Optimal operations
Optimal operations of the holder facilities, oxygen generation facilities, and power generation facilities are performed as these facilities have a particularly large energy-saving effect in steelworks. In addition, overall optimal operation plans (daily and monthly plans) are provided. Based on the results of these operations, the operation balance of the by-product gas, power and steam facilities is optimized to minimize the operating costs.
Minimization of the amount of by-product gas emissions improves the recovery efficiency of by-product gas and reduces the amount of energy purchased.
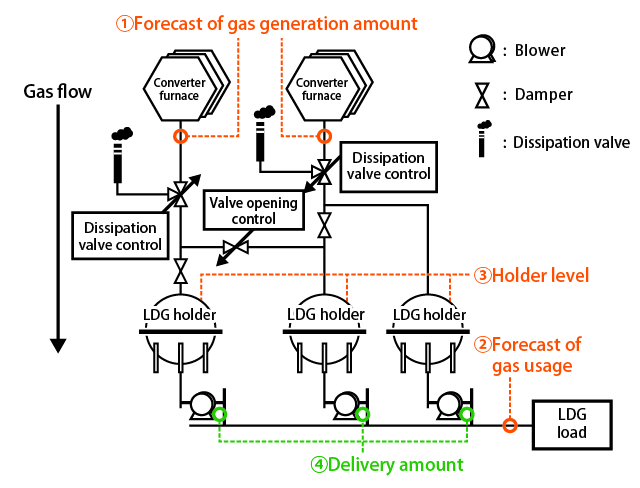
-
Input data and output data
The LDG generation amount forecast (①), the LDG usage amount forecast (②), and the current holder level (③) are input, and the LDG release amount for each holder that minimizes the amount of emissions (④) is output by an optimization calculation.
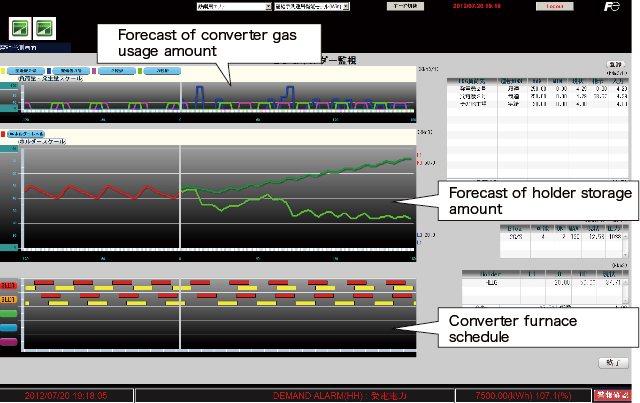
An optimal operation plan is created based on the displayed actual LDG generation and usage amounts and the forecast LDG generation and usage amounts, and a decision is made to minimize the fluctuation of the emission amounts and the delivery amounts.
90% reduction of emissions (annual)
Trial calculation condition
Additional holders are installed and operations are optimized at a steelworks producing about 10 million tons of crude steel annually
Minimization of the amount of power consumed from the forecasts of required oxygen amounts reduces the amount of energy purchased.
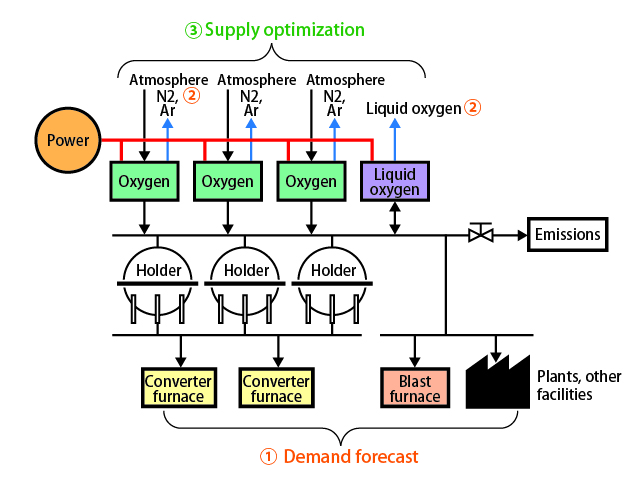
-
Input data and output data
The demand forecast for oxygen (①), and the delivery amounts of N2, Ar, and liquid oxygen (②) are input, and an oxygen generation plan that minimizes power consumption (oxygen supply balance ③) is output by an optimization calculation.
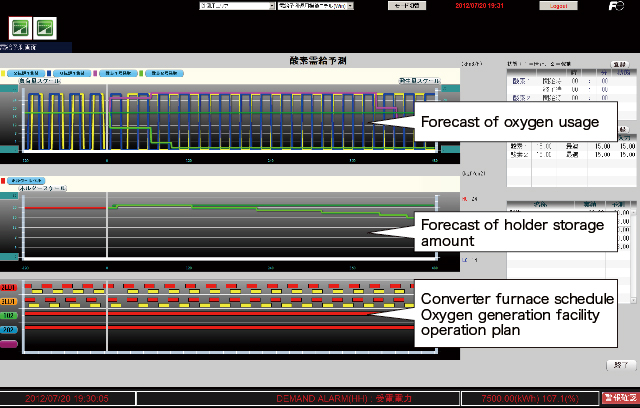
Minimization of the amount of power consumed from the displayed oxygen generation amount and actual holder level values and from the forecast required amount of oxygen reduces the liquid oxygen evaporation amount and emission amount.
2.8% reduction in energy consumed by oxygen generation facility (annual)
Trial calculation condition
Trial calculation for a steelworks producing about 8 million tons of crude steel annually (compared with operation by conventional operators)
Understanding the differences in the efficiency of multiple power generation facilities and obtaining maximum power generation from by-product gas by allocation of boiler fuel and turbine steam minimizes the amount of power purchased.
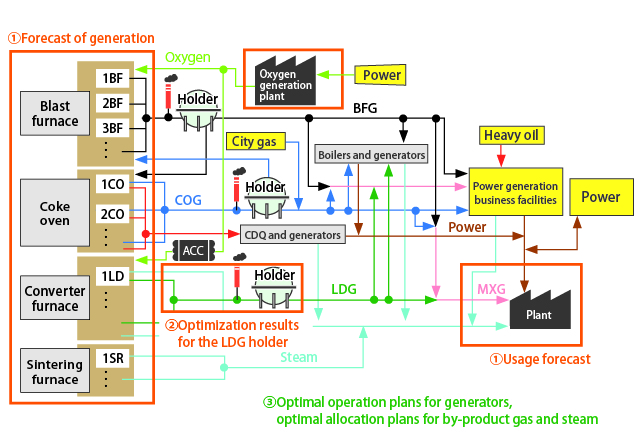
-
Input data and output data
The generation and usage forecast results for by-product gas and steam (①), and the optimization results for the LDG holder and oxygen generation plant (②) are input, and optimal operation plans for the generators and optimal allocation plans for byproduct gas and steam that minimize the operation cost (③) are output by optimization calculation.
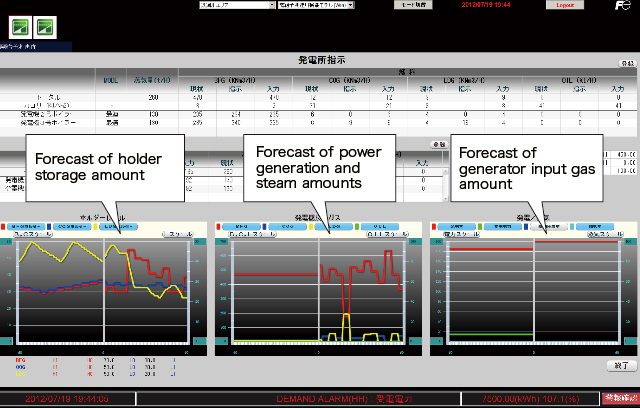
Based on the efficiency of each of the power generation facilities, create operation plans and by-product gas and steam allocation plans to make maximum use of the power generation facilities. These plans will improve the power generation efficiency.
2.0% increase in power generation (annual)
Trial calculation condition
Optimal operation of generators at a steelworks producing about 8 million tons of crude steel annually
While meeting the required demand based on generation and usage forecasts for various types of energy, an optimal allocation plan for about one day in 30-minute cycles is devised. At the same time, implementing an optimal allocation plan for one month also minimizes the monthly operation costs.
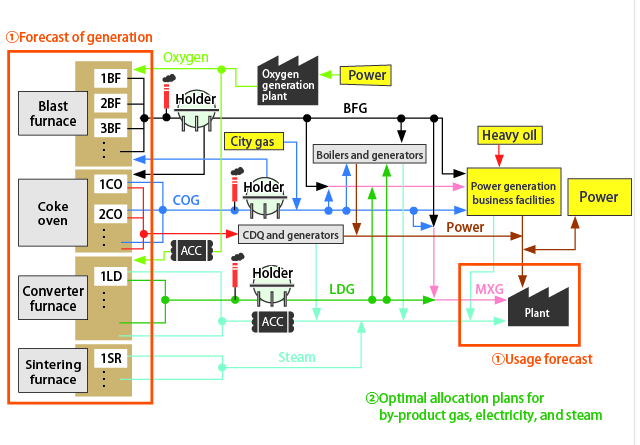
-
Input data and output data
The generation and usage forecast results for by-product gas and steam (①) are input, and optimal allocation plans for byproduct gas, electricity, and steam that minimize the operation cost of one day (②) are output by optimization calculation.
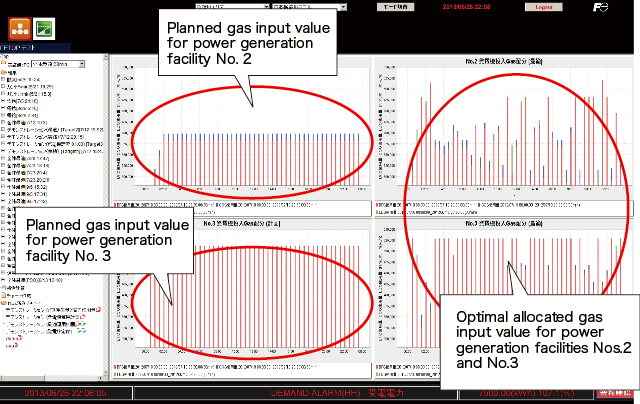
Optimal allocation plans for 24 hours in 30 minute-intervals are devised for each energy source: by-product gas, power, and steam. The operation balance of each facility is optimized. The operation results while maintaining the current operation and after optimization can be compared using the simulation function.
3.5% reduction in cost of purchased power
Trial calculation condition
Overall optimal operations at a steelworks producing about 8 million tons of crude steel annually