One Step Ahead! Fuji Electric's Fundamental Technologies
We provide an overview of our latest fundamental technologies that enhance our product development capabilities.
Epoxy Resin Flux
Developed flux with improved bond strength to adapt to the miniaturization of industrial equipment
In soldering, a soldering accelerator called flux is generally used in addition to the soldering material. Flux has the role of removing any dirt on the solder surface, preventing the oxidation of the base metal and improving solderability on the metal surface.
As industrial equipment becomes miniaturized, printed boards and electrodes are also becoming smaller. Smaller electrodes require a reduction of the amount of solder used, which may result in the inability to maintain sufficient bond strength. Smaller electrodes also mean a higher temperature on the electrode.
The main component of the flux we use is rosin, which is not resistant to high temperatures, and it was necessary to take steps to prepare for the further size reduction of industrial equipment. So, with the aim of making a flux that has sufficient bond strength even in small amounts and at high temperatures, we developed a flux material with epoxy resin as the main component.
Significantly reducing costs by eliminating the cleaning process necessary in conventional solder
Rosin has been used as the main component of flux, and because it is inexpensive and readily available, it has long been in wide use. However, some products require thorough cleaning after soldering. Incomplete cleaning could result in creating gaps between the metal and solder caused by liquefaction or cracking the flux residue*, allowing moisture between the printed board and electrode, which results in the corrosion or degradation of insulation.
Epoxy resin has recently been attracting attention as a way to deal with these issues. Flux that uses epoxy resin can maintain its strength thanks to the flux residue, which improves the adhesion of the solder joints, contributing to improved insulation.
We started developing an epoxy resin flux material in 2012.We repeated many cycles where we combined different types and amounts of raw materials, then had manufacturing done by a material manufacturer, and performed adjustment in response to the results. After about four years of research,we successfully developed solder containing flux with epoxy resin as the main component. It can be used at high temperatures,for example in industrial equipment applications,and it eliminates the need to clean flux residue. This renders cleaning equipment and fluid unnecessary and allows significant cost reduction. Since cleaning equipment and cleaning management are unnecessary, it makes it easier to transfer production overseas. In the future, we plan to apply this material to printed boards for general-purpose inverters and other products.
-
*
-
Unnecessary remains
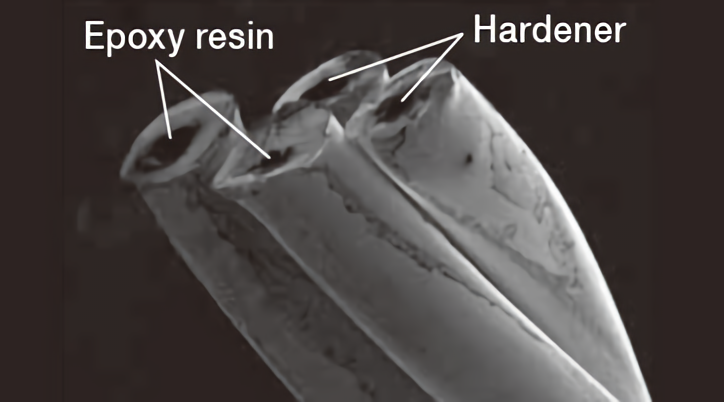
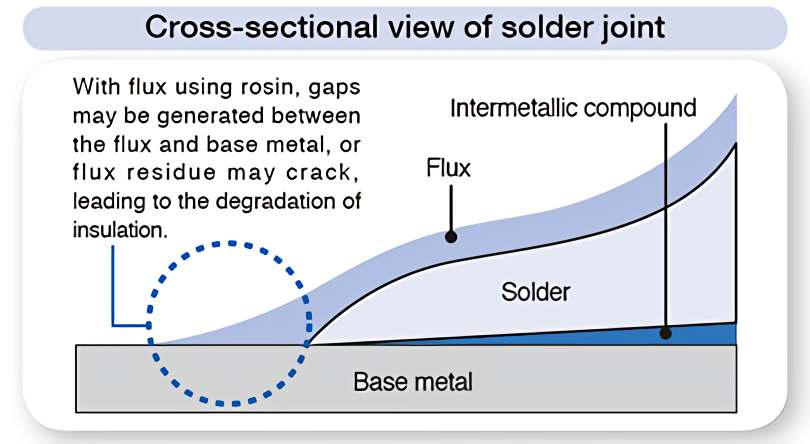
Voices of developers
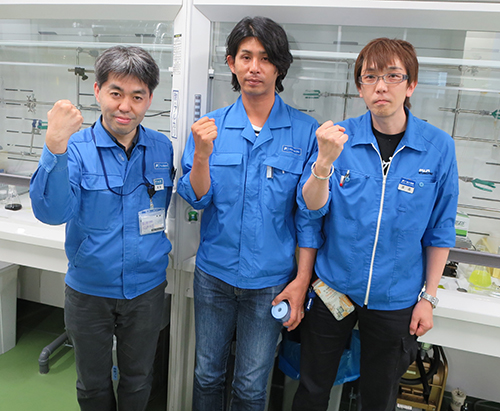
Equipment Technology Department, MONOTSUKURI Strategy Center, Production & Procurement Group
We listen to Manufacturing personnel
This solder with fl ux cream allows effi cient soldering at many points, but is not suitable for minute repair work to deal with defects. In response to a request from the manufacturing department, we worked to solve this issue and developed a solder containing thread-like epoxy fl ux, which has four solder threads, each of which has epoxy resin and hardener to solidify the solder injected at the center.
We intend to continue material development like this to improve the value of our products.
The article and the affiliations are at the time of coverage.