Sustainability
Product Quality Assurance
Our Basic Quality Assurance Approach
Fuji Electric established its Quality Assurance Policy in 1970, stipulating the Company's assurance of the industry's highest standard for quality in all of its products and services.
Every year, we formulate a High Reliability Activities Policy based upon the Quality Assurance Policy and work hard to improve quality at every stage of our business, from product planning through sales and service.
(Established in 1970, revised in 2022)
-
Quality Assurance Policy
To ensure the satisfaction of all customers, the duty of Fuji Electric is to maintain the highest levels of quality in the industry for the products and services it produces and sells. -
Goals
Aiming to be a Company with high value in society, we will remain aware of our roles and responsibilities in society and continue to provide products and services useful to the public and thereby earn their trust.
We aim to eliminate accidents and complaints that would harm the trust and reliance our customers place in us, and eliminate defective products. -
Fundamentals Underlying Our Activities
-
1.
The firm determination of top executives
-
2.
The strong adherence to quality of each employee
-
3.
Enhancement of technologies and technical skills
Quality Assurance Activities Promotion Framework
Fuji Electric recognizes that quality is an important factor in production technology. In November 2005, we established the Quality Assurance Working Group, as one of four cross-company subcommittees within the Production Technology Committee. This working group is tasked with advancing the Company’s production technology capabilities.
In April 2022, we took some additional initiatives to further enhance the robustness of our quality improvement activities that aim at achieving “100% Quality.” These included renaming the working group the “High Reliability Working Group” and strengthened the overall framework.
Quality improvement activities are promoted mainly by the High Reliability Working Group in coordination with other subcommittees. The activities aim to achieve stable, uniform levels of production technology as a means of enhancing customer satisfaction.
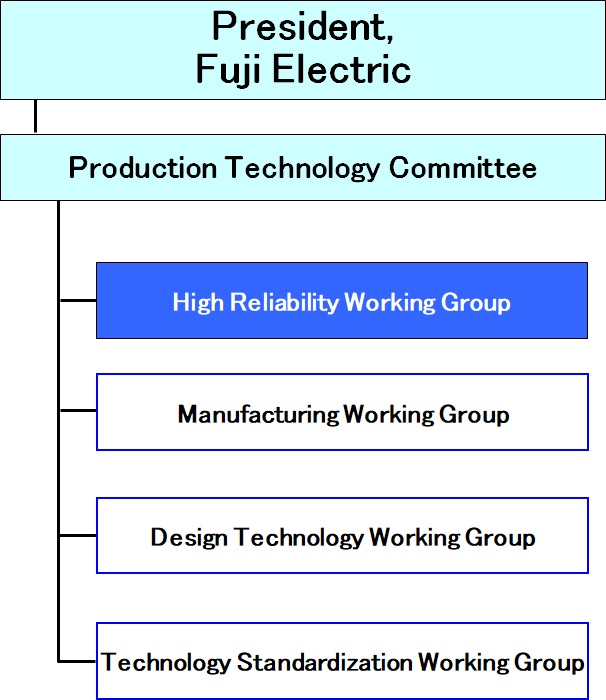
Range of Production Technologies
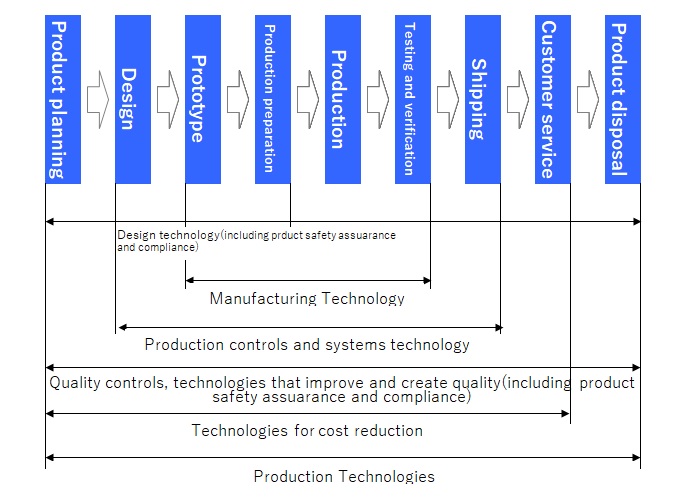
Initiatives for High Reliability Activities
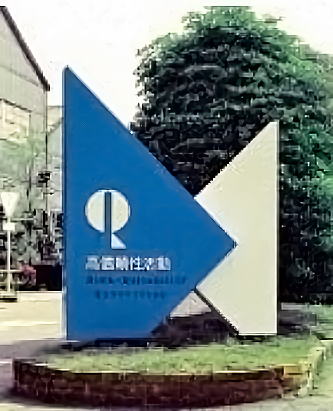
Every year, we formulate a High Reliability Activities Policy based upon the Quality Assurance Policy, and this policy is applied to business divisions and factories. Then, all business divisions and factories also formulate their own high reliability activities policies.
Based on the Quality Assurance Policy and High Reliability Activities Policy and using the PDCA (plan, do, check, act) cycle, we continuously improve quality.
In fiscal year 2024, with the aim of enhancing soundness, we implemented cross-factory mutual diagnostics of manufacturing processes, standardization of QC patrols, and revision of the soundness guidelines. Furthermore, as measures to strengthen technical capabilities in development and design, we worked on reviewing DR (Design Review) regulations and creating a database of our proprietary technologies, re-examining QMS (Quality Management Systems) at key overseas sites, promoting digitalization of testing and inspection & SPC (Statistical Process Control) management, improving quality at priority sites (Suzuka, Kawasaki, Chiba, Tsukuba), and quality improvement activities for plant operations.
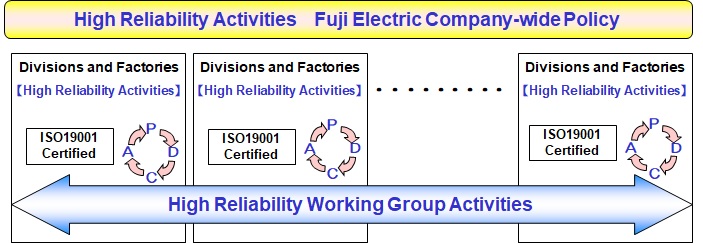
Fuji Electric has acquired ISO 9001 international certification to maintain and enhance our QMS structure. As of the end of March 2025, 38 organizations at bases inside and outside of Japan and at subsidiaries, including 100% of production bases and companies, excluding sales companies, have been certified.
Human Resource Cultivation to Support Quality
Enhance the Training System
Fuji Electric conducts quality management training based on its Quality Assurance Policy to enhance employees’ techniques and skills.
Fuji Electric cultivates the human resources that support quality mainly at two places, the Human Resource Development Dept. in Hino City, Tokyo, which trains human resources Company-wide, and the Technical & Skill Training Department in Konosu City, Saitama, which forms the core of strengthening production technology capabilities.Quality assurance training is given in groups under themes including managing quality and high reliability, statistical methods and problem-solving methods, etc. Holding regular training links to nurturing employees’ techniques and skills.
Increasing the Number of Successful QC Examination Applicants
To raise quality assurance awareness among each employee, Fuji Electric encourages more people to pass the QC examination that is sponsored by the Japanese Standards Association and the Union of Japanese Scientists and Engineers. As of fiscal 2024, a total of 2,900 employees had passed the third grade, 1,478 had passed the second grade, and 20 had passed the first grade.
We aim to increase the number of qualifications holding employees even further as a Company-wide activity going forward.
Holding Workshops on Learning from Failures

Since fiscal year 2006, we have continuously held "Workshops on Learning from Failures" as part of our efforts to thoroughly learn from past product defects and failures to prevent recurrences. In each case study presentation, the root causes and the background/history of the failure are elucidated, lessons learned are derived, and these are shared with the participants. We also aim to conceptualize and systematize these lessons so that they can be utilized in our business operations.
In fiscal year 2024, we held three workshops in total: two sessions each featuring case studies on three themes (such as missed extraction of design requirement specifications, failures due to new technologies, insufficient design/reliability evaluation, and inadequate manufacturing work instructions), and one lecture by an external lecturer on the theme “Role and Application of TQM in Management.” A total of 550 employees attended these sessions.