Combat Power Outages! The Distribution Automation System Maintaining Okinawa’s Supply of Electricity
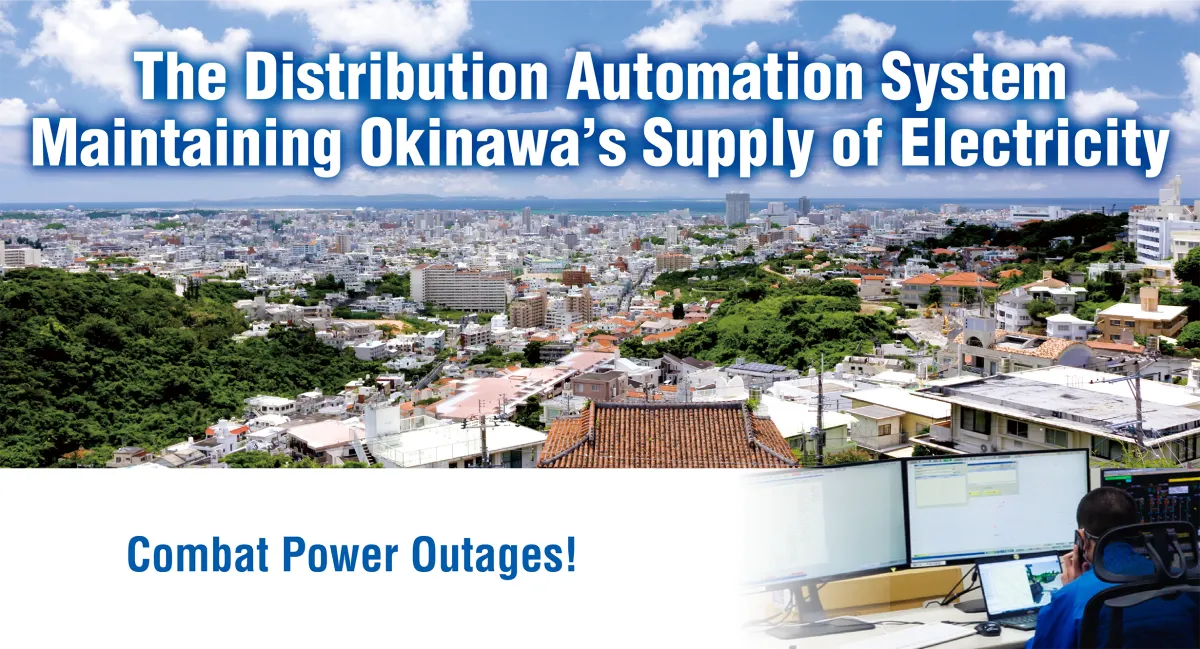
As we surround ourselves with smartphones, home appliances, and other electronics, our lifestyles are not possible without electricity. When a blackout occurs, everyone wants the power to come back on as soon as possible.
Japan is highly susceptible to natural disasters. Once disaster strikes, damaging power lines and utility poles, power outages are inevitable. To address this issue, distribution automation systems have been deployed almost everywhere in the country. They are designed to automatically manage the flow of electricity during emergencies, thereby minimizing the affected area and reducing the duration of outages.
Fuji Electric has built such a system in Okinawa, where the risk of power outages is the highest in the country due to typhoons. What issues faced by society do Fuji Electric's systems address? What benefits do they bring?
Related Content(Customer Interview)
Minimizing the Area and Duration of Power Outages Without Visiting the Affected Area
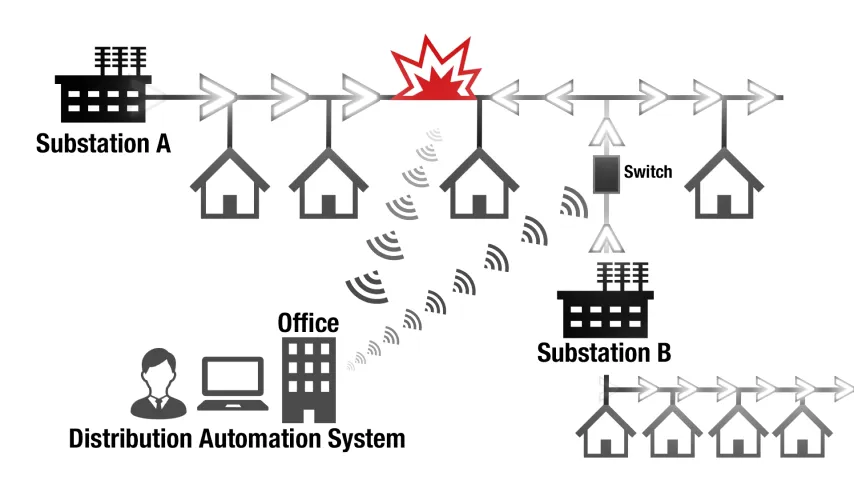
The distribution region and direction of power transmission are fixed at each substation. For example, though the transmission area of Substation A is connected to Substation B via distribution lines, the direction of transmission is fixed, and under normal circumstances, power is not distributed from Substation B. A power outage occurs when power distribution lines are damaged by fallen trees in the Substation A area.
This is where power distribution automation comes in.
First, the system identifies the area in which damage of the power distribution line occurred. When it is found that there are areas to which power cannot be transmitted from Substation A, switches installed on utility poles in the adjacent Substation B area are operated remotely to transmit power from Substation B in the opposite of the usual direction. By using a distribution automation system, electricity can be sent even to sections with operational facilities in the Substation A area affected by the blackout.
Before these systems were introduced, transmitting electricity to the end of a damaged power distribution line required workers to manually operate these switches. It took workers a long time to locate and travel to the sites of the damaged power distribution lines. With a distribution automation system, however, the area and duration of the blackout can be minimized.
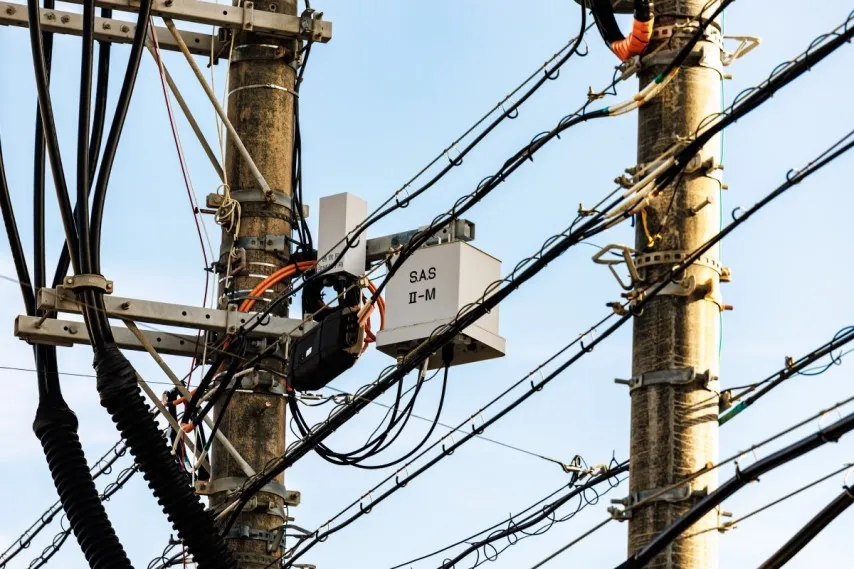
Two Challenges Faced by OEPC
The Okinawa Electric Power Company, Incorporated first deployed the distribution automation system in 1995. But the company faced two challenges related to this system, according to Masato Oshiro, head of the Okinawa Electric Power Distribution Operations Group, who was tasked with updating the system.
“The first challenge was to strengthen the coordination between the multiple systems used within the main island of Okinawa. The second challenge was to standardize the systems used on the remote islands with those of the main island. In doing so, we wanted to reduce the workload of the operators of power distribution systems and further improve safety conditions for restoration workers.”
In previous distribution automation systems, operators collected information on multiple systems during disasters and other emergencies, analyzed the situations, and established recovery procedures to reduce the duration of power outages.
“Workers would go to the sites to identify where incidents were occurring. As such, the operators needed to gather a lot of information to accurately assess the situation. If an operator made an error in their assessment, they ran the risk of misdirecting power to sites where work is being performed. To remedy this problem, we needed to strengthen the coordination between multiple systems.”
Power outages caused by typhoons are common both on the main island and the remote islands of Okinawa. When it has been determined that the Miyako and Yaeyama areas will suffer severe damage due to an approaching typhoon, Okinawa Electric Power Company has been proactive in dispatching employees from the main island to the affected areas. However, the specifications of the power distribution automation system used on the remote islands differed from those of the main island. Because of this, employees who came from the main island to provide assistance could not always carry out their work smoothly.
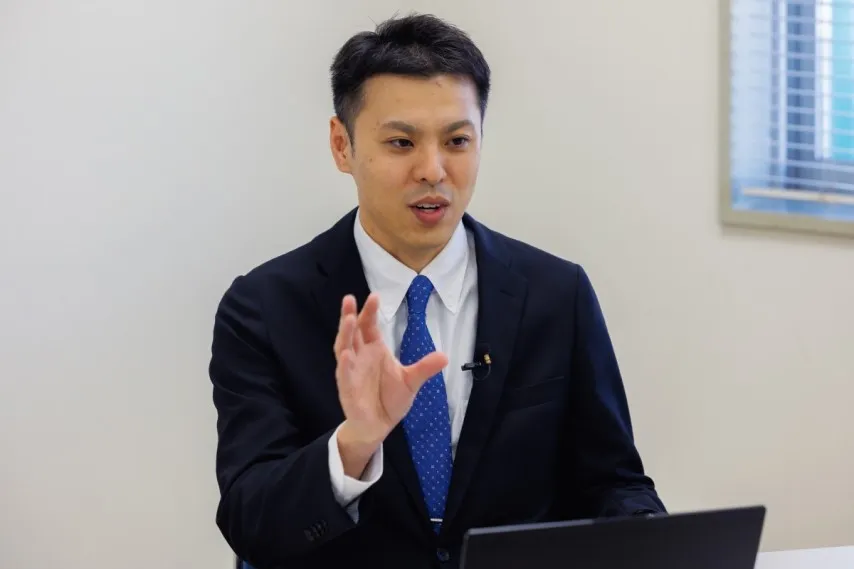
These issues were communicated to Fuji Electric, and several adjustments were made accordingly. The resulting new system includes the addition of maps and search capabilities. Information on distribution lines is now compiled and managed by a single system. The systems on Okinawa Main Island were consolidated, commencing operations in 2018. By 2020, the same system had been deployed in Miyako Island and Ishigaki Island.
“By enhancing the coordination between these systems, we have enabled workers to accurately ‘visualize’ various information, which has greatly reduced the workload of operators in charge of power distribution. At the same time, the safety functions have been upgraded to ensure the safety of workers involved in restoration work. Furthermore, the specifications for the main island and the remote islands have been standardized, enabling restoration work to be carried out quickly throughout Okinawa Prefecture.”
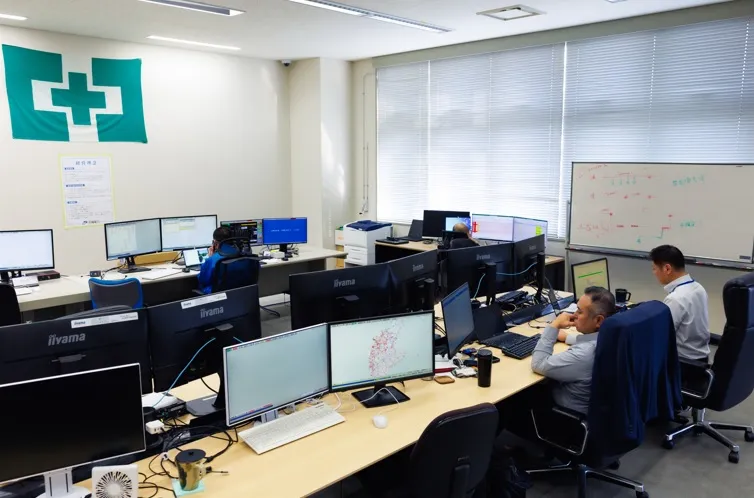
Intuitive Control of Distribution Even for Remote Islands
Oshiro comments on the advantages of the new system.
“It was made to be intuitive, like a Windows PC, making it easier to operate. This makes erroneous operations less likely and improves safety.”
Standardized specifications are not only beneficial for night duty, but also for improving the efficiency of daytime work and addressing labor shortages. This is because it is now possible to monitor, measure, and control distribution on the entire main island, Miyako Island, and Ishigaki Island from a single base, thereby enabling the efficient deployment of limited personnel.
But that's not the only feature of the new system.
Two Years of Middleware Development for BCP Compatibility
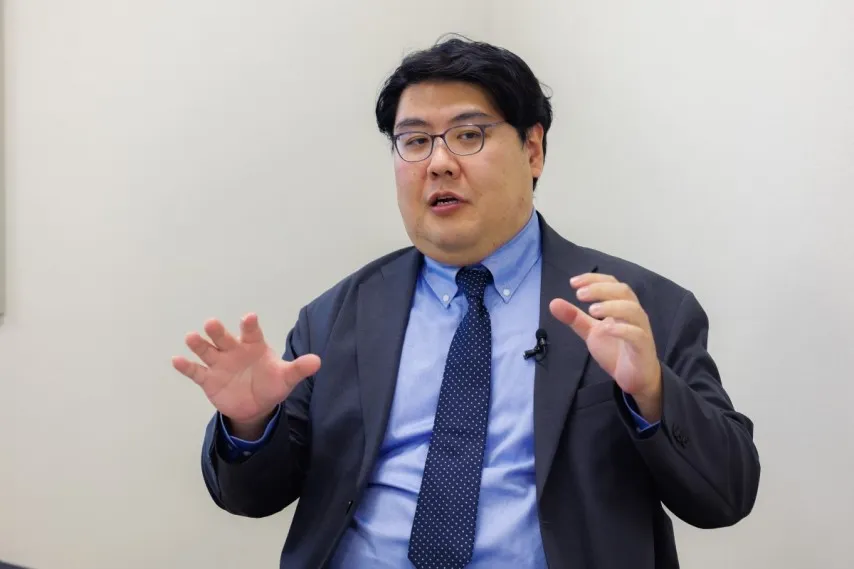
“It is also important that the new system is compatible with BCPs.”
These are the words of Tsurugi Matsueda, Chief Expert of Technology Division I in the Power & Energy Management Department of Fuji Electric’s Energy Business Group.
There is a serious need to establish a system that can provide a stable supply of electricity, which is part of our infrastructure. To address this demand, in 2018, Okinawa Electric Power Company launched a system that is compatible with BCPs, thereby ensuring business continuity even in the event of natural disasters, fire, terrorism, or other emergencies.
Fuji Electric has developed proprietary middleware that continually matches the original data with the backup data.
Matsueda describes this as the “most difficult part of the system update.” The middleware took about two years to develop, from requirements to completion.
This led to the creation of a new system that is compatible with BCPs and allows servers to be switched instantly so that if one server stopped, the other can continue to operate. Mr. Oshiro of Okinawa Electric Power Company shares his thoughts on this system.
“Fortunately, there have been no incidents where the main server became unusable after the update. There are times when we must temporarily shut down a server for maintenance, but spreading out the servers has made maintenance and inspections smoother. The benefits of BCP compatibility are notable.”
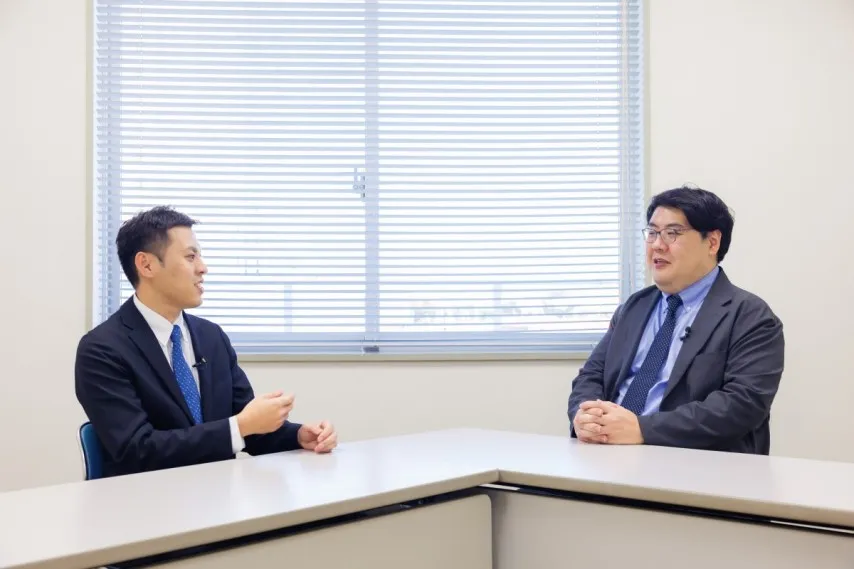
Ten Nights in the Control Room During Typhoon No. 6 in 2023
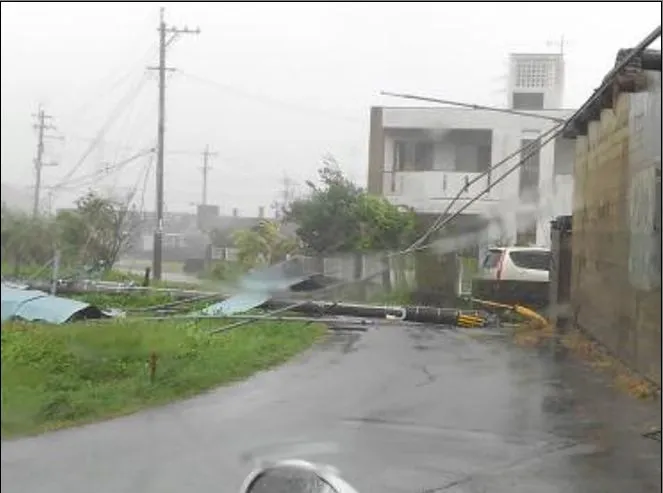
The new system was tested by Typhoon No. 6, which hit Okinawa between July and August 2023.
After having passed through the main island once, Typhoon No. 6 then made a U-turn and approached the main island once again. Okinawa found itself in the middle of a storm zone for about two weeks.
Mr. Oshiro stayed in the command room for ten nights to carry out his duties.
“After a prolonged period of harsh conditions at the response sites, we were reminded of the importance of the distribution automation system.”
Operating in a region at high risk of power outages due to typhoons, the employees of Okinawa Electric Power Company are capable of handling the entire response process, from the assessment of damage from the control room, to on-site repair work such as the removal and pruning of trees in contact with power lines and the subsequent repair work.
However, restoration work cannot be carried out during storms. This is due to the risk of secondary disasters, such as workers sustaining falls due to strong winds, injuries caused by flying objects, and electric shocks due to contact with broken electrical wires.
System Benefits: Newspaper Report on the Decrease in the Number of Homes Affected by the Blackout
Thanks to an automated system that reduces the need for direct visual inspection and allows distributed power to bypass problematic areas, the time required to recover from power outages has been significantly shortened.
The Okinawa Times Plus (electronic version) reported on the situation of power outages in the prefecture on August 9, 2023.
“At 10:00 a.m. on the second day, there were 215,800 homes in 34 municipalities were affected. As a general rule, Okinawa Electric Power Company does not carry out restoration work at affected sites in the midst of ongoing storms to avoid secondary disasters involving workers. However, by 7:00 p.m. on the same day damage assessments began, the number of affected homes had dropped to 185,550.”
A Conviction Arising from the Great East Japan Earthquake
Mr. Matsueda joined the company in 2009 and was assigned to the power distribution business, a field unrelated to his university research. He says that it has always been in his nature to want to support people from behind the scenes, and the Great East Japan Earthquake in 2011 reinforced this desire. The disaster struck while Mr. Matsueda was assigned to the Tohoku region. Watching the disaster unfold on TV changed the way he approached his work.
“I thought to myself, ‘I'm the only one who can make this situation better. This is the work that I must do.’”
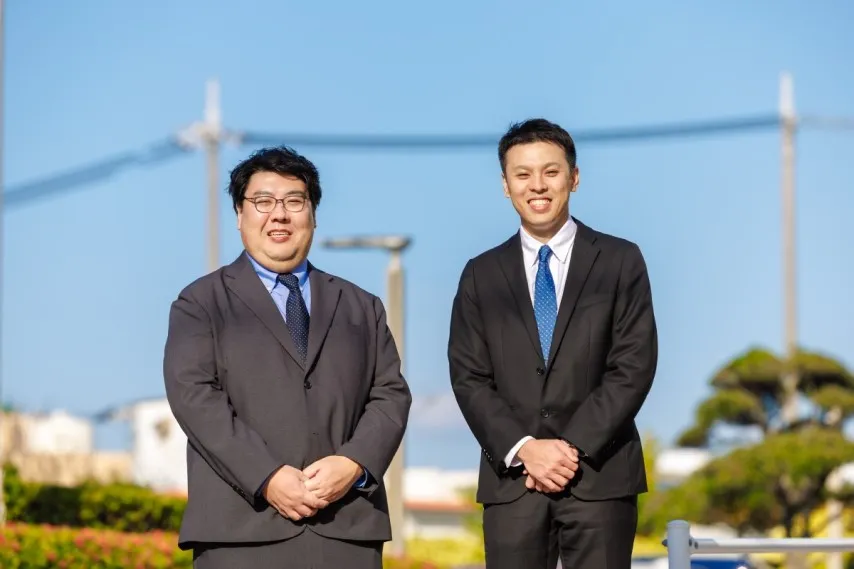
Brainstorming for the Next System
The new system has been in place for over five years.
As Mr. Oshiro describes, the Okinawa Electric Power Company and Fuji Electric have begun to design specifications for the next system.
“The current system requires further improvement. In the 2018 update, the specifications were standardized so that they can be controlled at one site, but facility data is still managed at each site. In the next update, we want to consolidate our database of facilities so that we can control them more seamlessly.”
Mr. Matsueda adds his own thoughts.
“I want to continue working with the Okinawa Electric Power Company to build good infrastructure. Meanwhile, there are some areas in Japan where our systems have not yet been adopted, so we would like to propose our solutions to those regions as well.”
Behind the scenes, the lifestyles that we lead without a second thought are sustained by the sense of mission upheld by power companies and the continuous technological innovation of Fuji Electric.
Recommended
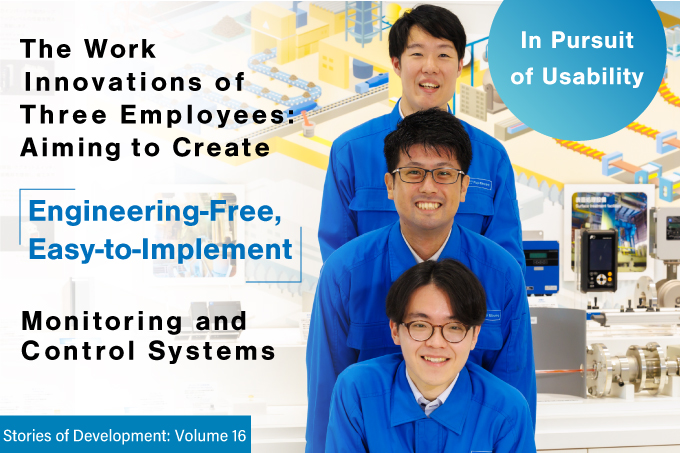
July 2,2025
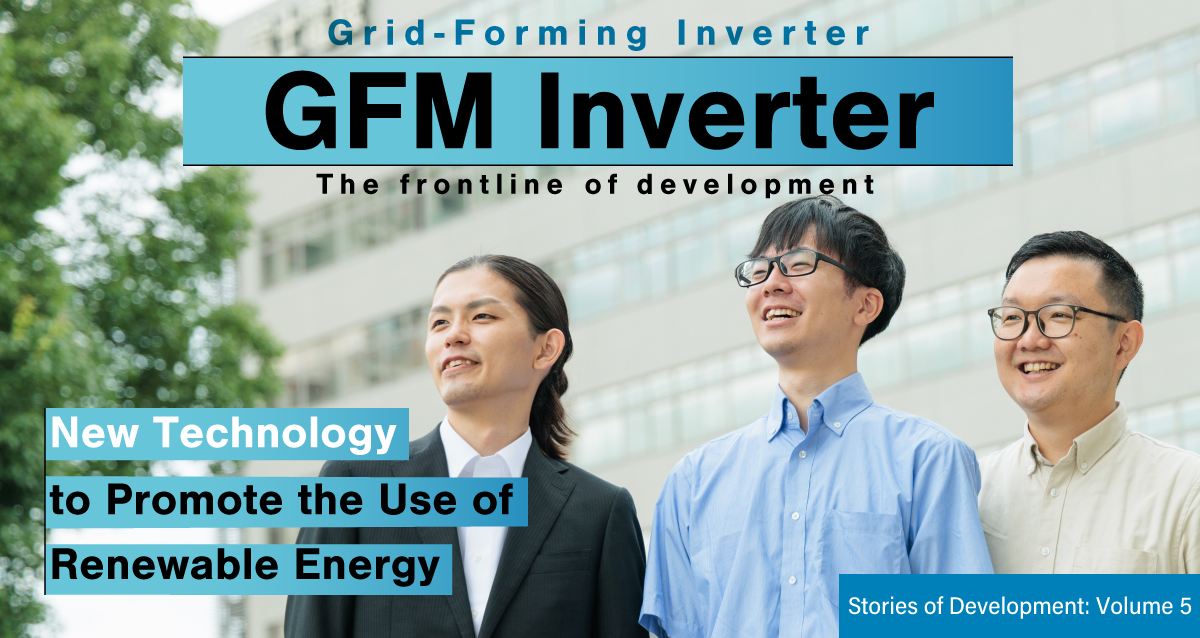
October 31,2024
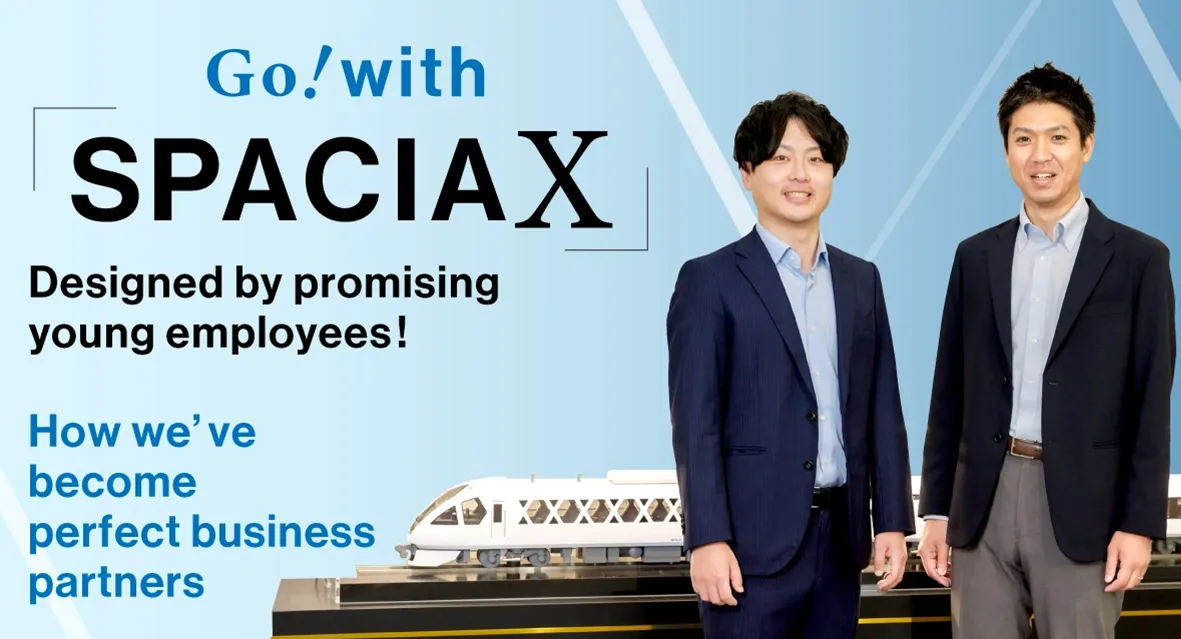
October 21,2024
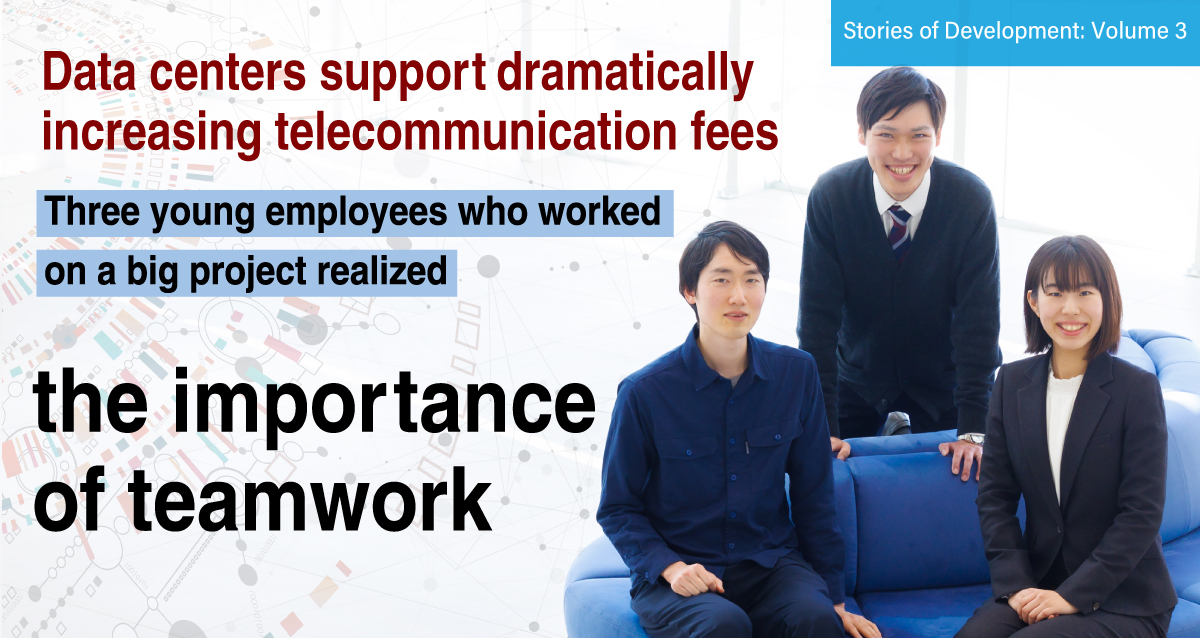
October 2,2024