What is PLC
Understand in just 10 minutes!
Complete explanation of PLC essentials for automation
Complete explanation of PLC essentials for automation
In Japan, the automation of machinery and equipment has been progressing since the 1980s in various manufacturing industries, particularly in the automotive industry.
As you already know, automated equipment and industrial robots are actively being used in many assembly and processing production lines.
Devices called PLCs (programmable logic controllers or programmable controllers) play an important role in controlling the operation of these types of machines. We will start with a complete explanation of the basics of PLCs, and then describe their structure,types and programming languages.
What are PLCs and what makes them the most important component in machine automation?
PLCs are very useful for automating production lines, but they also support everyday facilities, such as elevators, water and sewage plants, dams, plant factories and amusement park attractions.
To explain what PLCs are very concisely, they are just like “small computers.” It may be easier to understand them if you think of them as devices that can control machines by using programming instructions.
Prior to the advent of PLCs, electrical circuits were designed from scratch using relays, timers and other devices to perform “sequence control” in order to operate machines in a sequential order.
However, PLCs have made it possible to freely control machines with just programming instructions.
In addition to on/off output, the control provided by PLCs can now perform processing using more advanced operations (such as PID control and S-curve velocity control). PLC functionality has continued to evolve over the years.
Recently, the advancement of digital transformation (DX) has enabled PLCs to become one of the key components behind IoT and smart factories.
In the past, PLCs could only perform simple operations such as addition and subtraction, but today’s PLCs can handle trigonometric functions such as sin, cosine and tan.
For example, PLCs can be used to optimally calculate the angle at which wind strikes the blades in wind power generation systems in order to generate electricity more efficiently.
What are the internal structures, types, advantages and disadvantages of PLCs?
In the previous section, we explained that PLCs are like “small computers,” but we will now take a look at their internal structure, functionality and available types
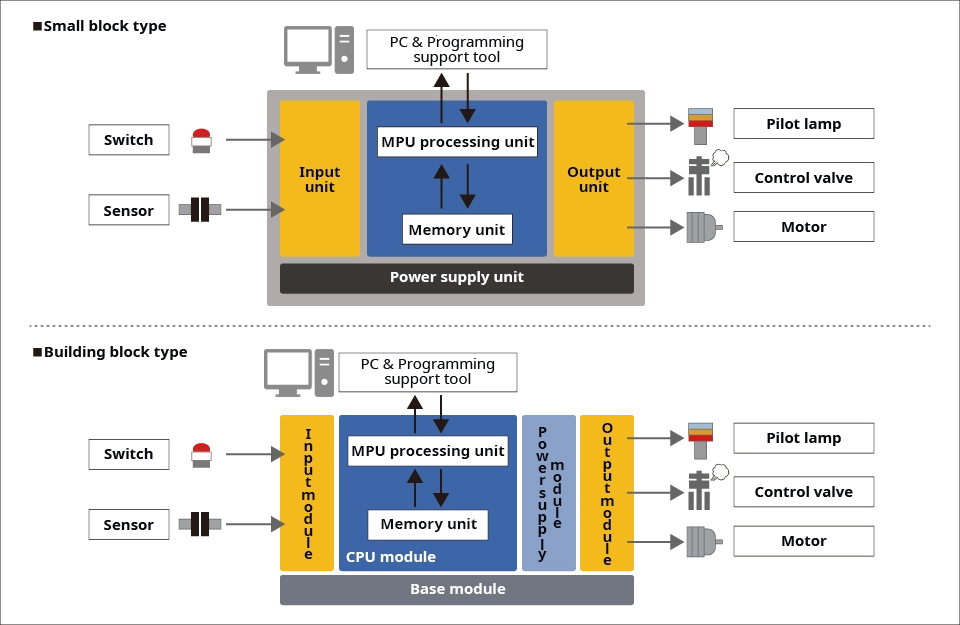
To begin with, PLCs come with an “input unit” that captures signals from switches and various sensors.
The core components of a PLC consist of an “MPU* processing unit” that processes input signals and a “memory unit” that stores programs and data.
Its main components also include an “output unit” for outputting the MPU’s processing results to external devices and a “power supply unit” for supplying necessary power.
(*Electronic component that performs processing on the CPU)
There are two types of products: a “small block type”that combines all of these functions in a single enclosure and a “building block type ”that allows users to freely combine and customize modules that are categorized by functionality. The advantages and disadvantages of each type are as follows:
【Small block type】
The biggest advantage of this type is that it is small and affordable, making it easy to introduce. However, its disadvantage is that it lacks flexibility, since the basic functions are integrated in a single enclosure.
It also has limited program capacity and I/O points, and also lacks advanced features.
However, if your company’s system is small and requires only simple control, a small block type PLC will do the job sufficiently.
【Building block type】
Since the necessary modules (blocks) are assembled together, this type’s advantage is that it provides flexible control suitable for your company’s machines and systems. Sometimes a base module is also provided for mounting modules.
By expanding its I/O modules, this type can support large-scale control applications with tens of thousands of I/O points.
For critical systems that cannot be shut down, such as public infrastructure, redundancy can be used to increase reliability.
However, it is more expensive than the small block type because it must be purchased on a per module basis.
Modules for building block type include CPU modules, I/O modules and power supply modules.
Some CPU modules come with useful features such as the ability to download setup data from a host machine to change PLC settings, or conversely, to upload logging data collected by the PLC.
Depending on the product, communication modules (Ethernet, as well as fieldbuses such as PROFIBUS or DeviceNet) used for communication on dedicated networks and positioning modules used for machine positioning control by high-speed pulses are also available.
Which types are mainstream? What are the five languages for creating control programs with PLCs?
One of the main features of PLCs is that they can be programmed to freely change the operation and timing of a machine.
So, what must I do to create a PLC control program? In general, users must install dedicated software (programming support tool) provided by PLC manufacturers on their PCs and then transfer control programs created with the software to their PLCs.
When creating programs for PLCs, each PLC manufacturer has traditionally used its own language.
However, more and more PLCs are adopting languages that conform to the “IEC61131-3” International Electrotechnical Commission (IEC) standard.
The following five programming languages are used in “IEC61131-3”:
【PLC languages】
The instruction list (IL) language is a text language that offers commands similar to microcomputer assemblers, such as “LD,” “OR” and “AND.” It is useful for making applications smaller and faster, but has weaknesses in terms of programming productivity and maintainability.
The most commonly used language is LD (ladder diagram).
The LD language is popular because it resembles the sequence diagram notation used in the past and is easier for engineers to understand
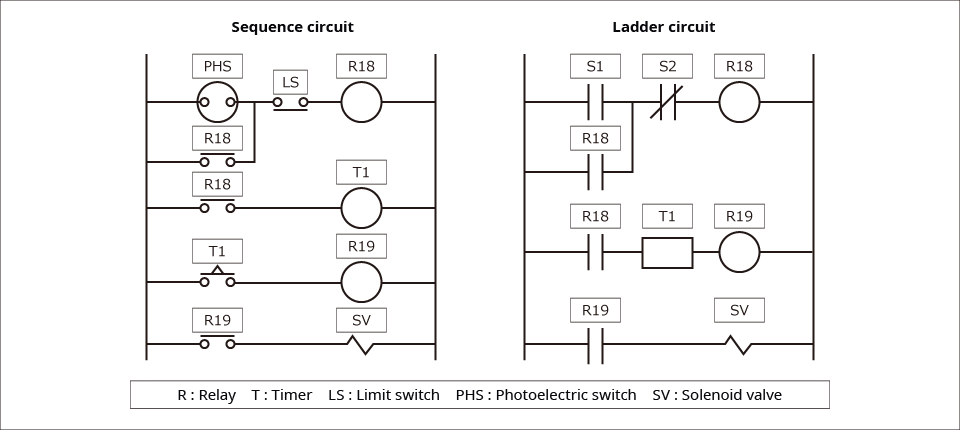
The FBD (function block diagram) language enables users to combine graphical function blocks (e.g., addition and subtraction) to create arithmetic logic Frequently used programs and circuits can be reused more easily by making use of function blocks.
The ST (structured text) language is a PASCAL-based structured text language.
It is similar to the C language and this makes it suitable for software engineers.
It is very useful for complex control and nesting of branch conditions that are difficult to implement in ladder language.
The SFC (sequential function chart) language is a graphical language that enables users to create clear descriptions of transition conditions and processes that take place between production line processes.
Each process is represented by a box-shaped step.
When transition conditions are fulfilled, the next step in the sequence is executed (this is called activation).
So far, we have briefly introduced the features of the languages used to develop programs for PLCs. As mentioned before, each manufacturer has its own distinctive programming support tools.
Some tools support all of these languages, while others support only a few commonly used languages.
When selecting a PLC, the first thing to do is to consider the scale of the machine or system to be controlled.
Then, carefully check the PLC type (small block type or building block type), functions and performance according to the control target.
As far as hardware is concerned, some PLCs can achieve high-performance control with speeds of just a few milliseconds. As for software, it is important to consider the ease of programming and functionality of the programming support tools.
The latest PLCs come with so many features that we cannot cover them all here.
If you have any questions or concerns about introducing PLCs or need more information, please visit our website using the following link: