Innovating with core technologies for hydrogen production! Four talented people taking on emerging markets
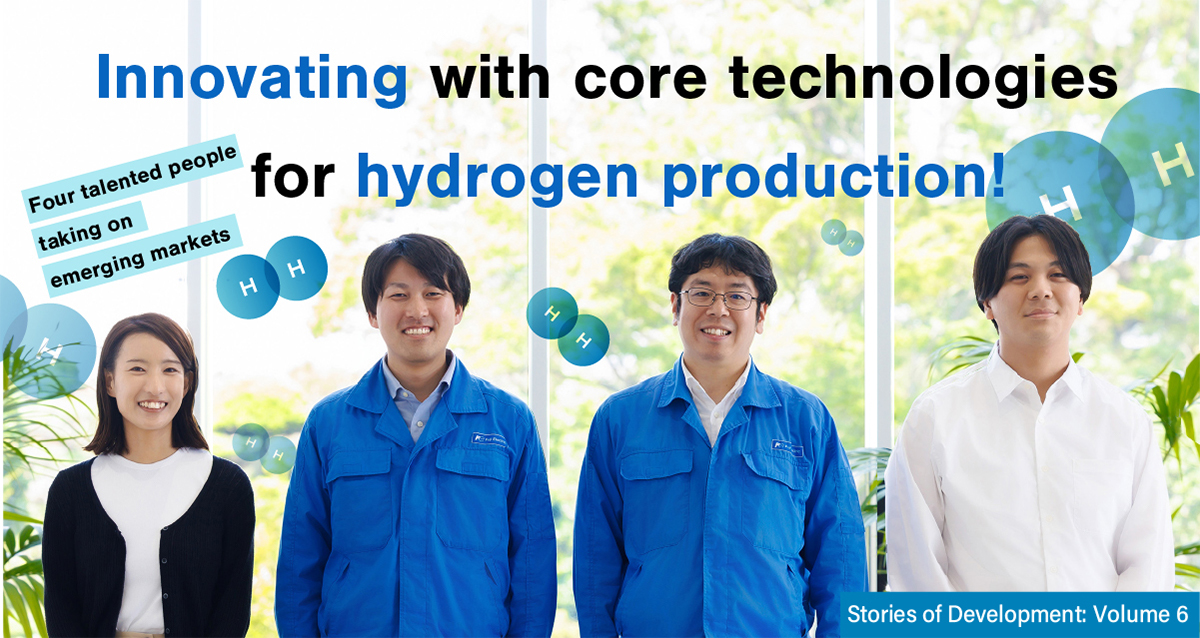
Hydrogen energy is expected to be utilized for realizing a decarbonized society. Fuji Electric is developing products that are indispensable for the production of “hydrogen” by utilizing the knowledge and technology it has cultivated in aluminum smelting and caustic soda production. When we visited the development site where researchers are striving to contribute to society in the rapidly developing industry of hydrogen energy, we were met by four talented people.
Utilizing world-leading aluminum smelting technology
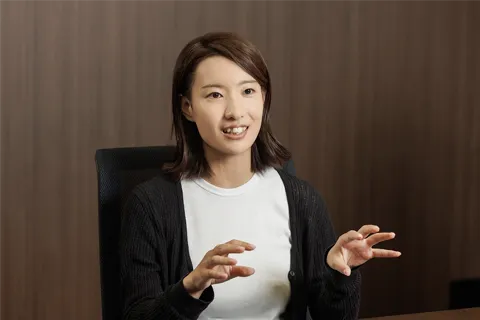
Hydrogen can be combined with oxygen to generate electricity or combusted for use as energy. Since it does not emit CO2 in the process, it is attracting attention worldwide as a clean energy source.
Ms. Ogawa, who is in charge of overseas sales, expressed her expectations saying, “Hydrogen is a new market, and there are still some unknowns as it is not yet a mature business sector, but an increasing number of new manufacturers are entering the market to take advantage of the trend toward decarbonization.”
Fuji Electric has advanced technology in rectifiers, which are used to electrolyze raw materials in aluminum smelting and caustic soda production, and enjoys the largest market share in the aluminum smelting market in the Middle East and North America. Rectifiers are products that convert AC electricity into DC and then deliver the high DC current required for electrolysis. Speaking figuratively, rectifiers are like the heart that pumps the blood in the human body.
“Green hydrogen” refers to hydrogen produced by electrolyzing water using electricity derived from renewable energy without emitting CO2 in the production process. Rectifier technology can also be used in the production of green hydrogen, since electrolysis of water requires DC electricity.
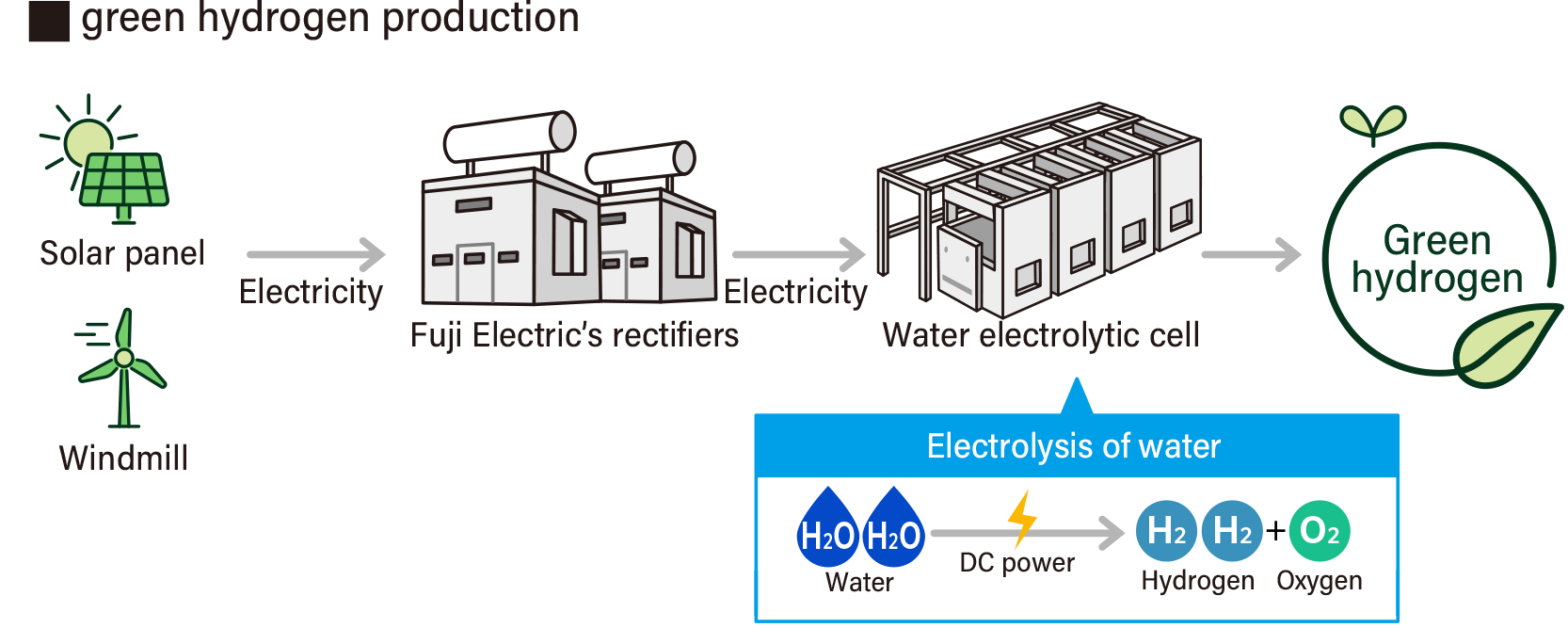
In 2020, Fuji Electric delivered rectifiers to a pilot plant for hydrogen production in Japan as part of NEDO’s (New Energy and Industrial Technology Development Organization) project to develop technology for building a hydrogen-based society. Ms. Ogawa remarked, “At that time, there were no rectifiers specially designed for hydrogen production. To stay competitive in the hydrogen energy business, we knew we needed a product specifically designed for hydrogen production.”
In October 2021, efforts began in earnest to develop a “rectifier for hydrogen production.”
Created using a four-person relay approach
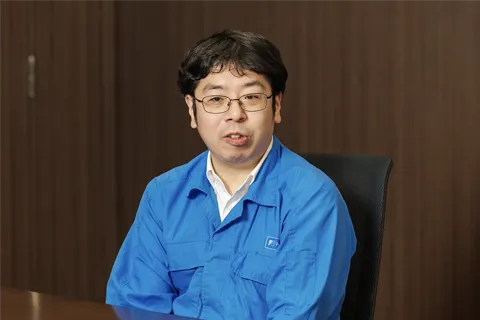
Mr. Tamai, who has been with the company for 20 years, has been involved in the research and development of substation equipment and industrial power supply equipment at the Chiba Factory. In the development of a rectifier for hydrogen production, Mr. Tamai has been in charge of the control system for supplying an appropriate amount of current and voltage to the electrolytic cell that performs electrolysis.
In conventional rectifiers, diodes and thyristors have been used as semiconductor devices for power conversion, but the newly developed hydrogen production system uses IGBTs (see Note 1).
Mr. Tamai commented, “IGBTs can be switched on and off to reduce current distortion and maintain a constant voltage in power grids, making them effective when using renewable energy sources with unstable output, such as solar and wind power. In order to increase the amount of ‘green hydrogen’ produced from renewable energy, we decided that IGBTs should also be used in rectifiers. However, it is necessary to reconfigure the circuitry when applying IGBTs. Of course, this raised the technical hurdles, such as the need to devise a control system from scratch.”
Because there were concerns that the size of equipment and costs would increase if new circuits were configured using existing IGBTs, Mr. Tamai worked with the Matsumoto Factory, which develops and manufactures semiconductor devices, to develop a dedicated IGBT. Fuji Electric used its comprehensive strengths to meet the challenge.
-
(Note 1)
-
IGBT is an abbreviation for Insulated Gate Bipolar Transistor.
It is a transistor suitable for high breakdown voltages and large currents.
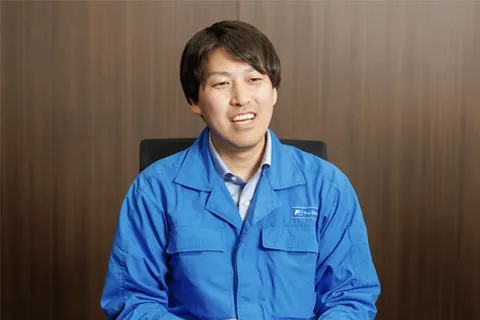
Mr. Yamanodera, who is in charge of design, will commercialize the product based on the control system developed by Mr. Tamai.
Because rectifiers for aluminum smelting are large products that are made-to-order and have different specifications depending on the customer, the delivery time from order to shipment is normally about one year. However, to facilitate applications in hydrogen production, we needed to create a design that would allow for mass production.
Mr. Yamanodera remarked, “In order to mass-produce the rectifier, we decided on the structure and parts from the initial design stage, while keeping in mind the assembly procedure and workability. In addition, when we built the prototype, we personally observed the assembly work by the manufacturing department and repeatedly made improvements by reflecting the requests and technical advice of workers into the design, as well as the insights we gained from first-hand observation of the assembly work.”
Furthermore, in contrast to aluminum smelting, which uses large amounts of electricity, hydrogen production requires more compact products while providing sufficient space for maintenance. Mr. Yamanodera continued by saying, “We were able to save space and secure the space required for maintenance by utilizing the water-cooling technology developed for rectifiers and designing a system that efficiently cools the heat generated during equipment operation.”
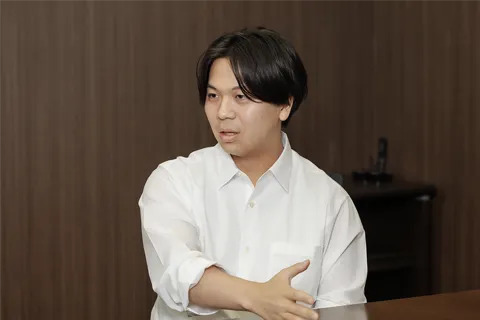
Finally, Mr. Yoshida is in charge of verifying the system in which the product is used. In hydrogen production plants, many components such as rectifiers and electrolyzers work together, and interference between these components can affect the power grid and cause problems such as voltage flicker (see Note 2).
Mr. Yoshida said, “Engineering firms and end users evaluate the entire system, not just Fuji Electric’s products. To ensure that the product works properly no matter what equipment is connected to it, we verify and check everything one by one to eliminate any defects. Fuji Electric also develops equipment to compensate for unstable power, and our strength is that we can offer a wide range of systems to our customers.”
-
(Note 2)
-
This refers to flickering of lighting and other phenomena due to voltage fluctuations.
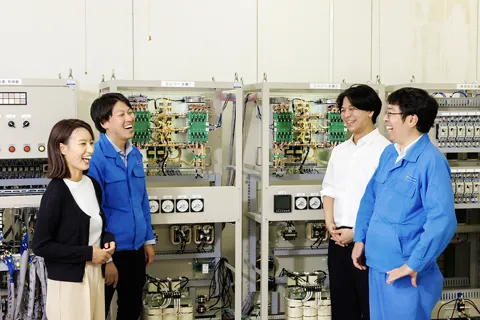
Based on Mr. Yoshida’s verification data, Mr. Tamai recreates the control program, and Mr. Yamanodera carries out the design.―― Just like a in relay race, after making several laps around the track, the baton is finally handed off to the anchor, Ms. Ogawa, who delivers the product to the customer.
Ms. Ogawa commented, “The hydrogen market is just getting started. Since customers were proceeding on their own, they have had varying voltage and current requirements for rectifiers. This made it difficult to identify common ground in specifications.”
To address this challenge, we developed a standard product with a capacity of 6 MW and an output current of 8000 A, which can be connected in series or parallel to accommodate the scale required by customers.
The specifications were finalized in July 2023. Operation verification was completed on the mini-model and now efforts are proceeding to verify the full-size prototype.
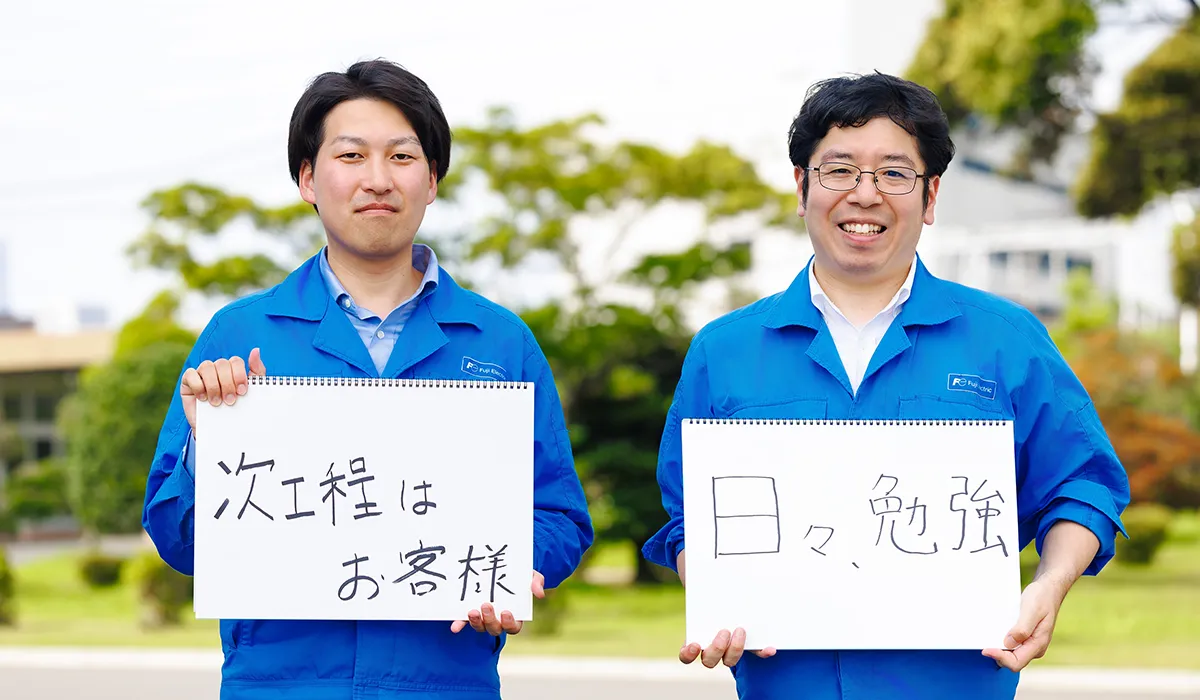
Mr. Tamai (right): “Technology is advancing at an incredible pace in the world. My personal goal is to study every day and expand my skills so that I can learn new things quickly.”
Creating results from scratch
In June 2024, prior to the completion of the product, Ms. Ogawa attended an exhibition for companies involved in hydrogen energy in the United States. She experienced something very surprising there.
Ms. Ogawa remarked, “Fuji Electric is widely recognized overseas as a manufacturer of rectifiers. So, when I told people that I worked for a manufacturer of rectifiers, they immediately understood that our product was a core component in hydrogen production plants. But I was really surprised at how many people in the hydrogen industry asked me what a rectifier was.”
There are many new entrants from other industries in the emerging hydrogen energy market. Ms. Ogawa continued by saying, “At any rate, it is important to make a good first impression among these new entrants. This means helping them understand the importance of rectifiers and the reputation of Fuji Electric. In some ways, it feels like we are starting from scratch.”
These four talented people are passing on the baton of the product, which is nearing completion and is scheduled to be launched by the end of fiscal 2025.
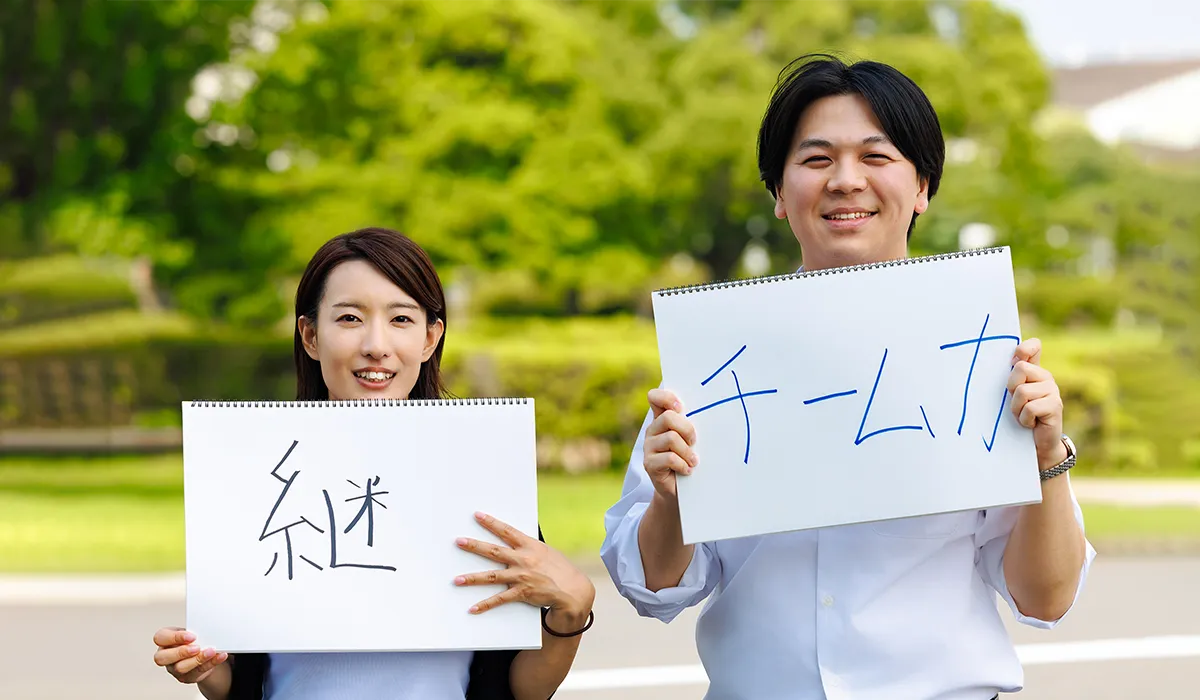
Mr. Yoshida (right): “This kind of work is not something that can be done singlehandedly. Therefore, it is important to emphasize ‘teamwork,’ which means working together with colleagues within the company as well as with customers.”
The four of them share a common goal, saying “Fuji Electric wants to make ‘rectifiers for hydrogen production’ one of its mainstay products in this promising field of hydrogen energy.”