Solutions and Case Studies
EMS solutions for the semiconductor field
at Fuji Electric’s Yamanashi Factory (Semiconductor manufacturing)
to solve energy-saving and production line stoppage challenges
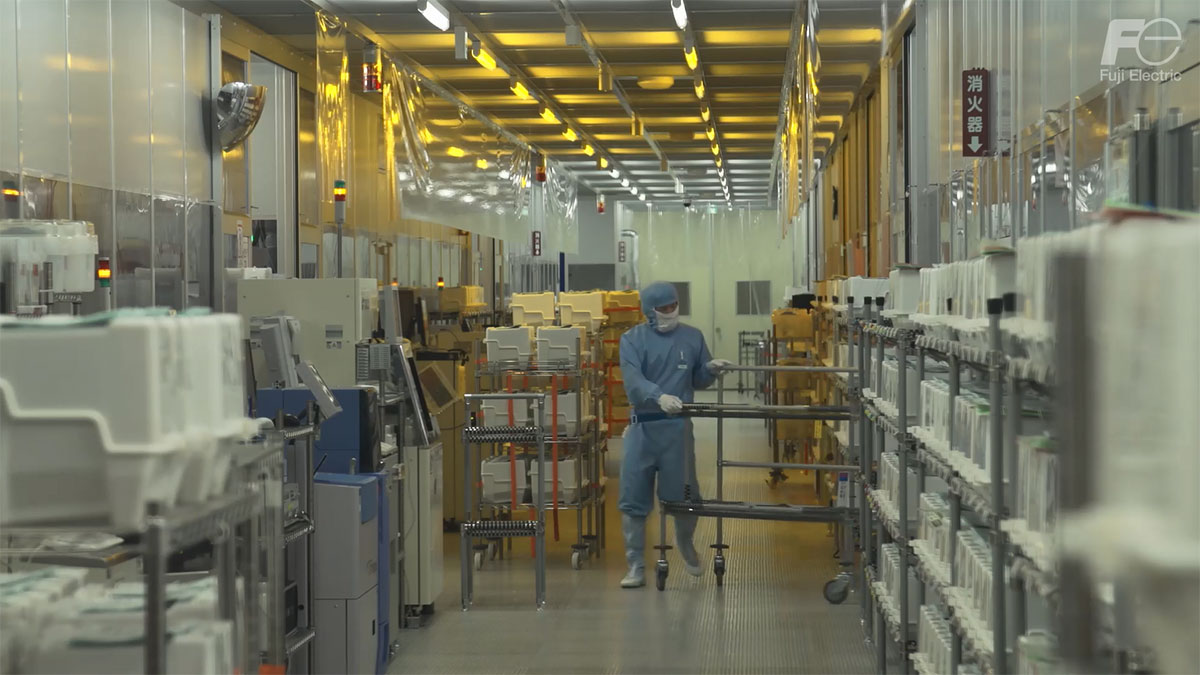
What were the challenges at the Yamanashi Factory ?
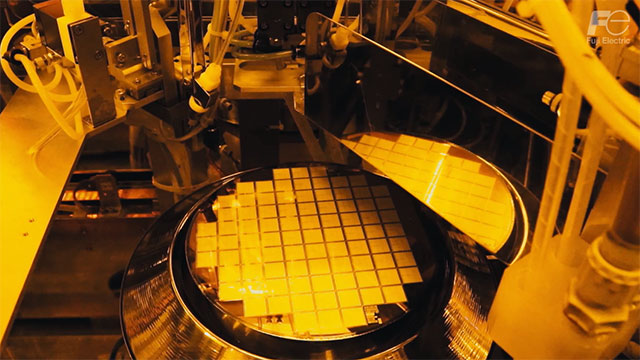
Fuji Electric’s Yamanashi Factory produces chips for power semiconductors — the key devices that enable energy conservation and miniaturization. The production of semiconductor chips requires a particularly large amount of energy. In addition, production line stoppages resulting from momentary power drops and power outages caused by lightning or wildlife damage can lead to heavy losses. As such, the factory grappled with the challenges of energy conservation and full-time energy.
To address these challenges, our Yamanashi Factory decided to build systems to optimize its use of electric and thermal energy.
Achieving a 34% reduction in energy usage over five years
To achieve energy conservation, Fuji Electric followed the steps of visualization, interpretation, and optimization in our energy management work.
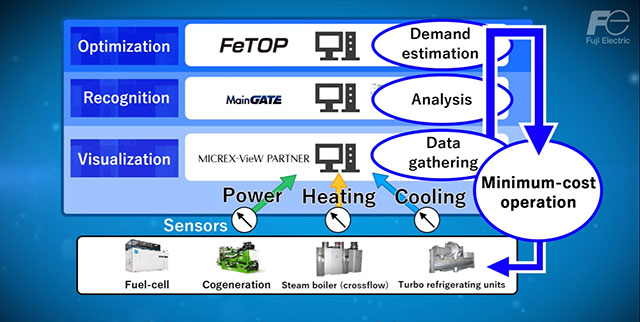
We collect data using sensors and make use of our analysis software to analyze the accumulated performance data from a number of aspects in order to find the muri, muda, mura — the burdens, waste, and unevenness.
For the optimization, an AI engine predicts the latest energy demand and creates a plan for the optimal operation patterns that will minimize the energy cost. Through the following measures, our Yamanashi Factory has achieved a 34% reduction in energy usage over five years.
Three measures implemented to keep production lines running
1. Reducing the risk of momentary power drops and power outages on the grid
We implemented high-efficiency fuel cells and gas cogeneration to prevent production line stoppages that can lead to large losses. These measures minimize the risk of momentary power drops and power outages on the grid.
2. Measures against power outages caused by lightning or wildlife damage
Production lines can be impacted by natural environmental causes. To keep the production lines from stopping when a power failure caused by lightning or wildlife damage occurs, we implemented a one-cycle circuit breaker that instantly disconnects critical loads from the grid and switches over to independent fuel cell and cogeneration operation without interruption to maintain the operations of the factory.
3. Implementation of high-voltage UPS for the most critical loads
The most critical loads are protected by a UPS to ensure double and triple layers of protection.
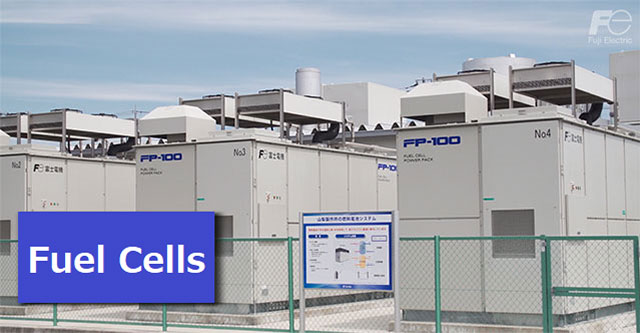
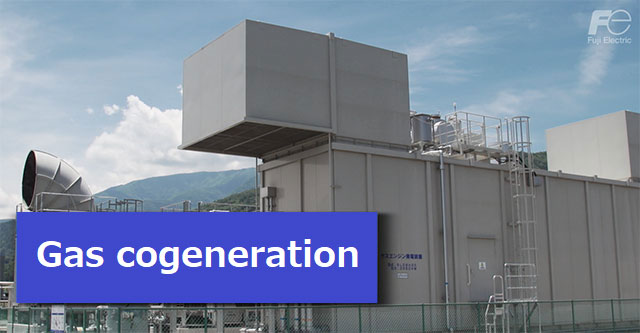
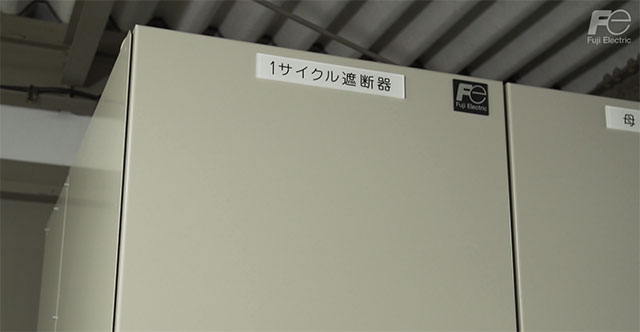
Our Yamanashi Factory has achieved significant energy savings through the implementation of these solutions and various initiatives despite the factory’s increase in production volume. The factory received the 2016 Energy Conservation Grand Prize in the Minister of Economy, Trade and Industry Awards for its efforts in achieving 100% self-sufficiency in energy.
In the future, we will utilize IoT and AI technologies to automatically analyze factors that reduce the efficiency of each device and system. We will additionally implement functions such as automatic tuning of operating parameters based on the analysis results and will continue to proceed from partial to overall optimization of the equipment in the factory.