Fuji Electric Product Column
What Does an Inverter Do ?
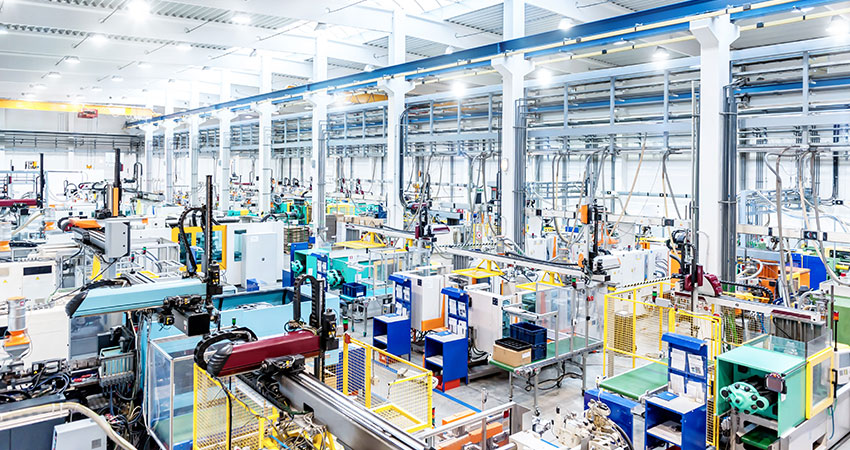
What Does an Inverter Do ?
People often see inverter air conditioners and inverter refrigerators at home and offices lately. Inverter appliances are widely in malls and online shops. Customers buy them because they are known to be energy efficient. But sales representatives and even commercials do not explain how an inverter works.
What Does an Inverter Do ?
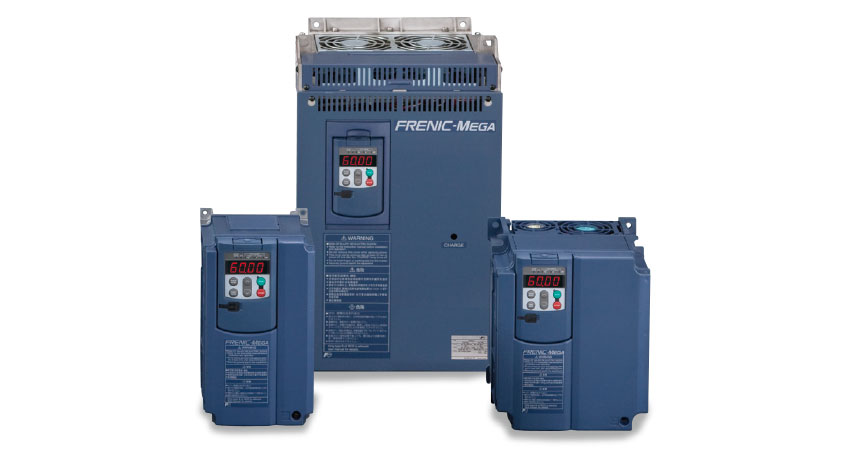
Inverters are also called AC Drives, or VFD (variable frequency drive). They are electronic devices that can turn DC (Direct Current) to AC (Alternating Current). It is also responsible for controlling speed and torque for electric motors.
Electric motors are found in most devices we use to do work such as small electronics, transportation, and office appliances. These motors need electricity to run. Matching the motor’s speed to the required process is essential to avoid wasting energy. In factories, wasted energy and materials could put the business at risk, and so inverters are used to control electric motors, boosting productivity and saving energy.
The Technology Behind Power Conversion and Motor Control
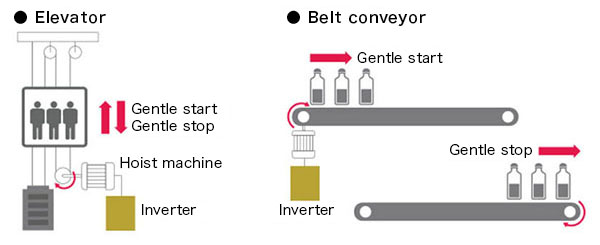
An AC drive works between a power supply and an electric motor. Power goes into the AC drive and regulates it. The regulated power is then sent to the motor.
An AC drive consists of a rectifier unit, a DC intermediate circuit, and an inverse conversion circuit. The rectifier unit inside an AC drive can be unidirectional or bidirectional. The former can accelerate and run the motor by taking energy from the electrical network. A bidirectional rectifier can take the mechanical rotation energy from the motor and send it back to the electrical system. A DC circuit will store the electrical power for the inverse conversion unit to use.
Before the regulated power is received by the motor, it undergoes a process inside the AC drive. The input power runs into a rectifier unit and the AC voltage is converted to DC voltage. The DC intermediate circuit smoothens the DC voltage. It then flows through the inverse conversion circuit to convert the DC voltage back into AC voltage.
This process allows the AC drive to adjust the frequency and voltage supplied to the motor depending on the demands of process. The speed of the motor increases when the output voltage is at a higher frequency. This means that the speed of the motor can be controlled via the operator interface.
Benefits
1. Energy-saving
Fan and pump applications benefit significantly from AC drives. Superior to dampers and on/off controls, using AC drives can reduce energy consumption by 20 to 50 percent by controlling motor rotation. It is similar to reducing the speed of a car. Instead of using breaks, the speed of the car can be reduced by lightly pressing on the accelerator.
2. Soft Starters
An AC Drive starts the motor by delivering power at a low frequency. It gradually increases the frequency and motor speed until the desired speed is met. Operators can set the acceleration and deceleration at any time, which is ideal for escalators and conveyor belts to avoid dropouts of loads.
3. Controlled Starting Current
It takes seven to eight times of the AC motor’s full-load current to start the motor. The AC drive reduces the starting current, resulting in fewer motor rewinds, and this extends motor life.
4. Reduced Power Line Disturbances
Starting an AC motor across the line can place an enormous drain in the power distribution system, causing a voltage sag. Sensitive equipment such as computers and sensors will trip when a large motor starts. The AC drive eliminates this voltage sag by removing the power from the motor instead of tripping.
5. Easily Changes the Direction of Rotation
AC drives can handle frequent start and stop operations. It only needs a small current to change the direction of rotation after changing the rotation command. Stand mixers can produce the right output as the direction of rotation, and the number of revolutions can be controlled with an inverter drive
6. Simple Installation
AC drives are pre-programmed. Control power of auxiliaries, communication lines, and motor leads are already factory wired. The contractor only needs to connect the line to the power source that will supply the AC drive.
7. Adjustable Torque Limit
AC Drives can protect motors from damage by accurately controlling the torque. For example, in a machine jam, the motor will continue to rotate until the overload device opens. An AC drive can be set to limit the amount of torque applied to the motor to avoid exceeding the torque limit.
8. Elimination of Mechanical Drive Components
An AC drive can deliver low or high-speed required by the load without speed-increasing or reduction devices and gearboxes. This saves maintenance costs and floor-space requirements.
Low and Medium Voltages
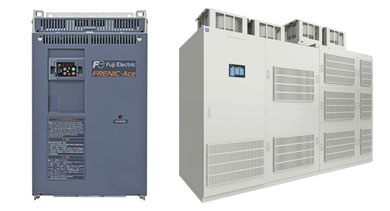
AC drives are classified as Low Voltage (LV) and Medium Voltage (MV). In procuring AC drives, there are several factors to consider.
An LV drive has an output of 240 to 600 volts of alternating current (VAC). They are commonly used in conveyor belts, compressors, and pumps. Since LV drives cause less stress to the motor, minimal maintenance is required. It also consumes less energy. An LV drive produces high frequency and better motor performance at low voltage, thus reducing production cost.
On the downside, low voltage creates more current. If LV drives are used with high horsepower (HP) machines, it generates more heat and increases the room temperature. More current means more generated heat. Installing vents and additional air-conditioning is necessary.
Huge and multi-megawatt electric motors in power stations and metal processing plants use MV drives. They have an output of 4160 VAC but can go high as 69,000 VAC. They require a high input voltage to achieve a high output voltage. In terms of costs, MV drives require larger and expensive breakers and transformers. They are physically bigger compared to LV drives. MV Drives also undergo regular maintenance under the supervision of an OEM Engineer, unlike LV drives that can be maintained by an in-house electrical maintenance team.
Conclusion
Companies and regular consumers strive to conserve energy. This has propelled the development of inverters in machineries and regular appliances. Inverters are hidden and stored in rooms with adequate ventilation. Nonetheless, they play a great role in energy saving. The ability to accurately control office devices depending on demand can significantly reduce energy consumption and production waste.
Related products
Recommended
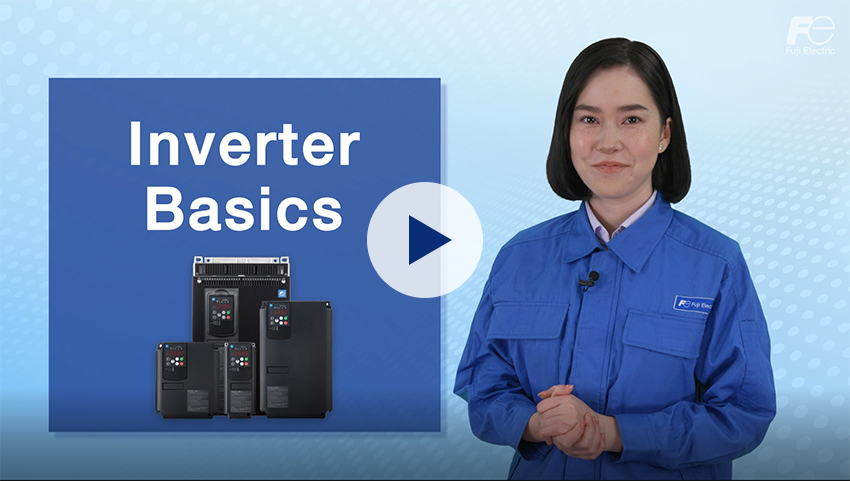
Understanding application, benefits, basic structure, case study, types, and Fuji Electric's inverters with this video.
December 27,2021
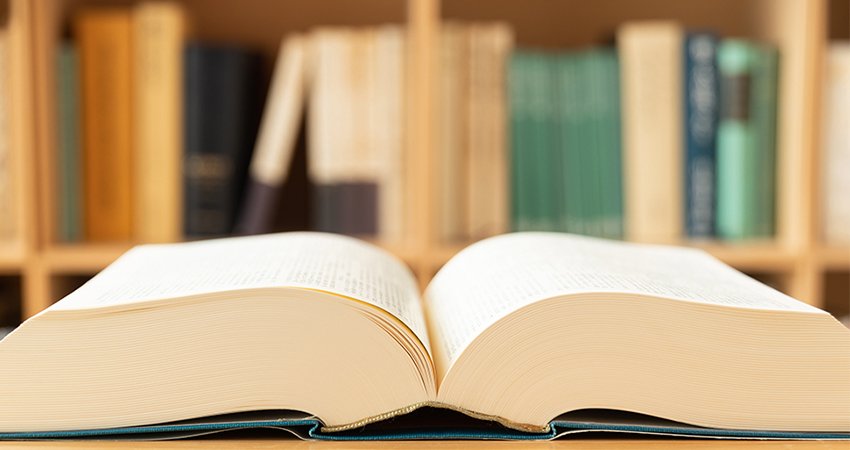
Understanding the basics: Differences between inverters and converters
January 20,2021
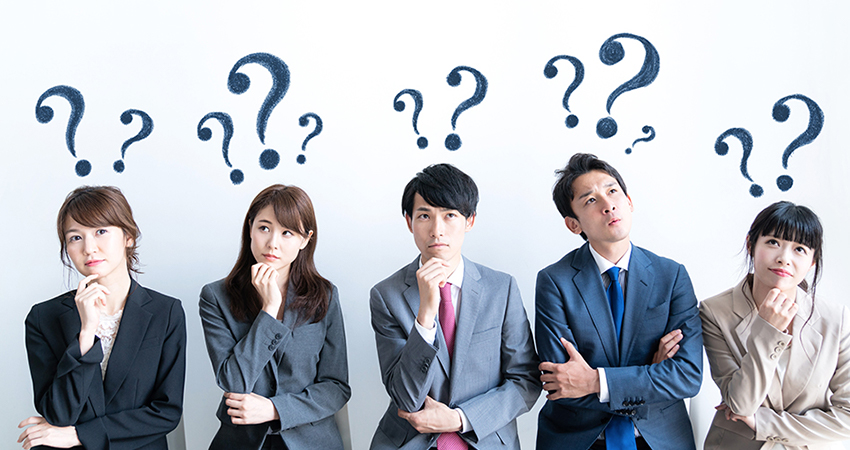
How and what does an inverter take control of? A brief explanation to grasp the basic structure.
January 20,2021