Control functions and engineering functions
Meeting a wide range of requirements through various combinations of control functions and efficient engineering
In addition to special-purpose controllers from the former series to the latest series, new and former programmable logic controllers (PLC) are also supported.
This capability enables flexible configurations to match the application and scale requirements.
And in addition to engineering tools that conform to the IEC 61131-3 international standard, efficient engineering is made possible using machine-less simulation and engineering support tools.
XCS-3000, XCS-3000R(*1) and XCS-3000 Type E(*1) special-purpose controllers(*1)
High-performance CPU
Use of a 1 GHz dual-core processor for the CPU enables high-speed control from a minimum cycle of 1 ms. As a result, combined high-speed electrical machinery control and high-performance measurement control can be performed by one unit. Additionally, with the use of a multiprocessor architecture and scheduling technology that can execute network processing and arithmetic processing of application programs in parallel, the controller also features excellent communication performance.
High-speed LAN
Equalization bus
High-speed transfer of large volumes of data has become possible with large-capacity equalization technology and enables equalization of the whole area of application data.
Network adapter bus(*1)
This is a high-speed LAN used as a network adapter to connect to Fuji Electric legacy networks and various other networks.
E-SX bus
The E-SX bus is a high-speed I/O network that supports redundancy.
Large-capacity memory
Features a program memory of 512 k steps, a large-capacity data memory of 2,368 k words, and I/O can be connected up to 4,096 words (32 nodes) per control station.
High-reliability CPU
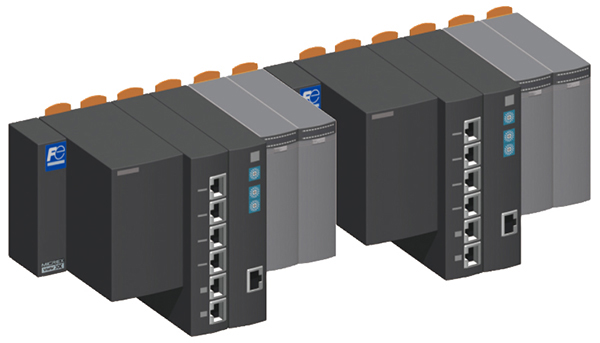
The CPU supports redundancy and enables a high-reliability control station through the use of error-correcting code (ECC) memory and enhanced reliability, availability, and serviceability (RAS) functions.
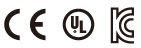
Remote I/O lineup for various applications
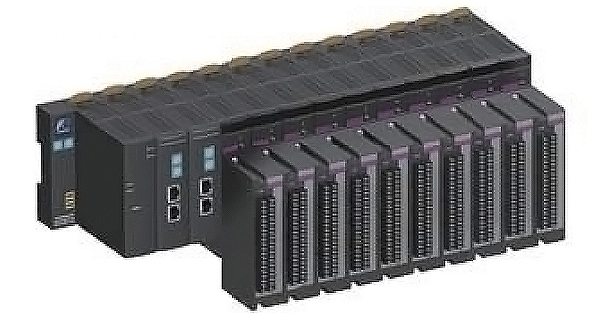
High-reliability I/O
The I/O network uses a 100 Mbps E-SX bus and inherits the features and specifications of existing I/O networks. Furthermore, the XCS-3000 control station supports mixed mounting with [E-SX I/O]. Moreover, this is highly reliable I/O that enables power supply redundancy, I/O network redundancy, and I/O module redundancy (module pair or node pair redundancy).
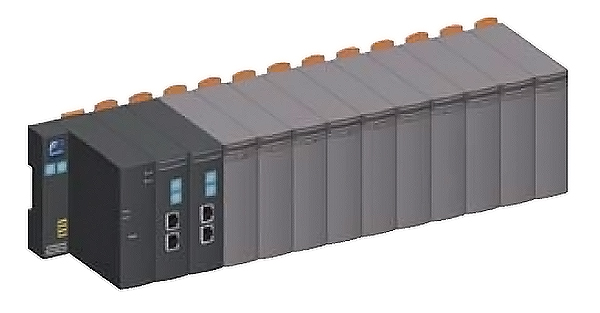
E-SX I/O
The I/O network uses a 100 Mbps E-SX bus and can be mounted to an XCS-3000 control station. In addition to I/O networks, communication modules such as Ethernet and RS-232C can be selected for mounted modules. It also enables power supply redundancy and I/O network redundancy.
Legacy network connections(*1)
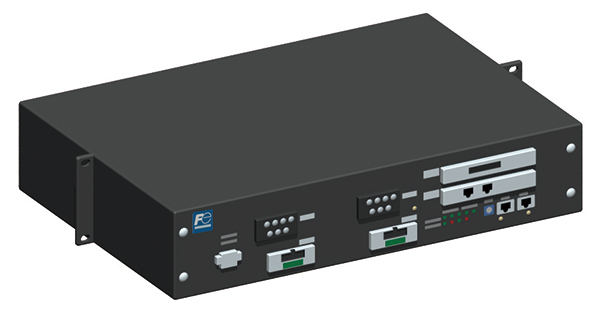
The network adapter connects to up to four types of networks, including Fuji Electric legacy networks such as PE-link, T-link, as well as the open FL-net network. Furthermore, since redundant network adapters can be installed with the control station, a highly reliable system can be constructed.
Supported networks
-
FL-net Ver. 3 compliant LANs
-
PE-link
-
T-link (IPU-I, FTU, FTK)
-
Ethernet EPAP (IPU-II)
MICREX-SX general-purpose PLC
MICREX-SX general-purpose PLC with high-performance CPU
With a program capacity up to 512 k steps and I/O control of up to 65,536 points, it is possible to construct an optimal system from small to large scale. A 1 ms program scan and I/O refresh are possible. Construction and performance can be distributed with a multi CPU system of up to eight CPUs.
Open network connections
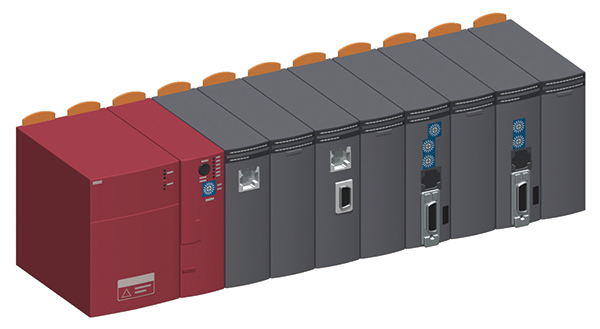
Various open networks are supported including Ethernet, LONWORKS(*1), FL-net, Device-net(*1), PROFIBUS-DP(*1) and AS-i(*1).
Engineering functions
Software for both special-purpose controllers and general- purpose PLCs can be developed in the same engineering environment.
Machine-less simulation
Use of the simulator enables system equipment such as control stations and operator stations to be built and operated on a personal computer.
For example, it is possible to check functions that combine control station control functions and screen functions while simulating input and output signals, or check the data of inter-station communication without using actual machines. This enables efficient and high-quality engineering.
IEC 61131-3 compliant
The engineering tool of the control station (Expert D 300 win) supports five types of program representations that conform to the IEC 61131-3 international standard (JIS B 3503), enabling an optimal combination to be used for engineering.
Supported programming languages
-
IL(Instruction List)
-
LD(Ladder Diagram)
-
FBD(Function Block Diagram)
-
ST(Structure Text)
-
SFC(Sequential Function Chart)
Engineering support tool HEART-BELIEVE-ESPER/SELECT (option)
Control function specifications created using familiar general-purpose OA software such as Excel or Visio can be automatically converted to control station programs. The execution status of the control station on the control function specification can be monitored for easy-to-handle efficient engineering from specification study to design, testing, and post-delivery maintenance.
Instrumentation flow (Visio)
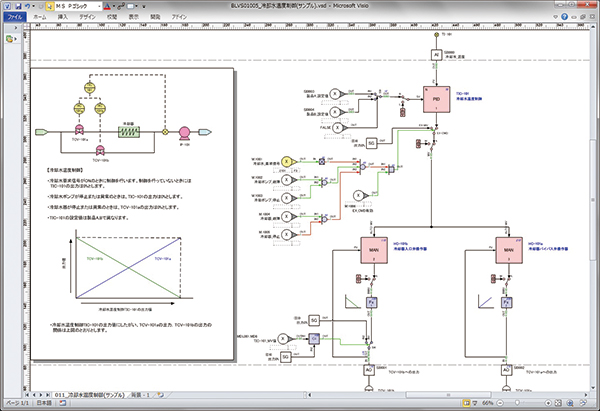
SFC(Excel)
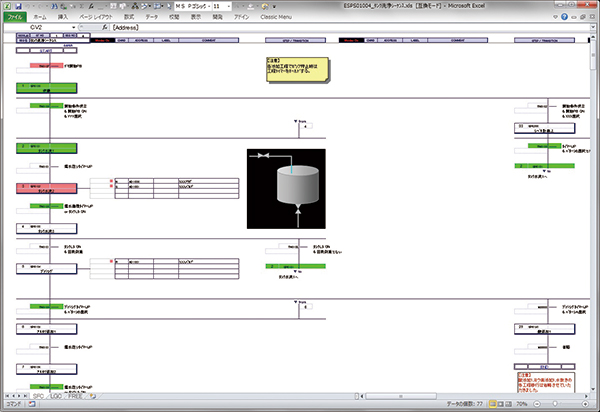
Time chart (Excel)
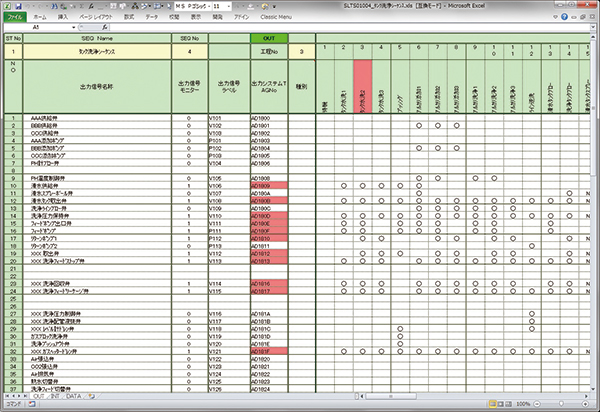
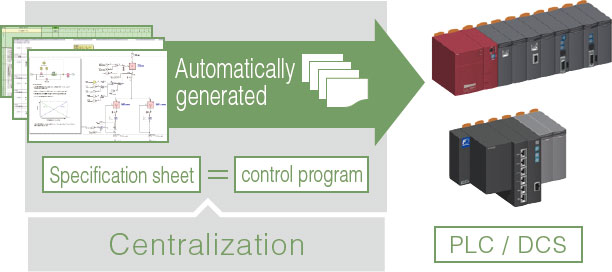
Since the program is automatically generated from the specifications, human errors such as programming mistakes and input mistakes are eliminated. The software is generated as described in the specifications.
-
*1
-
This feature will be also available on MICREX-View FOCUS Evolution in future.