Launch of the Industrial Drives FRENIC-GS Series for Plants to Contribute to Decarbonization and DX on the Production Sites
Launch of the Industrial Drives FRENIC-GS Series for Plants to Contribute to Decarbonization and DX on the Production Sites
( PDF(134KB))
May 30,2024
Fuji Electric Co., Ltd.
Fuji Electric Co., Ltd. is pleased to announce the launch of the industrial drives FRENIC-GS series for plants, which reduces power loss and increases the amount of data that can be transmitted to help achieve decarbonization and DX on the production sites of the material industry and the assembly processing industry.
1. Background
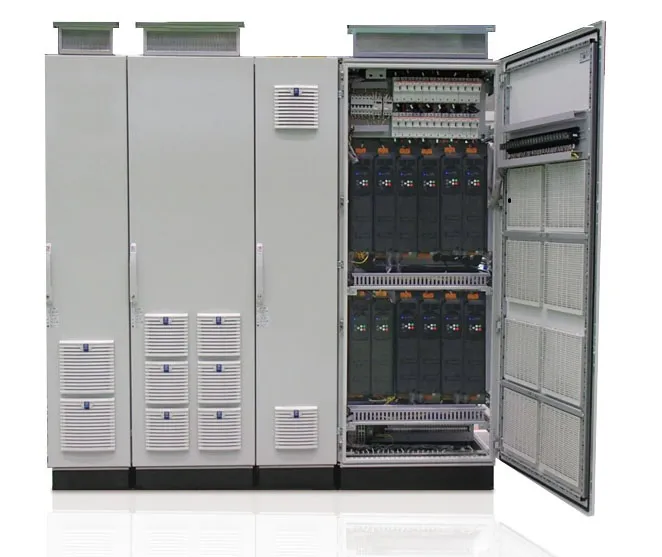
Both in Japan and around the world, there are movements to achieve decarbonization by reducing CO2 emissions on the production sites of the material industry, which includes steelmaking and papermaking, and of the assembly processing industry, which includes automobiles. Labor shortages also pose an issue, which has led to the promotion of DX (digital transformation) on the production sites. DX involves the collection and utilization of a variety of information, such as product quality and production equipment operation status, in order to save manpower and labor in operation and maintenance.
Motors are used to power harbor cranes and production equipment such as rolling mills at steelworks. The optimal operation of these motors is controlled by drive control systems for plants, which consist of inverters and converters.
Fuji Electric has recently launched its the industrial drives FRENIC-GS series for plants, which reduces power loss in motor control and increases the amount of data that can be transmitted. In addition to Japan and China, this system will be rolled out in Southeast Asia and India, which are seeing continued economic growth.
2. Features
-
-
(1) Reduced power consumption by reducing power loss
With harbor cranes and production equipment, in order to save energy, the energy generated when the motor decelerates or stops (called “regenerative power”) is returned to the power supply system and reused for the operation of other motors. In general, regenerative power is converted by inverters and converters and then returned to the power supply system. However, this system optimizes the circuit configuration so it can reuse regenerative power without returning it to the power supply system. Reducing the instances of power conversion reduces loss during conversion, resulting in a reduction of power consumption by up to approximately 4%.
When a drive control system is used to control a motor, it causes a slight distortion in the power supply waveform. Because this distortion has an adverse effect on peripheral devices, a filter is generally provided in the circuit to reduce distortion, but the resistor in the filter causes loss in the process. Fuji Electric has developed a power control technology that reduces distortion without using resistors, thereby successfully reducing loss. These features save energy on the production site, contributing to reducing CO2 emissions.
-
-
(2) Increased the amount of data that can be transmitted by applying high-performance CPU and separating the communication networks
Generally, drive control systems for plants use the same network both to collect information for recording and monitoring the operation and failure status of equipment and to transmit data to control motors according to instructions. However, there are limits to the transmission speed and amount, and the data for control was given priority.
This system uses a high-performance CPU for the main unit of the system to improve data processing capability and uses separate networks for information collection (the information LAN) and control (the control LAN) to increase the amount of data that can be transmitted while maintaining responsiveness and other aspects of control performance. This will promote the utilization of information by customers and contribute to the achievement of DX on the production sites.
-
-
(3) Improved the cooling structure of the converter and the wind tunnel structure to the smallest level in the industry
When conversion equipment, such as inverters and converters, is energized, it generates heat due to power loss. This system improves the cooling structure of such equipment for higher cooling efficiency to reduce heat dissipation space. In addition, the product size (dimensions) has been reduced to the smallest level in the industry (approximately 20% smaller than the company’s conventional product) by reviewing the wind tunnel structure to release heat in the panel for storing inverters and converters.
This contributes to space saving at the installation site.
3. Main Applications and Regions
-
-
[Applications]
• The material industry, including steel and non-ferrous metal, paper, cement and petrochemicals
• The assembly processing industry, including automobiles
• Cranes for harbors and construction
[Regions]
Japan, China, Asia, and India
4. Launch Schedule
-
-
As of the date of this announcement.
5. Product Inquiries
-
-
Sales Department I, Industrial Solution Division, Power Electronics Sales Group, Fuji Electric Co., Ltd.
☎ +81-3-5435-7031
-
-
*The information contained in this release (product features, inquiry information, prices, etc.) is accurate as of the date of this announcement. This information is subject to change without prior notice.