One Step Ahead! Fuji Electric's Fundamental Technologies
We provide an overview of our latest fundamental technologies that enhance our product development capabilities.
Technology to prevent the corrosion of steam turbines for geothermal power systems
The world’s leading manufacturer in geothermal power generation tackles the development of next-generation technology
Geothermal power generation is a technology with low environmental impact that uses underground vapor of approximately 200°C to turn turbines to generate electricity. Fuji Electric is among the best-delivering manufacturers in this field worldwide.
Recently, there is a growing interest in hot dry rock geothermal power generation which utilizes geothermal steam thigher than 350°C pumped from within the Earth’s crust. This system enables several hundred megawatts of power generation, approximately a ten-fold increase on conventional capacity, expected potential markets dozens of times the size of the current market. Fuji Electric leverages our cutting-edge technologies to develop turbines for this next-generation power system.
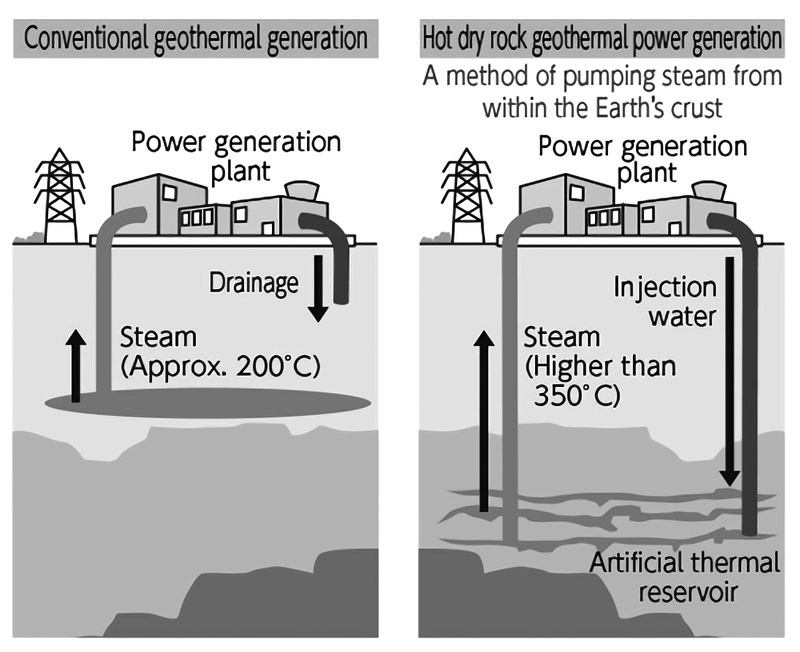
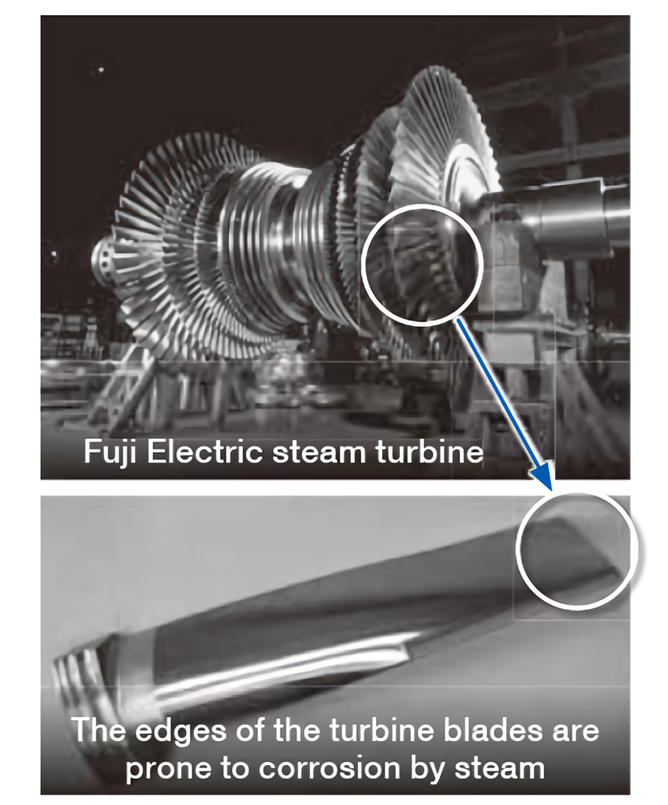
Durable, corrosion-resistant turbine blade developed using a mixture of two metallic materials and high-temperature laser coating technology
In geothermal generation, the higher the thermal gas temperature, the more efficient the power generation. However, gases from within the Earth's crust are contaminated with more corrosive substances, such as hydrogen sulfide and chlorine. Conventional turbine blades have stainless steel plates brazed onto their edges to protect against corrosion caused by steam, which is an issue in hot dry rock geothermal power generation because the bonding metal is not capable of resisting higher temperatures, and the stainless steel plates cannot endure the harsher and more corrosive environment.Then we chose a method of spraying metallic powder instead of brazing the metal plates. We selected ceramics as opposed to stainless steel for its excellent properties of hardness and corrosion-resistance.
Because ceramics are highly porous, we decided to also apply corrosion resistant alloy in finer particles to prevent the permeation of corrosive substances. In our challenge to create durable, corrosion-resistant turbine blades, we devised this method of metallic film coating by treating the powder metal mixture which is sprayed on the edges of the blades under a high-temperature laser beam.
The most difficult task in the development was to identify the optimal conditions for the ceramics and corrosion resistant alloy to maximize their combined performance. To find a solution, we collaborated with Osaka University, which has expertise in laser technology. In our joint research, we sought the best conditions of laser emissions and temperature. We also captured the metal film formation process with a high speed camera to visualize the film-forming mechanism, which then facilitated the identification of the best mixing ratio of the ceramics and anticorrosion alloy as well as of the best spraying conditions.
Once established, this technology will remove the brazing process, in which it takes approximately 180 hours per one turbine for a skilled engineer to finish manually brazing stainless steel plates. This is why it helps to streamline the manufacturing process. In the future, we will use simulation technology to investigate the degradation of turbine blades in the operational environment and the corrosive effects of different geological conditions in the aim of bringing this turbine to practical application soon.
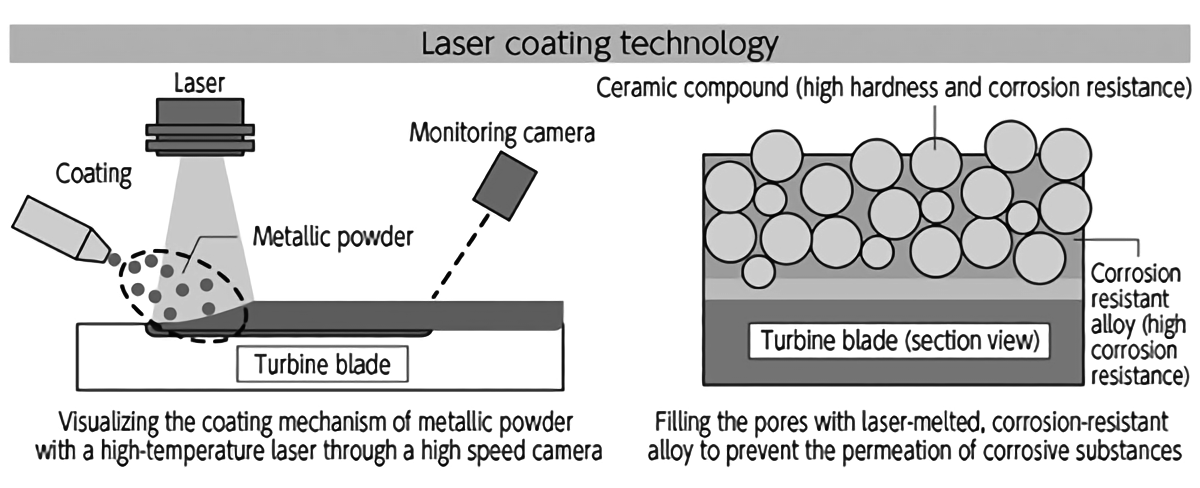
Voices of developers
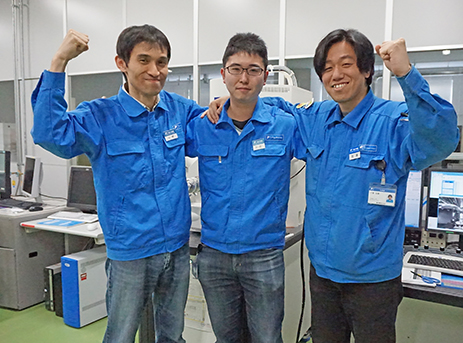
Contributing to value-adding activities through customer-oriented basic research
It is a source of pride and motivation to serve as the backbone of the core technologies in the geothermal power business, and so we consider it important to visit the site at every opportunity and consider the customer’s views in pursuing our basic research. In the future, we will look into the possibility of furthering the corrosion protection and introducing IoT technologies, such as remote corrosion monitoring systems using sensors. In this way, we will continue to contribute to creating high-value-added products.
The article and the affiliations are at the time of coverage.