Sustainability
Efficient Use of Water Resources | Our Contribution Activities to SDGs
Semiconductor manufacturing process / efficient water use project Contributing to the realization of a recycling-oriented society through the efficient use of water resources
Published in October 2023. Affiliations and responsibilities are as of the time of the interview.
Aiming to achieve a recycle-oriented society, Fuji Electric promotes 3R (Reduce, Reuse, Recycle) activities in the entire supply chain. One of our initiatives toward this goal is making efficient use of water resources while complying with wastewater requirements. Specifically, we have been working toward the efficient use of water resources at the Matsumoto Factory and the Yamanashi Factory, which are power semiconductor manufacturing bases, for many years. In this article, we will take a closer look at the efficient use of water resources at these two factories that implement one of Fuji Electric’s key SDG targets, “12. Responsible Consumption and Production.”
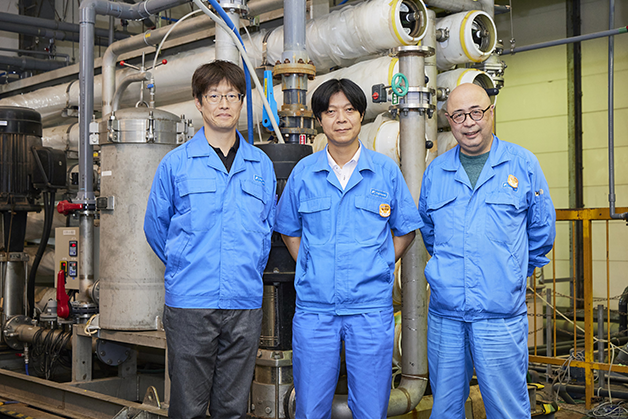
The efficient use of water resources is Fuji Electric’s mission.
Fuji Electric’s semiconductor business is centered around manufacturing power semiconductors, a key component for energy-saving. This product plays a key role in achieving a decarbonized society, as it is used in electric vehicles, railroads, solar and wind power generation systems, etc.
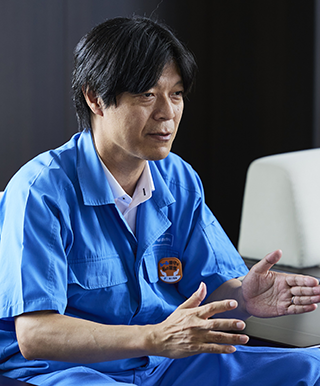
In the manufacturing process, the Matsumoto Factory and the Yamanashi Factory carry out the preprocess of power semiconductor manufacturing. They form an electrical circuit in a thin sheet (silicon wafer) and cut them into chips. Water is an indispensable resource in this important process that determines the performance of power semiconductors. In the semiconductor manufacturing process, processes like film forming, coating, and etching are repeated multiple times, and each time, they require a large amount of ultrapure water for cleaning. In addition, a lot of water is required for the cooling water in production facilities, the air conditioners that maintain the specific temperature and humidity required in the cleanroom, the decomposition or removal of chlorofluorocarbons, which have a greenhouse effect, and other processes. Hidenori Takahashi, Senior Manager, Wafer Production Department, Matsumoto Factory, explains the reason behind their efforts toward the efficient use of water resources as follows.
“Water is indispensable for manufacturing semiconductors. We take its effect on the local environment into full consideration. We also minimize the costs associated with wastewater as much as possible. Efficiently using this valuable resource as much as possible is our mission as we continue operating in this area. The Matsumoto Factory and the Yamanashi Factory take their surrounding environment into consideration and accordingly make efforts to recycle water instead of discarding it.”
Improvements added up to yield concrete results.
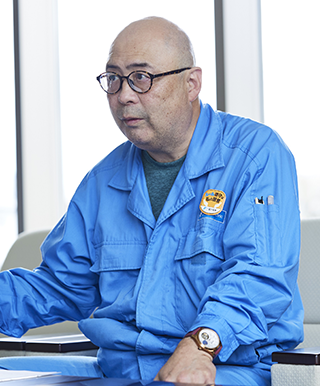
Matsumoto Basin is fortunate to have an abundance of underground water that provides a water supply to every household and to local industries. That said, knowing the amount of resources and saving water is important to preserve the water resources in the entire area. The Matsumoto Factory has been working on separating and recycling reusable water from the wastewater produced by the production facilities for a long time. The turning point was in 2005. Integrated Water Management (IWM) facilities were implemented to further increase the amount of recycled water. The factory had decided to work on recycling wastewater, which is conventionally known to be difficult to recycle. Yoshitomo Ogimura, who is responsible for facility maintenance at the Matsumoto Factory, explains the advantages of doing this as follows.
“The wastewater produced by the semiconductor factory is first treated to get rid of toxic substances, such as hydrofluoric acid and heavy metals. After that, it is neutralized in the sewerage treatment plant inside the Matsumoto Factory, then drained into the public sewerage system. IWM facilities reuse the water after it’s neutralized, right before it’s drained into the public sewerage system. Not only does this reduce the amount of wastewater and cut down on the costs of wastewater, but it also limits underground water withdrawal, contributing to the preservation of underground water resources.”
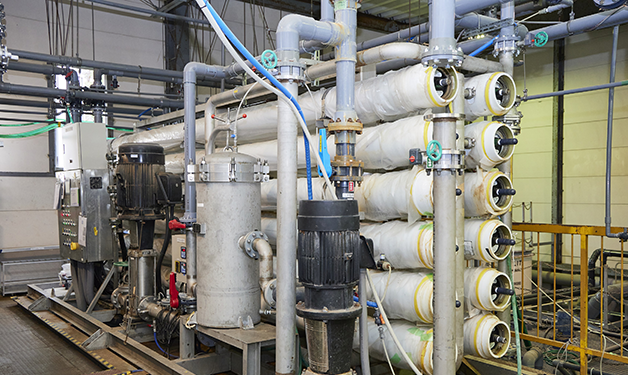
However, just implementing the facilities doesn’t solve all the problems. The trial and error of the past facility managers is what made it possible to reuse the water resources that had not been reusable before then.
“They identified the influx route of phosphoric acid, which caused an increase in the concentration of hydrofluoric acid and promoted the growth of bacteria that blocked the filtration membrane in the membrane filtration process, and regularly monitored the concentration to prevent the influx. They were also able to prolong the life of the filtration membrane by eliminating more bacteria and regularly changing the cleaning method of the filtration membrane. In addition, they cut down on the maintenance costs of the expensive reverse osmosis membranes by soaking them in regular membrane cleaning chemicals before reusing them. These various improvements added up, enabling them to transform the IWM facilities into a sustainable operation that recycles more than 20% of the wastewater that is produced in the process. This was the fruit of 20 long years of gathering data and repeating trial and error. We hope to savor this joy with the past managers.” (Ogimura)
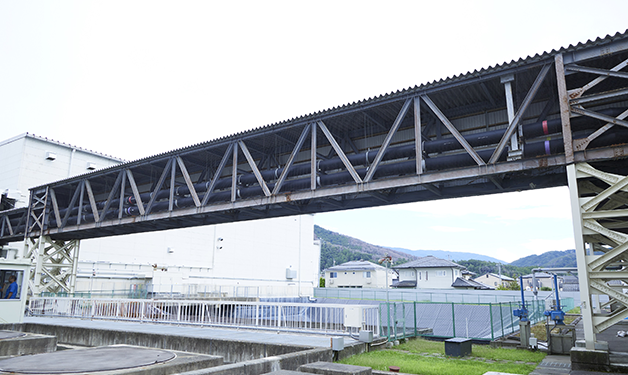
Creating the desired equipment without halting manufacturing.
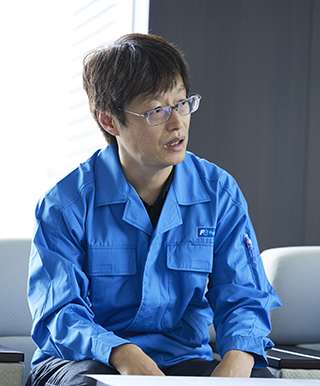
As for the Yamanashi Factory, only a small amount of underground water can be used by businesses on the basin hill where it’s situated, accounting for only about 20% of the water used in the factory. The factory must rely on municipal water supplied by the public water supply for most of the water it uses. Ryoichi Ichikawa, Wafer Production Department, Yamanashi Factory, explains the water recycling initiatives at the Yamanashi Factory as follows.
“There is a limit to the supply of municipal water, and increasing the amount of wastewater recovered is directly linked to the reduction of water charges. It is safe to say that recovering and reusing wastewater are essential efforts for continuing to manufacture semiconductors at the Yamanashi Factory. In the past, we used to recover acidic wastewater, such as waste rinse water produced by the cleaning process, and low-concentration chemical wastewater, because they were relatively easy to recycle. However, this time, we started working on recovering the grinding process wastewater to further increase the amount we recover.”
When implementing and setting up the equipment for recovering and recycling the grinding process wastewater, they focused on establishing an automated system that doesn’t increase the number of operations required on-site and doesn’t affect the existing manufacturing process. They were looking to automatically recycle water resources without involving manual work. They also wanted to create a control system suitable for the existing wastewater treatment equipment and the new grinding process wastewater recovery equipment that would be established. Above all, they needed to set up this large system without halting the manufacturing of semiconductors. It looks like they made an enormous effort to achieve all these conditions.
“The Yamanashi Factory halts the manufacturing of semiconductors only a few days a year. In order not to affect operations, it was our mission as equipment professionals to create something that functioned properly. We repeatedly held extensive meetings, carried out adjustments, and conducted test runs for inspections during operations. I still can’t forget the relief I felt when we were able to recover the desired amount of water and succeeded in operating the equipment. We were able to contribute to manufacturing semiconductors while making efficient use of water resources. All members certainly seemed proud.” (Ichikawa)
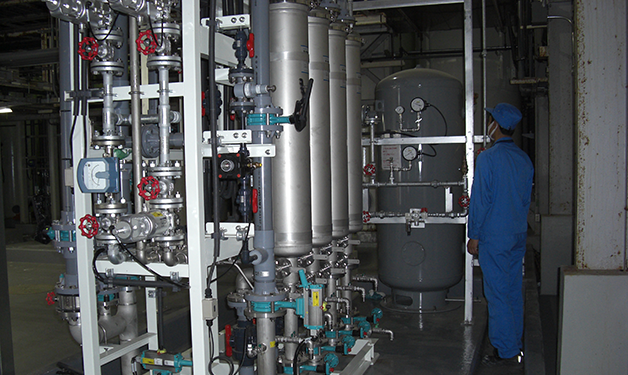
Manufacturing eco-design products using a process that takes the recycling-oriented society into consideration.
Thanks to the members’ hard work, the series of projects was a huge success. They were able to recycle a quarter of the water resources required for manufacturing semiconductors at Fuji Electric. The power semiconductor produced in the course of these projects will not only contribute to decarbonization as an eco-design product but will also continue to be produced using a manufacturing process that takes the recycling-oriented society into consideration. The members are looking to tackle more challenges for various causes, such as continuing to meet society’s expectations and maintaining a sustainable local environment.
“Power semiconductors are in increasing demand as a key component for energy-saving, and their production is currently increasing to help achieve a decarbonized society. Meeting this demand will certainly lead to a further increase in water demand. This will require more innovation with water supply and waste. Making efforts toward the efficient use of water resources is our most important task to keep up the manufacturing capacity required by society while taking the local environment into consideration. We will work on this task together as a team with a stronger will than ever.” (Takahashi)
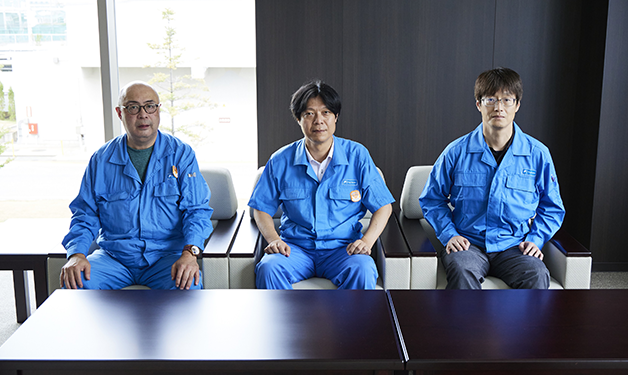
The trend of Fuji Electric’s water recycling amount (Japan)
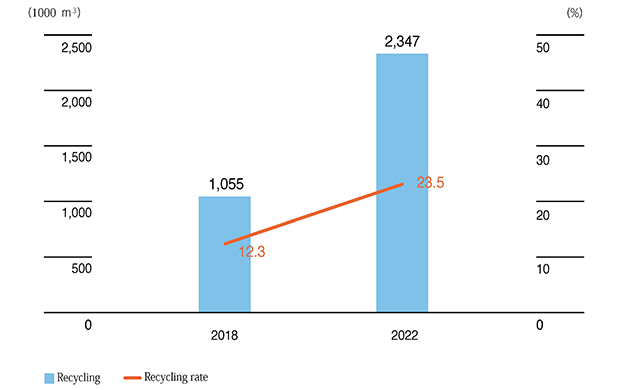
Contribution to SDGs
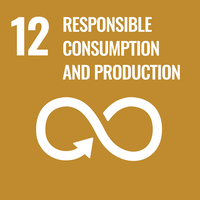
Fuji Electric considers the SDG target, “12. Responsible Consumption and Production” one of its key targets, and aims to achieve a recycling-oriented society according to the Environmental Vision 2050. The company promotes activities aimed at implementing the 3Rs (Reduce, Reuse, Recycle) in the entire supply chain. As part of these activities, it is making efforts toward the efficient use of water resources while complying with wastewater requirements.