One Step Ahead! Fuji Electric's Fundamental Technologies
We provide an overview of our latest fundamental technologies that enhance our product development capabilities.
Joining and Adhesives Technologies
As automobiles become increasingly lightweight,there is demand for joining technologies for new materials.
With the background of worldwide environmental regulations, various automakers are working on reducing CO2 emissions, and one of the key issues is reducing the weight of vehicle bodies for the purpose of improving fuel efficiency. For automobile bodies, it is expected that ultrahigh tensile strength steel,* aluminum alloy, plastic, and other new lightweight materials will become the mainstream in the near future. Currently, joining these new materials together requires the introduction of expensive equipment such as laser welders, and therefore it is expeced that less expensive joining technologies suited for mass production will be applied.
The current mainstream of vehicle body welding is spot welding. Unlike other welding technologies, spot welding does not use any joining materials but passes electric current through the components themselves and uses the heat generated by electrical resistance in the contact area to melt some parts of the components for joining ( Figure 1 ). The quality of welding depends largely on the mechanical and electrical characteristics of the components, and therefore the use of spot welding for new materials required specification of the welding conditions (welding time and current) suitable for the respective materials.
In these circumstances, we have developed a high-accuracy simulation technology to identify the welding conditions best suited for new materials.
-
*
-
Steel materials made stronger and lighter than conventional materials
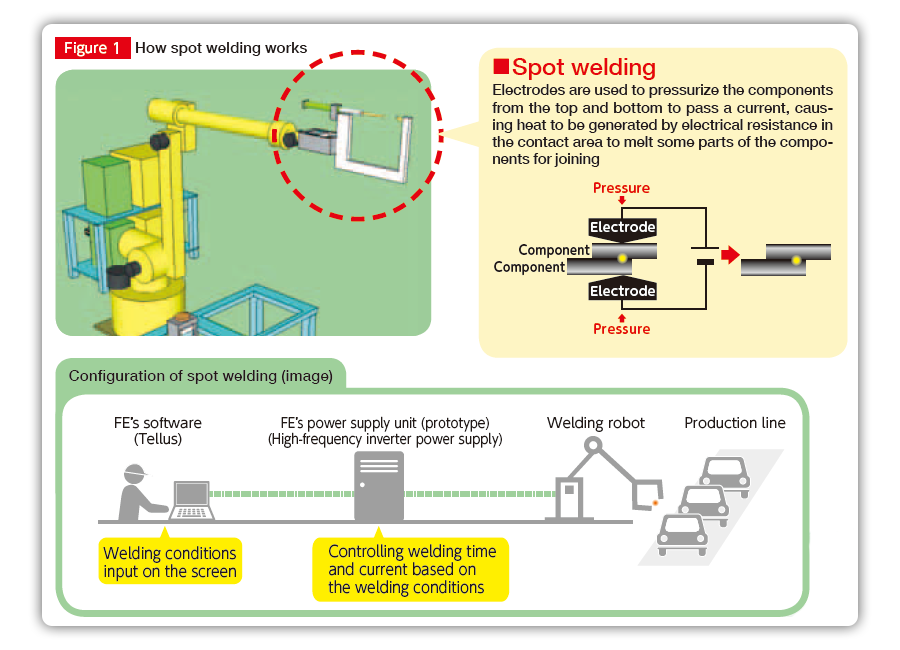
Developed simulation technology capable of predicting changes in heat generated by electrical resistance
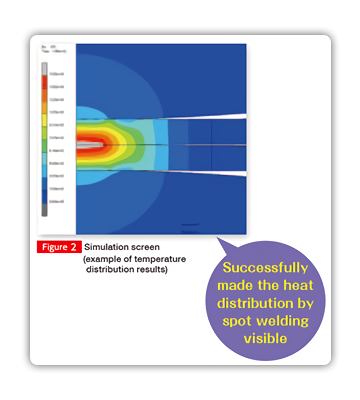
The electrical resistance (contact resistance) in the contact area in spot welding depends on a variety of factors, such as the thermal conductivity of the components (on the surface in particular), the pressure applied to the surface, and the amount of current. As these factors can change at short intervals (a few milliseconds), it was considered unfeasible to apply a simulation.
To deal with this issue, FE has carefully examined an enormous number of papers in that field to devise a prediction model for resistance value changes. We developed formulas that can be applied to software through joint research with a university to achieve an advanced simulation close to testing with a real machine ( Figure 2 ).
This led to the establishment of the conditions for welding ultra-high tensile strength steel with aluminum alloy. This has also reduced the verification period for establishing the welding conditions by approximately 80% compared to demonstration with a real machine alone.
In the future, we intend to expand the range of materials to which this technology can be applied and work on applying it to FE’s manufacturing processes for products such as switchboards, semiconductor modules, and vending machines.
Voices of developers
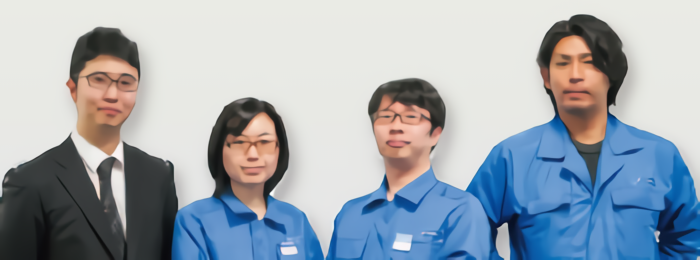
We develop the technique that we can differentiate from competition
In the future, we will develop technology for joining different materials such as ultra-high tensile strength steel and aluminum in order to develop products that set us apart from competitors and contribute to the internal manufacturing processes!
The article and the affiliations are at the time of coverage.