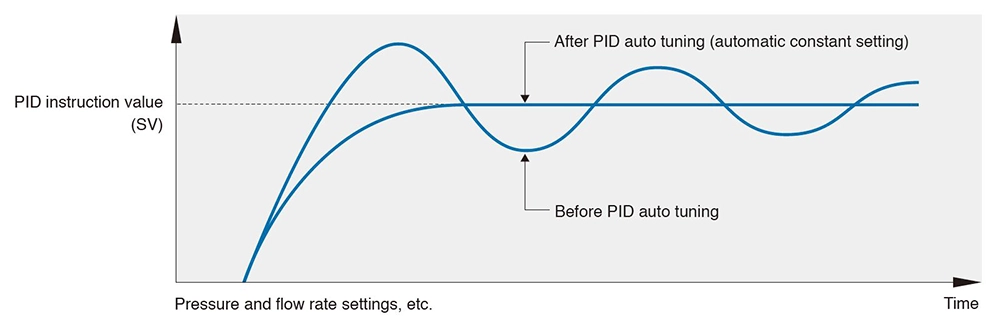
Load limiter
Improves system reliability by stopping when excessivetorque is detected and by allowing operation only in thedirection opposite to that in which the excessive loadwas detected.
Load adaptive control
When the actual load level is lower than the configuredload level, the system can be operated at a ratio-multipliedfrequency, resulting in significantly better efficiency.
Customizable logic functions
Customizable inverter functions to meet your own specific needs.
Requires no PLC or external control equipment (relays, timers, etc.) circuits, and can be configured simply by setting and combining various parameters inside the inverter.
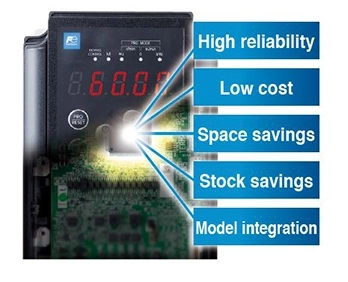
-
Note)
-
The programming tool software can be downloaded for free from our website.
PID Control (with 4 PIDs)
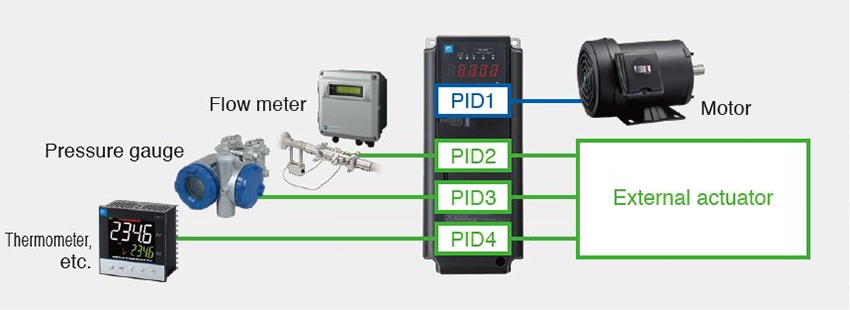
Allows switching between two types of process commands and feedback values. PID control function that is easy to adjust using an anti-reset windup function to prevent overshoot of PID control and PID output limiter and integral hold/reset signal.
In addition, up to three external actuators can be controlled simultaneously with motor PID control, eliminating the need for a PLC and contributing to system cost reductions.
Linearize
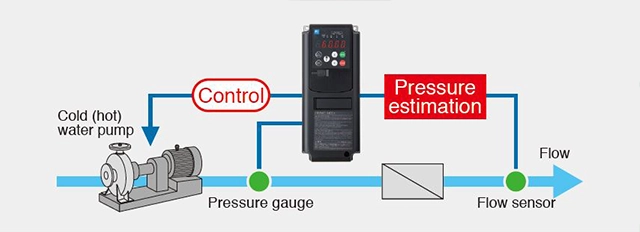
By controlling the pumping pressure at an appropriate value based on the flow rate and target end pressure, it maintains the discharge pressure and reduces wasteful power consumption, contributing to energy-saving effects.
Cascade operation
Function to control multiple pumps with one inverter. Control by combining inverter-driven and commercial power-driven operation. The flow and pressure sensor signals are controlled by the PID controller built-in the inverter, and each pump is driven by commercial power or the inverter using switching signals from the inverter.
As a result, when the discharge flow rate is low, only inverter-driven operation is used, and when the discharge flow rate is high, commercial power-driven operation is used in addition to inverter-driven operation to ensure the necessary total discharge flow rate.


It consists of a combination of a inverter-driven motor (M0), commercial power-driven motors (M1 to M8), and an auxiliary motor (MA). The inverter-driven motor is fixed to motor M0. When the desired discharge flow rate is not achieved with only motor M0, control is performed by sequentially adding commercial power-driven motors.

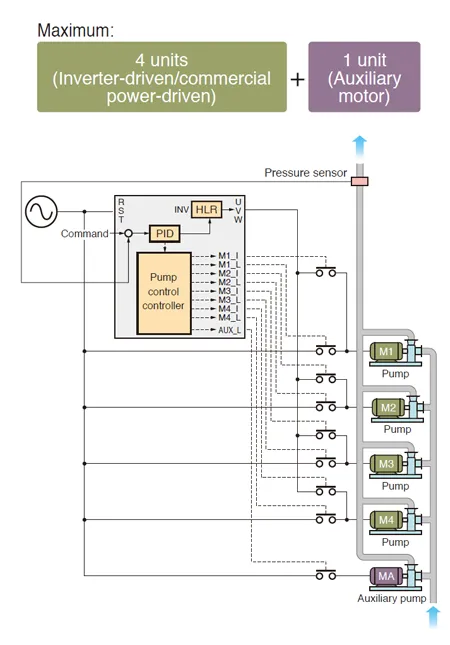
It consists of a combination of motors(M1 to M4) that can switch betweeninverter-driven and commercialpower-driven operation, and anauxiliary motor (MA) that is driven bycommercial power. Variable speedcontrol using inverter-driven operationat startup. If the desired discharge flowrate is not achieved with only the firstmotor, the operation of FLOATING-1 orFLOATING-2 can be selected.

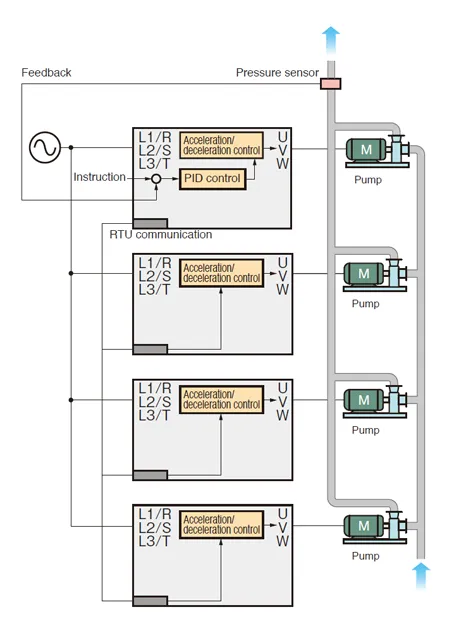
Each inverter is connected via acommunication link, eliminating theneed for a controller when buildingsystems. In addition, the communicationlink reduces wiring withoutrequiring any additional options.
Constant control of temperature and pressure differences
Reduces wasteful power consumption bylowering fan output when it is difficult to lowerinternal temperatures due to environmentalfactors such as the outdoor air temperaturebeing higher than that of the cooling water.
Temperature can be detected directly with theresistance temperature sensor by using anOPC-PT option card.
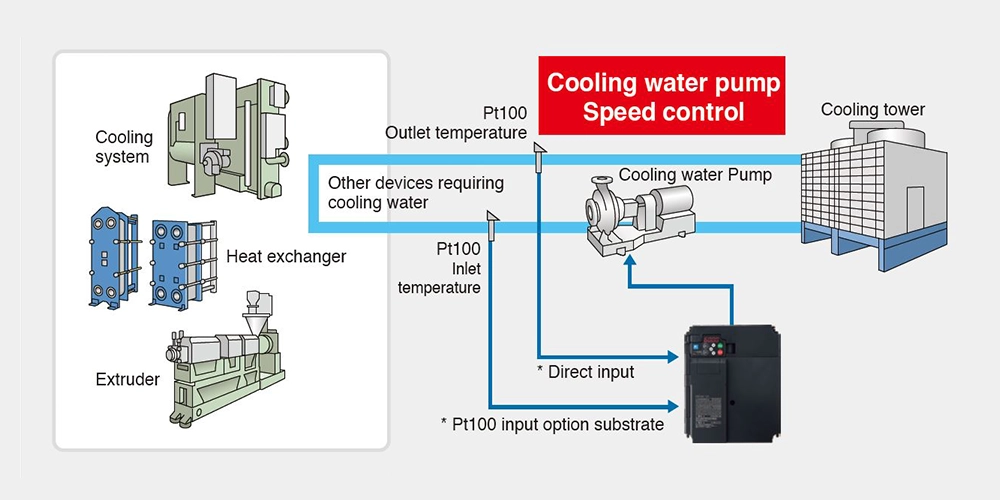
-
Note)
-
The resistance temperature sensor needs to be purchased separately
Prevention of filter clogging
It detects filter clogging due to dust, etc., based on output current and pressure sensor values, and removes the dust through reverse rotation.
In addition, an alarm is used to indicate that maintenance is required.
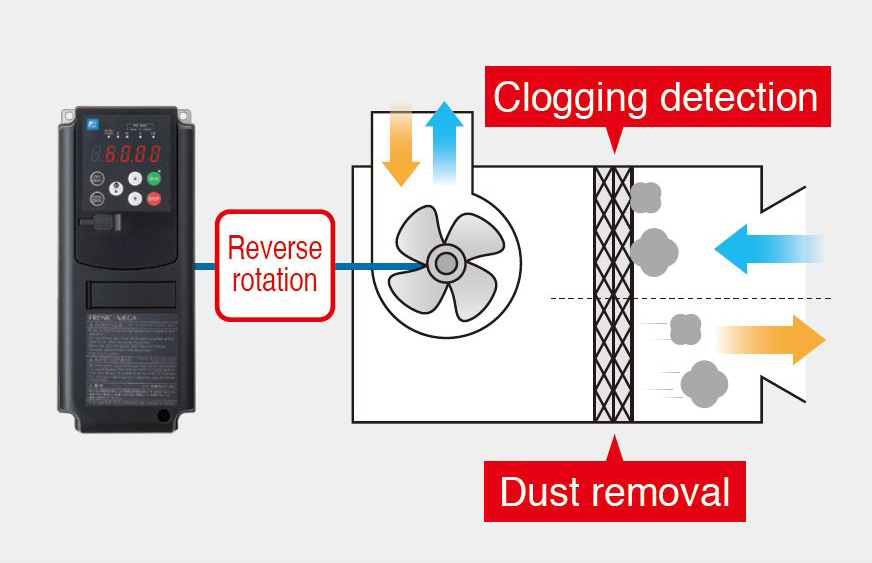
Fire Mode
In the event of a fire or other emergency, the inverter's protective function (output shutoff) is partially ignoredand operation is continued. This prevents the buildingfrom being filled with smoke and secures an evacuationpassage.
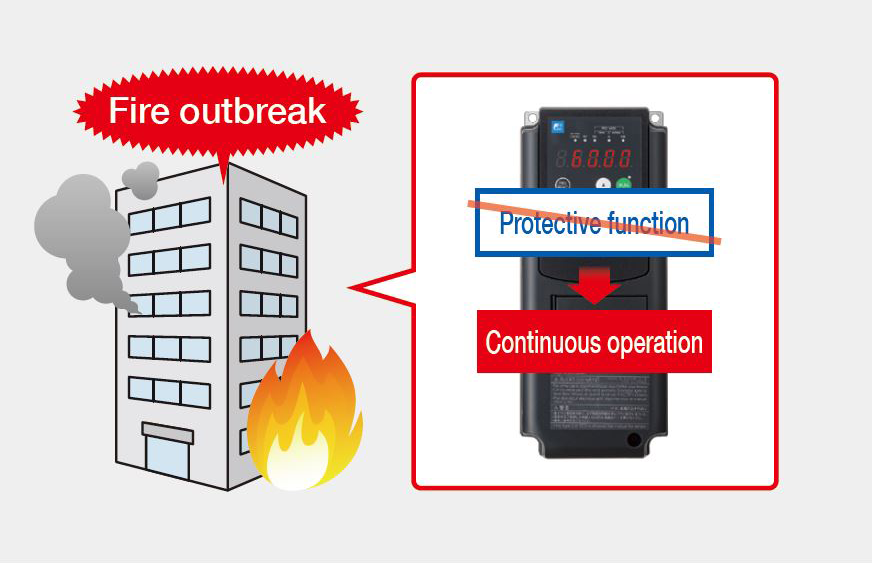
Supports a variety of networks
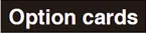
-
Note)
-
For other types of option cards, please refer to page 69.
Enhanced network functions
Comes standard with an RS-485 terminal in addition to a port (RJ-45 connector) that is shared with the keypad.
Simplifies multi-drop connections via terminal connection.
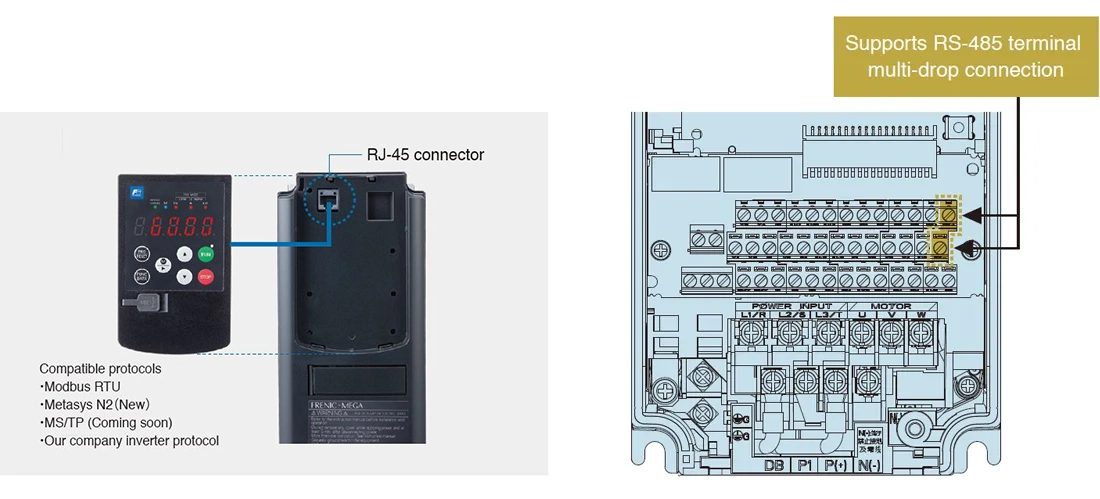
Enhances work efficiency through simplified wiring and configuration and ensures safety and security through standard features such as preventive and predictive maintenance functions.
Same mounting dimensions
The appearance and mounting dimensions of the inverter are fully compatible.
The 3D position and size of the main circuit screw terminals are also the same.
-
Note)
-
Can be installed as a replacement for conventional FRENIC-MEGA(G1) Series products.
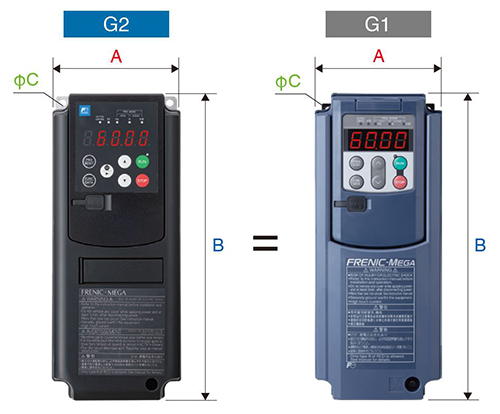
Simple wiring
Supports replacement or mounting of conventional
FRENIC-MEGA(G1) Series' round terminal blocks(35-pole ⊕ screw).
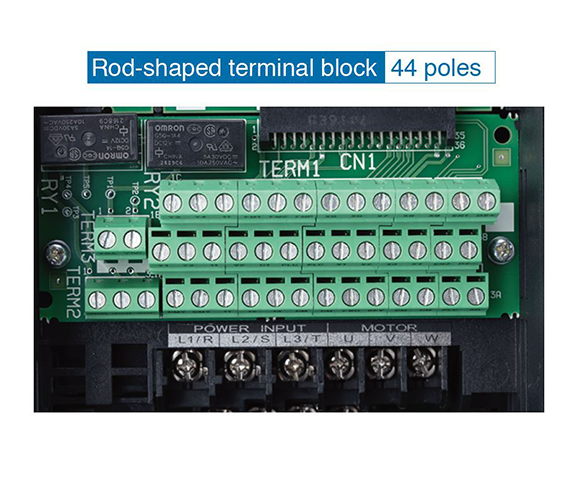
Easy parameter migration
Compatibility mode allows parameters read from the previous model to be written directly to the G2 Series.
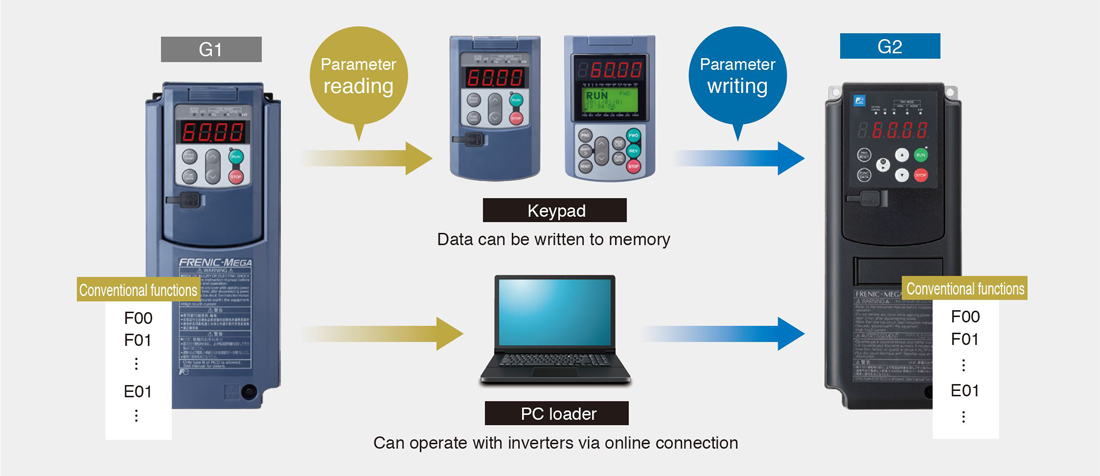
-
Note)
-
The previous models include FRENIC-MEGA(G1) and FRENIC-MEGA(GX1) FRENIC-Eco series products.
-
Note)
-
Data can be read from a keypad (TP-E1U/TP-G1-J1) or PC loader from a conventional FRENIC-MEGA(G1) Series product and copied to the G2 Series.
Please be assured that the function codes newly added in the G2 Series will not be changed.
Designed with new operation keypad
Comes standard with a 7-segment 5-display whose large screen is very intuitive and enhances maintainability via improved key button operability and cursor digit control.
Standard
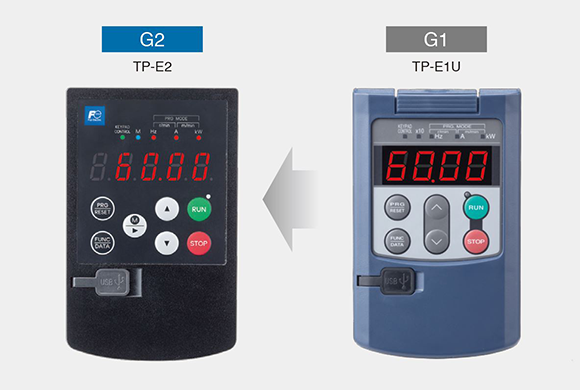
Additional features
Character display
-
7-segment, 5-digit LED display.
“M/Shift” key
-
The cursor can be moved to any position.
-
Can assign the same signals as the digital input terminal (X terminal).
-
Can fix the assigned signal to ON by pressing and holding the key.
“M” LED display
-
Can use LEDs to monitor the digital output signals of inverters.
-
Y-terminal signals can be assigned to enable checking without using a conventional PC loder or keypad.
Multi-function Option
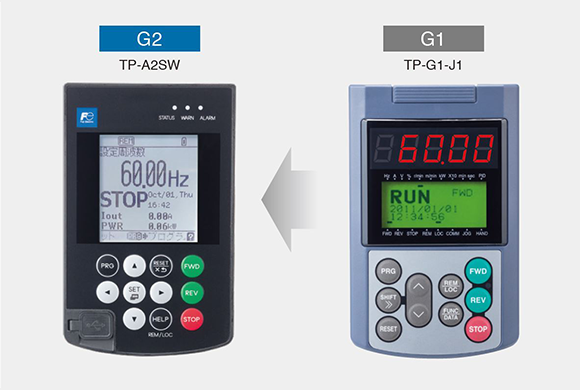
Additional features
Character display
-
Equipped with a highly visible LCD.
-
Supports a total of 20 languages, including Japanese hiragana, katakana and kanji.
-
Note)
-
Compatible with the software version, main product ROM0500 or later and the multifunctional keypad ROM5020 or later.
USB port
-
Mounts to both standard keypad and multifunctional keypad.
-
Can be directly connected to a PC with a commercially available USB cable (mini B).
Clock function
-
Time data can be added to the alarm history.
-
Note)
-
Battery (CR2032 type) not included
SD card slot
-
Can store traceback data on micro SD card.
-
Note)
-
SD card not included.
Water resistant
-
The front surface and sides are IP55 protected.
-
Note)
-
The back side is IP20 protected.
Built-in Bluetooth
-
Parameter changes and maintenance can be performed remotely using a mobile device.
-
Note)
-
Radio law certified countries: Japan, Europe, North America, China, Thailand
Enhancement of alarm history/traceback function
-
Capable of displaying and saving the last 10 alarm codes and the last 4 detailed information, including output voltage and output frequency.
-
Note)
-
Adding HVAC functions will enable this function.
-
Note)
-
When using the multifunctional keypad, you can also obtain data on the time of occurrence.
However, batteries are required.
-
When an alarm occurs, previous waveform data can be acquired and saved.
-
Note)
-
The above is the number of saved tracebacks.
Enhanced PC loader functions
-
The PC loader can be used by directly connecting the keypad to a PC using a commercially available USB cable(mini B).
-
It makes it easy to store or check various types of information at the office, or send information and check abnormalities at
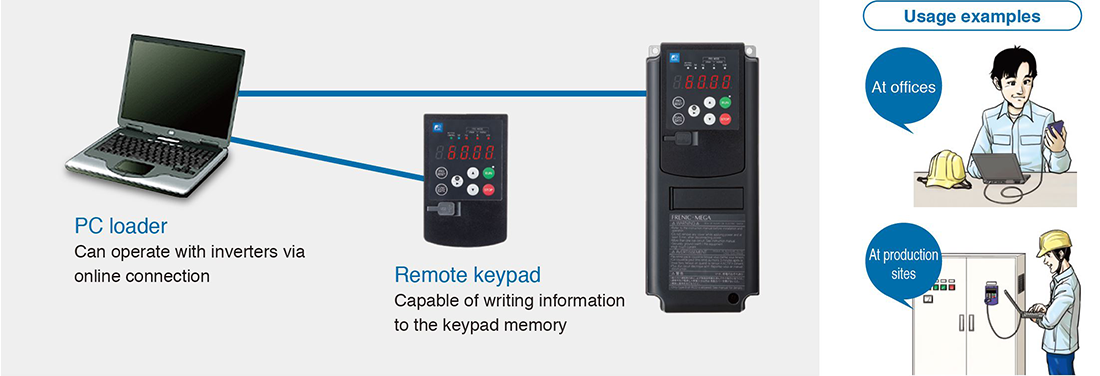
Life expectancy diagnosis and maintenance functions
The keypad and PC loader make it easy to check the status of equipment and detect problems before they occur, helping to reduce production equipment maintenance time and downtime.
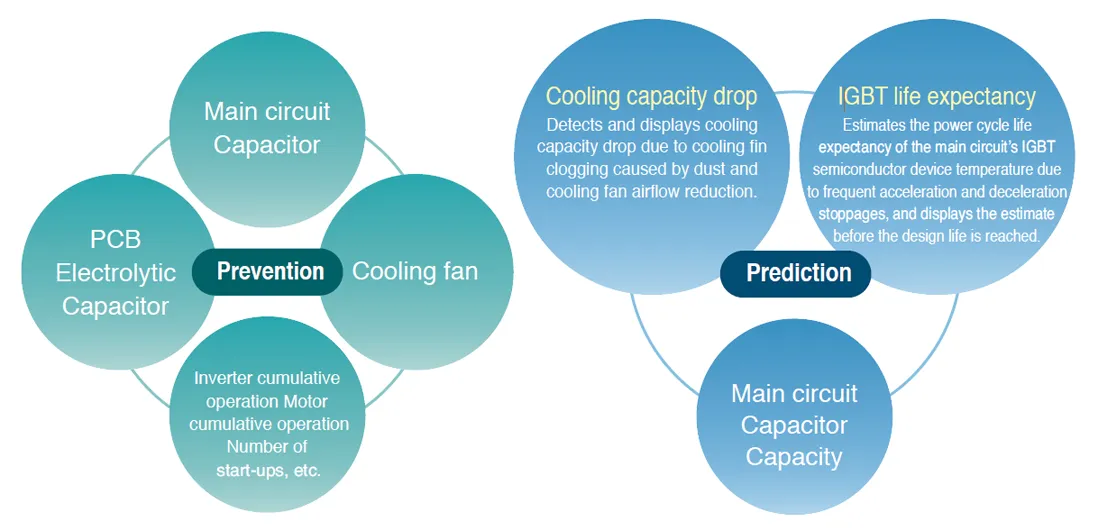
Long life expectancy (main components)
Many of the serviceable parts inside the inverter have been designed to meet
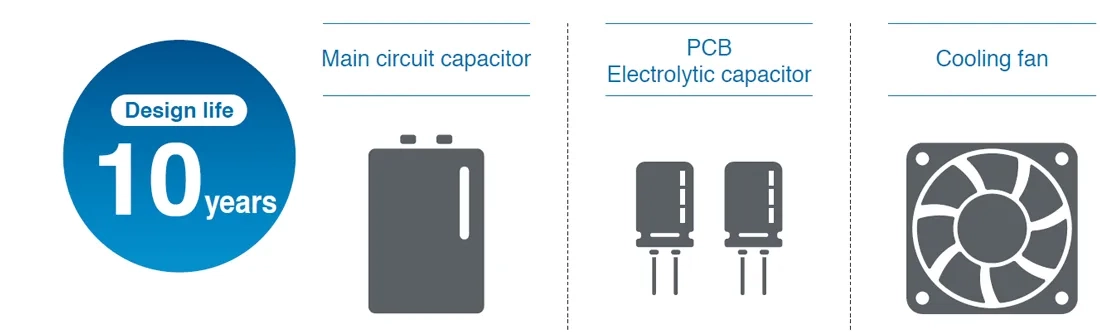
-
Note)
-
The above values refer to the design life (calculated values) and are not guaranteed values.
Globally compliant lineup compatible with adverse atmospheres and various safety standards.
Improves environmental resistance
Note) Derating is required when used at 50℃ or higher. (JIS C 60721-3-3 Class 3C2) Note) If you are using or considering using the product under the following conditions, please contact our sales department.
(2) Ambient operating temperature up to +55℃
Note) Products also available with enhanced salt-resistance and made-to-order specifications.
(4) IP55 protection for the inverter's main cooling unit contributes to enhanced cooling outside the panel, lower costs, and downsizing.
a. Environments containing sulfurized gas (e.g., some applications in the tire manufacturing, paper manufacturing, sewage treatment, textile industries, etc.)
b. Environments containing conductive dust and foreign objects(e.g., metal processing machines, extruders, printing machines, waste disposal machinery, etc.)
c. When using the product in non-standard environments
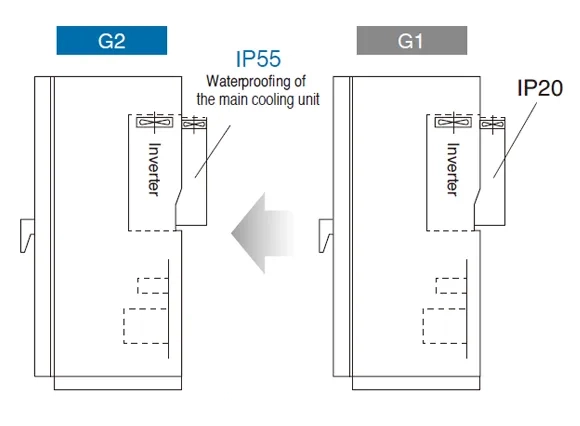
-
Note)
-
Supports only 30 kW to 630 kW
Includes safety functions
・Compliant with European safety standards. Note) The zero-phase reactor built-in type does not comply with the EC Directive (CE marking). ・The inverter comes with a function that enables it to adapt to machine safety. This provides safe shutdown without the need for an external output circuit breaker.
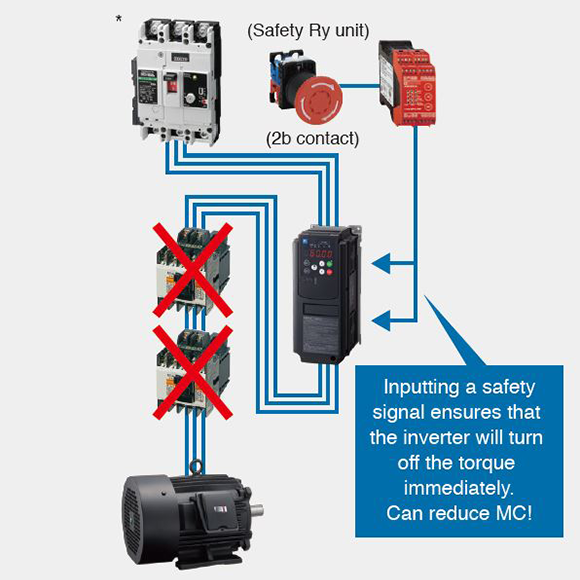
-
Note)
-
Always turn off the breaker when touching the electrical circuit during maintenance.
Compliant with the revised European RoHS Directive
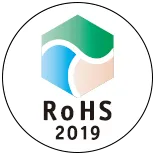
Lead, mercury, cadmium, and hexavalent chromium
Polybrominated biphenyl (PBB)
Polybrominated diphenyl ether (PBDE)
Di-2-ethylhexyl phthalate (DEHP)
Butyl benzyl phthalate (BBP)
Di-n-butyl phthalate (DBP)
Diisobutyl phthalate (DIBP)
Globally compliant
Compliant with overseas safety standards.
-
Note)
-
The zero-phase reactor built-in type does not comply with the EC Directive (CE marking).